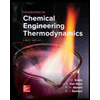
The reaction of solid calcium fluoride and sulfuric acid produces calcium sulfate solids and gaseous HF. The gas product is dissolved in water to form hydrofluoric acid. Fluorite ore, a source of calcium fluoride, contains 95%wt CaF2 and 5%wt SiO2.
In a certain process, the ore is reacted with 93%wt aqueous sulfuric acid, supplied 15% in excess. From this, 95% of the ore dissolves in the acid. Some of the HF formed reacts with the dissolved silica in the reaction: HF reacts with SiO2 to produce H2SiF6 and liquid water.
If 60%wt of hydrofluoric acid was formed when hydrogen fluoride (which exits the reactor) is dissolved in water, determine the amount of ore needed to produce one metric ton of acid.

Step by stepSolved in 5 steps with 21 images

- An engine is using hydrocarbon for fuel at a barometric pressure of 540 mmHg absolute. The air is practically dry at a temperature of 20°F. The exhaust gases leave the engine at 1000°F. The Orsat analysis of the combustion gas is conducted at 25°C and 750 mmHg and shows 15.39% CO2, 1.67% O2, 82.94%N2. Calculate a) the percent excess air, b) atom carbon to atom hydrogen ratio in the fuel, and c) the liters of exhaust gases, under the conditions they leave the engine, per liter of air entering the air intake.arrow_forwardCrude petroleum oil is generally considered to be formed from animal and vegetable debris accumulating in sea basins orestuaries and decomposed by anaerobic bacteria resulting in a black viscous product. A typical elemental analysis shows 80%C, 13% H, 1% N, 3% O, and 3% S. During a certain combustion, air supplied is less than the theoretical so that all of theO2is used up. 70% of the C burns toCO2, the rest to CO; the molal ratio of CO toH2in the exhaust gas is 1:2.Assume that the Sulfur in the fuel burns toSO2and the Nitrogen combines with the nitrogen from air. Calculate:a)Orsat analysis of the exhaust gasb)% of the theoretical air which is supplied for combustioarrow_forwardprovide diagramarrow_forward
- Biodiesel from a palm oil has an approximate formula of CxHyOz. Excess air is supplied at 30°C, 100kPa and 85%RH. The exhaust gas leaves at 250°C and 750 mm Hg with a complete analysis of 12.08% CO2, 0.25% CO, 0.55% H2, 2.12% O2, 71.17% N2 and the rest is H2O. Finda) formula of biodiesel (C19H34O2)b) Equivalence Ratio (0.91)arrow_forwardThe pressure of methane (CH4) and acetylene (C2H2) gas mixture in a container is 70.5 torr. This gas mixture is burned with sufficient O2 and converted to CO2 and H2O. The H2O and excess O2 in the environment are removed and only CO2 is left in the container. Since the pressure of CO2 is 96.4 torr at the same temperature, what is the mole fraction of acetylene in the starting gas mixture?arrow_forwardBlast furnace gas is a by-product in converting iron ore to metallic iron using metallurgical coke. A blast furnace gas extracted from a blast furnace is composed of 30% N2, 32% CO, 12% CO2, 8% H₂O and 18% H2. This fuel gas contains high carbon monoxide content and low heating value but can be used as fuel within the steel works and sometimes combined with natural gas to sustain combustion. If 100 mol of the fuel gas is burned with 250 mol of air, what is the percent excess air supplied?arrow_forward
- Ammonia is oxidized in a continuous reactor 4NH3 g + 5O2 g --> 4NO g + 6H2O g delta AHr= -904.7KJ mol The feed stream (40 mole% NH3 and 60 mole% O2 )enters the reactor at 200 degrees celsius with 80% conversion of ammonia and the products leave at 300 degrees celsius. Determine the quantity of heat required to be added or removed from the reactor.arrow_forwardAcetaldehyde is synthesized by the catalytic dehydrogenation of ethanol: Fresh feed (pure ethanol) is blended with a recycle stream (95 mole% ethanol and 5% acetaldehyde), and the combined stream is heated and vaporized, entering the reactor at 280°C. Gases leaving the reactor are cooled to condense the acetaldehyde and unreacted ethanol. Off-gas from the condenser is sent to a scrubber, where the uncondensed organic compounds are removed and hydrogen is recovered as a by-product. The condensate from the condenser, which is 45 mole% ethanol, is sent to a distillation column that produces a distillate containing 99 mole% acetaldehyde and a bottoms product that constitutes the recycle blended with fresh feed to the process. The production rate of the distillate is 1000 kg/h. The pressure throughout the process may be taken as 1 atm absolute. Calculate the flow rate of the distillate in mol/s (use the actual composition of the distillate, 99 mole% acetaldehyde and 1 mole%…arrow_forwardAcetaldehyde is synthesized by the catalytic dehydrogenation of ethanol: Fresh feed (pure ethanol) is blended with a recycle stream (95 mole% ethanol and 5% acetaldehyde), and the combined stream is heated and vaporized, entering the reactor at 280°C. Gases leaving the reactor are cooled to condense the acetaldehyde and unreacted ethanol. Off-gas from the condenser is sent to a scrubber, where the uncondensed organic compounds are removed and hydrogen is recovered as a by-product. The condensate from the condenser, which is 45 mole% ethanol, is sent to a distillation column that produces a distillate containing 99 mole% acetaldehyde and a bottoms product that constitutes the recycle blended with fresh feed to the process. The production rate of the distillate is 1000 kg/h. The pressure throughout the process may be taken as 1 atm absolute. Assume that the vapor leaving the top tray of the distillation column is at 475 K and 1 atm, contains the same molar composition as the distillate,…arrow_forward
- A countercurrent extraction system uses 3 steps for acid extraction acetic acid/water/isopropyl ether at 20°C and 1 atm. The feed consists of 40% (by mass) of acetic acid and 60% (by mass) of water. The feed is 2000 kg/h. The solvent used contains 1% (by mass) of acetic acid. It is necessary that the raffinate at the exit of the extractor contains 5% of acetic acid (by mass). Determine: The amount of solvent, extract in MS and raffinate R1 Equilibrium data: Equilibrium diagrams of the ternary system: acetic acid/water/isopropyl ether(in mass fractions at 20°C and 1 atm).arrow_forwardAmmonia is oxidized in a continuous reactor 4NH3 g + 5O2 g --> 4NO g + 6H2O g delta AHr= -904.7KJ mol The feed stream (40 mole% NH3 and 60 mole% O2 )enters the reactor at 200 degrees celsius with 80% conversion of ammonia and the products leave at 300 degrees celsius. Determine the quantity of heat required to be added or removed from the reactor. The basis of calculation: 10mol/s of feed stream. given: the constant heat capacity, Cp, of NH3(g), O2(g), NO(g), and H2O(v) are 0.035, 0.029, 0.029 and 0.033KJ/ mol. degrees celsius respectively.) Cp O2 or table 8 for the calculation. can you please explaing each steparrow_forwardAcetaldehyde is synthesized by the catalytic dehydrogenation of ethanol: Fresh feed (pure ethanol) is blended with a recycle stream (95 mole% ethanol and 5% acetaldehyde), and the combined stream is heated and vaporized, entering the reactor at 280°C. Gases leaving the reactor are cooled to condense the acetaldehyde and unreacted ethanol. Off-gas from the condenser is sent to a scrubber, where the uncondensed organic compounds are removed and hydrogen is recovered as a by-product. The condensate from the condenser, which is 45 mole% ethanol, is sent to a distillation column that produces a distillate containing 99 mole% acetaldehyde and a bottoms product that constitutes the recycle blended with fresh feed to the process. The production rate of the distillate is 1000 kg/h. The pressure throughout the process may be taken as 1 atm absolute. If the vapor leaving the condenser (off-gas to scrubber) is at -40 ̊C and 760 torr, what is the molar composition of this stream?What…arrow_forward
- Introduction to Chemical Engineering Thermodynami...Chemical EngineeringISBN:9781259696527Author:J.M. Smith Termodinamica en ingenieria quimica, Hendrick C Van Ness, Michael Abbott, Mark SwihartPublisher:McGraw-Hill EducationElementary Principles of Chemical Processes, Bind...Chemical EngineeringISBN:9781118431221Author:Richard M. Felder, Ronald W. Rousseau, Lisa G. BullardPublisher:WILEYElements of Chemical Reaction Engineering (5th Ed...Chemical EngineeringISBN:9780133887518Author:H. Scott FoglerPublisher:Prentice Hall
- Industrial Plastics: Theory and ApplicationsChemical EngineeringISBN:9781285061238Author:Lokensgard, ErikPublisher:Delmar Cengage LearningUnit Operations of Chemical EngineeringChemical EngineeringISBN:9780072848236Author:Warren McCabe, Julian C. Smith, Peter HarriottPublisher:McGraw-Hill Companies, The
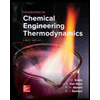
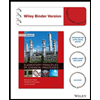
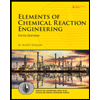
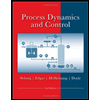
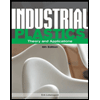
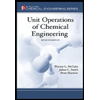