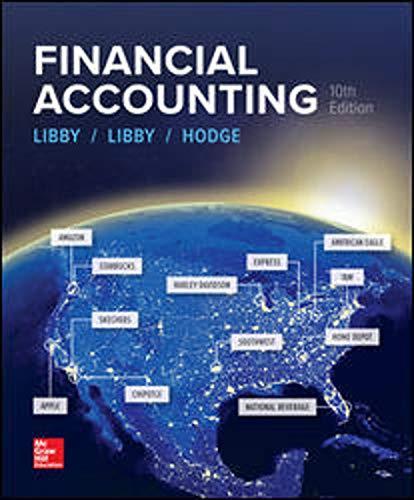
Problem B-5 Volume Trade-Off Decision; Managing the Constraint [LOB-2, LOB-3]
Sammamish Brick, Inc., manufactures bricks using clay deposits on the company’s property. Raw clays are blended and then extruded into molds to form unfired bricks. The unfired bricks are then stacked onto movable metal platforms and rolled into the kiln where they are fired until dry. The dried bricks are then packaged and shipped to retail outlets and contractors. The bottleneck in the production process is the kiln, which is available for 2,850 hours per year. Data concerning the company’s four main products appear below. Products are sold by the pallet.
Traditional Brick |
Textured Facing |
Cinder Block |
Roman Brick |
|
Gross revenue per pallet | $817 | $1,396 | $652 | $946 |
Contribution margin per pallet | $510 | $ 650 | $416 | $485 |
Annual demand (pallets) | 110 | 130 | 120 | 130 |
Hours required in the kiln per pallet | 10 | 10 | 4 | 5 |
No fixed costs could be avoided by modifying how much is produced of any product.
4. The kiln could be operated for more than 2,850 hours per year by running it after normal working hours. Up to how much per hour should the company be willing to pay in overtime wages, energy costs, and other incremental costs to operate the kiln additional hours?
5. The company is considering introducing a new product, glazed Venetian bricks, whose variable cost would be $865 per pallet and that would require 10 hours in the kiln per pallet. What is the minimum acceptable selling price for this new product?
6. Salespersons are currently paid a commission of 5% of gross revenues. Will this motivate the salespersons to make the right choices concerning which products to sell most aggressively?
Yes | |
No |

Trending nowThis is a popular solution!
Step by stepSolved in 3 steps

- Please do not give solution in image formatarrow_forwardH2.arrow_forwardQuestion #1 Bridgestone Tires manufactures two types of tires that it sells as wholesale products to various specialty retail auto supply stores. Each tire requires a three-step process. The first step is mixing. The mixing department combines some of the necessary direct materials to create the material mix that will become part of the tire. The second step includes the forming of each tire where the materials are layered to form the tire. This is an entirely automated process. The final step is finishing, which is an entirely manual process. The finishing department includes curing and quality control. Required: Costs involved in the process are listed next. For each cost, indicate whether it is a direct variable, direct fixed, indirect variable, or indirect fixed cost, assuming “units of production of each kind of tire” is the cost object. Costs: Rubber Mixing department manager Reinforcement cables Material handlers in each department Other direct…arrow_forward
- Problem 15-40 (Algo) Evaluate Profit Impact of Alternative Transfer Decisions (LO 15-2, 3) Amazon Beverages produces and bottles a line of soft drinks using exotic fruits from Latin America and Asia. The manufacturing process entails mixing and adding juices and coloring ingredients at the bottling plant, which is a part of Mixing Division. The finished product is packaged in a company-produced glass bottle and packed in cases of 24 bottles each. Because the appearance of the bottle heavily influences sales volume, Amazon developed a unique bottle production process at the company’s container plant, which is a part of Container Division. Mixing Division uses all of the container plant’s production. Each division (Mixing and Container) is considered a separate profit center and evaluated as such. As the new corporate controller, you are responsible for determining the proper transfer price to use for the bottles produced for Mixing Division. At your request, Container Division’s…arrow_forward1.5 Sort the costs of a paper industry into product cost and period cost: Salaries of scientists exploring ways to accelerate forest expansion Computer software cost to monitor production in progress Cost of electricity in the paper mill Salaries of the company's top executives Chemical costs for paper processing TV advertising costs Depreciation of the production plant Cost of buying wood pulp Life insurance of the chief executive officerarrow_forwardChapter 9 Section 4 Problem 2 (09.04-PR002) - use MACRS-GDS 7 year property using excel to a answer the following. Michelin is considering going “lights out” in the mixing area of the business that operates 24/7. Currently, personnel with a loaded cost of $600,000 per year are used to manually weigh real rubber, synthetic rubber, carbon black, oils, and other components prior to manual insertion in a Banbary mixer that provides a homogeneous blend of rubber for making tires (rubber products). New technology is available that has the reliability and consistency desired to equal or exceed the quality of blend now achieved manually. It requires an investment of $2.5 million, with $110,000 per year operational costs and will replace all of the manual effort described above. The planning horizon is 8 years and there will be a $300,000 salvage value at that time for the new technology. The income-tax rate is 25% and the after-tax MARR is 10%. A. Determine the annual cost of purchasing the…arrow_forward
- Problem 15-40 (Static) Evaluate Profit Impact of Alternative Transfer Decisions (LO 15-2, 3) Amazon Beverages produces and bottles a line of soft drinks using exotic fruits from Latin America and Asia. The manufacturing process entails mixing and adding juices and coloring ingredients at the bottling plant, which is a part of Mixing Division. The finished product is packaged in a company-produced glass bottle and packed in cases of 24 bottles each. Because the appearance of the bottle heavily influences sales volume, Amazon developed a unique bottle production process at the company’s container plant, which is a part of Container Division. Mixing Division uses all of the container plant’s production. Each division (Mixing and Container) is considered a separate profit center and evaluated as such. As the new corporate controller, you are responsible for determining the proper transfer price to use for the bottles produced for Mixing Division. At your request, Container Division’s…arrow_forwardQuestion 1.3 Identify if the following costs are "product" or "period" costs: CST Period Cost or Product Cost? 1. Television advertisements for Bailey's products 2. Lubricants used in running bottling machines 3. Research and Development related to the elimination of antibiotic residues in milk 4. Gasoline used to operate refrigerated trucks delivering finished dairy products to grocery stores 5. Company president's annual bonus 6. Depreciation on refrigerated trucks used to collect raw milk 7. Plastic gallon containers in which milk is packaged 8. Property insurance on dairy processing plant 9. Cost of milk purchased from local dairy farmers 10. Depreciation on tablets used by sales staff 11. Depreciation on chairs and tables in the factory lunchroom. 12. The cost of packaging the company's product. 13. The wages of the receptionist in the administrative offices. 14. Cost of leasing the corporate jet used by the company's executives. 15. The cost of renting rooms at a BC resort for…arrow_forward17 oints Split Corporation manufactures products X, Y, and Z from a joint production process. Joint costs are allocated to products based on relative sales value of the products at the split-off point. Additional information is as follows: Units produced Allocated joint costs Sales value at split-off 01:39:59 Sales value if processed further Additional costs for further processing Product X's sales value at the split-off point is: 26,000 $ 161,280 Z Total 22,000 $ 108,000 18,000 $180,000 66,000 $449,280 ? 150,000 66,000 250,000 624,000 46,000 186,000 341,000 279,000 1,268,000 74,000 648,000 0 Multiple Choice $156,000. $19,000. $190,000 $224,000 $117,000.arrow_forward
- HELP MEarrow_forwardQuestion Content Area Sell at Split-Off or Process Further Decision, Alternatives, Relevant Costs Betram Chemicals Company processes a number of chemical compounds used in producing industrial cleaning products. One compound is decomposed into two chemicals: anderine and dofinol. The cost of processing one batch of compound is $76,500, and the result is 5,900 gallons of anderine and 7,900 gallons of dofinol. Betram Chemicals can sell the anderine at split-off for $9.00 per gallon and the dofinol for $6.00 per gallon. Alternatively, the anderine can be processed further at a cost of $8.10 per gallon (of anderine) into cermine. It takes 3 gallons of anderine for every gallon of cermine. A gallon of cermine sells for $60. Required: 1. Which alternative is more cost effective and by how much?NOTE: Do NOT round interim calculations and, if required, round your answer to the nearest dollar. by $fill in the blank 2 2. What if the production of anderine into cermine required additional…arrow_forwardCan you assist me homwork question Chapter 15 Problem 5 I keep getting the calculations mixed up. Thank you.arrow_forward
- AccountingAccountingISBN:9781337272094Author:WARREN, Carl S., Reeve, James M., Duchac, Jonathan E.Publisher:Cengage Learning,Accounting Information SystemsAccountingISBN:9781337619202Author:Hall, James A.Publisher:Cengage Learning,
- Horngren's Cost Accounting: A Managerial Emphasis...AccountingISBN:9780134475585Author:Srikant M. Datar, Madhav V. RajanPublisher:PEARSONIntermediate AccountingAccountingISBN:9781259722660Author:J. David Spiceland, Mark W. Nelson, Wayne M ThomasPublisher:McGraw-Hill EducationFinancial and Managerial AccountingAccountingISBN:9781259726705Author:John J Wild, Ken W. Shaw, Barbara Chiappetta Fundamental Accounting PrinciplesPublisher:McGraw-Hill Education
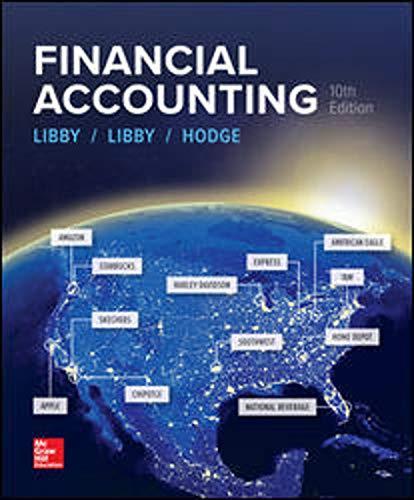
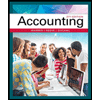
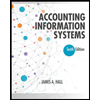
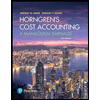
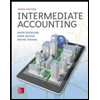
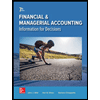