Destin Company produces water control valves, made of brass, that it sells primarily to builders for use in commercial real estate construction. These valves must meet rigid specifications (i.e., the quality tolerance is small). Valves that, upon inspection, get rejected are returned to the Casting Department; that is, they are returned to stage 1 of the four-stage manufacturing process. Rejected items are melted and then recast. As such, no new materials in Casting are required to rework these items. However, new materials must be added in the Finishing Department for all reworked valves. As the cost accountant for the company, you have prepared the following cost data regarding the production of a typical valve: Casting $ 220 Finishing Inspection $ 0 Packing $ 10 Total $ 240 Cost Direct materials $ 10 Direct labor 120 130 30 30 310 Variable manufacturing overhead 120 160 30 30 340 Allocated fixed overhead 80 90 50 20 240 $ 540 $ 390 $ 110 $ 90 $ 1,130 The company, spurred by intense price pressures from foreign manufacturers, recently initiated a number of quality programs. As a result, the rejection rate for valves has decreased from 5.4% to 3.5% of annual output (equal in total to 17,000 units). The reduction in reject rates has enabled the company to reduce its inventory holdings from $420,000 to $260,000. Destin estimates that the annual financing cost associated with inventory holdings is 11%. Required: 1. What are the estimated manufacturing cost savings per year associated with the reduction in rework costs? 2. What are the annual financing cost savings associated with the reduction in inventory holdings? 3. Provide a dollar estimate of the total annual cost savings associated with the recently enacted quality improvements. (Do not round intermediate calculations.) 1. Estimated annual manufacturing cost savings 2. Annual financing cost savings 3. Total estimated savings
Destin Company produces water control valves, made of brass, that it sells primarily to builders for use in commercial real estate construction. These valves must meet rigid specifications (i.e., the quality tolerance is small). Valves that, upon inspection, get rejected are returned to the Casting Department; that is, they are returned to stage 1 of the four-stage manufacturing process. Rejected items are melted and then recast. As such, no new materials in Casting are required to rework these items. However, new materials must be added in the Finishing Department for all reworked valves. As the cost accountant for the company, you have prepared the following cost data regarding the production of a typical valve: Casting $ 220 Finishing Inspection $ 0 Packing $ 10 Total $ 240 Cost Direct materials $ 10 Direct labor 120 130 30 30 310 Variable manufacturing overhead 120 160 30 30 340 Allocated fixed overhead 80 90 50 20 240 $ 540 $ 390 $ 110 $ 90 $ 1,130 The company, spurred by intense price pressures from foreign manufacturers, recently initiated a number of quality programs. As a result, the rejection rate for valves has decreased from 5.4% to 3.5% of annual output (equal in total to 17,000 units). The reduction in reject rates has enabled the company to reduce its inventory holdings from $420,000 to $260,000. Destin estimates that the annual financing cost associated with inventory holdings is 11%. Required: 1. What are the estimated manufacturing cost savings per year associated with the reduction in rework costs? 2. What are the annual financing cost savings associated with the reduction in inventory holdings? 3. Provide a dollar estimate of the total annual cost savings associated with the recently enacted quality improvements. (Do not round intermediate calculations.) 1. Estimated annual manufacturing cost savings 2. Annual financing cost savings 3. Total estimated savings
Cornerstones of Cost Management (Cornerstones Series)
4th Edition
ISBN:9781305970663
Author:Don R. Hansen, Maryanne M. Mowen
Publisher:Don R. Hansen, Maryanne M. Mowen
Chapter1: Introduction To Cost Management
Section: Chapter Questions
Problem 2E: Hepworth Communications produces cell phones. One of the four major electronic components is...
Related questions
Question

Transcribed Image Text:Destin Company produces water control valves, made of brass, that it sells primarily to builders for use in commercial real estate
construction. These valves must meet rigid specifications (i.e., the quality tolerance is small). Valves that, upon inspection, get rejected
are returned to the Casting Department; that is, they are returned to stage 1 of the four-stage manufacturing process. Rejected items
are melted and then recast. As such, no new materials in Casting are required to rework these items. However, new materials must be
added in the Finishing Department for all reworked valves. As the cost accountant for the company, you have prepared the following
cost data regarding the production of a typical valve:
Casting
$ 220
Finishing
$ 10
Inspection
$ 0
Packing
$ 10
Cost
Total
Direct materials
$ 240
Direct labor
120
130
30
30
310
Variable manufacturing overhead
120
160
30
30
340
Allocated fixed overhead
80
90
50
20
240
$ 540
$ 390
$ 110
$ 90
$ 1,130
The company, spurred by intense price pressures from foreign manufacturers, recently initiated a number of quality programs. As a
result, the rejection rate for valves has decreased from 5.4% to 3.5% of annual output (equal in total to 17,000 units). The reduction in
reject rates has enabled the company to reduce its inventory holdings from $420,000 to $260,000. Destin estimates that the annual
financing cost associated with inventory holdings is 11%.
Required:
1. What are the estimated manufacturing cost savings per year associated with the reduction in rework costs?
2. What are the annual financing cost savings associated with the reduction in inventory holdings?
3. Provide a dollar estimate of the total annual cost savings associated with the recently enacted quality improvements.
(Do not round intermediate calculations.)
1. Estimated annual manufacturing cost savings
2. Annual financing cost savings
3. Total estimated savings
Expert Solution

This question has been solved!
Explore an expertly crafted, step-by-step solution for a thorough understanding of key concepts.
This is a popular solution!
Trending now
This is a popular solution!
Step by step
Solved in 2 steps

Recommended textbooks for you
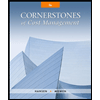
Cornerstones of Cost Management (Cornerstones Ser…
Accounting
ISBN:
9781305970663
Author:
Don R. Hansen, Maryanne M. Mowen
Publisher:
Cengage Learning
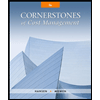
Cornerstones of Cost Management (Cornerstones Ser…
Accounting
ISBN:
9781305970663
Author:
Don R. Hansen, Maryanne M. Mowen
Publisher:
Cengage Learning