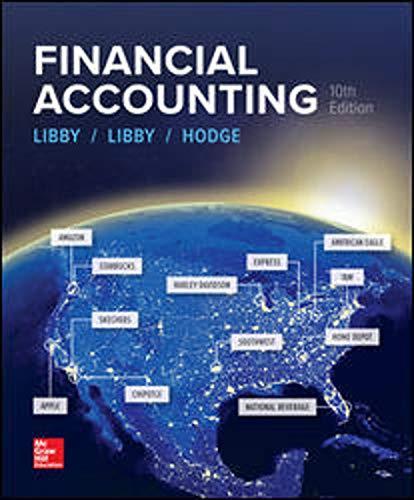
FINANCIAL ACCOUNTING
10th Edition
ISBN: 9781259964947
Author: Libby
Publisher: MCG
expand_more
expand_more
format_list_bulleted
Question
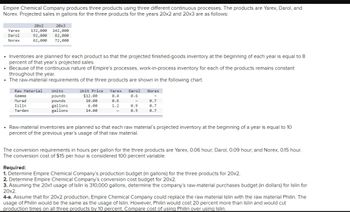
Transcribed Image Text:Empire Chemical Company produces three products using three different continuous processes. The products are Yarex, Darol, and
Norex. Projected sales in gallons for the three products for the years 20x2 and 20x3 are as follows:
Yarex
Darol
Norex
20x3
20x2
132,000 142,000
92,000 82,000
62,000 72,000
• Inventories are planned for each product so that the projected finished-goods inventory at the beginning of each year is equal to 8
percent of that year's projected sales.
• Because of the continuous nature of Empire's processes, work-in-process inventory for each of the products remains constant
throughout the year.
• The raw-material requirements of the three products are shown in the following chart.
Raw Material
Gamma
Murad
Islin
Tarden
Units
pounds
pounds
gallons
gallons
Unit Price
$12.00
10.00
6.00
14.00
Yarex Darol
0.4
0.6
0.6
1.2
-
0.9
0.5
Norex
0.7
0.7
0.7
• Raw-material inventories are planned so that each raw material's projected inventory at the beginning of a year is equal to 10
percent of the previous year's usage of that raw material.
The conversion requirements in hours per gallon for the three products are Yarex, 0.06 hour; Darol, 0.09 hour; and Norex, 0.15 hour.
The conversion cost of $15 per hour is considered 100 percent variable.
Required:
1. Determine Empire Chemical Company's production budget (in gallons) for the three products for 20x2.
2. Determine Empire Chemical Company's conversion cost budget for 20x2.
3. Assuming the 20x1 usage of Islin is 310,000 gallons, determine the company's raw-material purchases budget (in dollars) for Islin for
20x2.
4-a. Assume that for 20x2 production, Empire Chemical Company could replace the raw material Islin with the raw material Philin. The
usage of Philin would be the same as the usage of Islin. However, Philin would cost 20 percent more than Islin and would cut
production times on all three products by 10 percent. Compare cost of using Philin over using Islin.
Expert Solution

This question has been solved!
Explore an expertly crafted, step-by-step solution for a thorough understanding of key concepts.
This is a popular solution
Trending nowThis is a popular solution!
Step by stepSolved in 5 steps

Knowledge Booster
Learn more about
Need a deep-dive on the concept behind this application? Look no further. Learn more about this topic, accounting and related others by exploring similar questions and additional content below.Similar questions
- Suppose a company has 1,000 units of a raw material part on hand. If 750 of these units are routed into production, should the company place an order to stock up on more of these parts? (Show calculations). Determine the economic order quantity (EOQ) for this part, assuming the following:The company plans to use 10,000 units during the coming year.The company orders this part in lots of 1,000 units, and each order placed carries a processing cost of $2.50.Each unit of inventory carries an annual holding cost of $6.40.arrow_forwardFact Pattern: Atlas Foods produces the following three supplemental food products simultaneously through a refining process costing $93,000. The joint products, Alfa and Betters, have a final selling price of $4 per pound and $10 per pound, respectively, after additional processing costs of $2 per pound of each product are incurred after the split-off point. Morefeed, a by- product, is sold at the split-off point for $3 per pound. O A. $60,000 $31,000 $3,000 $30,000 O B. C. Alfa D. Betters Assuming Atlas Foods inventories Morefeed, the by-product, the joint cost to be allocated to Alfa using the net realizable value method is 10,000 pounds of Alfa, a popular but relatively rare grain supplement having a caloric value of 4,400 calories per pound 5,000 pounds of Betters, a flavoring material high in carbohydrates with a caloric value of 11,200 calories per pound Morefeed 1,000 pounds of Morefeed, used as a cattle feed supplement with a caloric value of 1,000 calories per poundarrow_forward. Quality Tea manufacturing company has given the following details for a particular process: During the month of June, 1,600 units were already in process, and another 10,000 units were started. At the end of the period, 8,600 units were completed. All of the Direct Materials (DM) are added at the beginning of the process; however, Conversion Costs (CC) are added evenly throughout the process. Quality follows the Weighted-Average method of inventory valuation. Ending Work-in-Progress (WIP) Inventory was two-thirds complete with respect to Conversion Costs. Find equivalent units in the ending WIP Inventory with respect to Conversion Costs. (Round units to whole number.) A) 1,000 units B) 2,000 units C) 3,000 units D) 8,600 unitsarrow_forward
- Hook Bait Incorporated processes king salmon for various distributors. Two departments are involved — processing and packaging. Data relating to tons of king salmon processed in the processing department during June 2020 are provided below: Tons of King Salmon Percent Completed Materials Conversion Work-in-process inventory — June 1 3,400 85 87 Work-in-process inventory — June 30 4,700 60 37 Started processing during June 9,600 Total equivalent units for materials under the weighted-average method are calculated to be: Multiple Choice 10,496 equivalent units. 8,010 equivalent units. 11,120 equivalent units. 7,865 equivalent units. 10,039 equivalent units.arrow_forward2. Lens Junction has required production of 15,400 units in January and 18,100 in February. Each lens consists of 2 pounds of silicon costing $2.50 per pound and 3 ounces of solution costing $3 per ounce. Desired inventory levels are: Jan. Feb. Mar. Beginning Inventory: Finished Goods (units) 4,500 4,900 5,000 DM - Silicon (pounds) 8,500 9,100 9,200 DM - Solution (ounces) 11,200 12,000 13,000 PLEASE NOTE: Units are rounded to whole numbers with commas as needed (i.e. 1,234) - no labels. All dollar amounts are rounded to whole dollars and shown with "$" and commas as needed (i.e. $12,345), except for any "per" amounts (units, pounds, ounces, or dollars), which are rounded to two decimal places and shown with "$" and commas as needed (i.e. $1,234.56) - no labels. Cost per Pound Desired Ending Inventory DM per Unit Ounces Needed for Production Required DM Ounces Pounds Needed for Production Units to be Produced Total Cost of DM Purchase Required DM Pounds…arrow_forwardVista Vacuum Company has the following production information for the month of March. All materials are added at the beginning of the manufacturing process. Units • Beginning inventory of 3,500 units that are 100 percent complete for materials and 23 percent complete for conversion. • 15,400 units started during the period. • Ending inventory of 3,400 units that are 14 percent complete for conversion. Manufacturing Costs • Beginning inventory was $20,200 ($8,900 materials and $11,300 conversion costs). • Costs added during the month were $29,600 for materials and $54,300 for conversion ($28,200 labor and $26,100 applied overhead). Assume the company uses Weighted-Average Method. Required: 1. Calculate the number of equivalent units of production for materials and conversion for March. 2. Calculate the cost per equivalent unit for materials and conversion for March. 3. Determine the costs to be assigned to the units transferred out and the units still in process. Complete this question…arrow_forward
- Dinesharrow_forwardCola Drink Company processes direct materials up to the splitoff point where two products, A and B, are obtained. The following information was collected for the month of July: Direct materials processed: 2,500 liters (with 20% shrinkage) Production: A 1,500 liters B 500 liters $15.00 per liter $10.00 per liter Sales: A В The cost of purchasing 2,500 liters of direct materials and processing it up to the splitoff point to yield a total of 2,000 liters of good products was $4,500. There were no inventory balances of A and B. Product A may be processed further to yield 1,375 liters of Product Z5 for an additional processing cost of $150. Product Z5 is sold for $25.00 per liter. There was no beginning inventory and ending inventory was 125 liters. Product B may be processed further to yield 375 liters of Product W3 for an additional processing cost of $275. Product W3 is sold for $30.00 per liter. There was no beginning inventory and ending inventory was 25 liters. 5. When using sales…arrow_forwardPT Y manufactures three products using the same production process. The costs incurred up to the split-off point are $200,000. The company decided to further process the three products before they were sold. The number of units produced (based on regular sales), the selling prices per unit of the three products at the split-off point and after further processing, and the additional processing costs are as follows. Product D E F Number of Units Produced 4,000 6,000 2,000 Selling Price at Split-Off Additional Processing Costs Selling Price after Processing $25.00 $26.60 $34.40 $14,000 $20,000 $9,000 $30.00 $31.20 $37.60 Instructions 1) Allocate the $200,000 joint cost to product D, E, and F using these methods: a. Physical-measure method (2%) b. NRV method (5%) 2) Which information is relevant to the decision on whether or not to process the products further? (2%). Explain why this information is relevant (2%). 3) Which product(s) should be processed further and which should be sold at…arrow_forward
arrow_back_ios
arrow_forward_ios
Recommended textbooks for you
- AccountingAccountingISBN:9781337272094Author:WARREN, Carl S., Reeve, James M., Duchac, Jonathan E.Publisher:Cengage Learning,Accounting Information SystemsAccountingISBN:9781337619202Author:Hall, James A.Publisher:Cengage Learning,
- Horngren's Cost Accounting: A Managerial Emphasis...AccountingISBN:9780134475585Author:Srikant M. Datar, Madhav V. RajanPublisher:PEARSONIntermediate AccountingAccountingISBN:9781259722660Author:J. David Spiceland, Mark W. Nelson, Wayne M ThomasPublisher:McGraw-Hill EducationFinancial and Managerial AccountingAccountingISBN:9781259726705Author:John J Wild, Ken W. Shaw, Barbara Chiappetta Fundamental Accounting PrinciplesPublisher:McGraw-Hill Education
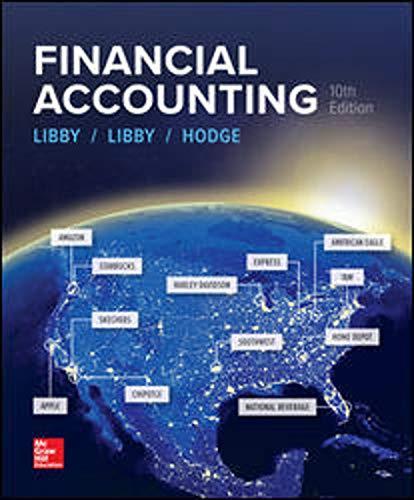
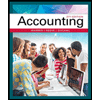
Accounting
Accounting
ISBN:9781337272094
Author:WARREN, Carl S., Reeve, James M., Duchac, Jonathan E.
Publisher:Cengage Learning,
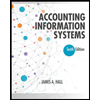
Accounting Information Systems
Accounting
ISBN:9781337619202
Author:Hall, James A.
Publisher:Cengage Learning,
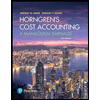
Horngren's Cost Accounting: A Managerial Emphasis...
Accounting
ISBN:9780134475585
Author:Srikant M. Datar, Madhav V. Rajan
Publisher:PEARSON
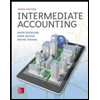
Intermediate Accounting
Accounting
ISBN:9781259722660
Author:J. David Spiceland, Mark W. Nelson, Wayne M Thomas
Publisher:McGraw-Hill Education
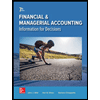
Financial and Managerial Accounting
Accounting
ISBN:9781259726705
Author:John J Wild, Ken W. Shaw, Barbara Chiappetta Fundamental Accounting Principles
Publisher:McGraw-Hill Education