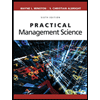
Case study of the company
SAFETY FIRST LIMITED
(Safety First) is a small, privately-owned UK limited company, led by its founder, Bianca Devayne, and occupies an industrial unit in the Northeast area of Wolverhampton, where all the company’s staff are based. The company currently employsfifteen staff in the following roles:
1 x Owner-Manager: Bianca Devayne.
1 x Administrator/Receptionist.
1 x Finance Manager;
1 x Marketing Assistant.
1 x Operations Manager.
1 x Human Resources Assistant.
7 x Picking and Packing Operatives.
1 x Delivery Driver
1 x Cleaning Operative.
Safety First supplies businesses with personal protective equipment (PPE) for catering, childcare, health care and social care purposes. Although the company does not produce PPE, the large warehouse unit owned by the company allows staff to store large quantities and use part of their space for packing once orders are received. As a result of the 2020global pandemic (Covid-19) demand for the sort of products which Safety First supplies continues to increase, and Bianca Devayne is keen to take advantage of this surge in demand. To rise to this challenge, a number of decisions need to be made regarding staffing, marketing, operations and finance, to ensure that Bianca and her team can meet the increased demand both effectively and efficiently.
The company has historically relied on a small number of loyal and regular regional business customers (ranging from childcare centers to private social care and residential care homes) for its supply of PPE and, as a result, has only a one-page website and no social media presence at all.
For the purposes of this assessment, you can assume the following:
- The company owns one small delivery van, insured for and used by the sole delivery driver.
- the warehouse unit is owned by the company and currently holds 100,000 pieces of PPE – just 10% of unit storage capacity.
- Regular stocks of 5,000 pieces of various PPE items are delivered to Safety First on a weekly basis and stock is rotated accordingly.
- The five regular business customers of Safety First receive 10,000 pieces of PPE each week.
- the production operatives who pick and pack PPE for posting and courier delivery occupy a spacious room situated alongside the company offices at the front of the unit – although this is fit for current purposes, any increase in demand from new and existing customers would require a larger space.
- The daily demand for PPE from businesses within the delivery range of Safety First is expected to be ten times the company’s current stockpile of 100,000 pieces.
- The Picking and Packing Operatives are all currently employed on part-time, permanent contracts, working morning shifts only.
- The Delivery Driver works on a part-time, permanent basis, working afternoons only.
Task 3 – Operations Management Plan (250 words)
This section requires you to focus on improving the demand lead time for Safety First products, so that the new and existing customers of Safety First wait for the shortest possible time between ordering PPE and taking delivery of their ordered product(s). In order to do this, you will need to undertake internet research, to find at least two companies which can supply wholesale quantities of Safety First’s three core products directly to your warehouse unit in Wolverhampton, along with the cost for each ‘unit’ – which will help you to produce your
financial projection for Task 5. You will also need to consider the number of existing staff and the potential new orders the company may receive, providing a final figure of additional staff, which will support your completion of Task 4. Finally, you will need to consider the current packing space available to new and existing staff and how this might be adapted to meet
increased staff levels and packing requirements

Step by stepSolved in 3 steps

- what is Definition of methods to provide evdence for reliability and validity?arrow_forwardPatient Safety: The Past Decade Describe the role of the National Quality Forum in helping to advance the goals of the Patient Safety and Quality Improvement Act. Describe the function and benefits of Patient Safety Organizations.arrow_forwardIn the design of their controls in year 1, Trinity relied on a practice-based, bottom up approach. What were the strengths and weaknesses of this approach? How effective was it? What would you recommend they should have done differently?arrow_forward
- You are building a Quality Assurance team for your company. The hourly workers are in place and it is time to find the team leader.A) Write a job description for the position of Quality Assurance Manager. This position will have 10 hourly team members reporting to the manager. Research this position and list a minimum of 5 duties the manager must be able to perform. Include educational requirements, determine experience necessary.B) Write a formal job offer for the position of Quality Manager. Offer must include at a minimum, job title, duties, salary, dress code, company drug policy, and benefits.arrow_forward8. Explain the essential components of the Malcolm Baldrige quality model.arrow_forward6. Outline a risk management approach to quality issues.arrow_forward
- Practical Management ScienceOperations ManagementISBN:9781337406659Author:WINSTON, Wayne L.Publisher:Cengage,Operations ManagementOperations ManagementISBN:9781259667473Author:William J StevensonPublisher:McGraw-Hill EducationOperations and Supply Chain Management (Mcgraw-hi...Operations ManagementISBN:9781259666100Author:F. Robert Jacobs, Richard B ChasePublisher:McGraw-Hill Education
- Purchasing and Supply Chain ManagementOperations ManagementISBN:9781285869681Author:Robert M. Monczka, Robert B. Handfield, Larry C. Giunipero, James L. PattersonPublisher:Cengage LearningProduction and Operations Analysis, Seventh Editi...Operations ManagementISBN:9781478623069Author:Steven Nahmias, Tava Lennon OlsenPublisher:Waveland Press, Inc.
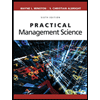
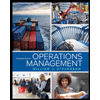
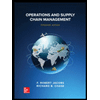
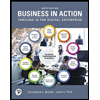
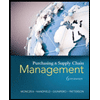
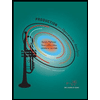