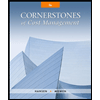
Cornerstones of Cost Management (Cornerstones Series)
4th Edition
ISBN: 9781305970663
Author: Don R. Hansen, Maryanne M. Mowen
Publisher: Cengage Learning
expand_more
expand_more
format_list_bulleted
Question
Show full workings
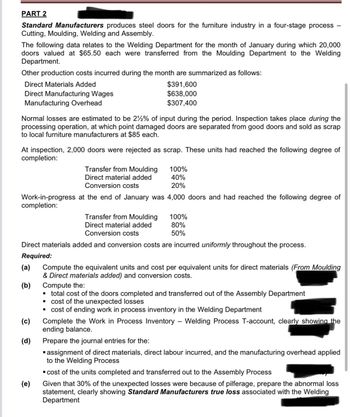
Transcribed Image Text:PART 2
Standard Manufacturers produces steel doors for the furniture industry in a four-stage process
Cutting, Moulding, Welding and Assembly.
The following data relates to the Welding Department for the month of January during which 20,000
doors valued at $65.50 each were transferred from the Moulding Department to the Welding
Department.
Other production costs incurred during the month are summarized as follows:
Direct Materials Added
Direct Manufacturing Wages
Manufacturing Overhead
$391,600
$638,000
$307,400
Normal losses are estimated to be 2% of input during the period. Inspection takes place during the
processing operation, at which point damaged doors are separated from good doors and sold as scrap
to local furniture manufacturers at $85 each.
At inspection, 2,000 doors were rejected as scrap. These units had reached the following degree of
completion:
Transfer from Moulding
Direct material added
Conversion costs
100%
40%
20%
Work-in-progress at the end of January was 4,000 doors and had reached the following degree of
completion:
Transfer from Moulding
Direct material added
Conversion costs
100%
80%
50%
Direct materials added and conversion costs are incurred uniformly throughout the process.
Required:
(a)
(b)
Compute the equivalent units and cost per equivalent units for direct materials (From Moulding
& Direct materials added) and conversion costs.
Compute the:
■ total cost of the doors completed and transferred out of the Assembly Department
cost of the unexpected losses
"
■ cost of ending work in process inventory in the Welding Department
(c)
Complete the Work in Process Inventory
-
Welding Process T-account, clearly showing the
ending balance.
(d)
(e)
Prepare the journal entries for the:
"
▪ assignment of direct materials, direct labour incurred, and the manufacturing overhead applied
to the Welding Process
■ cost of the units completed and transferred out to the Assembly Process
Given that 30% of the unexpected losses were because of pilferage, prepare the abnormal loss
statement, clearly showing Standard Manufacturers true loss associated with the Welding
Department
SAVE
AI-Generated Solution
info
AI-generated content may present inaccurate or offensive content that does not represent bartleby’s views.
Unlock instant AI solutions
Tap the button
to generate a solution
to generate a solution
Click the button to generate
a solution
a solution
Knowledge Booster
Similar questions
- SCHEDULE OF COST OF GOODS MANUFACTURED The following information is supplied for Sanchez Welding and Manufacturing Company. Prepare a schedule of cost of goods manufactured for the year ended December 31, 20--. Assume that all materials inventory items are direct materials. Work in process, January 1 20,500 Materials inventory, January 1 11,000 Materials purchases 12,000 Materials inventory, December 31 13,000 Direct labor 9,500 Overhead 5,500 Work in process, December 31 10,500arrow_forwardBasic Cost Flows Linsenmeyer Company produces a common machine component for industrial equipment in three departments: molding, grinding, and finishing. The following data are available for September: During September, 18,000 components were completed. There is no beginning or ending WIP in any department. Required: 1. Prepare a schedule showing, for each department, the cost of direct materials, direct labor, applied overhead, product transferred in from a prior department, and total manufacturing cost. 2. Calculate the unit cost. (Note: Round the unit cost to two decimal places.)arrow_forwardApplying factory overhead Bergan Company estimates that total factory overhead costs will be 620,000 for the year. Direct labor hours are estimated to be 80,000. For Bergan Company, (A) determine the predetermined factory overhead rate using direct labor hours as the activity base, (B) determine the amount of factory overhead applied to Jobs 200 and 305 in May using the data on direct labor hours from BE 16-2, and (C) prepare the journal entry to apply factory overhead to both jobs in May according to the predetermined overhead rate.arrow_forward
- (Appendix 4A) Journal Entries, Job Costs The following transactions occurred during the month of April for Nelson Company: a. Purchased materials costing 4,610 on account. b. Requisitioned materials totaling 4,800 for use in production, 3,170 for Job 518 and the remainder for Job 519. c. Recorded 65 hours of direct labor on Job 518 and 90 hours on Job 519 for the month. Direct laborers are paid at the rate of 14 per hour. d. Applied overhead using a plantwide rate of 6.20 per direct labor hour. e. Incurred and paid in cash actual overhead for the month of 973. f. Completed and transferred Job 518 to Finished Goods. g. Sold on account Job 517, which had been completed and transferred to Finished Goods in March, for cost (2,770) plus 25%. Required: 1. Prepare journal entries for Transactions a through e. 2. Prepare job-order cost sheets for Jobs 518 and 519. Prepare journal entries for Transactions f and g. (Note: Round to the nearest dollar.) 3. Prepare a schedule of cost of goods manufactured for April. Assume that the beginning balance in the raw materials account was 1,025 and that the beginning balance in the work-in-process account was zero.arrow_forwardKokomo Kayak Inc. uses the process cost system. The following data, taken from the organizations books, reflect the results of manufacturing operations during the month of March: Production Costs Work in process, beginning of period: Costs incurred during month: Production Data: 18,000 units finished and transferred to stockroom. Work in process, end of period, 3,000 units, two-thirds completed. Required: Prepare a cost of production summary for March.arrow_forwardSCHEDULE OF COST OF GOODS MANUFACTURED The following information is supplied for Maupin Manufacturing Company. Prepare a schedule of cost of goods manufactured for the year ended December 31, 20--. Assume that all materials inventory items are direct materials. Work in process, January 1 77,000 Materials inventory, January 1 31,000 Materials purchases 35,000 Materials inventory, December 31 26,000 Direct labor 48,000 Overhead 20,000 Work in process, December 31 62,000arrow_forward
- JOURNAL ENTRIES FOR MATERIAL, LABOR, AND OVERHEAD Eto Manufacturing had the following transactions during the month: (a) Purchased raw materials on account, 70,000. (b) Issued direct materials to Job No. 300, 25,000. (c) Issued indirect materials to production, 10,000. (d) Paid biweekly payroll and charged direct labor to Job No. 300, 8,000. (e) Paid biweekly payroll and charged indirect labor to production, 3,000. (f) Issued direct materials to Job No. 301, 20,000. (g) Issued indirect materials to production, 4,000. (h) Paid miscellaneous factory overhead charges, 6,000. (i) Paid biweekly payroll and charged direct labor to Job No. 301, 10,000. (j) Paid biweekly payroll and charged indirect labor to production, 2,000. REQUIRED Prepare general journal entries for transactions (a) through (j).arrow_forwardBaldwin Printing Company uses a job order cost system and applies overhead based on machine hours. A total of 150,000 machine hours have been budgeted for the year. During the year, an order for 1,000 units was completed and incurred the following: The accountant computed the inventory cost of this order to be 4.30 per unit. The annual budgeted overhead in dollars was: a. 577,500. b. 600,000. c. 645,000. d. 660,000.arrow_forwardThe records of Burris Inc. reflect the following data: Work in process, beginning of month2,000 units one-half completed at a cost of 1,250 for materials, 675 for labor, and 950 for overhead. Production costs for the monthmaterials, 99,150; labor, 54,925; factory overhead, 75,050. Units completed and transferred to stock38,500. Work in process, end of month3,000 units, one-half completed. Compute the months unit cost for each element of manufacturing cost and the total per unit cost.arrow_forward
- Work in process account data for two months; cost of production reports Pittsburgh Aluminum Company uses a process cost system to record the costs of manufacturing rolled aluminum, which consists of the smelting and rolling processes. Materials are entered from smelting at the beginning of the rolling process. The inventory of Work in ProcessRolling on September 1 and debits to the account during September were as follows: During September, 2,600 units in process on September 1 were completed, and of the 28,900 units entering the department, all were completed except 2,900 units that were 45 completed. Charges to Work in ProcessRolling for October were as follows: During October, the units in process at the beginning of the month were completed, and of the 31,000 units entering the department, all were completed except 2,000 units that were 25 completed. Instructions 1. Enter the balance as of September 1 in a four-column account for Work in ProcessRolling. Record the debits and the credits in the account for September. Construct a cost of production report and present computations for determining (A) equivalent units of production for materials and conversion, (B) costs per equivalent unit, (C) cost of goods finished, differentiating between units started in the prior period and units started and finished in September, and (D) work in process inventory. 2. Provide the same information for October by recording the October transactions in the four-column work in process account. Construct a cost of production report, and present the October computations (A through D) listed in part (1). 3. Comment on the change in costs per equivalent unit for August through October for direct materials and conversion cost.arrow_forwardDublin Brewing Co. uses the process cost system. The following data, taken from the organizations books, reflect the results of manufacturing operations during October: Production Costs Work in process, beginning of period: Costs incurred during month: Production Data: 13,000 units finished and transferred to stockroom Work in process, end of period, 2,000 units one-half completed Required: Prepare a cost of production summary for October.arrow_forwardDetermining job costcalculation of predetermined rate for applying overhead by direct labor cost and direct labor hour methods Beemer Products Inc. has its factory divided into three departments, with individual factory overhead rates for each department. In each department, all the operations are sufficiently alike for the department to be regarded as a cost center. The estimated monthly factory overhead for the departments is as follows: Forming, 64,000; Shaping, 36,000; and Finishing, 10,080. The estimated production data include the following: The job cost ledger shows the following data for X6, which was completed during the month: Required: Determine the cost of X6. Assume that the factory overhead is applied to production orders, based on the following: 1. Direct labor cost 2. Direct labor hours (Hint: You must first determine overhead rates for each department, rounding rates to the nearest cent.)arrow_forward
arrow_back_ios
SEE MORE QUESTIONS
arrow_forward_ios
Recommended textbooks for you
- Cornerstones of Cost Management (Cornerstones Ser...AccountingISBN:9781305970663Author:Don R. Hansen, Maryanne M. MowenPublisher:Cengage LearningCollege Accounting, Chapters 1-27AccountingISBN:9781337794756Author:HEINTZ, James A.Publisher:Cengage Learning,Managerial Accounting: The Cornerstone of Busines...AccountingISBN:9781337115773Author:Maryanne M. Mowen, Don R. Hansen, Dan L. HeitgerPublisher:Cengage Learning
- Managerial AccountingAccountingISBN:9781337912020Author:Carl Warren, Ph.d. Cma William B. TaylerPublisher:South-Western College PubPrinciples of Cost AccountingAccountingISBN:9781305087408Author:Edward J. Vanderbeck, Maria R. MitchellPublisher:Cengage LearningFinancial And Managerial AccountingAccountingISBN:9781337902663Author:WARREN, Carl S.Publisher:Cengage Learning,
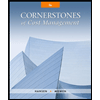
Cornerstones of Cost Management (Cornerstones Ser...
Accounting
ISBN:9781305970663
Author:Don R. Hansen, Maryanne M. Mowen
Publisher:Cengage Learning
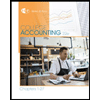
College Accounting, Chapters 1-27
Accounting
ISBN:9781337794756
Author:HEINTZ, James A.
Publisher:Cengage Learning,
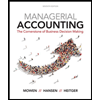
Managerial Accounting: The Cornerstone of Busines...
Accounting
ISBN:9781337115773
Author:Maryanne M. Mowen, Don R. Hansen, Dan L. Heitger
Publisher:Cengage Learning
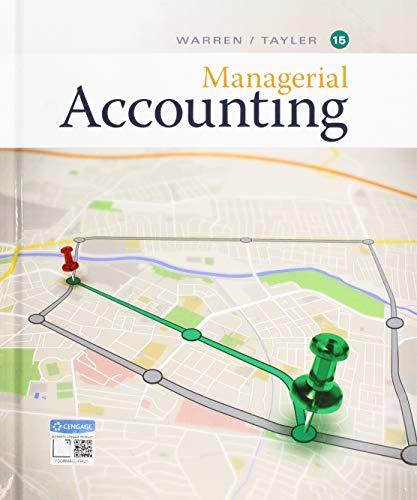
Managerial Accounting
Accounting
ISBN:9781337912020
Author:Carl Warren, Ph.d. Cma William B. Tayler
Publisher:South-Western College Pub
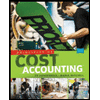
Principles of Cost Accounting
Accounting
ISBN:9781305087408
Author:Edward J. Vanderbeck, Maria R. Mitchell
Publisher:Cengage Learning
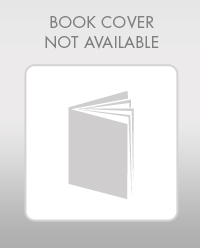
Financial And Managerial Accounting
Accounting
ISBN:9781337902663
Author:WARREN, Carl S.
Publisher:Cengage Learning,