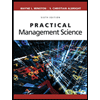
Practical Management Science
6th Edition
ISBN: 9781337406659
Author: WINSTON, Wayne L.
Publisher: Cengage,
expand_more
expand_more
format_list_bulleted
Concept explainers
Topic Video
Question
The question below is from the attached image of a video case file from Operations Management: Processes and Supply Chains (11th Edition) by by Krajewski, L. J., Malhotra, M. K. & Ritzman, L. P.
1. Explain how both independent and dependent demand items are present at Crayola.
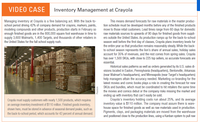
Transcribed Image Text:VIDEO CASE
Inventory Management at Crayola
Managing inventory at Crayola is a fine balancing act. With the back-to-
school period driving 42% of company demand for crayons, markers, paints,
modeling compounds and other products, production starts in February so
enough finished goods are in the 800,000 square foot warehouse in time to
supply 3,600 Walmarts, 1,400 Targets, and thousands of other retailers in
the United States for the fall school supply rush.
This means demand forecasts for raw materials in the master produc-
tion schedule must be developed months before any of the finished products
move to those retail customers. Lead times range from 60 days for domestic
raw materials sources to upwards of 90 days for finished goods from suppli-
ers outside the United States. As production ramps up for the back-to-school
season well before the first day of classes, Crayola plans inventory levels for
the entire year so that production remains reasonably steady. While the back-
to-school season represents the lion's share of annual sales, holiday sales
account for 35% of revenues, and the rest comes from spring sales. Crayola
has over 1,500 SKUS, with close to 225 top sellers, so accurate forecasts are
essential.
Historical sales patterns as well as orders generated by its U.S. sales di-
visions located in Easton, Pennsylvania (headquarters), Bentonville, Arkansas
(near Walmart's headquarters), and Minneapolis (near Target's headquarters)
help managers attain the accuracy needed. Marketing co-branding for the
latest movies and comic books plays a role in creating the forecast for new
SKUS and bundles, which must be coordinated to hit retailers the same time
the movies and comics debut or the company risks missing the market and
ending up with inventory that can't easily be sold.
Crayola's inventory holding costs run about 25%, and its average
inventory value is $110 million. The company must assure there is ware-
house space for finished goods as well as raw materials used in production.
Pigments, clays, and packaging materials are moved from the warehouse
and positioned close to the production lines, using a Kanban system to pull raw
Crayola must supply customers with nearly 1,500 products, which requires
an average inventory investment of $110 million. Finished goods inventory,
shown here, must be stored in advance of seasonal demand peaks, such as
the back-to-school period, which accounts for 42 percent of annual demand.
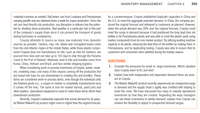
Transcribed Image Text:INVENTORY MANAGEMENT
CHAPTER 9
355
materials inventory as needed. Rail tanker cars from Louisiana and Pennsylvania
carying paraffin wax are delivered twice a week for crayon production. Since the
rail cars feed directly into production, any disruption in delivery has the poten-
tial for shutting down production. Bad weather is a particular risk in this part
of the company's supply chain since it can prevent the transport of goods
during hurricanes or snowstorms.
Crayola attempts to source as many raw materials from domestic
sources as possible. Cartons, clay, ink, labels and corrugated boxes come
from the mid-Atlantic region of the United States, while those plastic compo-
nents Crayola does not manufacture on site, such as nibs for markers, are
sourced from Asia and can take up to 120 days to ship through the Panama
Canal to the Port of Newark. Materials used in kits and bundles come from
As a countermeasure, Crayola established duplicate capacities in China and
the U.S. to meet the aggregate potential demand. In China, the company pro-
duced the original forecast and delivered to customers as planned. However,
when the actual demand was 26% over the original forecast, Crayola could
meet the surge in demand because it had positioned the long lead time ink
bottles in its Pennsylvania plants and was able to mold the plastic parts using
marker components from its core marker product. By utilizing existing machine
capacity in its plants, reducing the lead time of ink bottles by making them in
Pennsylvania, and by duplicating tooling, Crayola was able to ensure that its
customers and consumers were satisfied during the holiday season.
QUESTIONS
Korea, China, Vietnam and Brazil, and face similar shipping logistics.
When considering work-in-process inventories at Crayola, paints, mark-
ers, modeling clays, and many of the crayons coming off the production line
are boxed into trays for use downstream in creating kits and bundles. These
items are considered work-in-process items, even though the individual units
are finished goods (i.e., a crayon or marker is completely manufactured once
it comes off the line). The same is true for marker barrels, paint pots and
other plastics. Specialized equipment is used to make these items which feed
downstream production.
Recently, Crayola's leadership expected that actual demand for its popu-
lar Marker Maker© toy product might come in higher than the original forecast.
1. Consider the pressures for small vs. large inventories. Which situation
does Crayola seem to fit, and why?
2. Explain how both independent and dependent demand items are pres-
ent at Crayola.
3. The Marker Maker© product recently experienced an unexpected surge
in demand and the supply chain's agility was credited with helping to
meet the crisis. We have discussed four ways to classify operational
inventories by how they are created. Regarding the ways managers
can use these inventories to satisfy demand, explain how Crayola can
achieve the flexibility to adjust to unexpected demand surges.
Expert Solution

This question has been solved!
Explore an expertly crafted, step-by-step solution for a thorough understanding of key concepts.
This is a popular solution
Trending nowThis is a popular solution!
Step by stepSolved in 2 steps

Knowledge Booster
Learn more about
Need a deep-dive on the concept behind this application? Look no further. Learn more about this topic, operations-management and related others by exploring similar questions and additional content below.Similar questions
- Fanning Company and Finch Company both apply overhead to the Work in Process Inventory account using direct labor hours. The following information is available for both companies for the year. Actual manufacturing overhead Actual direct labor hours Underapplied overhead Overapplied overhead) Required Fanning Company Finch Company $ 145,750 $ 261,600 23,000 27,000 10,500 $ 21,000 a. Compute the predetermined overhead rate for each company. b. Using T-accounts, record the entry to close the overapplied or underapplied overhead at the end of the accounting period for each company, assuming the amounts are immaterial.arrow_forwardHau Lee Furniture, Inc., spends 45% of its sales dollars in the supply chain and finds its current profit of $15,000 inadequate. The bank is insisting on an improved profit picture prior to approval of a loan for some new equipment. Hau would like to improve the profit line to $20,000 so he can obtain the bank's approval for the loan. Current Situation Sales Cost of material $100,000 $45,000 (45%) Production costs Fixed cost Profit $25,000 (25%) $15,000 (15%) $15,000 (15%) a) What percentage improvement is needed in the supply chain strategy for profit to improve to $20,000? What is the cost of material with a $20,000 profit? A decrease of 11.1 % in material (supply-chain) costs is required to yield a profit of $20,000, for a new material cost of $40000. (Enter your response for the percentage decrease to one decimal place and enter your response for the new material cost as a whole number.)arrow_forwardDistinguish between multiprocessing and parallel processing. Explain the value chain and the supply chain to students B Give instances of what you're referring to.arrow_forward
- Samson is trying to solve the inventory needs for his fidget spinner business. He is in talks with two manufacturing businesses that can solve his problems. He is debating with himself if he should choose one or the other for his business. What role of Operations Management is Samson embodying in this scenario? (A) Storage and Inventory System (B Materials and Requisition Evaluation of Suppliers D Quality Control Managementarrow_forwardHow are operational scheduling and supply chain sustainability related? The issue is whether or not the company can make use of both.arrow_forward9.15 If the annual cost of goods sold is $30,000,000 and the average inventory is $5,000,000: a. What is the inventory turns ratio? b. What would be the reduction in average inventory if, through better materials management, inventory turns were increased to 10 times per year? c. If the cost of carrying inventory is 25% of the average inventory, what is the annual savings?arrow_forward
- part barrow_forwardAndrew Manufacturing held an average inventory of $1.5 million (raw materials, work-in-process, finished goods) last year. Its sales were $8.5 million, and its cost of goods sold was $6.2 million. The firm operates 290 days a year. What is the inventory days’ supply? What target inventory level is necessary to reach a 15- and 10-day inventory days supply during the next two years?arrow_forward8:02 ◄ Search Expert Q&A ☎ differentiation all can reduce the amount of inventory in the supply chain? Which of the following best explains why location pooling, lead-time pooling, and delayed Done All three strategies reduce the in-stock probability. O All three strategies make customers wait longer to receive their product. O All three strategies reduce the total lead time from the supply source (e.g., a factory) to the end consumer. All three strategies reduce the variability demand within the supply chain.arrow_forward
- Frank’s Contract Bakery measured her 2021 Cost of Goods Sold to be 6516265. Her Average Aggregate Inventory Value on raw materials was 2,310,000, work in process (WIP) was 1,500,000 and the finished goods was 1,400,000. Last year Days of Supply is: No decimalsarrow_forwardwith the complexity of the product range and the need for high levels of quality, she has found it difficult to influence sourcing strategy. Formal procurement procedures and systems at PEC are very limited. Currently, the buyer waits to receive a requisition from the production function to place orders for equipment, materials and products. This means that orders are usually urgent and the buyer has little opportunity to review alternative suppliers or sourcing approaches. Low value maintenance, repair and operations (MRO) requirements cause particular problems as the requisitions are difficult to aggregate. This causes excessive and time-consuming administration for the buyer. Testing requirements Pressure testing machinery used for testing the quality of seams in the protective work-wear is nearing the end of its life and will soon require replacement. Product testing is essential to confirm final quality of manufacture and conformance to industry standards. The test equipment is…arrow_forwardSupplier Raw Materials Inventory Management Production Question related to the diagram: Quality Control Packaging Finished Goods Distribution Retail Customer The process starts from the supplier, goes through raw materials, inventory management, production, quality control, packaging, finished goods, distribution, retail, and finally reaches the customer. How does the 'Inventory Management' stage interact with the 'Production' stage, and what strategies can be implemented to optimize this interaction?arrow_forward
arrow_back_ios
SEE MORE QUESTIONS
arrow_forward_ios
Recommended textbooks for you
- Practical Management ScienceOperations ManagementISBN:9781337406659Author:WINSTON, Wayne L.Publisher:Cengage,Operations ManagementOperations ManagementISBN:9781259667473Author:William J StevensonPublisher:McGraw-Hill EducationOperations and Supply Chain Management (Mcgraw-hi...Operations ManagementISBN:9781259666100Author:F. Robert Jacobs, Richard B ChasePublisher:McGraw-Hill Education
- Purchasing and Supply Chain ManagementOperations ManagementISBN:9781285869681Author:Robert M. Monczka, Robert B. Handfield, Larry C. Giunipero, James L. PattersonPublisher:Cengage LearningProduction and Operations Analysis, Seventh Editi...Operations ManagementISBN:9781478623069Author:Steven Nahmias, Tava Lennon OlsenPublisher:Waveland Press, Inc.
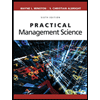
Practical Management Science
Operations Management
ISBN:9781337406659
Author:WINSTON, Wayne L.
Publisher:Cengage,
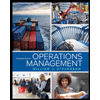
Operations Management
Operations Management
ISBN:9781259667473
Author:William J Stevenson
Publisher:McGraw-Hill Education
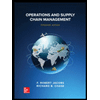
Operations and Supply Chain Management (Mcgraw-hi...
Operations Management
ISBN:9781259666100
Author:F. Robert Jacobs, Richard B Chase
Publisher:McGraw-Hill Education
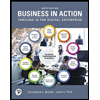
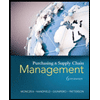
Purchasing and Supply Chain Management
Operations Management
ISBN:9781285869681
Author:Robert M. Monczka, Robert B. Handfield, Larry C. Giunipero, James L. Patterson
Publisher:Cengage Learning
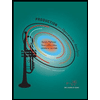
Production and Operations Analysis, Seventh Editi...
Operations Management
ISBN:9781478623069
Author:Steven Nahmias, Tava Lennon Olsen
Publisher:Waveland Press, Inc.