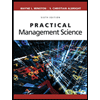
Practical Management Science
6th Edition
ISBN: 9781337406659
Author: WINSTON, Wayne L.
Publisher: Cengage,
expand_more
expand_more
format_list_bulleted
Question
I have little experience in Excel with formulas and have never used Solver before. How can the attached information be entered into Solver in Excel? I have added information to help.
Decision Variables
Cakes (x1)
Danishes (x2)
Objective Function
Max Z = $1x1 + 5x2
Constraints
5x1 + 5x2 ≤ 25 (flour, lb.)
2x1 + 4x2 ≤ 16 (sugar, lb.)
x1 ≤ 5 (demand, cakes)
x1 , x2 ≥ 0
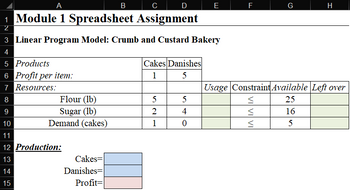
Transcribed Image Text:A
B
C D
E
1 Module 1 Spreadsheet Assignment
2
3 Linear Program Model: Crumb and Custard Bakery
4
FL
G
H
5 Products
Cakes Danishes
6 Profit per item:
1
5
7 Resources:
Usage Constraint Available Left over
8
Flour (lb)
5
5
<
25
9
Sugar (lb)
2
4
16
10
Demand (cakes)
1
0
5
11
12 Production:
13
Cakes=
14
Danishes=
15
Profit=
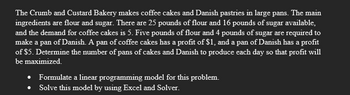
Transcribed Image Text:The Crumb and Custard Bakery makes coffee cakes and Danish pastries in large pans. The main
ingredients are flour and sugar. There are 25 pounds of flour and 16 pounds of sugar available,
and the demand for coffee cakes is 5. Five pounds of flour and 4 pounds of sugar are required to
make a pan of Danish. A pan of coffee cakes has a profit of $1, and a pan of Danish has a profit
of $5. Determine the number of pans of cakes and Danish to produce each day so that profit will
be maximized.
Formulate a linear programming model for this problem.
Solve this model by using Excel and Solver.
Expert Solution

This question has been solved!
Explore an expertly crafted, step-by-step solution for a thorough understanding of key concepts.
Step by stepSolved in 2 steps

Knowledge Booster
Similar questions
- The local supermarket buys lettuce each day to ensure very fresh produce. Each morning, any lettuce that is left from the previous day is sold to a dealer that resells it to farmers who use it to feed their animals. This week, the supermarket can buy fresh lettuce for $4 a box. The lettuce is sold for $10 a box and the dealer that sells old lettuce is willing to pay $1.50 a box. Past history says that tomorrow’s demand for lettuce averages 250 boxes, with a standard deviation of 34 boxes. How many boxes of lettuce should the supermarket purchase tomorrow?arrow_forward49 The local supermarket buys lettuce each day to ensure really fresh produce. Each morning, any lettuce that is left from the previous day is sold to a dealer that resells it to farmers who use it to feed their animals. This week, the supermarket can buy fresh lettuce for $7.00 a box. The lettuce is sold for $18.00 a box and the dealer that sells old lettuce is willing to pay $2.00 a box. Past history says that tomorrow's demand for lettuce averages 255 boxes with a standard deviation of 40 boxes.arrow_forwardJoint Products Choi Company manufactures two skin care lotions, Smooth Skin and Silken Skin,from a joint process. The joint costs incurred are $420,000 for a standard production run that generates 180,000 pints of Smooth Skin and 120,000 pints of Silken Skin. Smooth Skin sells for $2.40 perpint, while Silken Skin sells for $3.90 per pint.Required1. Assuming that both products are sold at the split-off point, how much of the joint cost of each production run is allocated to Smooth Skin using the relative sales value method?2. If no separable costs are incurred after the split-off point, how much of the joint cost of each productionrun is allocated to Silken Skin using the physical measure method method?3. If separable processing costs beyond the split-off point are $1.40 per pint for Smooth Skin and $0.90 perpint for Silken Skin, how much of the joint cost of each production run is allocated to Silken Skin usinga net realizable value method?4. If separable processing costs beyond the…arrow_forward
- 2.28 A foundry produces castings to order. An order for 20 special castings has been re- ceived. Since the casting process is highly variable, not all castings produced are good. The cost of producing each casting is $550; the additional cost of finishing a good casting is $125. If a casting is not good, it is recycled at a value of $75; excess good castings are not finished but are recycled at a value of $75. The customer has agreed to accept 15, 16, 17, 18, 19, or 20 castings at a price of $1250 each. If fewer than 15 good castings are produced, none will be purchased by the customer. Prob- ability distributions for the number of good castings produced in a batch of varying sizes are given below. How many castings should be scheduled in order to maximize expected profit? #Good Castings 5 6 7 8 9 10 11 12 13 14 15 16 17 18 19 20 21 22 23 24 25 26 27 28 29 30 79 2 PRODUCT, PROCESS, AND SCHEDULE DESIGN Number of Castings Scheduled 15 16 17 0.05 0.00 0.00 0.00 0.00 0.00 0.05 0.05 0.00…arrow_forwardAnnie bought one dozen smartphones for 200,000 pesos with a discount of 5%. She sold half dozen at a price of 18,000 pesos per unit. However, a new model of smartphone became available in the market, so she sold the remaining half dozen at 12,000 pesos each unit. What was her profit or loss? Compute the following requirements: a. Gross profit rate b. Operating profit margin rate c. Net profit margin rate d. Return on investmentarrow_forwardSuppose Firm A can manufacture 100 pens and 20 umbrellas with a unit of labor, and Firm B can manufacture 80 pens and 10 umbrellas with a unit of labor. Which one of the following statements is true? Firm A has the comparative advantage in both pen and umbrella production.Firm B has an absolute advantage in umbrella production.Firm A has a comparative advantage only in pen production.Firm B has a comparative advantage in pen production.Neither firm has a comparative advantage in either pen or umbrella production.arrow_forward
- Consider a hardware supply warehouse that is contractually obligated to deliver 1000units a specialized fastener to a local manufaturing company each week. Each time thewarehouse places an order for these items from its supplier, an ordering and transporationfee off $20 is charged to the warehouse. The warehouse pays $1.00 for each fastener andcharges the local firm $5.00 for each fastener. Annual holding cosst iss 25% off inventoryvalue, or $0.25 per year. The warehouse manager would like to know how much to orderwhen inventory gets to zero.Assume that the warehouse works 50 weeks/year.arrow_forwardRoss White wants to reconsider his decision of buying the brackets and is considering making the brackets in-house. He has determined that setup cost would be $25 in machinist time and lost production time and that 50 brackets could be produced in a day once the machine has been set up. Ross estimates that the cost (inlcuding labor time and materials) of producing one bracket woldbe $14.80. The holding cost would be 10% of this cost. a) What is the daily demand rate? b) What is the optimal production quantity? c) How long will it take to produce the optimal quanitty? How much inventory is sold during the time? d) if Ross uses the opitmal produciton quantity, what would be the maximum inventory level? What is the annual holding cost? e) How many production runs would there be each year? What would be the annual setup cost? f) Given the optimal production run size, what is the total annual inventory cost? g) if the lead time is one-half day, what is the ROP?arrow_forwardThe local supermarket buys lettuce each day to ensure really fresh produce. Each morning, any lettuce that is left from the previous day is sold to a dealer that resells it to farmers who use it to feed their animals. This week, the supermarket can buy fresh lettuce for $8.00 a box. The lettuce is sold for $16.00 a box and the dealer that sells old lettuce is willing to pay $1.80 a box. Past history says that tomorrow's demand for lettuce averages 245 boxes with a standard deviation of 38 boxes. How many boxes of lettuce should the supermarket purchase tomorrow? (Use Excel's NORMSINV() function to find the correct critical value for the given a-level. Do not round intermediate calculations. Round your answer to the nearest whole number.) Number of boxesarrow_forward
- 14. 12 The purchasing manager for the Atlantic Steel Company must determine a policy for ordering coal to operate 12 converters. Each converter requires exactly 5 tons of coal per day to operate, and the firm operates 360 days per year. The purchasing manager has determined that the ordering cost is $80 per order and the cost of holding coal is 20% of the average dollar value of inventory held. The purchasing manager has negotiated a contract to obtain the coal for $12 per ton for the coming year. a. Determine the optimal quantity of coal to receive in each order. (Ans: 1200 tons) b. Determine the total inventory-related costs associated with the optimal ordering policy (do not include the cost of the coal). (Ans: TC= $2880) c. If 5 days of lead time are required to receive an order of coal, how much coal should be on hand when an order is placed? (Ans= R=300 tons)arrow_forwardA plant manager of a chemical plant must determine the lot size for a particular chemical that has a steadydemand of 30 barrels per day. The production rate is 190 barrels per day, annual demand is 10,500 barrels,setup cost is $200, annual holding cost is $0.21 per barrel, and the plant operates 350 days per year.a. Determine the economic production lot size (ELS).b. Determine the total annual setup and inventory holding cost for this item.c. Determine the time between orders (TBO), or cycle length, for the ELS.d. Determine the production time per lot.What are the advantages of reducing the setup time by 10 percent?arrow_forwardUsing method 1 (combined depreciation and investment cost) determine the probable cost per hour of owning and operating a caterpillar that uses rubber tires.The equipment is a 185-hp diesel engine and the following conditions apply. Factor delivered price = $ 472,550Sales tax = 6.5% of delivered priceUnloading and assembling = $2,175Salvage value = $ 115,000Useful life = $ 6 yr.Hours used per year = 1,675 hrInterest on investment = 9.5%Maintenance and repair = 65% of straight line depreciationDiesel engine = 185 hpOperating factor = 0.60Fuel cost = $5.45/galCrankcase capacity = 9 galHours between oil changes = 135 hr.Oil cost = $14.25/galTires = $ 62,500Tire life = 4950 hr.Tire repairs = 12% of tire depreciation.arrow_forward
arrow_back_ios
SEE MORE QUESTIONS
arrow_forward_ios
Recommended textbooks for you
- Practical Management ScienceOperations ManagementISBN:9781337406659Author:WINSTON, Wayne L.Publisher:Cengage,
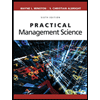
Practical Management Science
Operations Management
ISBN:9781337406659
Author:WINSTON, Wayne L.
Publisher:Cengage,