Problem 11-11 (Static) A manager is attempting to put together an aggregate plan for the coming nine months. She has obtained a forecast of expected demand for the planning horizon. The plan must deal with highly seasonal demand; demand is relatively high in periods 3 and 4, and again in period 8, as can be seen from the following forecasts. Period Forecast 1 2 3 190 230 260 4 280 5 210 6 170 7 160 8 260 9 180 Total 1,940 The department now has 20 full-time employees, each of whom produces 10 units of output per period at a cost of $6 per unit. Beginning inventory for period 1 is zero. Inventory carrying cost is $5 per unit per period, and backlog cost is $10 per unit per period. The manager has decided to use part-time workers to assist during seasonal peaks. The cost per unit, including hiring and training, is $11. The output rate is 10 units per worker per period for all workers. A maximum of 10 part-time workers can be used, and the same number of part-time workers must be used in all periods that have part-time workers. The ending inventory in period 9 should be 10 units. The limit on backlogs is 20 units per period. Try to make up backlogs as soon as possible. Compute the total cost for this plan. Assume 20 full-time workers and regular monthly production regular capacity. Total cost
Problem 11-11 (Static) A manager is attempting to put together an aggregate plan for the coming nine months. She has obtained a forecast of expected demand for the planning horizon. The plan must deal with highly seasonal demand; demand is relatively high in periods 3 and 4, and again in period 8, as can be seen from the following forecasts. Period Forecast 1 2 3 190 230 260 4 280 5 210 6 170 7 160 8 260 9 180 Total 1,940 The department now has 20 full-time employees, each of whom produces 10 units of output per period at a cost of $6 per unit. Beginning inventory for period 1 is zero. Inventory carrying cost is $5 per unit per period, and backlog cost is $10 per unit per period. The manager has decided to use part-time workers to assist during seasonal peaks. The cost per unit, including hiring and training, is $11. The output rate is 10 units per worker per period for all workers. A maximum of 10 part-time workers can be used, and the same number of part-time workers must be used in all periods that have part-time workers. The ending inventory in period 9 should be 10 units. The limit on backlogs is 20 units per period. Try to make up backlogs as soon as possible. Compute the total cost for this plan. Assume 20 full-time workers and regular monthly production regular capacity. Total cost
Fundamentals of Financial Management, Concise Edition (with Thomson ONE - Business School Edition, 1 term (6 months) Printed Access Card) (MindTap Course List)
8th Edition
ISBN:9781285065137
Author:Eugene F. Brigham, Joel F. Houston
Publisher:Eugene F. Brigham, Joel F. Houston
Chapter15: Working Capital Management
Section: Chapter Questions
Problem 11SP: CASH BUDGETING Rework Problem 15-10 using a spreadsheet model. After completing Parts a through d,...
Related questions
Question

Transcribed Image Text:Problem 11-11 (Static)
A manager is attempting to put together an aggregate plan for the coming nine months. She has obtained a forecast of expected
demand for the planning horizon. The plan must deal with highly seasonal demand; demand is relatively high in periods 3 and 4, and
again in period 8, as can be seen from the following forecasts.
Period
Forecast
1
2
3
190
230
260
4
280
5
210
6
170
7
160
8
260
9
180
Total
1,940
The department now has 20 full-time employees, each of whom produces 10 units of output per period at a cost of $6 per unit.
Beginning inventory for period 1 is zero. Inventory carrying cost is $5 per unit per period, and backlog cost is $10 per unit per period.
The manager has decided to use part-time workers to assist during seasonal peaks. The cost per unit, including hiring and training, is
$11. The output rate is 10 units per worker per period for all workers. A maximum of 10 part-time workers can be used, and the same
number of part-time workers must be used in all periods that have part-time workers. The ending inventory in period 9 should be 10
units. The limit on backlogs is 20 units per period. Try to make up backlogs as soon as possible. Compute the total cost for this plan.
Assume 20 full-time workers and regular monthly production regular capacity.
Total cost
Expert Solution

This question has been solved!
Explore an expertly crafted, step-by-step solution for a thorough understanding of key concepts.
Step by step
Solved in 2 steps

Recommended textbooks for you
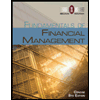
Fundamentals of Financial Management, Concise Edi…
Finance
ISBN:
9781285065137
Author:
Eugene F. Brigham, Joel F. Houston
Publisher:
Cengage Learning
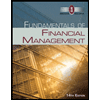
Fundamentals of Financial Management (MindTap Cou…
Finance
ISBN:
9781285867977
Author:
Eugene F. Brigham, Joel F. Houston
Publisher:
Cengage Learning
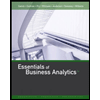
Essentials of Business Analytics (MindTap Course …
Statistics
ISBN:
9781305627734
Author:
Jeffrey D. Camm, James J. Cochran, Michael J. Fry, Jeffrey W. Ohlmann, David R. Anderson
Publisher:
Cengage Learning
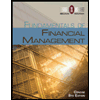
Fundamentals of Financial Management, Concise Edi…
Finance
ISBN:
9781285065137
Author:
Eugene F. Brigham, Joel F. Houston
Publisher:
Cengage Learning
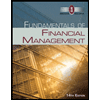
Fundamentals of Financial Management (MindTap Cou…
Finance
ISBN:
9781285867977
Author:
Eugene F. Brigham, Joel F. Houston
Publisher:
Cengage Learning
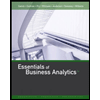
Essentials of Business Analytics (MindTap Course …
Statistics
ISBN:
9781305627734
Author:
Jeffrey D. Camm, James J. Cochran, Michael J. Fry, Jeffrey W. Ohlmann, David R. Anderson
Publisher:
Cengage Learning
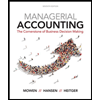
Managerial Accounting: The Cornerstone of Busines…
Accounting
ISBN:
9781337115773
Author:
Maryanne M. Mowen, Don R. Hansen, Dan L. Heitger
Publisher:
Cengage Learning