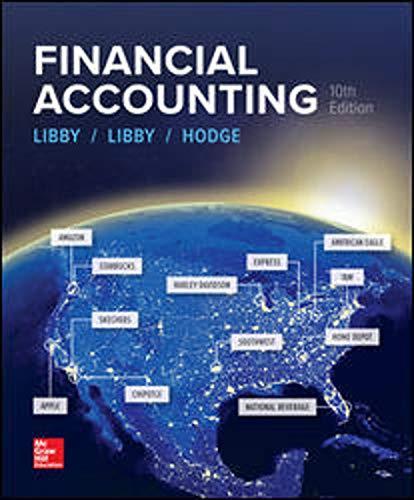
FINANCIAL ACCOUNTING
10th Edition
ISBN: 9781259964947
Author: Libby
Publisher: MCG
expand_more
expand_more
format_list_bulleted
Question
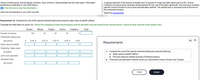
Transcribed Image Text:**Joint Cost Allocation in Poultry Processing**
**Background:**
Choice Chicken grows and processes chickens, disassembling each into five main parts: breast, wings, thighs, bones, and feathers. This information is based on production data from July 2020.
**Production Details:**
- A joint cost of production in July 2020 was $50.
- A special shipment of 60 pounds of breasts and 15 pounds of wings was destroyed in a fire.
- Choice Chicken needs to evaluate its financial reporting for this loss, using joint-cost allocation at the time of production.
- The split-off point is at the end of the production process.
**Table Explanation:**
The table is designed to complete joint cost allocation using the sales value at the split-off method. Each product type has a wholesale selling price per pound allocated for computation.
- **Products and Prices per Pound:**
- Breast: $0.45
- Wings: $0.25
- Thighs: $0.35
- Bones: $0.05
- Feathers: $0.05
- **Weights (in pounds):**
- Breast: 100
- Wings: 20
- Thighs: 30
- Bones: 45
- Feathers: 5
- **Columns to Compute:**
1. **Sales Value at Splitoff:**
- Calculate by multiplying the weight of each part by its price per pound.
2. **Weighting:**
- Express each product's sales value as a proportion of the total sales value.
3. **Joint Costs Allocated per Sales Value:**
- Allocate the joint costs ($50) based on weighted proportions.
**Requirements for Completion:**
1. **Cost Computation:**
- Calculate the cost of the special shipment destroyed using the sales value method.
- Present values rounded according to provided instructions.
2. **Allocation Method Recommendation:**
- Recommend a joint-cost allocation method for Choice Chicken, explaining your reasoning.
**Actionable Items:**
- Use the table to perform calculations.
- Review Requirements section for guidance on completion.
- Complete by filling all necessary values following rounding instructions.
This module helps understand joint cost allocation, a critical accounting practice, especially in scenarios with by-products or diversified outputs.
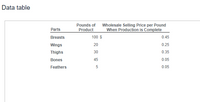
Transcribed Image Text:## Data Table Overview
The table provides detailed information on various parts of a product, measured in pounds, and their corresponding wholesale selling prices per pound once production is complete.
### Table Columns:
1. **Parts**: This column lists the different parts of the product. The parts included are:
- Breasts
- Wings
- Thighs
- Bones
- Feathers
2. **Pounds of Product**: This column indicates the total weight in pounds for each part of the product.
- Breasts: 100 pounds
- Wings: 20 pounds
- Thighs: 30 pounds
- Bones: 45 pounds
- Feathers: 5 pounds
3. **Wholesale Selling Price per Pound When Production is Complete**: This column shows the selling price for each pound of the product part at the wholesale level.
- Breasts: $0.45 per pound
- Wings: $0.25 per pound
- Thighs: $0.35 per pound
- Bones: $0.05 per pound
- Feathers: $0.05 per pound
This data can be useful for understanding the distribution of different product parts and their market value after processing.
Expert Solution

This question has been solved!
Explore an expertly crafted, step-by-step solution for a thorough understanding of key concepts.
This is a popular solution
Trending nowThis is a popular solution!
Step by stepSolved in 3 steps

Knowledge Booster
Learn more about
Need a deep-dive on the concept behind this application? Look no further. Learn more about this topic, accounting and related others by exploring similar questions and additional content below.Similar questions
- Munkoyo Ltd, a company based in Kasama, manufactures a variety of sweet beer which passes through a number of processes. One of Munkoyo’s products, the morning fresh, passes through processes 1,2 and 4 before being transferred to finished goods warehouse. For process 4, the following data is available for the month of November 2023: Work in progress, November 1, 2023: 3,000 litres, costing K38,800 Degree of completion: Direct materials added 60% Direct labour and overheads 40% Transferred from process 2; 24,000 units at K4.60 per litre Transferred to finished goods; 23,250 litres Incurred: Direct materials added K54,360 Direct labour K36,480 Production overheads K72,960 Work in progress, 30 November, 2013; 2,000 litres complete as: Direct material added 50% Direct labour and production overhead 30% Normal loss in process is 6% of units in opening work in progress plus transfers from process 2…arrow_forwardCalculating conversion costs and unit cost—FIFO methodSpring Fresh produces premium bottled water. Spring Fresh purchases artesian Water, stores the water in large tanks, and then runs the water through two processes: filtration and bottling. During February, the filtration process incurred the following costs in processing 200,000 liters: Spring Fresh had no beginning Work-in-Process Inventory in the Filtration Department in February. Requirements Use the FIFO method to compute the February conversion costs in the Filtration Department. The Filtration Department completely processed 200,000 liters in February. Use the FIFO method to determine the filtration cost per liter.arrow_forwardDeporte Company produces single-colored t-shirts. Materials for the shirts are dyed in large vats. After dying the materials for a given color, the vats must be cleaned and prepared for the next batch of materials to be colored. The following standards for changeover for a given batch have been established: 1 Direct materials (2.6 lbs. @ $0.95) $2.47 2 Direct labor (0.60 hr. @ $7.2) 4.32 3 Standard prime cost $6.79 During the year, 76,950 pounds of material were purchased and used for the changeover activity. There were 27,000 batches produced, with the following actual prime costs: Direct materials $60,979 Direct labor (for 16,155 hrs.) $114,341 Required: 1. Prepare a journal entry on Dec. 31 for the purchase of raw materials. Record the transaction as a compound entry. 2. Prepare a journal entry on Dec. 31 for the issuance of raw materials. Record the transaction as a compound entry. 3. Prepare a journal entry…arrow_forward
- K Fish Fillet Incorporated obtains fish and then processes them into frozen fillets and then prepares the frozen fish fillets for distribution to its retail sales department. Direct materials are added at the initiation of the cycle. Conversion costs are incurred evenly throughout the production cycle. Before inspection, some fillets are spoiled due to undetectable defects. Spoiled fillets generally constitute 4% of the good fillets. Data for April 2017 are as follows: 90,000 fillets WIP, beginning inventory 4/1/2017 Direct materials (100% complete) Conversion costs (50% complete) Started during April Completed and transferred out 4/30/2017 WIP, ending inventory 4/30/2017 Direct materials (100% complete) Conversion costs (25% complete) Costs for April: WIP, beginning Inventory: Direct materials Conversion costs Direct materials added Conversion costs added 135,000 fillets 189,000 fillets 26,000 fillets $135,000 100,910 303,000 388,130 What is the amount of direct materials and…arrow_forwardQuality Chicken grows and processes chickens. Each chicken is disassembled into five main parts. Information pertaining to production in July 2020 follows: (Click the icon to view the information.) Joint cost of production in July 2020 was $50. Data table Parts Breasts Wings Thighs Bones Feathers Pounds of Wholesale Selling Price per Pound Product When Production is Complete 100 $ 20 40 80 10 Print Done 0.55 0.20 0.35 0.10 0.05 X A special shipment of 40 pounds of breasts and 15 pounds of wings has been destroyed in a fire. Quality Chicken's insurance policy provides reimbursement for the cost of the items destroyed. The insurance company permits Quality Chicken to use a joint-cost-allocation method. The splitoff point is assumed to be at the end of the production process. Read the requirements. Requirements 1. Compute the cost of the special shipment destroyed using the following: a. Sales value at splitoff method b. Physical-measure method (pounds of finished product) 2. What…arrow_forwardThe Atlanta Company processes unprocessed goat milk up to the split-off point where two products, condensed goat milk and skim goat milk result. Total cost of purchasing and processing 120,000 gallons of goat milk in Joint Process was $144,000 which resulted into 35,640 gallons of goat milk and 72,360 gallons of skim goat milk (the remaining materials was shrinkage). Additional shrinkage occurred during additional processing as follows:Condensed 35,640 gallons of goat milk is processed further at $3.60 per gallon to yield 33,600 gallons of a medicinal milk product, called Xyla (the remainder is shrinkage). Xyla can be sold for $21.60 per gallon. The 72,360 gallons of Skim goat milk can be processed further at $2.40 per gallon to yield 64,800 gallons of skim goat ice cream. Each gallon of skim goat ice cream can be sold for $14.40 per gallon. The following information was collected for the month of March: Products Quantity yield at split off Additional processing cost per…arrow_forward
- Let's start with the joint cleaning and separation process, which allows for the cotton seed and the lint to be separately identifiable. The following quantities of cotton seed and lint were produced for a total cost (including the raw cotton and processing costs) of $232,000. 435,000 pounds of cotton seed 315,000 pounds of lint (fiber) Both of these products can be sold at this point, or they can be processed further. In their present state, they're worth: $0.13 per pound for cotton seed $0.75 per pound for lint This particular company presses the cotton seed to make oil and uses the lint to make thread. The additional costs and processes generate higher sales values for the final products, as follows. Seed/Oil Lint/Thread Additional cost $21,000 $79,200 Final sales value $84,000 $335,000 (a) (b) Allocate the joint process costs using the NRV method. (Round proportion to 3 decimal places, e.g. 0.251 and final answers to O decimal places, e.g. 5,125.) Share of joint cost $ Seed $ Lintarrow_forwardDouglass Minerals mines ore and then processes it into other products. At the end of the mining process, the ore splits off into three products: Metal-A, Metal-B, and Metal-C. Douglass sells Metal-C at the split-off point, with no further processing. Metal-A is processed in Plant A, and Metal-B is processed in Plant B. The following is a summary of costs and other related data for the period ended December 31: Process: Mining Plant A Plant B Labor $ 470,000 $ 406,000 $ 278,000 Manufacturing overhead $ 386,000 $ 338,800 $ 134,000 Products Metal-A Metal-B Metal-C Units sold 224,000 176,000 76,000 Units in ending inventory (December 31) 76,000 0 64,000 Sales revenue $ 1,120,000 $ 584,000 $ 190,000 Douglass Minerals had no beginning inventories on hand at the beginning of the period. Douglass Minerals uses the net realizable value method to allocate joint costs. Required: Compute the following: The net realizable value of Metal-C for the period ended December…arrow_forwardDura-Conduit Corporation manufactures plastic conduit that is used in the cable industry.A conduit is a tube that encircles and protects the underground cable. In the process for making the plastic conduit, called extrnsio11, the melted plastic (resin) is pressed through a die to form a tube.Scrap is produced in this process. Information from the cost of production reports for three months is as follows, assuming that inventory remains constant: Assume that there is one-half pound of 1·esin per foot of the finished product. Determine the resin materials cost per foot of finished product for each Round to the nearest whole cent. Determine the ratio of the number of resin pounds output in conduit by the number of pounds input into the process for each month. Round percentages to one decimal pl Interpret the resin materials cost per foot for the three months.Use the information in (a) and (b) to explain what is happening. Determine the conversion cost per foot of finished product…arrow_forward
- Deporte Company produces single-colored t-shirts. Materials for the shirts are dyed in large vats. After dying the materials for a given color, the vats must be cleaned and prepared for the next batch of materials to be colored. The following standards for changeover for a given batch have been established: 1 Direct materials (2.8 lbs. @ $0.80) $2.24 2 Direct labor (0.80 hr. @ $7.2) 5.76 3 Standard prime cost $8.00 During the year, 103,700 pounds of material were purchased and used for the changeover activity. There were 34,000 batches produced, with the following actual prime costs: Direct materials $66,622 Direct labor (for 27,143 hrs.) $192,111 Required: 1. Prepare a journal entry on Dec. 31 for the purchase of raw materials. Record the transaction as a compound entry. 2. Prepare a journal entry on Dec. 31 for the issuance of raw materials. Record the transaction as a compound entry. 3. Prepare a journal entry…arrow_forwardPet Products Company uses an automated process to manufacture its pet replica products. For June, the company had the following activities: Beginning work in process inventory 4,500 items, 1/4 complete with regards to conversion costs Units placed in production 15,000 units Units completed 17,500 units Ending work in process inventory 2,000 items, 3/4 complete with regards to conversion costs Cost of beginning work in process $5,250 Direct material costs, current $16,500 Conversion costs, current $23,945 Direct materials are placed into production at the beginning of the process and conversion costs are incurred evenly throughout the process. Prepare a production cost worksheet using the FIFO methodarrow_forwardDeporte Company produces single-colored t-shirts. Materials for the shirts are dyed in large vats. After dying the materials for a given color, the vats must be cleaned and prepared for the next batch of materials to be colored. The following standards for changeover for a given batch have been established: 1 Direct materials (2.4 lbs. @ $0.95) $2.28 2 Direct labor (0.75 hr. @ $7.40) 5.55 3 Standard prime cost $7.83 During the year, 79,500 pounds of material were purchased and used for the changeover activity. There were 30,000 batches produced, with the following actual prime costs: Direct materials $ 63,000 Direct labor (for 22,450 hrs.) $163,385 Required: 1. Prepare a journal entry on Dec. 31 for the purchase of raw materials. Record the transaction as a compound entry. 2. Prepare a journal entry on Dec. 31 for the issuance of raw materials. Record the transaction as a compound entry. 3. Prepare a journal entry…arrow_forward
arrow_back_ios
SEE MORE QUESTIONS
arrow_forward_ios
Recommended textbooks for you
- AccountingAccountingISBN:9781337272094Author:WARREN, Carl S., Reeve, James M., Duchac, Jonathan E.Publisher:Cengage Learning,Accounting Information SystemsAccountingISBN:9781337619202Author:Hall, James A.Publisher:Cengage Learning,
- Horngren's Cost Accounting: A Managerial Emphasis...AccountingISBN:9780134475585Author:Srikant M. Datar, Madhav V. RajanPublisher:PEARSONIntermediate AccountingAccountingISBN:9781259722660Author:J. David Spiceland, Mark W. Nelson, Wayne M ThomasPublisher:McGraw-Hill EducationFinancial and Managerial AccountingAccountingISBN:9781259726705Author:John J Wild, Ken W. Shaw, Barbara Chiappetta Fundamental Accounting PrinciplesPublisher:McGraw-Hill Education
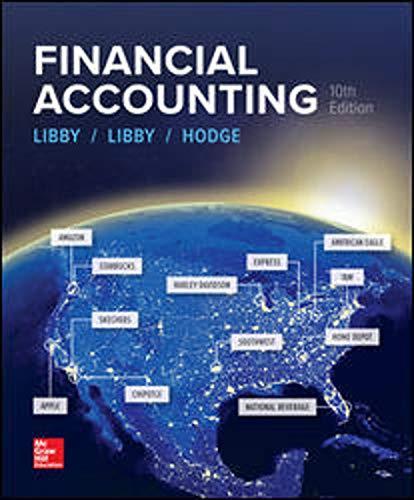
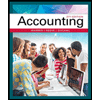
Accounting
Accounting
ISBN:9781337272094
Author:WARREN, Carl S., Reeve, James M., Duchac, Jonathan E.
Publisher:Cengage Learning,
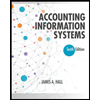
Accounting Information Systems
Accounting
ISBN:9781337619202
Author:Hall, James A.
Publisher:Cengage Learning,
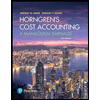
Horngren's Cost Accounting: A Managerial Emphasis...
Accounting
ISBN:9780134475585
Author:Srikant M. Datar, Madhav V. Rajan
Publisher:PEARSON
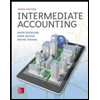
Intermediate Accounting
Accounting
ISBN:9781259722660
Author:J. David Spiceland, Mark W. Nelson, Wayne M Thomas
Publisher:McGraw-Hill Education
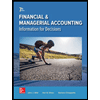
Financial and Managerial Accounting
Accounting
ISBN:9781259726705
Author:John J Wild, Ken W. Shaw, Barbara Chiappetta Fundamental Accounting Principles
Publisher:McGraw-Hill Education