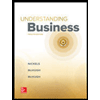
Understanding Business
12th Edition
ISBN: 9781259929434
Author: William Nickels
Publisher: McGraw-Hill Education
expand_more
expand_more
format_list_bulleted
Question
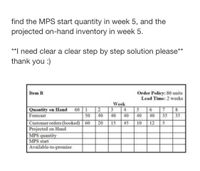
Transcribed Image Text:find the MPS start quantity in week 5, and the
projected on-hand inventory in week 5.
**I need clear a clear step by step solution please**
thank you :)
Order Policy: 80 units
Lead Time: 2 weeks
Item B
Week
Quantity on Hand
Forecast
60 1
50
2
3
4.
5
6.
8.
40
40
40
40
40
35
35
Customer orders (booked) | 60
Projected on Hand
MPS quantity
20
15
45
10
12
5.
MPS start
Available-to-promise
Expert Solution

This question has been solved!
Explore an expertly crafted, step-by-step solution for a thorough understanding of key concepts.
This is a popular solution
Trending nowThis is a popular solution!
Step by stepSolved in 4 steps with 4 images

Knowledge Booster
Similar questions
- • What is the Reorder Point (ROP)? • What is the fill rate? What is the average inventory? • What is the average flow time? Given Data: Coefficient of variation (CV) = 0.24 Average weekly demand = 540 units Standard deviation = 130 units Lead time=2 Lot size = 1641 Safety inventory: NORMSINV(0.95) = 1.64 Standard deviation * sqrt(2) * 1.64 130*√√2*1.64 301.51 301 = 301 unitsarrow_forwardQUESTION 2 When used effectively, S&OP Planning does not require cross-functional collaboration. O True Falsearrow_forwardThe president of Hill Enterprises, Terri Hill, projects the firm's aggregate demand requirements over the next 8 months as follows: 2,200 January 1,400 May February 1,600 June 2,200 March April 1,800 1,800 July August 1,800 1,400 Her operations manager is considering a new plan, which begins in January with 200 units of inventory on hand. Stockout cost of lost sales is $100 per unit. Inventory holding cost is $25 per unit per month. Ignore any idle-time costs. The plan is called plan C. Plan C: Keep a stable workforce by maintaining a constant production rate equal to the average gross requirements excluding initial inventory and allow varying inventory levels. Conduct your analysis for January through August.arrow_forward
- K Develop a lot-for-lot solution and calculate total relevant costs for the gross requirements in the following table*. Period 1 Gross requirements 30 Develop a lot-for-lot solution (enter your responses as whole numbers). Period Gross requirements On-hand at beginning of period On-hand at end of period Order receipt Order release 2 40 3 40 1 30 U 4 2 *Holding cost = $2.50/unit/week; setup cost = $150; lead time = 1 week; beginning inventory = 40. 5 6 7 30 70 20 3 40 8 4 9 10 10 80 5 6 7 30 70 20 8 11 9 10 D 12 50 10 11 12 80 50arrow_forwardQUESTION 15 ID-planned order release using EOQ technique Clancy's Motors has the following demand to meet for custom manufactured fuel injector parts. The holding cost for that item is $2 per month and each setup costs $80. Lead time is 0 months. Calculate the planned order releases using: the EOQ technique including the holding cost of any inventory left over after month 7? Month Requirement 1 400 What is the total cost? 2016 2509 1405 1536 2 150 3 200 150 100 150 250arrow_forwardDevelop a lot-for-lot solution and calculate total relevant costs for the gross requirements in the following table*. 5 6 7 30 70 30 9 10 11 12 60 10 70 Period 1 Gross requirements 20 2 Period Gross requirements On-hand at beginning of period 40 On-hand at end of period Order receipt Order release 3 40 1 20 4 *Holding cost = $3.50/unit/week; setup cost = $200; lead time = 1 week; beginning inventory = 40. Develop a lot-for-lot solution (enter your responses as whole numbers). 2 3 40 4 8 5 6 30 7 70 30 8 9 10 11 12 10 70 60 cornarrow_forward
- Inventory is not a property that is acquired for the purpose of resale in a business activity. Question 4 options: True Falsearrow_forwardPlease do not give solution in image format thankuarrow_forwardFlora’s Fabulous Fountains’ (FFF) top product is its ModelA. Using the information given, draw the product structure treefor the Model Aarrow_forward
arrow_back_ios
arrow_forward_ios
Recommended textbooks for you
- Understanding BusinessManagementISBN:9781259929434Author:William NickelsPublisher:McGraw-Hill EducationManagement (14th Edition)ManagementISBN:9780134527604Author:Stephen P. Robbins, Mary A. CoulterPublisher:PEARSONSpreadsheet Modeling & Decision Analysis: A Pract...ManagementISBN:9781305947412Author:Cliff RagsdalePublisher:Cengage Learning
- Management Information Systems: Managing The Digi...ManagementISBN:9780135191798Author:Kenneth C. Laudon, Jane P. LaudonPublisher:PEARSONBusiness Essentials (12th Edition) (What's New in...ManagementISBN:9780134728391Author:Ronald J. Ebert, Ricky W. GriffinPublisher:PEARSONFundamentals of Management (10th Edition)ManagementISBN:9780134237473Author:Stephen P. Robbins, Mary A. Coulter, David A. De CenzoPublisher:PEARSON
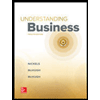
Understanding Business
Management
ISBN:9781259929434
Author:William Nickels
Publisher:McGraw-Hill Education
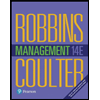
Management (14th Edition)
Management
ISBN:9780134527604
Author:Stephen P. Robbins, Mary A. Coulter
Publisher:PEARSON
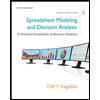
Spreadsheet Modeling & Decision Analysis: A Pract...
Management
ISBN:9781305947412
Author:Cliff Ragsdale
Publisher:Cengage Learning
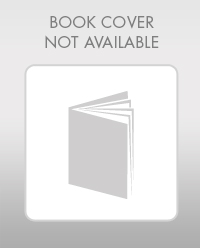
Management Information Systems: Managing The Digi...
Management
ISBN:9780135191798
Author:Kenneth C. Laudon, Jane P. Laudon
Publisher:PEARSON
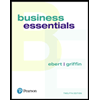
Business Essentials (12th Edition) (What's New in...
Management
ISBN:9780134728391
Author:Ronald J. Ebert, Ricky W. Griffin
Publisher:PEARSON
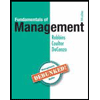
Fundamentals of Management (10th Edition)
Management
ISBN:9780134237473
Author:Stephen P. Robbins, Mary A. Coulter, David A. De Cenzo
Publisher:PEARSON