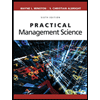
Concept explainers
Cogent Technology has computer stores on the West Coast. Their stores are set up like warehouse clubs focusing on high volume. Cogent Technology has a hub set up for their distribution. For instance, to serve the Silicon Valley area, a Cogent Technology warehouse is set up in San Jose to serve nearby stores. Cogent Technology warehouse managers generally purchase their items in bulk to get volume discounts from their vendors. Cogent Technology warehouse has an agreement with the vendors that they can return unsold inventory if it does not sell in six months. Cogent Technology has a policy of fulfilling all customer orders. In some cases when the store managers foresee a stockout situation, they are authorized to buy from other vendors rather than wait for the warehouse to deliver their items. In some cases, the prices bought directly by the store managers are cheaper than what the warehouses buy in bulk.
A good example of a sellable item is tablets. Cogent Technology warehouses purchase their stock from vendors based in Alum Rock, Berkeley, Concord, Daly City, and East Foothills and then ships it to its six stores in Silicon Valley. The vendors know that Cogent Technology retail stores are authorized to buy directly from other vendors so they decide to limit the number of tablets the warehouse can purchase. The table below shows the profit that Cogent Technology makes per tablet, based on which location the item is purchased and at which warehouse it is sold. The table also includes the available tablets per week at the retail locations and the display space available at each retail store per week.
1) Determine the most optimal model for Cogent Technology to maximize their profits. You may use a computer application to solve this problem.
2) If a Cogent Technology warehouse can buy all its tablets from a local store that will result in a profit of $7 per tablet at store 5; $8 per tablet at stores 2 and 6; and $9 per tablet at stores 1, 3, and 4, should Cogent Technology purchase all, some or none of its tablets from this vendor? Explain your answer quantitatively and qualitatively.
3) Recommend a strategy for Cogent Technology.
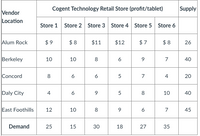

Trending nowThis is a popular solution!
Step by stepSolved in 9 steps with 6 images

- Which of the following defines Inbound Logistics the most? 1. The process of finding and purchasing goods and services for the needs of the supply chain. 2. The process of storage and transportation of finished products from a warehouse or distribution center to customers. 3. The process of acquiring raw materials and resources from suppliers and distributing them to manufacturing facilities. 4. The process of planning and control over the use of inventory to ensure that materials are available as required to meet production schedules.arrow_forwardYour options for shipping $96,970 of machine parts from Baltimore to Kuala Lumpur, Malaysia, are (1) use a ship that will take 32 days at a cost of $3,370, or (2) truck the parts to Los Angeles and then ship at a total cost of $5,180. The second option will take only 20 days. You are paid via a letter of credit the day the parts arrive. Your holding cost is estimated at 30% of the value per year. If you have a third option and it costs only $4,440 and also takes 20 days, what is your most economical plan? The daily holding cost of Alternative 1 is $ 79.70 . (Enter your response rounded to two decimal places.) The daily cost of faster shipping with Alternative 2 is $ 150.83. (Enter your response rounded to two decimal places.) The daily cost of faster shipping with Alternative 3 is $ (Enter your response rounded to two decimal places.)arrow_forwardValles Galactic Industries (VGI) owns a small company (VGI-Durango Sur) that manufactures various electronic products for original equipment manufacturers. Customer companies provide engineering designs, materials lists, and some unique materials. VGI-DS provides labor and space for the manufacturing and assembly operations and stocking a variety of inventory items for production, such as wire, cables, some electronic components, etc. Thus, VGI-DS orders a variety of components and raw materials by contract. The labor pool is primarily composed of about 100 retirees picking up extra cash by working four to six-hour shifts. Thus, the assembly operations must be simple and easy to teach. Skilled employees must do several raw material conversions for packaging—there are currently three such employees. VGI-DS receives forecasts from VGI headquarters for planned production for two years on a rolling quarterly basis. Staff at VGI-DS develop schedules and inventory plans based on this…arrow_forward
- The U.S. Airfilter company has hired you as a supply chain consultant. The company makes air filters for residential heating and air- conditioning systems. These filters are made in a single plant located in Louisville, Kentucky, in the United States. They are distributed to retailers through wholesale centers in 100 locations in the United States, Canada, and Europe. You have collected the following data relating to the value of inventory in the U.S. Airfilter supply chain: QUARTER 1 QUARTER 3 (JULY THROUGH QUARTER 4 QUARTER 2 (APRIL THROUGH JUNE) (JANUARY (OCTOBER THROUGH THROUGH MARCH) SEPTEMBER) DECEMBER) All amounts in millions of U.S. dollars Sales (total quarter): United states 356 532 552 436 Canada 130 127 116 151 Europe 42 34 49 24 Cost of goods sold (total quarter) 338 445 465 398 Raw materials at the Louisville plant (end-of-quarter) 93 49 79 89 Work-in-process and finished goods at the Louisville plant (end-of-quarter) 194 175 127 176 Distribution center inventory…arrow_forwardYour options for shipping $104,800 of machine parts from Baltimore to Kuala Lumpur, Malaysia, are (1) use a ship that will take 30 days at a cost of $3,370, or (2) truck the parts to Los Angeles and then ship at a total cost of $5,030. The second option will take only 18 days. You are paid via a letter of credit the day the parts arrive. Your holding cost is estimated at 30% of the value per year. If you have a third option and it costs only $4,080 and also takes 18 days, what is your most economical plan? Part 2 The daily holding cost of Alternative 1 is $________. (Enter your response rounded to two decimal places.) Part 3 The daily cost of faster shipping with Alternative 2 is $________. (Enter your response rounded to two decimal places.) Part 4 The daily cost of faster shipping with Alternative 3 is $________. (Enter your response rounded to two decimal places.) Part 5 ▼ Alternative 1? Alternative 2? Alternative 3? is more economical.arrow_forwardA business introduces e-purchasing and is able to process the same number of orders with lesser buyers. As a result of this: inventory pooling must be initiated inventory holding cost must be reduced purchase lead time should be reduced purchase quantity should be reducedarrow_forward
- Which one of the following happens at a supply point? Goods are created and consumed at this point. Goods are created at this node. Goods are passing through this point. Goods are consumed at this point.arrow_forwardIn this problem, your company is a distributor of products. You serve as an inventorymanager for the regional distribution center (DC) here in the Atlanta area. In this role,you schedule the purchase and shipment of products from various suppliers inbound to theAtlanta DC. Once you receive the products at the DC, they are stored in inventory untilthey are picked, packed, and shipped outbound to your company’s downstream customersin response to orders.For each of your products, you currently use a single, dedicated supplier. Each of yoursuppliers ships their products to you from their facility using trucking services, and theyprovide you with choices of different LTL or truckload trucking carriers depending on yourshipment size.Consider managing inventory now for product 101 produced by Supplier A. Currently,you face demand for product 101 of about 200 units per week. Each unit of product 101has a purchase cost p of $500 and you decide to value your inventory at the slightly higherrate…arrow_forwardIn this problem, your company is a distributor of products. You serve as an inventorymanager for the regional distribution center (DC) here in the Atlanta area. In this role,you schedule the purchase and shipment of products from various suppliers inbound to theAtlanta DC. Once you receive the products at the DC, they are stored in inventory untilthey are picked, packed, and shipped outbound to your company’s downstream customersin response to orders.For each of your products, you currently use a single, dedicated supplier. Each of yoursuppliers ships their products to you from their facility using trucking services, and theyprovide you with choices of different LTL or truckload trucking carriers depending on yourshipment size.Consider managing inventory now for product 101 produced by Supplier A. Currently,you face demand for product 101 of about 200 units per week. Each unit of product 101has a purchase cost p of $500 and you decide to value your inventory at the slightly higherrate…arrow_forward
- Need help! A-1 is incorrect.arrow_forwardIn the event that a physical retail establishment opts to utilize Fulfillment by Amazon (FBA), what measures would be taken to incorporate its information systems with those of Amazon?arrow_forwardAlgro Inc. keeps a wide range of parts and materials on hand for use in its production processes. Management has recently had difficulty managing parts inventory as demand for its finished goods has increased; they frequently run out of some critical parts while having an endless supply of others. They would like to classify their parts inventory according to the ABC approach to better control inventory. The following is a list of parts, along with their annual usage and unit value: Item Annual Unit Item Annual Unit Number Usage Cost Number Usage Cost 1 36 $350 2 510 30 3 50 23 4 300 45 5 18 1900 6 500 8 7 710 4 8 80 26 9 344 28 10 67 440 11 510 2 12 682 35 13 1216 95 50 14 10 3 15 820 1 KARAN2222222222 16 60 $610 17 120 20 18 270 15 19 45 50 20 19 3200 21 910 3 12 4750 23 30 2710 24 24 1800 25 870 105 26 244 30 27 750 15 28 45 110 29 46 160 30 165 25 a. Classify the inventory items according to the ABC approach using the dollar value of annual demand. b. Clearly explain why you…arrow_forward
- Practical Management ScienceOperations ManagementISBN:9781337406659Author:WINSTON, Wayne L.Publisher:Cengage,Operations ManagementOperations ManagementISBN:9781259667473Author:William J StevensonPublisher:McGraw-Hill EducationOperations and Supply Chain Management (Mcgraw-hi...Operations ManagementISBN:9781259666100Author:F. Robert Jacobs, Richard B ChasePublisher:McGraw-Hill Education
- Purchasing and Supply Chain ManagementOperations ManagementISBN:9781285869681Author:Robert M. Monczka, Robert B. Handfield, Larry C. Giunipero, James L. PattersonPublisher:Cengage LearningProduction and Operations Analysis, Seventh Editi...Operations ManagementISBN:9781478623069Author:Steven Nahmias, Tava Lennon OlsenPublisher:Waveland Press, Inc.
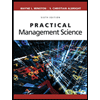
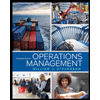
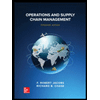
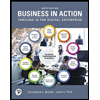
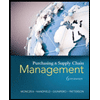
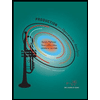