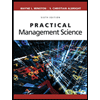
Concept explainers
Chapter 13 Homework
Kansas Furniture has received the following demand requirements:
Month Demand
July 1,000
August 1,200
September 1,400
October 1,800
November 1,800
December 1,600
Stockout costs are $100 per unit
Inventory costs are $25 per unit per month
No inventory left over from June for plans A, B, and D.
Plan A:
Produce at a steady rate equal to minimum requirements and subcontract the rest at $60 per unit. Store additional units in inventory. What is the total cost?
Plan B:
Vary the workforce. June’s production was 1,300 units. The cost of hiring is $3,000 per 100 units. The cost of layoffs is $6,000 per 100 units. What is the total cost?
Plan C:
Keep the current workforce steady at a level producing 1,300 units per month. Subcontract the remainder to meet demand at $60 per unit. Assume 300 units in inventory available at end of June and usable in July. What is the total cost?
Plan D:
Keep the current workforce steady at a level producing 1,300 units per month. Permit maximum overtime at 20% at $40 per unit. The warehouse can only store 180 units. Idle the plant at $60 per unit. Subcontract any additional units at $60 per unit. What is the total cost?

Trending nowThis is a popular solution!
Step by stepSolved in 4 steps with 8 images

- Discuss the role of cross-functional collaboration in effective aggregate planningarrow_forward#7 A toy manufacturing company has prepared its forecasted demand for the next six months. Develop an aggregate plan to meet this demand given this additional information. A level production rate of 100 units per month will be used. Backorders are allowed, and they are charged at the rate of RM10 per unit per month. Inverntory holding costs are RM2 per unit per month. Determine the cost of this plan if the regular time cost is RM20 per unit and the beginning inventory is zero. Month January February March Forecasted Demand 06 110 120 110 April Мay 100 June 90 Answer A RM12.20O 2014 - 2022 Chat With Us ENG 9.26 AM US 2/22/2022arrow_forwardDevelop a lot-for-lot solution and calculate total relevant costs for the gross requirements in the following table*. Period Gross requirements 1 2 20 3 4 56 7 8 9 10 11 12 30 30 60 20 20 80 60 *Holding cost $1.50/unit/week; setup cost $200; lead time = 1 week; beginning inventory = 40. Develop a lot-for-lot solution (enter your responses as whole numbers). Period Gross requirements On-hand at beginning of period On-hand at end of period 1 2 3 4 56 7 8 9 10 11 12 20 30 30 60 20 20 80 60 40 20 30 20 20 Order receipt Order releasearrow_forward
- The partially completed inventory record for the driveshaft subassembly in the table below shows gross requirements, scheduled receipts, lead time, and current on-hand inventory. a. Complete the last three rows of the record for an FOQ of 60 units. (Enter your responses as integers. A response of "0" is equivalent to being not applicable.) Item: Driveshaft subassembly Gross requirements Scheduled receipts Projected on-hand inventory Planned receipts 15 1 30 70 2 25 3 20 4 25 ☐☐ Lot Size: FOQ-60 units Lead Time: 3 weeks Week 5 35 6 35 7 60 8 60 00arrow_forwardFlora’s Fabulous Fountains’ (FFF) top product is its ModelA. Using the information given, draw the product structure treefor the Model Aarrow_forwardExplain what ABC production analysis consists of.arrow_forward
- Practical Management ScienceOperations ManagementISBN:9781337406659Author:WINSTON, Wayne L.Publisher:Cengage,Operations ManagementOperations ManagementISBN:9781259667473Author:William J StevensonPublisher:McGraw-Hill EducationOperations and Supply Chain Management (Mcgraw-hi...Operations ManagementISBN:9781259666100Author:F. Robert Jacobs, Richard B ChasePublisher:McGraw-Hill Education
- Purchasing and Supply Chain ManagementOperations ManagementISBN:9781285869681Author:Robert M. Monczka, Robert B. Handfield, Larry C. Giunipero, James L. PattersonPublisher:Cengage LearningProduction and Operations Analysis, Seventh Editi...Operations ManagementISBN:9781478623069Author:Steven Nahmias, Tava Lennon OlsenPublisher:Waveland Press, Inc.
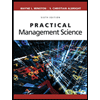
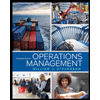
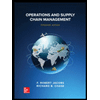
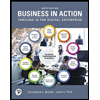
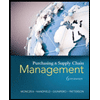
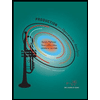