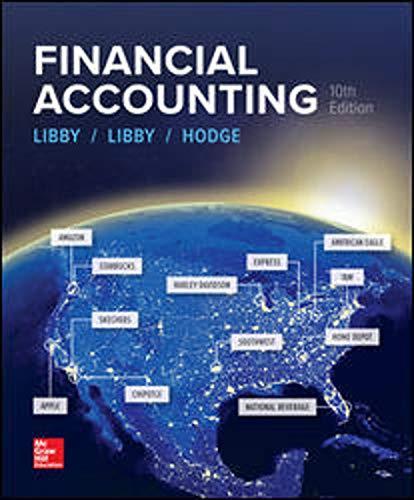
FINANCIAL ACCOUNTING
10th Edition
ISBN: 9781259964947
Author: Libby
Publisher: MCG
expand_more
expand_more
format_list_bulleted
Question
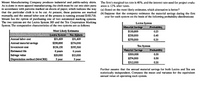
Transcribed Image Text:Mount Manufacturing Company produces industrial and public-safety shirts.
As is done in most apparel manufacturing, the cloth must be cut into shirt parts
in accordance with patterns marked on sheets of paper, which indicate the way
that the particular cloth is to be cut. At present, these patterns are marked
manually, and the annual labor cost of the process is running around $103,718.
Mount has the option of purchasing one of two automated marking systems.
The two systems are the Lectra System 305 and the Tex Corporation Marking
System. The comparative characteristics of the two systems are as follows:
The firm's marginal tax rate is 40%, and the interest rate used for project evalu-
ation is 12% after taxes.
(a) Based on the most likely estimates, which alternative is better?
(b) Suppose that the company estimates the material savings during the first
year for each system on the basis of the following probability distributions:
Lectra System
Material Savings
Probability
Most Likely Estimates
$150,000
0.25
Lectra System Tex Syatem
$230,000
0.40
Annual labor cost
$51,609
$51,609
$270,000
0.35
Annual material savings
$230,000
$274,000
Теx System
Material Suvings
Investment cost
$136,150
$195,500
Estimated life
6 уears
б уеars
Probubliity
$200,000
0.30
Salvage value
Depreciation method (MACRS)
$20,000
$15,000
5 year
5 year
$274,000
0.50
$312,000
0.20
Further assume that the annual material savings for both Lectra and Tex are
statistically independent. Compute the mean and variance for the equivalent
annual value of operating each system.
Expert Solution

This question has been solved!
Explore an expertly crafted, step-by-step solution for a thorough understanding of key concepts.
Step by stepSolved in 2 steps

Knowledge Booster
Learn more about
Need a deep-dive on the concept behind this application? Look no further. Learn more about this topic, accounting and related others by exploring similar questions and additional content below.Similar questions
- Oriole Stairs Co. designs and builds factory-made premium wooden stairways for homes. The manufactured stairway components (spindles, risers, hangers, hand rails) permit installation of stairways of varying lengths and widths. All are of white oak wood. Budgeted manufacturing overhead costs for the year 2025 are as follows. Purchasing Handling materials Production (cutting, milling, finishing) Setting up machines Overhead Cost Pools Inspecting Inventory control (raw materials and finished goods) Utilities Total budgeted overhead costs Purchasing Handling materials Production (cutting, milling, finishing) Setting up machines Inspecting Inventory control (raw materials and finished goods) Utilities Activity Cost Pools Direct labor For the last 4 years, Oriole Stairs Co. has been charging overhead to products on the basis of machine hours. For the year 2025, 100,000 machine hours are budgeted. Jeremy Nolan, owner-manager of Oriole Stairs Co., recently directed his accountant, Bill…arrow_forwardMuffin Factory (MF) bakes and sells muffins. MF buys materials from suppliers and bakes, frosts, and packages them for resale. Currently the firm offers 2 different types of muffins to gourmet bake shops in boxes, each containing a dozen muffins. The major cost is direct materials; however, a substantial amount of factory overhead is incurred in the baking, frosting, and packing process. MF prices its muffins at full product cost, including allocated overhead, plus a markup of 40%. Data for the current budget include factory overhead of $919,400, which has been allocated by its current costing system on the basis of each product’s direct labor cost. The budgeted direct labor cost for the current year totals $300,000. The budgeted direct costs for a one-dozen box of two of the company’s most popular muffins are as follows: Costs per one dozen Blueberry Cinnamon Activity Cost Driver Budgeted Activity Budgeted Cost Direct materials $…arrow_forwardThe Pittsburgh division of Vermont Machinery, Inc., manufactures drill bits.One of the production processes for a drill bit requires tipping, whereby carbide tips are inserted into the bit to make it stronger and more durable. This tipping process usually requires four or five operators, depending on the weekly workload. The same operators are also assigned to the stamping operation, where the size of the drill bit and the company's logo is imprinted on the bit. Vermont is considering acquiring three automatic tipping machines to replace the manual tipping and stamping operations. If the tipping process is automated, the division's engineers will have to redesign the shapes of the carbide tips to be used in the machine. The new design requires less carbide, resulting in savings on materials. The following financial data have been compiled: Project life: six years. Expected annual savings: reduced labor, $56,000; reduced material, $75,000; other benefits (reduced carpal tunnel syndrome…arrow_forward
- Rene is working with the operations manager to determine what the standard labor cost is for a spice chest. He has watched the process from start to finish and taken detailed notes on what each employee does. The first employee selects and mills the wood, so it is smooth on all four sides. This takes the employee 1 hour for each chest. The next employee takes the wood and cuts it to the proper size. This takes 30 minutes. The next employee assembles and sands the chest. Assembly takes 2 hours. The chest then goes to the finishing department. It takes 1.5 hours to finish the chest. All employees are cross-trained so they are all paid the same amount per hour, $14.50. A. What are the standard hours per chest? Standard hour per chest fill in the blank 1 hours B. What is the standard cost per chest for labor? Round your answer to two decimal places. Standard cost per chest $fill in the blank 2arrow_forwardMarigold, Ltd. manufactures shirts, which it sells to customers for embroidering with various slogans and emblems. The standard cost card for the shirts is as follows. Direct materials Direct labor Variable overhead Fixed overhead Indirect material Indirect labor Equipment repair Equipment power Total Supervisory salaries Insurance Property taxes Depreciation Standard Price $3 per yard $14 per DLH $3.20 per DLH $3 per DLH Utilities Quality inspection Total Sandy Robison, operations manager, was reviewing the results for November when he became upset by the unfavorable variances he was seeing. In an attempt to understand what had happened, Sandy asked CFO Suzy Summers for more information. She provided the following overhead budgets, along with the actual results for November. Annual Budget $449,000 The company purchased 82,000 yards of fabric and used 93,600 yards of fabric during the month. Fabric purchases during the month were made at $2.80 per yard. The direct labor payroll ran…arrow_forwardCoastal Cycles makes three models of electric bicycles: E20, E35, and E60. The models differ by the size of the battery and the quality of the components. The bicycles are produced in two departments. The Assembly Department purchases components from vendors and assembles them into bicycles. The models E20 and E35 are complete and ready for sale after completing the assembly process. The model E60 undergoes further process in Customization Department, which is actually just a small area in the same building as the Assembly Department. Conversion costs in both the Assembly Department and Customization Department are based on the number of units produced. There are never any work-in-process inventories. Data for production in November are shown in the following table. Total E20 E35 E60 Units produced 11,500 4,500 4,000 3,000 Materials cost $ 8,395,000 $ 2,250,000 $ 2,845,000 $ 3,300,000 Conversion costs…arrow_forward
- Bio Doc Corporation is a biotech company based in Milpitas. It makes a cancer-treatmentdrug in a single processing department. Direct materials are added at the start of the process.Conversion costs are added evenly during the process. Bio Doc uses the FIFO method of processcosting. The following information for July 2008 is available.arrow_forwardMcCourt Company produces two types of leather purses: standard and handcrafted. Both purses use equipment for cutting and stitching. The equipment also has the capability of creating standard designs. The standard purses use only these standard designs. They are all of the same size to accommodate the design features of the equipment. The handcrafted purses can be cut to any size because the designs are created manually. Many of the manually produced designs are in response to specific requests of retailers. The equipment must be specially configured to accommodate the production of a batch of purses that will receive a handcrafted design McCourt Company assigns overhead using direct labor dollars. Muggs Clark, sales manager, is convinced that the purses are not being costed correctly. To illustrate his point, he decided to focus on the expected annual setup and machine-related cut to. costs, which are as follows: Setup equipment $ 45,000 Depreciation 50,000…arrow_forwardShady Fabrication Group (SFG) manufactures components for manufacturing equipment at several facilities. The company produces two, related, parts at its Park River Plant, the models SF-08 and SF-48. The differences in the models are the quality of the materials and the precision to which they are produced. The SF-48 model is used in applications where the precision is critical and thus requires greater oversight in the production process. Although sales remain reasonably strong, managers at SFG have noticed that the company is meeting more resistance to the pricing for SF-08, although there seems to be little need for negotiation on the price of the SF-48 model. As a result, the marketing manager at SFG has asked the financial staff to review the costs of the two products to understand better what might be happening in the market. Manufacturing overhead is currently assigned to products based on their direct labor costs. For the most recent month manufacturing overhead was $208,800.…arrow_forward
- I need requirement 2 please.arrow_forwardCalifornia Circuits Company (3C) manufactures a variety of components. Its Valley plant specializes in two electronic components used in circuit boards. These components serve the same function and perform equally well. The difference in the two products is the raw material. The XL-D chip is the older of the two components and is made with a metal that requires a wash prior to assembly. Originally, the plant released the wastewater directly into a local river. Several years ago, the company was ordered to treat the wastewater before its release, and it installed relatively expensive equipment. While the equipment is fully depreciated, annual operating expenses of $260,000 are still incurred for wastewater treatment. Two years ago, company scientists developed an alloy with all of the properties of the raw materials used in XL-D that generates no wastewater. Some prototype components using the new material were produced and tested and found to be indistinguishable from the old…arrow_forwardCoastal Cycles makes three models of electric bicycles: E20, E35, and E60. The models differ by the size of the battery and the quality of the components. The bicycles are produced in two departments. The Assembly Department purchases components from vendors and assembles them into bicycles. The models E20 and E35 are complete and ready for sale after completing the assembly process. The model E60 undergoes further process in Customization Department, which is actually just a small area in the same building as the Assembly Department. Conversion costs in both the Assembly Department and Customization Department are based on the number of units produced. There are never any work-in-process inventories. Data for production in November are shown in the following table. Total E20 E35 E60 Units produced 9,400 3,800 3,300 2,300 Materials cost $ 6,868,000 $ 1,900,000 $ 2,508,000 $ 2,460,000 Conversion costs Assembly…arrow_forward
arrow_back_ios
SEE MORE QUESTIONS
arrow_forward_ios
Recommended textbooks for you
- AccountingAccountingISBN:9781337272094Author:WARREN, Carl S., Reeve, James M., Duchac, Jonathan E.Publisher:Cengage Learning,Accounting Information SystemsAccountingISBN:9781337619202Author:Hall, James A.Publisher:Cengage Learning,
- Horngren's Cost Accounting: A Managerial Emphasis...AccountingISBN:9780134475585Author:Srikant M. Datar, Madhav V. RajanPublisher:PEARSONIntermediate AccountingAccountingISBN:9781259722660Author:J. David Spiceland, Mark W. Nelson, Wayne M ThomasPublisher:McGraw-Hill EducationFinancial and Managerial AccountingAccountingISBN:9781259726705Author:John J Wild, Ken W. Shaw, Barbara Chiappetta Fundamental Accounting PrinciplesPublisher:McGraw-Hill Education
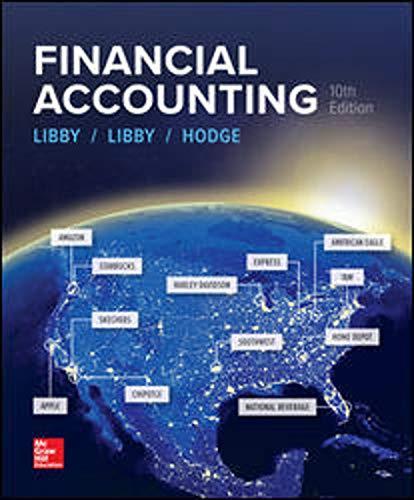
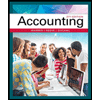
Accounting
Accounting
ISBN:9781337272094
Author:WARREN, Carl S., Reeve, James M., Duchac, Jonathan E.
Publisher:Cengage Learning,
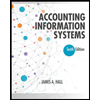
Accounting Information Systems
Accounting
ISBN:9781337619202
Author:Hall, James A.
Publisher:Cengage Learning,
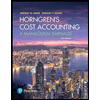
Horngren's Cost Accounting: A Managerial Emphasis...
Accounting
ISBN:9780134475585
Author:Srikant M. Datar, Madhav V. Rajan
Publisher:PEARSON
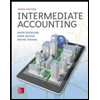
Intermediate Accounting
Accounting
ISBN:9781259722660
Author:J. David Spiceland, Mark W. Nelson, Wayne M Thomas
Publisher:McGraw-Hill Education
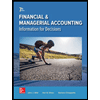
Financial and Managerial Accounting
Accounting
ISBN:9781259726705
Author:John J Wild, Ken W. Shaw, Barbara Chiappetta Fundamental Accounting Principles
Publisher:McGraw-Hill Education