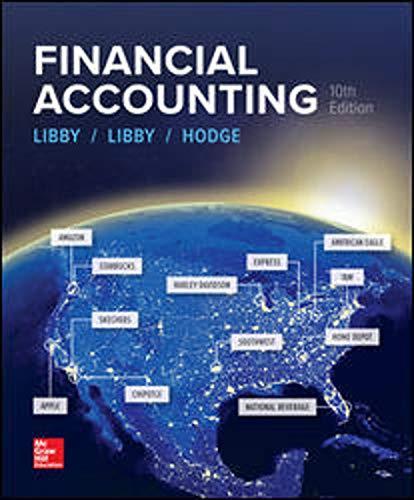
FINANCIAL ACCOUNTING
10th Edition
ISBN: 9781259964947
Author: Libby
Publisher: MCG
expand_more
expand_more
format_list_bulleted
Question

Transcribed Image Text:Quality Chicken grows and processes chickens. Each chicken is disassembled into five main parts.
Information pertaining to production in July 2020 follows:
(Click the icon to view the information.)
Joint cost of production in July 2020 was $50.
Data table
Parts
Breasts
Wings
Thighs
Bones
Feathers
Pounds of Wholesale Selling Price per Pound
Product When Production is Complete
100 $
20
40
80
10
Print
Done
0.55
0.20
0.35
0.10
0.05
X
A special shipment of 40 pounds of breasts and 15 pounds of wings has been destroyed in a fire.
Quality Chicken's insurance policy provides reimbursement for the cost of the items destroyed. The
insurance company permits Quality Chicken to use a joint-cost-allocation method. The splitoff point is
assumed to be at the end of the production process.
Read the requirements.
Requirements
1. Compute the cost of the special shipment destroyed using the following:
a. Sales value at splitoff method
b. Physical-measure method (pounds of finished product)
2. What joint-cost-allocation method would you recommend Quality Chicken use? Explain.
preferred method.
Print
Done
Expert Solution

This question has been solved!
Explore an expertly crafted, step-by-step solution for a thorough understanding of key concepts.
Step by stepSolved in 4 steps with 4 images

Knowledge Booster
Learn more about
Need a deep-dive on the concept behind this application? Look no further. Learn more about this topic, accounting and related others by exploring similar questions and additional content below.Similar questions
- Iguana, Inc., manufactures bamboo picture frames that sell for $25 each. Each frame requires 4 linear feet of bamboo, which costs $2.00 per foot. Each frame takes approximately 30 minutes to build, and the labor rate averages $12.00 per hour. Iguana has the following inventory policies: Ending finished goods inventory should be 40 percent of next month’s sales. Ending direct materials inventory should be 30 percent of next month’s production. Expected unit sales (frames) for the upcoming months follow: March 275 April 250 May 300 June 400 July 375 August 425 Variable manufacturing overhead is incurred at a rate of $0.30 per unit produced. Annual fixed manufacturing overhead is estimated to be $7,200 ($600 per month) for expected production of 4,000 units for the year. Selling and administrative expenses are estimated at $650 per month plus $0.60 per unit sold.Iguana, Inc., had $10,800 cash on hand on April 1. Of its sales, 80 percent is in cash. Of the…arrow_forwardBandar Industries manufactures sporting equipment. One of the company's products is a football helmet that requires special plastic. During the quarter ending June 30, the company manufactured 3,200 helmets, using 2,048 kilograms of plastic. The plastic cost the company $13,517. According to the standard cost card, each helmet should require 0.58 kilograms of plastic, at a cost of $7.00 per kilogram. Required: 1. What is the standard quantity of kilograms of plastic (SQ) that is allowed to make 3,200 helmets? 2. What is the standard materials cost allowed (SQ x SP) to make 3,200 helmets? 3. What is the materials spending variance? 4. What is the materials price variance and the materials quantity variance? Note: For requirements 3 and 4, indicate the effect of each variance by selecting "F" for favorable, "U" for unfavorable, and "None" for no effect (i.e., zero variance). Input all amounts as positive values. Do not round intermediate calculations. 1. Standard quantity of kilograms…arrow_forwardBandar Industries manufactures sporting equipment. One of the company's products is a football helmet that requires special plastic. During the quarter ending June 30, the company manufactured 3,800 helmets, using 2,812 kilograms of plastic. The plastic cost the company $21,371. According to the standard cost card, each helmet should require 0.66 kilogram of plastic, at a cost of $8.00 per kilogram. Required: 1. What is the standard quantity of kilograms of plastic (SQ) that is allowed to make 3,800 helmets? 2. What is the standard materials cost allowed (SQ x SP) to make 3,800 helmets? 3. What is the materials spending variance? 4. What are the materials price variance and the materials quantity variance? Note: For requirements 3 and 4, indicate the effect of each variance by selecting "F" for favorable, "U" for unfavorable, and "None" for no effect (i.e., zero variance). Input all amounts as positive values. Do not round intermediate calculations. 1. Standard quantity of kilograms…arrow_forward
- Quality Clothing, Inc., produces skorts and jumper uniforms for school children. In the process of cutting out the cloth pleces for each product, a certain amount of scrap cloth is produced. Quality has been selling this cloth scrap to Jorge's Scrap Warehouse for $3.30 p pound. Last year, the company sold 42,000 lb. of scrap, which would be enough to make 10,500 teddy bears that the management of Quality is now interested in producing. Their processes would need some reprogramming, particularly in the cutting and stitching processes, but it would require no additional worker training. However, new packaging would be needed. The total variable cost to produce the teddy bears $3.80. Fixed costs would increase by $93,000 per year for the lease of the packaging equipment and Quality estimates it could produce and sell 10,500 teddy bears per year. Finished teddy bears could be sold for $18.00 each. Calculate the effect on operating Income. Round your answers to the nearest dollar. Sell at…arrow_forwardParadise Marine Sails manufactures sails for sailboats. The company’s capacity is 29,000 sails per month. They are currently producing 25,000 sails a month. Current production cost can be found in the chart below: Sales Price $200 Variable Cost Manufacturing Cost $100 Administrative Cost $50 Total Fixed Cost Manufacturing $500,000 Administrative $480,000 Should you accept a special order at a price of $170 for 3000 sails? Fixed cost will increase by $9,000 to produce these sails. Give a numerical justification Would your answer be different if the company was currently producing 28,000 sails?arrow_forwardRelling Corporation manufactures a drink bottle, model CL24. During 2017, Relling produced 210,000 bottles at a total cost of $808,500. Kraff Corporation has offered to supply as many bottles as Relling wants at a cost of $3.75 per bottle. Relling anticipates needing 225,000 bottles each year for the next few years. Q. Can Relling use the answer in requirement 1a to determine the cost of manufacturing 225,000 drink bottles? Explain.arrow_forward
- PLEASE MAKE IT IN EXCEL AND SHOW THE FORMULAS Comercial El Suspiro, S.A., purchases 2'100,000 units per year of a component. The cost of each order is $25.00. The annual unit maintenance cost is 27% of its cost of $2.00. On a 360-day basis, calculate the reorder point, knowing that it takes 10.5 days for the supplier to put in the LAB company the goods, and the company sorts and stores them in 1.5 days, calculate the reorder point.arrow_forwardYou are required show ALL supportingworkings where necessary and state any assumption(s) made. _C-V-P AnalysisGreek Manufacturing Company produces and sells a line of product that are sold usually all year round. Thecompany has a maximum production capacity of 100,000 units per year. Operating at normal capacity, thebusiness earned Operating Income of $600,000 in 2020. The following cost data has been prepared for theyear ended December 31, 2020.Selling price per unit……………………………………… $50.00Production Costs:Direct Materials …………………………………. $10.00Direct Labour ……………………………………. $8.00Variable Manufacturing Overhead ……………. $7.00Fixed Manufacturing Overhead…………....................... $450,000Fixed Selling & Administrative Expenses……………… $300,000Variable selling expense per unit ………………………. $10.00Required: a. Using the equation method calculate the normal capacity of the business b.Assuming sales equal to the normal capacity calculated in (a) above, prepare a contribution margin income…arrow_forwardPlease help me with show calculation thankuarrow_forward
- Rubble, Inc. produced 1,000 backpacks, the company's product in 2020. The standard cost was 3 yards of cloth at a standard cost of $1.00 per yard. The accounting records show that 2,900 yards of cloth were used, and the company paid $1.05 per yard. Standard time to make the backpacks was 2 direct labor hours per unit at a standard rate of $9.75 per direct labor hours. Employees worked a total of 1,800 hours and were paid $9.25 per hour.1. Calculate the direct materials cost variance and the direct materials efficiency variance.arrow_forwardAshvinbhaiarrow_forwardThe Walton Toy Company manufactures four dolls and a sewing kit. It provided the following data for next year: Product Demand Next year (units) Selling Price per Unit Direct Materials Direct Labor Debbie 59,000 $ 30.00 $ 5.20 $ 2.10 Trish 51,000 $ 7.00 $ 2.00 $ 0.70 Sarah 44,000 $ 42.00 $ 7.79 $ 4.20 Mike 54,500 $ 12.00 $ 2.90 $ 2.80 Sewing kit 334,000 $ 8.90 $ 4.10 $ 0.35 The following additional information is available: The company’s plant has a capacity of 76,800 direct labor-hours per year on a single-shift basis. Each employee and piece of equipment are capable of making all five products. Next year’s direct labor pay rate will be $7 per hour. Fixed manufacturing costs total $610,000 per year. Variable overhead costs are $4 per direct labor-hour. All of the company’s nonmanufacturing costs are fixed. The company’s finished goods inventory is negligible and can be ignored. Required: How many direct labor-hours are used to manufacture one unit of each of the…arrow_forward
arrow_back_ios
arrow_forward_ios
Recommended textbooks for you
- AccountingAccountingISBN:9781337272094Author:WARREN, Carl S., Reeve, James M., Duchac, Jonathan E.Publisher:Cengage Learning,Accounting Information SystemsAccountingISBN:9781337619202Author:Hall, James A.Publisher:Cengage Learning,
- Horngren's Cost Accounting: A Managerial Emphasis...AccountingISBN:9780134475585Author:Srikant M. Datar, Madhav V. RajanPublisher:PEARSONIntermediate AccountingAccountingISBN:9781259722660Author:J. David Spiceland, Mark W. Nelson, Wayne M ThomasPublisher:McGraw-Hill EducationFinancial and Managerial AccountingAccountingISBN:9781259726705Author:John J Wild, Ken W. Shaw, Barbara Chiappetta Fundamental Accounting PrinciplesPublisher:McGraw-Hill Education
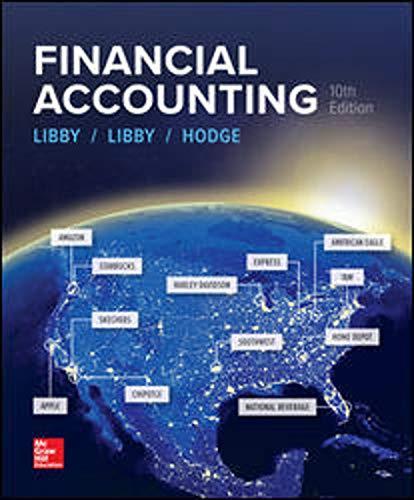
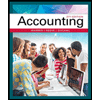
Accounting
Accounting
ISBN:9781337272094
Author:WARREN, Carl S., Reeve, James M., Duchac, Jonathan E.
Publisher:Cengage Learning,
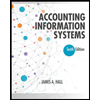
Accounting Information Systems
Accounting
ISBN:9781337619202
Author:Hall, James A.
Publisher:Cengage Learning,
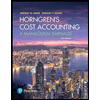
Horngren's Cost Accounting: A Managerial Emphasis...
Accounting
ISBN:9780134475585
Author:Srikant M. Datar, Madhav V. Rajan
Publisher:PEARSON
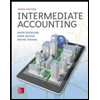
Intermediate Accounting
Accounting
ISBN:9781259722660
Author:J. David Spiceland, Mark W. Nelson, Wayne M Thomas
Publisher:McGraw-Hill Education
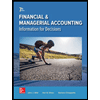
Financial and Managerial Accounting
Accounting
ISBN:9781259726705
Author:John J Wild, Ken W. Shaw, Barbara Chiappetta Fundamental Accounting Principles
Publisher:McGraw-Hill Education