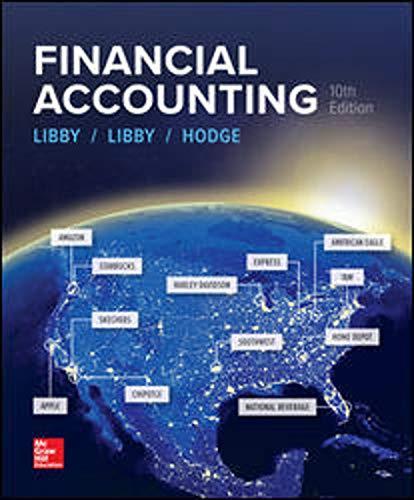
FINANCIAL ACCOUNTING
10th Edition
ISBN: 9781259964947
Author: Libby
Publisher: MCG
expand_more
expand_more
format_list_bulleted
Question
A company processes raw material into Products R, B, T and D. Products R, B and T are joint products and D is classified as a by-product.
In process 1, 50 000 kg of material will be processed at a cost of R220 600 worth of material, R40 500 labour and R24 500 overheads. After the basic processing in process 1, thirty percent of the input is transferred to process B. In Process B additional costs of R25 400 are incurred and product B (from process B) can then be sold for R28 per kg.
They transfer 60% of the original material input (from process 1) to process 2 and then the remainder to Process D. The products in process D are considered a by-product (By-product D) and have a sales price of R6 per kilogram. The cost involved with the selling of the by-product is R7 000 in total. The business account for this by crediting the net market value of by-products produced to the general production costs.
In process 2 the materials processed further at a cost of R21 200. They then transfer 60% of the material in process 2 to process R where additional processing is done at R62 400. They can sell Product R (from process R) for R35 per kilogram.
They transfer the remainder of the materials of process 2 to process T where they incur additional costs of R12 800. Product T (from Process T) has a sales value of R29 per kilogram.
3
Calculate the total production cost of every product type.
Expert Solution

This question has been solved!
Explore an expertly crafted, step-by-step solution for a thorough understanding of key concepts.
This is a popular solution
Trending nowThis is a popular solution!
Step by stepSolved in 2 steps with 2 images

Knowledge Booster
Similar questions
- The cost of direct materials transferred into the Rolling Department of Kraus Company is $3,000,000. The conversion cost for the period in the Rolling Department is $462,600. The total equivalent units for direct materials and conversion are 4,000 tons and 3,855 tons, respectively. Determine the direct materials and conversion costs per equivalent unit.arrow_forwardNorthern Company processes 100 gallons of raw materials into 75 gallons of product GS-50 and 25 gallons of GS-80. GS-50 is further processed into 50 gallons of product GS-505 at a cost of $7,250, and GS-80 is processed into 50 gallons of product GS-805 at a cost of $5,750. The production process starts at point 1. A total of $20,000 in joint manufacturing costs are incurred in reaching point 2. Point 2 is the split-off point of the process that manufactures GS-50 and GS-80. At this point, GS-50 can be sold for $725 a gallon, and GS-80 can be sold for $145 a gallon. The process is completed at point 3-products GS-505 and GS-805 have a sales price of $585 a gallon and $225 a gallon, respectively. Required: Allocate the joint product costs and then compute the cost per unit using each of the following methods: (1) physical measure, (2) sales value at split-off, and (3) net realizable value. (Do not round intermediate calculations. Round your final answers to nearest whole dollar amount.)…arrow_forwardThe Marshall Company has a joint production process that produces two joint products and a by-product. The joint products are Ying and Yang, and the by-product is Bit. Marshall accounts for the costs of its products using the net realizable value method. The two joint products are processed beyond the split-off point, incurring separable processing costs. There is a $1,500 disposal cost for the by- product. A summary of a recent month's activity at Marshall is shown below: Ying 75,000 75,000 $ 210,000 $ 15,000 $ 6.00 Total joint costs for Marshall in the recent month are $211,000, of which $90,730 is a variable cost. Units sold Units produced Separable processing costs-variable Separable processing costs-fixed Sales price Manufacturing cost per unit Total gross margin Yang 60,000 60,000 $ 65,000 $ 10,000 $ 12.50 Required: 1. Calculate the manufacturing cost per unit for each of the three products. (Round manufacturing cost per unit answers to 2 decimal places.) 2. Calculate the total…arrow_forward
- Lawn Products produces two products (X and Y) and a by-product (Z) from a joint process using a raw material (Alpha). The company chooses to allocate the costs on the basis of the physical quantities method. Last month, it processed 26,000 pounds of Alpha at a total cost of $102,000. The output of the process consisted of 30,150 units of product X, 36,850 units of product Y, and 7,400 units of by-product Z. By-product Z can be sold for $10,800. This is considered to be its net realizable value, which is deducted from the processing costs of the main products. Required: What amount of joint costs should be assigned to each of product X and product Y?arrow_forwardam.1234.arrow_forwardCullumber Inc. manufactures a single product in a continuous processing environment. All materials are added at the beginning of the process, and conversion costs are incurred uniformly throughout the process. To assign costs to inventories, the company uses weighted-average process costing. The following information was available for 2022: Sales (selling price per unit, $43) Actual manufacturing overhead Selling and administrative expenses Unit production costs: Direct materials (1 kilogram) Direct labour (1/2 hour) Manufacturing overhead Total $5,000,900 752,400 373,920 $6.00 8.00 9.00 $23.00 Units completed and transferred to finished goods Materials purchased Materials used in process (a) Raw materials Work in process inventory (45% complete) Finished goods An inventory count at year end (December 31, 2022) revealed that the inventories had the following balances: Calculate the following amounts for Cullumber Inc.: 159,600 units The January 1, 2022, work in process inventory units…arrow_forward
arrow_back_ios
arrow_forward_ios
Recommended textbooks for you
- AccountingAccountingISBN:9781337272094Author:WARREN, Carl S., Reeve, James M., Duchac, Jonathan E.Publisher:Cengage Learning,Accounting Information SystemsAccountingISBN:9781337619202Author:Hall, James A.Publisher:Cengage Learning,
- Horngren's Cost Accounting: A Managerial Emphasis...AccountingISBN:9780134475585Author:Srikant M. Datar, Madhav V. RajanPublisher:PEARSONIntermediate AccountingAccountingISBN:9781259722660Author:J. David Spiceland, Mark W. Nelson, Wayne M ThomasPublisher:McGraw-Hill EducationFinancial and Managerial AccountingAccountingISBN:9781259726705Author:John J Wild, Ken W. Shaw, Barbara Chiappetta Fundamental Accounting PrinciplesPublisher:McGraw-Hill Education
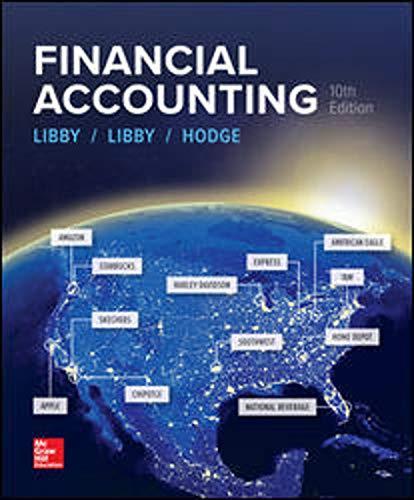
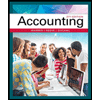
Accounting
Accounting
ISBN:9781337272094
Author:WARREN, Carl S., Reeve, James M., Duchac, Jonathan E.
Publisher:Cengage Learning,
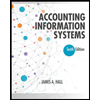
Accounting Information Systems
Accounting
ISBN:9781337619202
Author:Hall, James A.
Publisher:Cengage Learning,
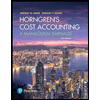
Horngren's Cost Accounting: A Managerial Emphasis...
Accounting
ISBN:9780134475585
Author:Srikant M. Datar, Madhav V. Rajan
Publisher:PEARSON
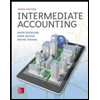
Intermediate Accounting
Accounting
ISBN:9781259722660
Author:J. David Spiceland, Mark W. Nelson, Wayne M Thomas
Publisher:McGraw-Hill Education
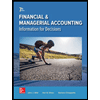
Financial and Managerial Accounting
Accounting
ISBN:9781259726705
Author:John J Wild, Ken W. Shaw, Barbara Chiappetta Fundamental Accounting Principles
Publisher:McGraw-Hill Education