The attached answer was provided for the attached question. The equation uses the given temperature in celcius and the answer is also given in celcius. The temperature was used in the equation without converting from F and the answer was supposed to be in F. I am worried that even if I converted the answer to celcius that it would be correct because temperature was used in the equation using the incorrect unit.
The attached answer was provided for the attached question. The equation uses the given temperature in celcius and the answer is also given in celcius. The temperature was used in the equation without converting from F and the answer was supposed to be in F. I am worried that even if I converted the answer to celcius that it would be correct because temperature was used in the equation using the incorrect unit.
Elements Of Electromagnetics
7th Edition
ISBN:9780190698614
Author:Sadiku, Matthew N. O.
Publisher:Sadiku, Matthew N. O.
ChapterMA: Math Assessment
Section: Chapter Questions
Problem 1.1MA
Related questions
Question
The attached answer was provided for the attached question. The equation uses the given temperature in celcius and the answer is also given in celcius. The temperature was used in the equation without converting from F and the answer was supposed to be in F. I am worried that even if I converted the answer to celcius that it would be correct because temperature was used in the equation using the incorrect unit.

Transcribed Image Text:Step 1 Given data
inlet diameter (d)= 0.35 inch
Temperature (T,)- 50°F
other diameter ( D)= 0.10 inch
Step 2 Calculation of temperature
Properties of Red brass (C83400):
Coefficient of thermal Expansion (a)=18x10-6/CO
modulus of elasticity (E)= 110 GPa
Yield Strength (a)- 69 MPa
Properties of Magnesium Alloy:
Coefficient of thermal Expansion (a)=18x10-6 /CO
modulus of elasticity (E)= 45 GPa
Yield Strength (o)= 150 MPa
Step 3 further Calculation
BY applying the Equation:
Stress (o)= Ex e
In case of thermal stresso= exALL=ExaAT= Syc ( Compression Strength)As the temperature is increased s
o compression stress will devlop.according to theory of failure :maximum shear stress theory:Ssy(yield s
trength)= 0.5 Syc( compressive strength)for red brass :Ssy= 0.5×EaxAT69×106 =0.5×110×109×18×10-6×(T-
50C)T=74.797 C
for mg alloy:Ssy= 0.5×EaAT150x106 =0.5-25.2x106x45x109×(T- 5)T= 269.55 CSo it is clear that the maxim
umtemperature that the brass cylinder can be subjected towithout causing yieldingof any one of the ma
terial is Tmax = 74.697 C

Transcribed Image Text:The 0.35-inch-diameter cylinder is made from C83400 red brass and is placed in the
device depicted below when temperature is T1 = 5 °F throughout. The two Am 1004-T-61
magnesium alloy carriage bolts each have a diameter of 0.10 inches and hold the
cylinder snug with negligible force against the rigid jaws. Determine the maximum
temperature (in °F) that the brass cylinder can be subjected to without causing yielding of
any one of the materials. The end plates will not deform or fail.
4 in-
-4.004 in-
Not to scale
Expert Solution

This question has been solved!
Explore an expertly crafted, step-by-step solution for a thorough understanding of key concepts.
Step by step
Solved in 2 steps

Knowledge Booster
Learn more about
Need a deep-dive on the concept behind this application? Look no further. Learn more about this topic, mechanical-engineering and related others by exploring similar questions and additional content below.Recommended textbooks for you
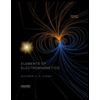
Elements Of Electromagnetics
Mechanical Engineering
ISBN:
9780190698614
Author:
Sadiku, Matthew N. O.
Publisher:
Oxford University Press
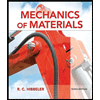
Mechanics of Materials (10th Edition)
Mechanical Engineering
ISBN:
9780134319650
Author:
Russell C. Hibbeler
Publisher:
PEARSON
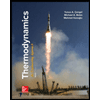
Thermodynamics: An Engineering Approach
Mechanical Engineering
ISBN:
9781259822674
Author:
Yunus A. Cengel Dr., Michael A. Boles
Publisher:
McGraw-Hill Education
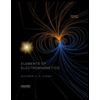
Elements Of Electromagnetics
Mechanical Engineering
ISBN:
9780190698614
Author:
Sadiku, Matthew N. O.
Publisher:
Oxford University Press
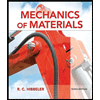
Mechanics of Materials (10th Edition)
Mechanical Engineering
ISBN:
9780134319650
Author:
Russell C. Hibbeler
Publisher:
PEARSON
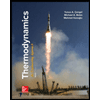
Thermodynamics: An Engineering Approach
Mechanical Engineering
ISBN:
9781259822674
Author:
Yunus A. Cengel Dr., Michael A. Boles
Publisher:
McGraw-Hill Education
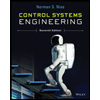
Control Systems Engineering
Mechanical Engineering
ISBN:
9781118170519
Author:
Norman S. Nise
Publisher:
WILEY
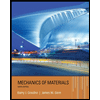
Mechanics of Materials (MindTap Course List)
Mechanical Engineering
ISBN:
9781337093347
Author:
Barry J. Goodno, James M. Gere
Publisher:
Cengage Learning
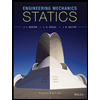
Engineering Mechanics: Statics
Mechanical Engineering
ISBN:
9781118807330
Author:
James L. Meriam, L. G. Kraige, J. N. Bolton
Publisher:
WILEY