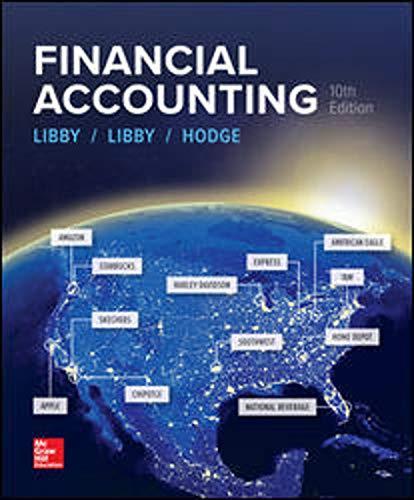
Concept explainers
The Enhanced Products Division of Forrest Industries makes ceramic pots that are used to hold large decorative plants. During 2013, the division produced 10,000 pots and incurred the following costs:
unit-level material costs (10,000@ $15) $15,000
unit-level labor costs (10,000@ $20) $200,000
Unit-level
Other manufacturing overhead ** $36,000
*The equipment was purchased for $150,000 and has a current book value of $120,000, remaining useful life of four years, and a zero salvage value. If the company does not use the equipment, it can be leased for $8,000 per year.
**Includes supervisors' salaries and rent for manufacturing plant.
The division is considering replacing the equipment used to manufacture its ceramic pots. Replacement equipment can be purchased at a price of $200,000. The new equipment, which is expected to last 4 years and have a salvage value of $20,000, will reduce unit-level labor costs by 25 percent.
The division desires to maintain its production and sales at 10,000 ceramic pots per year:
c) True or False: The existing equipment should be replaced.

Step by stepSolved in 2 steps with 1 images

- Cullumber Water Co. is a leading producer of greenhouse irrigation systems. Currently, the company manufactures the timer unit used in each of its systems. Based on an annual production of 52,000 timers, the company has calculated the following unit costs. Direct fixed costs include supervisory and clerical salaries and equipment depreciation. Direct materials Direct labor Variable manufacturing overhead Direct fixed manufacturing overhead Allocated fixed manufacturing overhead Total unit cost $12 7 4 9 541 10 (30% salaries, 70% depreciation) Clifton Clocks has offered to provide the timer units to Cullumbet at a price of $36 per unit. If Cullumber accepts the offer, the current timer unit supervisory and clerical staff will be laid offarrow_forwardPart U16 is used by Mcvean Corporation to make one of its products. A total of 17,000 units of this part are produced and used every year. The company's Accounting Department reports the following costs of producing the part at this level of activity: Per Unit Direct materials $ 3.70 Direct labor $ 8.30 Variable manufacturing overhead $ 8.80 Supervisor's salary $ 4.20 Depreciation of special equipment $ 2.60 Allocated general overhead $ 7.80 An outside supplier has offered to make the part and sell it to the company for $27.90 each. If this offer is accepted, the supervisor's salary and all of the variable costs, including the direct labor, can be avoided. The special equipment used to make the part was purchased many years ago and has no salvage value or other use. The allocated general overhead represents fixed costs of the entire company, none of which would be avoided if the part were purchased instead of produced internally. In addition, the space used to…arrow_forwardE7-6 Jobs, Inc. has recently started the manufacture of Tri-Robo, a three-wheeled robot that can scan a home for fi res and gas leaks and then transmit this information to a mobile phone. The cost structure to manufacture 20,000 Tri-Robos is as follows. CostDirect materials ($50 per robot) $1,000,000Direct labor ($40 per robot) 800,000Variable overhead ($6 per robot) 120,000Allocated fi xed overhead ($30 per robot) 600,000Total $2,520,000Jobs is approached by Tienh Inc., which offers to make Tri-Robo for $115 per unit or $2,300,000.Instructions(a) Using incremental analysis, determine whether Jobs should accept this offer under each of the…arrow_forward
- Part "Mendes" is used in one of Shawn's products. The company's Accounting Department reports the following costs of producing the 12,000 units of the part that are needed every year. Direct Materials $4.79 Direct labor $1.16 Variable overhead $2.68 Supervisor's salary $3.38 Depreciation of special equipment $2.67 Allocated general overhead $1.54 An outside supplier has offered to make the part and sell it to the company for $14.86 each. If this offer is accepted, the supervisor's salary and all of the variable costs, including direct labor, can be avoided. The special equipment used to make the part was purchased many years ago and has no salvage value or other use. The allocated general overhead represents fixed costs of the entire company. If the outside supplier's offer were accepted, only $5651 of these allocated general overhead costs would be avoided. What would be the impact on total net income if Shawn accepted the supplier's offer? Round only your final answer to the nearest…arrow_forwardOtsego Industries manufactured 300,000 units of product last year and identified the following costs associated with the manufacturing activity: Variable costs: Direct materials used Direct labor Indirect materials and supplies Power to run plant equipment Fixed costs: Supervisory salaries Plant utilities (other than for plant equipment) Depreciation on plant and equipment Property taxes on building Answer is not complete. $ 10,965.00 $ 8,160.00 $ 19,125.00 ($000) $ 6,120.0 4,060.0 1,420.0 1,300.0 Required: Unit variable costs and total fixed costs are expected to remain unchanged in the following year. However, management expects a slowdown in sales, because of the economy in the following year. Calculate the unit cost and the total cost if 255,000 units are produced next year. Note: Enter your total cost answers in thousands. Round your answers to 2 decimal places. Total variable costs Total fixed costs Total costs Unit costs $ 2,460.0 1,896.7 2,285.0 1,518.3arrow_forwardThe Enhanced Products Division of Forrest Industries makes ceramic pots that are used to hold large decorative plants. During 2013, the division produced 10,000 pots and incurred the following costs: unit-level material costs (10,000@ $15) $15,000 unit-level labor costs (10,000@ $20) $200,000 Unit-level overhead costs (10,000 @16) $160,000 Depreciation expenses on equipment* $30,000 Other manufacturing overhead ** $36,000 *The equipment was purchased for $150,000 and has a current book value of $120,000, remaining useful life of four years, and a zero salvage value. If the company does not use the equipment, it can be leased for $8,000 per year.**Includes supervisors' salaries and rent for manufacturing plant.The division is considering replacing the equipment used to manufacture its ceramic pots. Replacement equipment can be purchased at a price of $200,000. The new equipment, which is expected to last 4 years and have a salvage value of…arrow_forward
- Howell Corporaon produces an execuve jet for which it currently manufactures a fuel valve; the cost ofthe valve is indicated below:Cost per UnitVariable costsDirect material $900Direct labor 600Variable overhead 300Fixed costsDepreciaon of equipment 500Depreciaon of building 200Supervisory salaries 300The company has an offer from Duvall Valves to produce the part for $2,000 per unit and supply 1,000 valves(the number needed in the coming year). If the company accepts this offer and shuts down producon ofvalves, producon workers and supervisors will be reassigned to other areas. The equipment cannot be usedelsewhere in the company, and it has no market value. However, the space occupied by the producon of thevalve can be used by another producon group that is currently leasing space for $55,000 per year.What is the incremental savings of buying the valves? (The answer should be stated in a per‐unit format and is a positive number)arrow_forwardVikarmbhaiarrow_forward(Management Accounting) Davidson Company produces a part that is used in the manufacture of one of its products. The costs associated with the production of 5,000 units of this part are as follows: Direct materials $108,000 Direct labor 156,000 Variable factory overhead 70,000 Fixed factory overhead 168,000 Total costs $502,000 Of the fixed factory overhead costs, $72,000 are avoidable. Assuming there is no other use for the facilities. What is the highest price Davidson Company should be willing to pay for 5,000 units of the part? A) $264,000 B) $334,000 C) $406,000 D) $502,000arrow_forward
- Vernon Bike Company makes the frames used to build its bicycles. During Year 2, Vernon made 22,000 frames; the costs incurred follow. Unit - level materials costs (22,000 units \times $48) $ 1,056, 000 Unit - level labor costs (22,000 units \times $53) 1, 166,000 Unit - level overhead costs (22,000 \times $ 12) 264,000 Depreciation on manufacturing equipment 99,000 Bike frame production supervisor's salary 75, 800 Inventory holding costs 289,000 Allocated portion of facility - level costs 580,000 Total costs $ 3,529,800 Vernon has an opportunity to purchase frames for $110 each. Additional Information The manufacturing equipment, which originally cost $500,000, has a book value of $450,000, a remaining useful life of four years, and a zero salvage value. If the equipment is not used to produce bicycle frames, it can be leased for $78, 000 per year. Vernon has the opportunity to purchase for $960,000 new manufacturing equipment that will have an expected useful life of four years and a…arrow_forwardU-RIDE, Incorporated currently produces the electric engines that are used in golf carts made and sold by the Company. Electco has offered to sell the electric engines to U-RIDE at a price of $291 each. Current production information follows: Unit-level material and labor $240 Facility-level depreciation of manufacturing equipment Product-level engine production supervisor's salary $6,300 /month $3,300 /month $21,500 Annual facility-level utilities U-RIDE is currently operating profitably producing and selling 3,300 engines a year using 80% of its manufacturing capacity. Which of the following is true? Multiple Choice O O U-RIDE should make the engines for cost savings of $51 per unit. Buying the units would increase U-RIDE's cost by $39 per unit. U-RIDE has avoidable costs of greater than $291 per unit and should therefore buy the engines. Buying the units would increase profitability by $90 per unit.arrow_forwardMoss Ltd. has the following activities: creating bills of materials (BOM), studying manufacturing capabilities, improving manufacturing processes, training employees, and designing tooling. The general ledger accounts reveal the following expenditures for manufacturing engineering: Salaries £ 75,000Equipment 40,000Supplies __10,000 Total £125,000 The equipment is used for two activities: improving processes and designing tooling. Thirty-five percent of the equipment's time is used for improving processes and 65 percent is used for designing tools. The salaries are for two engineers. One is paid £50,000, while the other earns £25,000. The £50,000 engineer spends 40 percent of his time training employees in new processes and 60 percent of his time on improving processes. The remaining engineer spends equal time on all activities. Supplies are consumed in the following proportions: Creating BOMs 25%Studying capabilities 10%Improving processes 20%Training employees 25%Designing tooling…arrow_forward
- AccountingAccountingISBN:9781337272094Author:WARREN, Carl S., Reeve, James M., Duchac, Jonathan E.Publisher:Cengage Learning,Accounting Information SystemsAccountingISBN:9781337619202Author:Hall, James A.Publisher:Cengage Learning,
- Horngren's Cost Accounting: A Managerial Emphasis...AccountingISBN:9780134475585Author:Srikant M. Datar, Madhav V. RajanPublisher:PEARSONIntermediate AccountingAccountingISBN:9781259722660Author:J. David Spiceland, Mark W. Nelson, Wayne M ThomasPublisher:McGraw-Hill EducationFinancial and Managerial AccountingAccountingISBN:9781259726705Author:John J Wild, Ken W. Shaw, Barbara Chiappetta Fundamental Accounting PrinciplesPublisher:McGraw-Hill Education
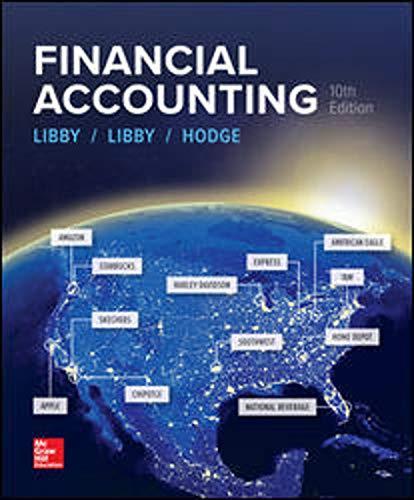
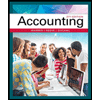
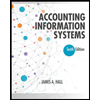
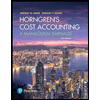
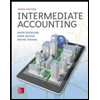
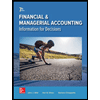