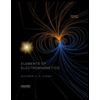
Elements Of Electromagnetics
7th Edition
ISBN: 9780190698614
Author: Sadiku, Matthew N. O.
Publisher: Oxford University Press
expand_more
expand_more
format_list_bulleted
Concept explainers
Question
In an orthogonal machining with a tool of gº orthogonal rake angle, the uncut chip thickness is 0.2 mm. The chip thickness fluctuates between 0.25 mm and 0 4 mm what is the ratio of the maximum shear angle to the minimum shear angle during machining?
Expert Solution

This question has been solved!
Explore an expertly crafted, step-by-step solution for a thorough understanding of key concepts.
This is a popular solution
Trending nowThis is a popular solution!
Step by stepSolved in 3 steps

Knowledge Booster
Learn more about
Need a deep-dive on the concept behind this application? Look no further. Learn more about this topic, mechanical-engineering and related others by exploring similar questions and additional content below.Similar questions
- formula and calculationarrow_forward1. In a production turning operation, the cylindrical workpiece is 425 mm long and 190 mm in diameter, Feed 0.30 mm/rev. What cutting speed must be used to achieve a machining time of 7.0 min?arrow_forwardIn a production turning operation, the workpart is 60 mm in diameter and 500 mm long. A feed of 0.75 mm/rev is used in the operation. If cutting speed=9 m/s, the tool must be changed every 4 workparts; But if cutting speed=5 m/s, the tool can be used to produce 50 pieces between tool changes. Determine the Taylor tool life equation for this job. (use the equations given below for solution)arrow_forward
- The following data was obtained from an orthogonal cutting test. Rake angle = 20° Depth of cut = 6 mm Feed rate = 0.25 mm/rev Cutting speed = 0.6 m/s Chip length before cutting = 29.4 mm Vertical cutting force = 1050 N Horizontal cutting force = 630 N Chip length after cutting = 12.9 mm Using Merchant's analysis, calculate (a) Magnitude of resultant force, (b) shear plane angle, (c) friction force and friction angle, and (d) various energies consumed.arrow_forward1.) The rake angle in an orthogonal cutting operation is -5.736°. The chip thickness before the cut is 0.249 mm, and the resulting chip thickness after the cut is 0.762 mm. The chip thickness ratio is _ 2.) The rake angle in an orthogonal cutting operation is 17.995°. The chip thickness before the cut is 0.254 mm, and the resulting chip thickness after the cut is 0.595 mm. The shear plane angle is _ degrees. 3.) The rake angle in an orthogonal cutting operation is -2.804°. The chip thickness before the cut is 0.204 mm, and the resulting chip thickness after the cut is 0.556 mm. The shear strain is _. 4.) Microscopic examination of chips obtained from actual machining operations have revealed that they are produced by _. 5.) Low-carbon steel with 300 MPa tensile strength and 220 MPa shear strength is turned at 2.5 m/s cutting speed on a lathe. Feed (cutting width) is 0.20 mm/rev and depth of cut is 3.0 mm. Rake angle is 5°. The resulting chip ratio = 0.45. The cutting force is _ N…arrow_forwardIn turning of stales steel alloy, 1100 mm length and 400 mm diameter, the Feed was 0.35 mm/rev, and depth of cut = 2.5 mm. The tool used in this cutting is cemented carbide tool where Taylor tool life parameters are n = 0.24 and C = 450 (tool life (min) and cutting speed (m/min). Compute the cutting speed that will allow the tool life to be 10% longer than the machining time for this part.arrow_forward
- Rake angle=20 degree, Depth of cut=6 mm, Feed rate =0.25mm/rev,Cutting speed=0.6 m/s, chip length before cutting=29.4mm, vertical cutting force= 1050 NHorizontal cutting force=630, chip length after cutting=12.9Using Merchant’s analysis calculate(a) direction and magnitude of resultant force(b) friction force and friction angle(c) shear plane anglearrow_forwardIn a production turning operation, the workpart is 60 mm in diameter and 500 mm long. A feed of 0.75 mm/rev is used in the operation. If cutting speed-9 m/s, the tool must be changed every 4 workparts; But if cutting speed=5 m/s, the tool can be used to produce 50 pieces between tool changes. Determine the Taylor tool life equation for this job. (use the equations given below for solution) L Tm- 1,= Nf N AD, vT" = C %3| AD,L Tm fvarrow_forwardTurning Operation In a production turning operation, the foreman has decreed that a single pass must be completed on the cylindrical workpiece in 4.8 min. The piece is 400 mm long and 150 mm in diameter. Using a feed = 0.43 mm/rev and a depth of cut = 4.0 mm, what cutting speed must be used to meet this machining time requirement? Hint: Re-arrange the Tm equation to find v in m/min Tm= T.DO.L v.f 1.522arrow_forward
- A slab milling operation is performed to finish the top surface of a steel workpiece 250*75 mm*mm. this will be done with a helical milling cutter with 60 mm. diameter and 8 teeth. The cutting conditions are V=30m/min, f = 0.23 mm/tooth, and t= 6 mm. Find; a) The machining time of one pass. b) The metal remove rate.arrow_forwardIn a turning operation, cutting speed =200 m/min; feed = 0.25mm mm/rev, and depth of cut = 4.00mm Thermal diffusivity of the work material = 20m mm^2/s and volumetric specific heat =3.5(10^ -3 )J/mm^ 3 -C If the temperature increase above ambient temperature (20degreesC) is the angle measured by a tool-chip thermocouple to be 700degreesC, determine the specific energy for the work material in this operation.arrow_forwardQ1. Calculate the time required to machine a workpiece 170 mm long, 60 mm diameter to 165 mm long 50 mm diameter. The workpiece rotates at 440 rpm, feed is 0.3 mm/rev and maximum depth of cut is 2 mm. Assume total approach and overtravel distance as 5 mm for turning operation. Answer Q2. A gray cast iron surface 280 wide and 540mm long may be machined either on a vertical milling machine, using a 100mm - diameter face mill having eight inserted HSS teeth, or on a horizontal milling machine using an HSS slab mill with eight teeth on a 200-mm. diameter. Which machine has the faster cutting time? The values of feed per tooth and cutting speed for both processes are 0.4mm/tooth and 80m/min, respectively. The depth of cut = 3.0 mm and assume A and O equal to 5. Answerarrow_forward
arrow_back_ios
SEE MORE QUESTIONS
arrow_forward_ios
Recommended textbooks for you
- Elements Of ElectromagneticsMechanical EngineeringISBN:9780190698614Author:Sadiku, Matthew N. O.Publisher:Oxford University PressMechanics of Materials (10th Edition)Mechanical EngineeringISBN:9780134319650Author:Russell C. HibbelerPublisher:PEARSONThermodynamics: An Engineering ApproachMechanical EngineeringISBN:9781259822674Author:Yunus A. Cengel Dr., Michael A. BolesPublisher:McGraw-Hill Education
- Control Systems EngineeringMechanical EngineeringISBN:9781118170519Author:Norman S. NisePublisher:WILEYMechanics of Materials (MindTap Course List)Mechanical EngineeringISBN:9781337093347Author:Barry J. Goodno, James M. GerePublisher:Cengage LearningEngineering Mechanics: StaticsMechanical EngineeringISBN:9781118807330Author:James L. Meriam, L. G. Kraige, J. N. BoltonPublisher:WILEY
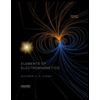
Elements Of Electromagnetics
Mechanical Engineering
ISBN:9780190698614
Author:Sadiku, Matthew N. O.
Publisher:Oxford University Press
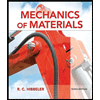
Mechanics of Materials (10th Edition)
Mechanical Engineering
ISBN:9780134319650
Author:Russell C. Hibbeler
Publisher:PEARSON
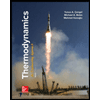
Thermodynamics: An Engineering Approach
Mechanical Engineering
ISBN:9781259822674
Author:Yunus A. Cengel Dr., Michael A. Boles
Publisher:McGraw-Hill Education
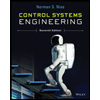
Control Systems Engineering
Mechanical Engineering
ISBN:9781118170519
Author:Norman S. Nise
Publisher:WILEY
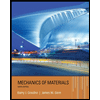
Mechanics of Materials (MindTap Course List)
Mechanical Engineering
ISBN:9781337093347
Author:Barry J. Goodno, James M. Gere
Publisher:Cengage Learning
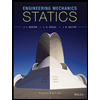
Engineering Mechanics: Statics
Mechanical Engineering
ISBN:9781118807330
Author:James L. Meriam, L. G. Kraige, J. N. Bolton
Publisher:WILEY