Principles of Accounting Volume 2
19th Edition
ISBN: 9781947172609
Author: OpenStax
Publisher: OpenStax College
expand_more
expand_more
format_list_bulleted
Concept explainers
Topic Video
Question
Mostera manufactures two components A & B. There are to be 5000 of each component manufactured next year. The following information is available for each unit of A&B.
Machine Hrs Variable Cost
Unit of A 4 25
Unit of B 6 34
A total of 30,000 machine hours are available.
A sub-contractor is willing to supply Monstera with units of A & B for P27 and P38 respectively.
Advise Monstera whether to make or buy.
Expert Solution

This question has been solved!
Explore an expertly crafted, step-by-step solution for a thorough understanding of key concepts.
Step by stepSolved in 2 steps with 2 images

Knowledge Booster
Learn more about
Need a deep-dive on the concept behind this application? Look no further. Learn more about this topic, accounting and related others by exploring similar questions and additional content below.Similar questions
- Remarkable Enterprises requires four units of part A for every unit of Al that it produces. Currently, part A is made by Remarkable, with these per-unit costs in a month when 4,000 units were produced: Variable manufacturing overhead is applied at $1.60 per unit. The other $0.50 of overhead consists of allocated fixed costs. Remarkable will need 8,000 units of part A for the next years production. Altoona Corporation has offered to supply 8,000 units of part A at a price of $8.00 per unit. If Remarkable accepts the offer, all of the variable costs and $2,000 of the fixed costs will be avoided. Should Remarkable accept the offer from Altoona Corporation?arrow_forwardDimitri Designs has capacity to produce 30,000 desk chairs per year and is currently selling all 30,000 for $240 each. Country Enterprises has approached Dimitri to buy 800 chairs for $210 each. Dimitris normal variable cost is $165 per chair, including $50 per unit in direct labor per chair. Dimitri can produce the special order on an overtime shift, which means that direct labor would be paid overtime at 150% of the normal pay rate. The annual fixed costs will be unaffected by the special order and the contract will not disrupt any of Dimitris other operations. What will be the impact on profits of accepting the order?arrow_forwardBeat Company manufactures 8,000 units of a certain component per year. This component is used in the production of the main product. The following are the costs to make the component per unit: Direct materials $4 Direct labor $4 Variable overhead $3 Fixed overhead $5 If Beat Company buys the component from an outside supplier, the company can rent out the released facilities for P12,360 a year. The cost of the component per unit as quoted by the supplier is P15. 25% of fixed overhead applied in the manufacture of the component will continue regardless of what decision is made. For all purchase made by the company, freight and handling costs are applied at 2% of the purchase price. The direct materials cost presented above is exclusive of such freight and handling cost. What is the advantage or disadvantage of buying the component?A. P12,240 advantage B. 24,600 advantage C. 5,400 disadvantage D. 8,600 advantagearrow_forward
- Division Y has asked Division X of the same company to supply it with 6,600 units of part L763 this year to use in one of its products. Division Y has received a bid from an outside supplier for the parts at a price of $41 per unit. Division X has the capacity to produce 26,400 units of part L763 per year. Division X expects to sell 23,760 units of part L763 to outside customers this year at a price of $43.60 per unit. To fill the order from Division Y, Division X would have to cut back its sales to outside customers. Division X produces part L763 at a variable cost of $33 per unit. The cost of packing and shipping the parts for outside customers is $2 per unit. These packing and shipping costs would not have to be incurred on sales of the parts to Division Y. Required: a. What is the range of transfer prices within which both the Divisions' profits would increase as a result of agreeing to the transfer of 6,600 parts this year from Division X to Division Y? Note: Round your final…arrow_forwardSpecter Company makes 20,000 units per year of a part it uses in the products it manufactures.The unit product cost of this part is computed as follows:Direct materials $25.10Direct labour 18.20Variable manufacturing overhead 2.40Fixed manufacturing overhead 13.40Unit product cost $56.70An outside supplier has offered to sell the company all these parts it needs for $56.00 a unit. Ifthe company accepts this offer, the facilities now being used to make the part could be used tomake more units of a product that is in high demand. The additional contribution margin on thisother product would be $50,000 per year.If the part were purchased from the outside supplier, all the direct labour cost of the part wouldbe avoided. However, $5.10 of the fixed manufacturing overhead cost being applied to the partwould continue even if the part were purchased from the outside supplier. This fixedmanufacturing overhead cost would be applied to the company's remaining products.Required:Part a:Calculate…arrow_forwardOffice Expert Inc. produces a component which is required for manufacturing many of its appliances. The monthly production data for the component are as follows: Monthly Production Data for Component Production Data Amounts Number of units produced 2,500 units Variable costs per unit $10 per unit Total monthly fixed costs (allocated) $18,000 The company received an offer from a foreign supplier to purchase the component for $15 per unit. The monthly fixed costs are unavoidable. However, if Office Expert decides to purchase the component, they can use the freed manufacturing space to earn an additional revenue of $20,000 per month. If Office Expert decides to purchase from the foreign supplier, monthly operating income would – Group of answer choices Decrease by $24,000 Increase by $7,500 Increase by $25,500 Decrease by $12,500arrow_forward
- Every year Riverbed Industries manufactures 7,300 units of part 231 for use in its production cycle. The per unit costs of part 231 are as follows: Direct materials $ 5.00 Direct labor 11.00 Variable manufacturing overhead 6.00 Fixed manufacturing overhead 10.00 Total $32.00 Ivanhoe, Inc., has offered to sell 7,300 units of part 231 to Riverbed for $34 per unit. If Riverbed accepts Ivanhoe’s offer, its freed-up facilities could be used to earn $10,500 in contribution margin by manufacturing part 240. In addition, Riverbed would eliminate 40% of the fixed overhead applied to part 231.(a) Calculate total relevant cost to make and net cost to buy. Total relevant cost to make $enter a dollar amount Net relevant cost to buy $enter a dollar amount (b) Should Riverbed accept Ivanhoe’s offer?arrow_forwardHenderson Company is in the process of evaluating a new part using the following information .•Part SLC2002 has one production run each month, each with $16,000 in setup costs. •Part SLC2002 incurred $40,000 in development costs and is expected to be produced over the next three years. •Direct costs of producing Part SLC2002 are $56,000 per run of 24,000 parts each. •Indirect manufacturing costs charged to each run are $88,000. •Destination charges for each run average $18,000. •Part SLC2002 is selling for $12.50 in the United States and $25 in all other countries. Sales are one-third domestic and two-thirds exported. •Sales units equal production units each year. Required: a.What are the estimated life-cycle revenues? b.What is the estimated life-cycle operating income for the first year?arrow_forwardAbolt Corporation makes 40,000 units per year of a part it uses in the products it manufactures. The unit product cost of this part is computed as follows: direct materials $11.30 direct labour $22.70 variable manufacturing overhead $1.20 fixed manufacturing overhead $24.70 unit product cost $59.90 An outside supplier has offered to sell the company all of these parts it needs for$46.20 a unit. If the company accepts this offer, the facilities now being used tomake the part could be used to make more units of a product that is in highdemand. The additional contribution margin on this other product would be$264,000 per year. Additionally, $21.90 of the fixed manufacturing overheadcost being applied to the part would continue even if the part were purchasedfrom the outside supplier.Required:I. What is the net total dollar advantage (disadvantage) of purchasing the partrather than making it?II. Calculate the maximum amount per unit the company should be willing topay an…arrow_forward
- Steve company produces 30000 units of parts each year for use on its production line. The cost per units of the part S6: Direct material $3.60 Direct labor $10.00 Variable manufacturing overhead $2.40 Fixed manufacturing overhead $9.00 Total cost per part$25.00 An outside supplier has offered to sell 30000 units of the part each year at a product company at $21.00 per part. If the products company accepts this offer, the facilities now being used to manufacturer the parts could be rented by another company at the annual rent of $80,000.00. However, the products have determined that two-thirds of the fixed manufacturing overhead being applied to the part would continue even if the part S6 was purchased by an outside supplier. What is the advantage or disadvantage of accepting the outside supplier's offer? and how much ?arrow_forwardBeta makes a component used in its engine. Monthly production costs for 1,000 component units are as follows: Direct materials $46,000 Direct labor 11,500 Variable overhead costs 34,500 Fixed overhead costs 23,000 Total costs $115,000 It is estimated that 8% of the fixed overhead costs will no longer be incurred if the company purchases the component from an outside supplier. Beta has the option of purchasing the component from an outside supplier at $97.75 per unit. 22) If Beta accepts the offer from the outside supplier, the monthly avoidable costs (costs that will no longer be incurred) total 23) If Beta purchases 1,000 units from the outside supplier per month, then what would be the change in operating income?arrow_forwardAhrends Corporation makes 43,000 units per year of a part it uses in the products it manufactures. The unit product cost of this part is computed as follows: Direct materials Direct labor Variable manufacturing overhead Fixed manufacturing overhead Unit product cost $ 12.80 23.30 2.10 26.50 $ 64.70 An outside supplier has offered to sell the company all of these parts it needs for $51.00 a unit. If the company accepts this offer, the facilities now being used to make the part could be used to make more units of a product that is in high demand. The additional contribution margin on this other product would be $301,000 per year. If the part were purchased from the outside supplier, all of the direct labor cost of the part would be avoided. However, $23.40 of the fixed manufacturing overhead cost being applied to the part would continue even if the part were purchased from the outside supplier. This fixed manufacturing overhead cost would be applied to the company's remaining products.…arrow_forward
arrow_back_ios
SEE MORE QUESTIONS
arrow_forward_ios
Recommended textbooks for you
- Principles of Accounting Volume 2AccountingISBN:9781947172609Author:OpenStaxPublisher:OpenStax CollegePrinciples of Cost AccountingAccountingISBN:9781305087408Author:Edward J. Vanderbeck, Maria R. MitchellPublisher:Cengage Learning
Principles of Accounting Volume 2
Accounting
ISBN:9781947172609
Author:OpenStax
Publisher:OpenStax College
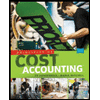
Principles of Cost Accounting
Accounting
ISBN:9781305087408
Author:Edward J. Vanderbeck, Maria R. Mitchell
Publisher:Cengage Learning