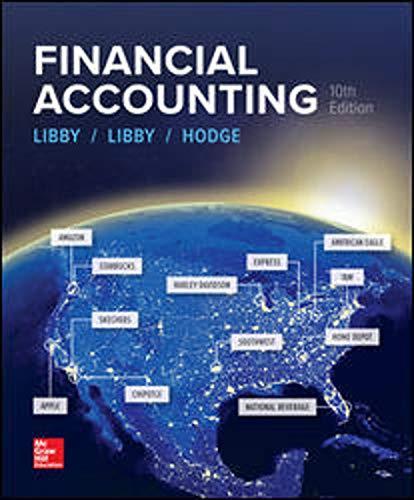
A Florida processing company, Sunshine ToGo, produces two products from a joint process: Alpha and Omega. Joint processing costs for this month's production cycle are $18,000.
Pounds |
Sales price per pound at split-off |
Disposal
cost per pound at split-off |
Further processing per pound |
Final sale price per pound |
|
Alpha |
1,260
|
$7.00
|
$4.50
|
$1.50
|
$ 8.00
|
Omega |
2,940
|
10.00
|
6.00
|
3.50
|
12.25
|
If Alpha and Omega are processed further, no disposal costs will be incurred or such costs will be borne by the buyer.
Using sales value at split-off, what amount of joint

Lets understand the basics.
In sales value at spllit off method, joint processing cost allocated to product using the sales value of the product against the total sales value.
Joint cost allocated to product = Total joint cost * (Sales value of joint product/Sales value of total product)
Trending nowThis is a popular solution!
Step by stepSolved in 2 steps

- 1arrow_forwardNeed help with question B sales vale at split off point. Please show how you got the numbers. I really need help calculating cost per liter for each product. Thanksarrow_forwardWindmire Company manufactures and sells to local wholesalers approximately 300,000 units per month at a sales price of $4 per unit. Monthly costs for the production and sale of this quantity follow. Direct materials $384,000 Direct labor 96,000 Overhead . 288,000 Selling expenses 120,000 Administrative expenses . 80,000 Total costs and expenses $968,000 A new out-of-state distributor has offered to buy 50,000 units next month for $3.44 each. These units would be marketed in other states and would not affect Windmire’s sales through its normal channels. A study of the costs of this new business reveals the following: ∙ Direct materials costs are 100% variable. ∙ Per unit direct labor costs for the additional units would be 50% higher than normal because their production would require overtime pay at 1½ times their normal rate to meet the distributor’s deadline. ∙ Twenty-five percent of normal annual overhead costs are fixed at any production level from 250,000 to 400,000 units. The…arrow_forward
- Fact Pattern: Atlas Foods produces the following three supplemental food products simultaneously through a refining process costing $93,000. The joint products, Alfa and Betters, have a final selling price of $4 per pound and $10 per pound, respectively, after additional processing costs of $2 per pound of each product are incurred after the split-off point. Morefeed, a by- product, is sold at the split-off point for $3 per pound. O A. $60,000 $31,000 $3,000 $30,000 O B. C. Alfa D. Betters Assuming Atlas Foods inventories Morefeed, the by-product, the joint cost to be allocated to Alfa using the net realizable value method is 10,000 pounds of Alfa, a popular but relatively rare grain supplement having a caloric value of 4,400 calories per pound 5,000 pounds of Betters, a flavoring material high in carbohydrates with a caloric value of 11,200 calories per pound Morefeed 1,000 pounds of Morefeed, used as a cattle feed supplement with a caloric value of 1,000 calories per poundarrow_forwardThe Happy Wimp Co. is in the business of processing corn into oil, sugar, meal, and chaff. Each month the Happy Wimp Co. processes 20,000 pounds. The yields, additional processing costs, and selling prices are: Sales Value at Product Yield Split-off Point Oil 200 lbs. $1.25 Sugar 200 lbs. .80 Meal 500 lbs..40 Chaff 100 lbs..10 Added Costs Price per lb. .50 per lb. $2.00 .30 per lb. 1.30 .60 .10 .20 per lb. 0 Joint processing costs per 1,000 pounds are: raw materials $100, labor $80, and depreciation $4,000/20 = $200; Total $380. Required: a.) Allocate the total joint costs to the different products according to the four allocation methods. Treat chaff as a main product. b.) Allocate the total joint costs to the different products according to the four allocation methods. Treat chaff as a by-product.arrow_forwarddarrow_forward
- kk.4arrow_forward2. Lens Junction has required production of 15,400 units in January and 18,100 in February. Each lens consists of 2 pounds of silicon costing $2.50 per pound and 3 ounces of solution costing $3 per ounce. Desired inventory levels are: Jan. Feb. Mar. Beginning Inventory: Finished Goods (units) 4,500 4,900 5,000 DM - Silicon (pounds) 8,500 9,100 9,200 DM - Solution (ounces) 11,200 12,000 13,000 PLEASE NOTE: Units are rounded to whole numbers with commas as needed (i.e. 1,234) - no labels. All dollar amounts are rounded to whole dollars and shown with "$" and commas as needed (i.e. $12,345), except for any "per" amounts (units, pounds, ounces, or dollars), which are rounded to two decimal places and shown with "$" and commas as needed (i.e. $1,234.56) - no labels. Cost per Pound Desired Ending Inventory DM per Unit Ounces Needed for Production Required DM Ounces Pounds Needed for Production Units to be Produced Total Cost of DM Purchase Required DM Pounds…arrow_forwardSubject: Acountingarrow_forward
- AccountingAccountingISBN:9781337272094Author:WARREN, Carl S., Reeve, James M., Duchac, Jonathan E.Publisher:Cengage Learning,Accounting Information SystemsAccountingISBN:9781337619202Author:Hall, James A.Publisher:Cengage Learning,
- Horngren's Cost Accounting: A Managerial Emphasis...AccountingISBN:9780134475585Author:Srikant M. Datar, Madhav V. RajanPublisher:PEARSONIntermediate AccountingAccountingISBN:9781259722660Author:J. David Spiceland, Mark W. Nelson, Wayne M ThomasPublisher:McGraw-Hill EducationFinancial and Managerial AccountingAccountingISBN:9781259726705Author:John J Wild, Ken W. Shaw, Barbara Chiappetta Fundamental Accounting PrinciplesPublisher:McGraw-Hill Education
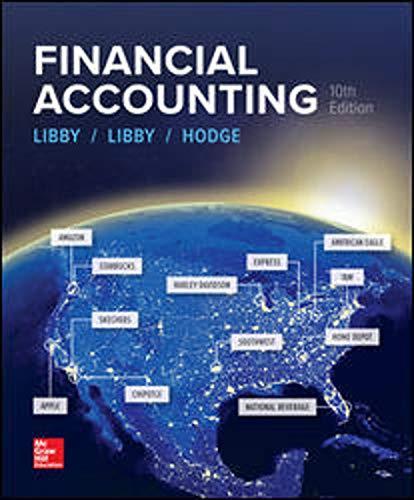
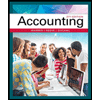
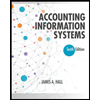
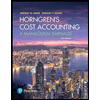
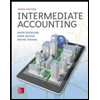
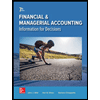