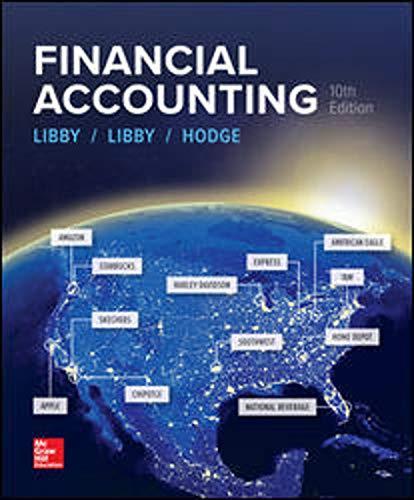
FINANCIAL ACCOUNTING
10th Edition
ISBN: 9781259964947
Author: Libby
Publisher: MCG
expand_more
expand_more
format_list_bulleted
Concept explainers
Topic Video
Question
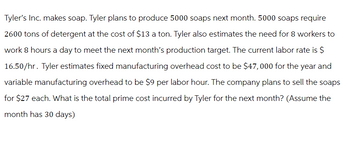
Transcribed Image Text:Tyler's Inc. makes soap. Tyler plans to produce 5000 soaps next month. 5000 soaps require
2600 tons of detergent at the cost of $13 a ton. Tyler also estimates the need for 8 workers to
work 8 hours a day to meet the next month's production target. The current labor rate is $
16.50/hr. Tyler estimates fixed manufacturing overhead cost to be $47,000 for the year and
variable manufacturing overhead to be $9 per labor hour. The company plans to sell the soaps
for $27 each. What is the total prime cost incurred by Tyler for the next month? (Assume the
month has 30 days)
Expert Solution

This question has been solved!
Explore an expertly crafted, step-by-step solution for a thorough understanding of key concepts.
Step by stepSolved in 3 steps

Knowledge Booster
Learn more about
Need a deep-dive on the concept behind this application? Look no further. Learn more about this topic, accounting and related others by exploring similar questions and additional content below.Similar questions
- MCO Leather manufactures leather purses. Each purse requires 2 pounds of direct materials at a cost of $3 per pound and 0.7 direct labor hour at a rate of $17 per hour. Variable overhead is budgeted at a rate of $3 per direct labor hour. Budgeted fixed overhead is $14,000 per month. The company’s policy is to end each month with direct materials inventory equal to 30% of the next month’s direct materials requirement. At the end of August the company had 2,880 pounds of direct materials in inventory. The company’s production budget reports the following. Production Budget September October November Units to produce 4,800 6,800 6,400 (1) Prepare direct materials budgets for September and October.(2) Prepare direct labor budgets for September and October.(3) Prepare factory overhead budgets for September and October.arrow_forwardSoul Socket Inc. manufactures socket wrenches. . For next month, the vice president of production plans on producing 4,450 wrenches per day. The company can produce as many as 5,000 wrenches per day, but is more likely to produce 4,500 per day. . The demand for wrenches over the past three years averaged 4,250 wrenches per day. • Fixed manufacturing costs per month total $374,000. . The company works 22 days a month. • Fixed manufacturing overhead is charged on a per-wrench basis. a. What is the overhead rate per wrench based on Theoretical Capacity? [Select] b. What is the overhead rate per wrench based on Practical Capacity? [Select] c. What is the overhead rate per wrench based on Normal Utilization? [Select] d. What is the overhead rate per wrench based on Master Budget Utilization? [Select]arrow_forwardParadise Marine Sails manufactures sails for sailboats. The company’s capacity is 29,000 sails per month. They are currently producing 25,000 sails a month. Current production cost can be found in the chart below: Sales Price $200 Variable Cost Manufacturing Cost $100 Administrative Cost $50 Total Fixed Cost Manufacturing $500,000 Administrative $480,000 Should you accept a special order at a price of $170 for 3000 sails? Fixed cost will increase by $9,000 to produce these sails. Give a numerical justification Would your answer be different if the company was currently producing 28,000 sails?arrow_forward
- Summer company manufactures beach chairs. $ 4.00 of direct materials are needed for each chair. Labor is $ 15 an hour. The company manufactures 3 chairs per hour. Indirect costs are $ 9.00 per hour. Commissions to sellers are $ 2.00 per unit sold. The cost of a chair will be:arrow_forwardSheridan Ranch Inc. has been manufacturing its own finials for its curtain rods. The company is currently operating at 100% of capacity, and variable manufacturing overhead is charged to production at the rate of 51% of direct labor cost. The direct materials and direct labor cost per unit to make a pair of finials are $4 and $5, respectively. Normal production is 31,700 curtain rods per year. A supplier offers to make a pair of finials at a price of $13.05 per unit. If Sheridan Ranch accepts the supplier's offer, all variable manufacturing costs will be eliminated, but the $46,900 of fixed manufacturing overhead currently being charged to the finials will have to be absorbed by other products. (a) Prepare the incremental analysis for the decision to make or buy the finials. (Enter negative amounts using either a negative sign preceding the number eg.-45 or parentheses eg. (45).) Direct materials Direct labor Variable overhead costs Fixed manufacturing costs Purchase price Make $ Buy…arrow_forwardLeeds Corp. produces product BR500. Shamokin expects to sell 10,000 units of BR500 and to have an ending finished inventory of 2,000 units. Currently, it has a beginning finished inventory of 800 units. Each unit of BR500 requires two labor operations, one labor hour of assembling and two labor hours of polishing. The direct labor rate for assembling is $10 per assembling hour and the direct labor rate for polishing is $12.50 per polishing hour. The expected number of hours of direct labor for BR500 for this period are O 8,800 hours of assembling; 17,600 hours of polishing O 11,200 hours of assembling: 22,400 hours of polishing 17,600 hours of assembling: 8,800 hours of polishing O 22,400 hours of assembling: 11,200 hours of polishingarrow_forward
- Ceder Company has compiled the following data for the upcoming year: Sales are expected to be 16,000 units at $52 each. Each unit requires 4 pounds of direct materials at $2.40 per pound. Each unit requires 2.1 hours of direct labor at $13 per hour. Manufacturing overhead is $4.90 per unit. Beginning direct materials inventory is $5,400. Ending direct materials inventory is $6,950. Selling and administrative costs totaled $138,720. Determine Ceder's budgeted cost of goods sold. Complete Ceder's budgeted income statement.arrow_forwardBecker Bikes manufactures tricycles. The company expects to sell 360 units in May and 490 units in June. Beginning and ending finished goods for May are expected to be 100 and 65 units, respectively. June's ending finished goods are expected to be 75 units. Each unit requires 3 wheels at a cost of $6 per wheel. Becker requires 20 percent of next month's material production needs on hand each month. July's production units are expected to be 460 units. Compute Becker's direct materials purchases budget with respect to wheels for May and June. Budgeted cost of wheels purchased May Junearrow_forwardSheridan Ranch Inc. has been manufacturing its own finials for its curtain rods. The company is currently operating at 100% of capacity, and variable manufacturing overhead is charged to production at the rate of 66% of direct labor cost. The direct materials and direct labor cost per unit to make a pair of finials are $4 and $5, respectively. Normal production is 34,300 curtain rods per year. A supplier offers to make a pair of finials at a price of $13.05 per unit. If Sheridan Ranch accepts the supplier's offer, all variable manufacturing costs will be eliminated, but the $45,700 of fixed manufacturing overhead currently being charged to the finials will have to be absorbed by other products. (a) Prepare the incremental analysis for the decision to make or buy the finials. (Enter negative amounts using either a negative sign preceding the number e.g. -45 or parentheses e.g. (45).) Direct materials. Direct labor Variable overhead costs Fixed manufacturing costs Purchase price Total…arrow_forward
- Sheridan Inc. has been manufacturing its own shades for its table lamps. The company is currently operating at 100% of capacity, and variable manufacturing overhead is charged to production at the rate of 50% of direct labour costs. The direct materials and direct labour costs per unit to make the lampshades are $4.50 and $5.50, respectively. Normal production is 48,000 table lamps per year. A supplier offers to make the lampshades at a price of $13.20 per unit. If Sheridan Inc. accepts the supplier's offer, all variable manufacturing costs will be eliminated, but the $40,000 of fixed manufacturing overhead currently being charged to the lampshades will have to be absorbed by other products. Prepare the incremental analysis for the decision to make or buy the lampshades. (Round answers to O decimal places, e.g. 5,275. If an amount reduces the net income then enter with a negative sign preceding the number e.g. -15,000 or parenthesis, e.g. (15,000). While alternate approaches are…arrow_forwardLay's Potato Chips is examining their Wavy Lays chip line. They began the year expecting to produce 500,000 bags of potato chips. They projected that each bag would require 3 pounds of potatos and 1.5 hours of labor to manufacture. They planned to pay $2 per pound for potatos and $20 per hour for labor. They also budgeted $900,000 for variable manufacturing overhead costs and $ 450,000 of fixed manufacturing overhead costs, with both variable and fixed manufacturing overhead costs being allocated based on direct labor hours. At the end of the year, Lay's finds that they produced 880,000 bags of potato chips, using 3.25 pounds of potatos per bag and 1.25 hours of labor per bag. Due to significant inflation, the purchasing department made a deal with the supplier and purchased 3,000,000 pounds of potatos for a per-pound price of $3.25. They also spent $22 per hour for direct labor. The Wavy Lays chip line spent $843,000 on variable manufacturing overhead costs and $562,000 on fixed…arrow_forwardIvanhoe Inc. has been manufacturing its own finials for its curtain rods. The company is currently operating at 100% of capacity, and variable manufacturing overhead is charged to production at the rate of 61% of direct labor cost. The direct materials and direct labor cost per unit to make a pair of finials are $4 and $5, respectively. Normal production is 32,300 curtain rods per year. A supplier offers to make a pair of finials at a price of $12.90 per unit. If Ivanhoe accepts the supplier's offer, all variable manufacturing costs will be eliminated, but the $46,500 of fixed manufacturing overhead currently being charged to the finials will have to be absorbed by other products. (a) Prepare the incremental analysis for the decision to make or buy the finials. (Enter negative amounts using either a negative sign preceding the number eg.-45 or parentheses e.g. (45)) Direct materials Direct labor Variable overhead costs Fixed manufacturing costs Purchase price Total annual cost (c) (b)…arrow_forward
arrow_back_ios
arrow_forward_ios
Recommended textbooks for you
- AccountingAccountingISBN:9781337272094Author:WARREN, Carl S., Reeve, James M., Duchac, Jonathan E.Publisher:Cengage Learning,Accounting Information SystemsAccountingISBN:9781337619202Author:Hall, James A.Publisher:Cengage Learning,
- Horngren's Cost Accounting: A Managerial Emphasis...AccountingISBN:9780134475585Author:Srikant M. Datar, Madhav V. RajanPublisher:PEARSONIntermediate AccountingAccountingISBN:9781259722660Author:J. David Spiceland, Mark W. Nelson, Wayne M ThomasPublisher:McGraw-Hill EducationFinancial and Managerial AccountingAccountingISBN:9781259726705Author:John J Wild, Ken W. Shaw, Barbara Chiappetta Fundamental Accounting PrinciplesPublisher:McGraw-Hill Education
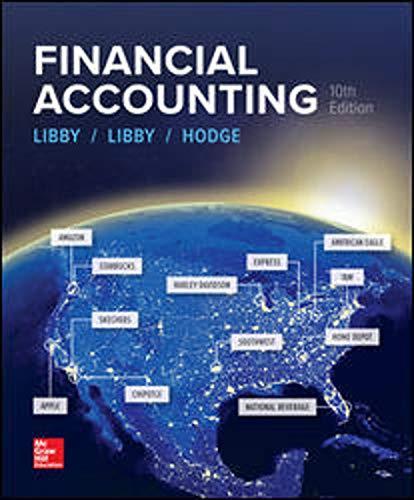
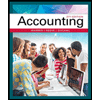
Accounting
Accounting
ISBN:9781337272094
Author:WARREN, Carl S., Reeve, James M., Duchac, Jonathan E.
Publisher:Cengage Learning,
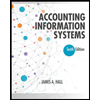
Accounting Information Systems
Accounting
ISBN:9781337619202
Author:Hall, James A.
Publisher:Cengage Learning,
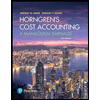
Horngren's Cost Accounting: A Managerial Emphasis...
Accounting
ISBN:9780134475585
Author:Srikant M. Datar, Madhav V. Rajan
Publisher:PEARSON
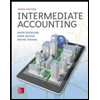
Intermediate Accounting
Accounting
ISBN:9781259722660
Author:J. David Spiceland, Mark W. Nelson, Wayne M Thomas
Publisher:McGraw-Hill Education
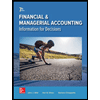
Financial and Managerial Accounting
Accounting
ISBN:9781259726705
Author:John J Wild, Ken W. Shaw, Barbara Chiappetta Fundamental Accounting Principles
Publisher:McGraw-Hill Education