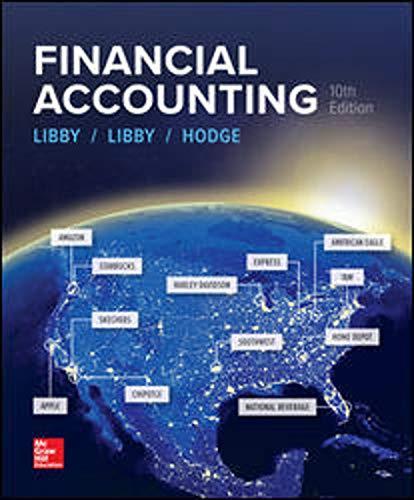
FINANCIAL ACCOUNTING
10th Edition
ISBN: 9781259964947
Author: Libby
Publisher: MCG
expand_more
expand_more
format_list_bulleted
Concept explainers
Question
Name of Budgeted Cost | Budgeted Cost | ||
Plant insurance | $ | 86,100 | |
Testing raw materials | 45,000 | ||
Manufacturing equipment setup | 7,200 | ||
Quality inspections | 57,000 | ||
Property taxes | 23,000 | ||
Electricity, plant | 14,000 | ||
Electricity, manufacturing equipment | 51,250 | ||
18,800 | |||
Depreciation, manufacturing equipment | 36,700 | ||
Maintenance worker (manufacturing equipment) | 22,500 | ||
Indirect labor (manufacturing equipment setup) | 8,300 | ||
Design engineering | 220,000 | ||
Required:
1. Assign each of the budgeted costs above to one of the following activity cost pools:
- Engineering
- Equipment setup
- Quality control
- Factory facilities
- Manufacturing equipment
2. Compute the total cost of each pool.
3. Indicate whether the activities in each pool are unit, batch, product, or facility level.
4. Identify the most likely driver for each cost pool from the following list:
- Number of inspections/tests
- Square feet
- Machine hours
- Engineering hours
- Number of setups
Use the following table to organize your answer. The engineering cost pool is done as an example. Other pools may have more than one cost item included.
How would i fill out the table?
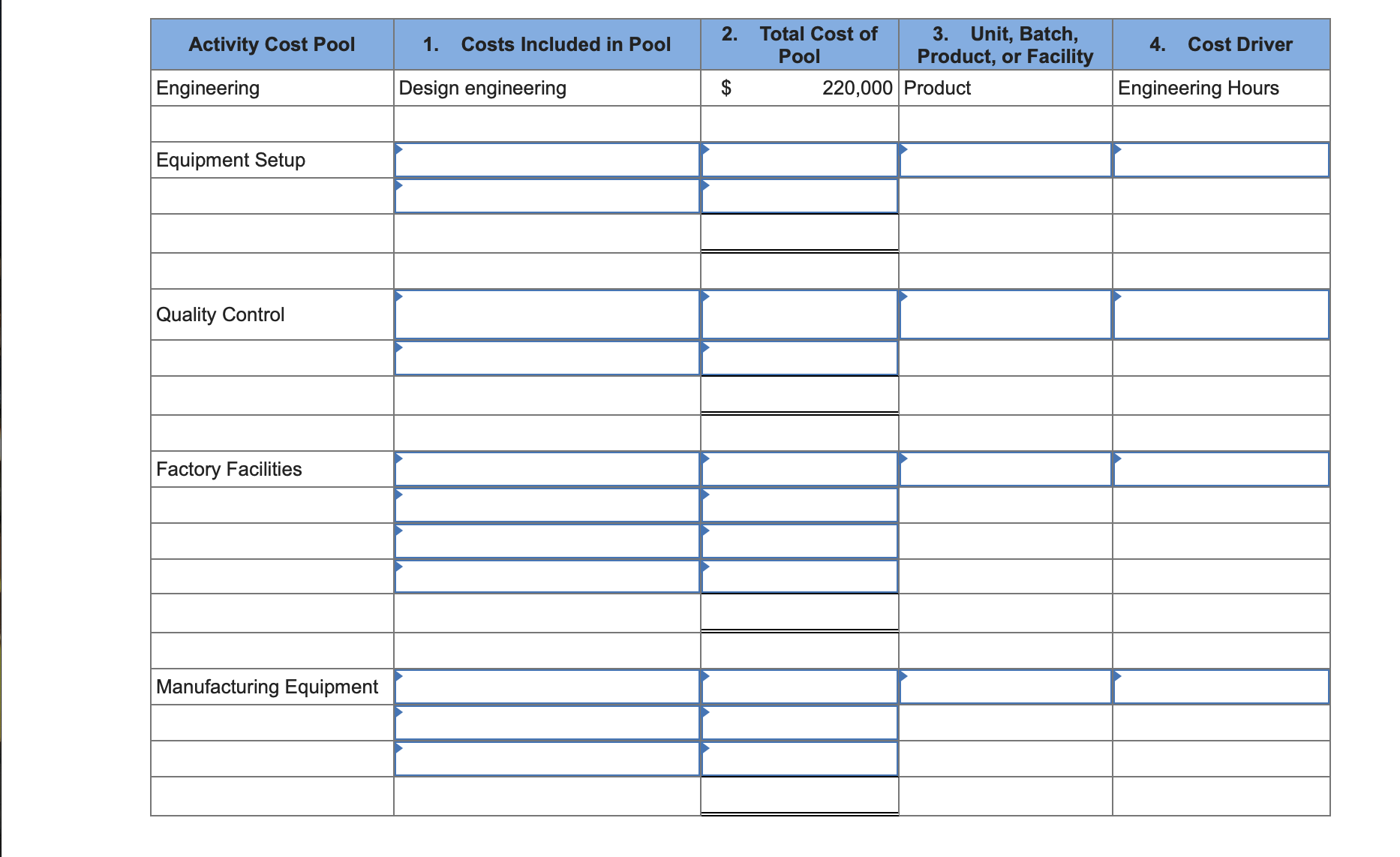
Transcribed Image Text:Total Cost of
Рool
3. Unit, Batch,
Product, or Facility
2.
Activity Cost Pool
1.
Costs Included in Pool
4.
Cost Driver
Design engineering
Engineering
$
220,000 Product
Engineering Hours
Equipment Setup
Quality Control
Factory Facilities
Manufacturing Equipment
Expert Solution

This question has been solved!
Explore an expertly crafted, step-by-step solution for a thorough understanding of key concepts.
This is a popular solution
Trending nowThis is a popular solution!
Step by stepSolved in 3 steps with 1 images

Knowledge Booster
Learn more about
Need a deep-dive on the concept behind this application? Look no further. Learn more about this topic, accounting and related others by exploring similar questions and additional content below.Similar questions
- Required information Use the following information for the Quick Studies below. (Algo) Rafner Manufacturing has the following budgeted data for its two production departments. Budgeted Data Overhead cost Direct labor hours Machine hours. Assembly 12,600 direct labor hours 5,400 machine hours Department Assembly Finishing Total $ 1,461,600 QS 17-8 (Algo) Allocating overhead with departmental rates LO P2 Allocate overhead to a job that uses 76 direct labor hours in the Assembly department and uses 62 machine hours in the Finishing department. Departmental Overhead Rate Hours Used $939,400 Finishing 19,400 direct labor hours 15,400 machine hours $ $ Overhead Allocated 0 0 0arrow_forwardActivity-Based Costing Steampunk Corporation has the following predicted indirect costs and cost drivers for 2019 for the given activity cost pools: FabricationDepartment FinishingDepartment Cost Driver Maintenance $ 36,000 18,000 Machine hours Materials handling 54,000 27,000 Material moves Machine 126,000 9,000 Machine setups Inspections - 45,000 Inspection hours Total $ 216,000 $ 99,000 The following activity predictions were also made for the year: FabricationDepartment FinishingDepartment Machine hours 5,000 2,500 Material moves 1,500 750 Machine setups 350 25 Inspection hours - 500 It is assumed that the cost per unit of activity for a given activity does not vary between departments. Steampunk's president, Abner Punk, is trying to evaluate the company's product mix strategy regarding two of its product models, SW100 and SG150. The company has been using a company wide overhead rate based on machine hours but is considering…arrow_forwardSilven Company has identified the following overhead activities, costs, and activity drivers for the coming year: Activity Expected Cost Activity Driver Activity Capacity $138,000 Number of setups 10,200 Number of orders 92,400 Machine hours 18,480 Receiving hours phones with the following expected activity demands: Setting up equipment Ordering materials Machining Receiving Silven produces two models of cell Model X 5,000 80 200 6,600 385 Units completed Number of setups Number of orders Machine hours Receiving hours Required: Model Y 10,000 40 400 4,950 770 120 600 11,550 1,155arrow_forward
- Support department cost allocation-direct method Becker Tabletops has two support departments (Janitorial and Cafeteria) and two production departments (Cutting and Assembly). Relevant detail Support Department Cost Driver Square footage to be serviced Janitorial Department Cafeteria Department Number of employees Janitorial Department $310,000 Cafeteria Department $169,000 5,000 3 Janitorial Department cost allocation. Cafeteria Department cost allocation Cutting Department $1,504,000 Department costs Square feet 50 1,000 Number of employees 10 30 Allocate the support department costs to the production departments using the direct method. Cutting Department Assembly Department $580,000 4,000 10 Assembly Departmentarrow_forwardA local picnic table manufacturer has budgeted these overhead costs - ERROR: "Handling materials" is $33,350 - (note their order as you will use the same order down below): Purchasing Handling materials Machine setups $70,000 33,333 70,500 25,500 45,000 Inspections Utilities They are considering adapting ABC costing and have estimated the cost drivers for each pool as shown (again, note their order): Cost Driver Activity Orders 700 Material moves Machine setups Number of inspections Square feet 1,334 15,000 5,000 180,000 Recent success has yielded an order for 1,000 tables. Assume direct labor costs per hour of $20. Determine how much the job would cost given the following activities (once more, note their order for the last worksheet): Activity Order (units) Direct materials 1,000 112,700 15,200 5,300 60 Machine hours Direct labor hours Number of purchase orders Number of material moves Number of machine setups Number of inspections Number of square feet occupied 800 100 450 8,000…arrow_forwardFrom the schedule below provided for quality control activities, determine the appraisal costs: Quality control activities Activity cost Finished goods inspection $12,000 Product design $22,000 Rework $8,900 Processing returned products $21,000 Training of machine operators $25,000 Process audit $32,000 $29.900 $33,000 $66.000 $44.000arrow_forward
- Journalize the following transactions: Materials used in production, $40,000 Paid plant supervisor’s salary, $6,000 Plant depreciation, $10,000 Production labor costs incurred, $80,000 MOH is allocated at the rate of 120% of direct labor costs Cost of goods manufactured, $200,000 Revenue on account, $450,000 Cost of goods sold, $300,000 Paid advertising costs, $90,000arrow_forwardBudgeted Data Assembly Finishing $ 3,600,000 12,000 direct labor hours 4,000 machine hours Overhead cost 2,400,000 Direct labor hours 20,000 direct labor hours Machine hours 16,000 machine hours 0:50:37 Compute the company's single plantwide overhead rate based on direct labor hours. Multiple Choice $150.00 per direct labor hour. $900.00 per direct labor hour. $300.00 per direct labor hour. $225.00 per direct labor hour. $187.50 per direct labor hour.arrow_forwardYou are in charge of the following cost Budgeted production in units: 10,000 Budgeted Cost: Indirect Materials Indirect Labor Utilities Depreciation Property Taxes Supervision 5 250,000 $ 260,000 $ 190,000 $ 280,000 70,000 50,000 S 1,100,000 Demand has increased 12,000 Actual Cost Indirect Materials $ 295,000 $ 312,000 5 225,000 S 280,000 70,000 50,000 5 1,232,000 Indirect Labor Utilities Depreciation Property Taxes Supervision Your manager put the following table together: Budget Actual Variance production in units: 10,000 12,000 Frfavorable U-Unfavcrable Budgeted Cost: Indirect Materials Indirect Labor $ 295,000 S 312,000 S 225,000 S 280,000 S 70,000 5 50.000 $1,232.000 $ 45,000 $ 52,000 $ 35,000 Utilities Depreciation Property Taxes Supervision 250,000 S 260,000 S 190,000 S 280,000 70,000 %24 50,000 S 1,100,000 S 132,000 Requirement: Looking at the table, he is very dissatisfied with your performance. Should he fire you today? Please explain. Show calculations where necessary.arrow_forward
arrow_back_ios
arrow_forward_ios
Recommended textbooks for you
- AccountingAccountingISBN:9781337272094Author:WARREN, Carl S., Reeve, James M., Duchac, Jonathan E.Publisher:Cengage Learning,Accounting Information SystemsAccountingISBN:9781337619202Author:Hall, James A.Publisher:Cengage Learning,
- Horngren's Cost Accounting: A Managerial Emphasis...AccountingISBN:9780134475585Author:Srikant M. Datar, Madhav V. RajanPublisher:PEARSONIntermediate AccountingAccountingISBN:9781259722660Author:J. David Spiceland, Mark W. Nelson, Wayne M ThomasPublisher:McGraw-Hill EducationFinancial and Managerial AccountingAccountingISBN:9781259726705Author:John J Wild, Ken W. Shaw, Barbara Chiappetta Fundamental Accounting PrinciplesPublisher:McGraw-Hill Education
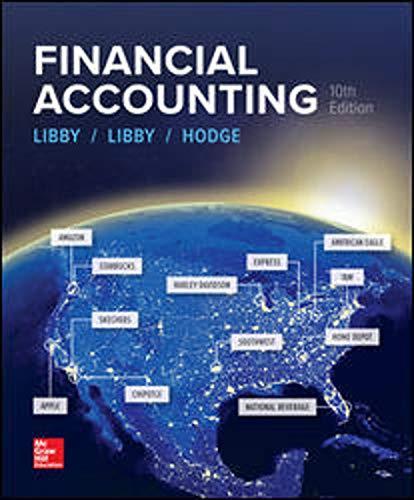
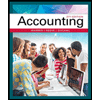
Accounting
Accounting
ISBN:9781337272094
Author:WARREN, Carl S., Reeve, James M., Duchac, Jonathan E.
Publisher:Cengage Learning,
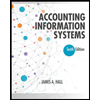
Accounting Information Systems
Accounting
ISBN:9781337619202
Author:Hall, James A.
Publisher:Cengage Learning,
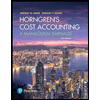
Horngren's Cost Accounting: A Managerial Emphasis...
Accounting
ISBN:9780134475585
Author:Srikant M. Datar, Madhav V. Rajan
Publisher:PEARSON
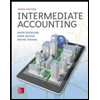
Intermediate Accounting
Accounting
ISBN:9781259722660
Author:J. David Spiceland, Mark W. Nelson, Wayne M Thomas
Publisher:McGraw-Hill Education
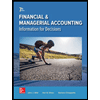
Financial and Managerial Accounting
Accounting
ISBN:9781259726705
Author:John J Wild, Ken W. Shaw, Barbara Chiappetta Fundamental Accounting Principles
Publisher:McGraw-Hill Education