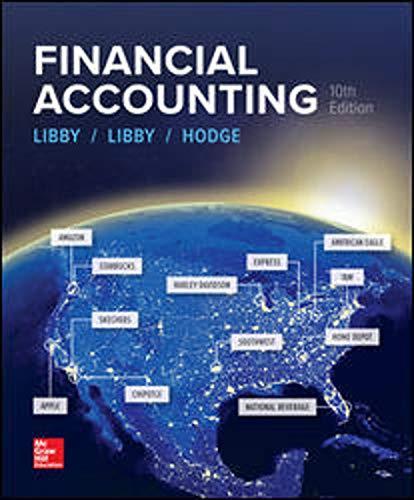
POPOL Company manufactures 100,000 units of Part P yearly as a major component for one of its finished goods. The current report shows the breakdown of the total
Direct materials P120,000
Direct labor 80,000
Variable
Fixed overhead 160,000
Kupa Company, a third party entity, has submitted a proposal to sell POPOL 100,000 units of Part P annually. If POPOL started sourcing these from outside, the plant and equipment currently used to product Part P can be used to manufacture other products of POPOL. This will yield potential savings of P10,000 related to lease production capability to support manufacture of other products of POPOL. As the

Step by stepSolved in 2 steps

- Session Company uses 5,000 units of Part Y each year as a component in the assembly of one of its products. The company is presently producing Part Y internally at a total cost of $72,000 as follows: Direct materials $18,000 Direct labor $20,000 Variable MOH $10,000 Fixed MOH $24,000 Total costs $72,000 An outside supplier has offered to provide Part Y at a price of $12 per unit. If Session Company stops producing the part internally, one-third of the fixed manufacturing overhead would be eliminated. Accepting the outside supplier's offer leads to an annual advantage/disadvantage of: Advantage of $4,000 Disadvantage of $4,000 Disadvantage of $12,000 Advantage of $12,000arrow_forwardThe Pixels Corporation produces a component used in the manufacture of one of its best-selling products. The costs associated with the production of 10,000 units of this component are presented in the table above. The PCAOB Corp. offered to sell Pixels 10,000 units of the same part at a price of $36 per unit. Assume that Pixels has no alternative use for the factory facilities that would be released. Based on all of the information above, should Pixels manufacture their own part or outsource to PCAOB? Note that if you agree to outsource, you would save $60,000 in indirect fixed costs. Direct Materials $90,000 Direct Manufacturing Labor $130,000 Variable Manufacturing Overhead $60,000 Fixed Manufacturing Overhead $140,000 Total Costs $420,000 a. Buy the part from PCAOB because you save $6 per unit b. Manufacture the part because it saves $6 per unit c. Make the part because you save $2 per unit d. Buy the part from PCAOB because you save $60,000arrow_forwardMagnificent Modems has excess production capacity and is considering the possibility of making and selling security tokens. The following estimates are based on a production and sales volume of 1,000 security tokens. Unit-level manufacturing costs are expected to be $20. Sales commissions will be established at $1 per unit. The current facility-level costs, including depreciation on manufacturing equipment ($60,000), rent on the manufacturing facility ($50,000), depreciation on the administrative equipment ($12,000), and other fixed administrative expenses ($71,950), will not be affected by the production of the security tokens. The chief accountant has decided to allocate the facility-level costs to the existing product (modems) and to the new product (security tokens) on the basis of the number of units of product made (i.e., 5,000 modems and 1,000 security tokens). Required a. Determine the per-unit cost of making and selling 1,000 security tokens. Note: Do not round intermediate…arrow_forward
- Delta produces a part that is used in the manufacture of one of its products. The costs associated with the production of 10,000 units of this part are as follows: Direct materials $ 90,000 Direct labor 130,000 Variable factory overhead Fixed factory overhead 140,000 Total costs $420,000 60,000 Of the fixed factory overhead costs, $60,000 is avoidable. 20) Conners has offered to sell 10,000 units of the same part to Delta for $36 per unit. Assuming there is no other use for the facilities, what is the effect on operating income if Delta buys from Conners? 21) Assuming no other use of their facilities, at what buying price per unit for Delta would Delta's operating income be the same whether they made the part or bought it from Conners?arrow_forwardOat Treats manufactures various types of cereal bars featuring oats. Simmons Cereal Company has approached Oat Treats with a proposal to sell the company its top selling oat cereal bar at a price of $27,500 for 20,000 bars. The costs shown are associated with production of 20,000 oat bars currently: Direct material Direct labor Manufacturing overhead Total The manufacturing overhead consists of $3,000 of variable costs with the balance being allocated to fixed costs. PLEASE NOTE: Costs per unit are rounded to two decimal places and shown with "$" and commas as needed (i.e. $1,234.56). All other dollar amounts are rounded to whole dollars and shown with "$" and commas as needed (i.e. $12,345). 1. What is Oat Treats' relevant cost? $14,000 6,000 8,000 $28,000 2. What does Simmons Cereal's offer cost? 3. If Oat Treats accepts the offer, what will the effect on profit be? o Incremental dollar amount = o Increase or Decrease? no quotes. Please note: Your answer is either "Increase" or…arrow_forwardBenitez Company currently outsources a relay switch that is a component in one of its products. The switches cost $40 each. The company is considering making the switches internally at the following projected annual production costs: Unit-level material cost $ 8 Unit-level labor cost $ 7 Unit-level overhead $ 6 Batch-level set-up cost (4,000 units per batch) $ 30,000 Product-level supervisory salaries $ 40,000 Allocated facility-level costs $ 25,000 The company expects an annual need for 4,000 switches. If the company makes the product, it will have to utilize factory space currently being leased to another company for $2,000 a month. If the company decides to make the parts, total costs will be: Multiple Choice a.$18,000 more than if the switches are purchased. b.$43,000 more than if the switches are purchased. c.$22,000 less than if the switches are purchased. d.$25,000 less than if the switches are purchased.arrow_forward
- Zycon has produced 10,000 units of partially finished Product A. These units cost $15,000 to produce, and they can be sold to another manufacturer for $20,000. Instead, Zycon can process the units further and produce finished Products X, Y, and Z. Processing further will cost an additional $22,000 and will yield total revenues of $35,000. Place an X in the appropriate column to identify whether the item is relevant or irrelevant to the sell or process further decision.arrow_forwardAhrends Corporation makes 43,000 units per year of a part it uses in the products it manufactures. The unit product cost of this part is computed as follows: Direct materials Direct labor Variable manufacturing overhead Fixed manufacturing overhead Unit product cost $ 12.80 23.30 2.10 26.50 $ 64.70 An outside supplier has offered to sell the company all of these parts it needs for $51.00 a unit. If the company accepts this offer, the facilities now being used to make the part could be used to make more units of a product that is in high demand. The additional contribution margin on this other product would be $301,000 per year. If the part were purchased from the outside supplier, all of the direct labor cost of the part would be avoided. However, $23.40 of the fixed manufacturing overhead cost being applied to the part would continue even if the part were purchased from the outside supplier. This fixed manufacturing overhead cost would be applied to the company's remaining products.…arrow_forwardSteve company produces 30000 units of parts each year for use on its production line. The cost per units of the part S6: Direct material $3.60 Direct labor $10.00 Variable manufacturing overhead $2.40 Fixed manufacturing overhead $9.00 Total cost per part$25.00 An outside supplier has offered to sell 30000 units of the part each year at a product company at $21.00 per part. If the products company accepts this offer, the facilities now being used to manufacturer the parts could be rented by another company at the annual rent of $80,000.00. However, the products have determined that two-thirds of the fixed manufacturing overhead being applied to the part would continue even if the part S6 was purchased by an outside supplier. What is the advantage or disadvantage of accepting the outside supplier's offer? and how much ?arrow_forward
- AccountingAccountingISBN:9781337272094Author:WARREN, Carl S., Reeve, James M., Duchac, Jonathan E.Publisher:Cengage Learning,Accounting Information SystemsAccountingISBN:9781337619202Author:Hall, James A.Publisher:Cengage Learning,
- Horngren's Cost Accounting: A Managerial Emphasis...AccountingISBN:9780134475585Author:Srikant M. Datar, Madhav V. RajanPublisher:PEARSONIntermediate AccountingAccountingISBN:9781259722660Author:J. David Spiceland, Mark W. Nelson, Wayne M ThomasPublisher:McGraw-Hill EducationFinancial and Managerial AccountingAccountingISBN:9781259726705Author:John J Wild, Ken W. Shaw, Barbara Chiappetta Fundamental Accounting PrinciplesPublisher:McGraw-Hill Education
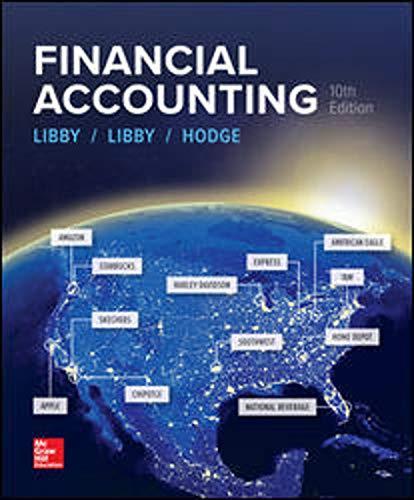
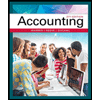
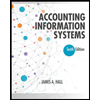
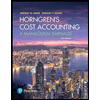
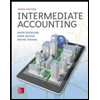
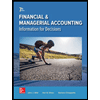