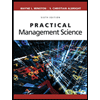
Practical Management Science
6th Edition
ISBN: 9781337406659
Author: WINSTON, Wayne L.
Publisher: Cengage,
expand_more
expand_more
format_list_bulleted
Concept explainers
Question
Charles Lackey operates a bakery in Idaho Falls, Idaho. Because of its excellent product and excellent location, demand has increased by
35%
in the last year. On far too many occasions, customers have not been able to purchase the bread of their choice. Because of the size of the store, no new ovens can be added. At a staff meeting, one employee suggested ways to load the ovens differently so that more loaves of bread can be baked at one time. This new process will require that the ovens be loaded by hand, requiring additional manpower. This is the only production change that will be made in order to meet the increased
demand.
The bakery currently makes
1,500
loaves per month. Employees are paid
$88
per hour. In addition to the laborcost, Charles also has a constant utility cost per month of
$800
and a per loaf ingredient cost of
$0.35
Current multifactor productivity for 640 work hours per month =
loaves/dollar (round your response to three decimal places).
Expert Solution

This question has been solved!
Explore an expertly crafted, step-by-step solution for a thorough understanding of key concepts.
This is a popular solution
Trending nowThis is a popular solution!
Step by stepSolved in 3 steps

Knowledge Booster
Learn more about
Need a deep-dive on the concept behind this application? Look no further. Learn more about this topic, operations-management and related others by exploring similar questions and additional content below.Similar questions
- WAI knows from historical records that approximately 40percent of its labor is used in Department 101 and 60 percentis used in Department 102. Th e reverse is true of machine time;60 percent is used in Department 101 and 40 percent is used inDepartment 102.(a) Calculate the labor and machine hours needed inDepartment 101 for each period of the MPS developed inProblem 4.(b) Calculate the labor and machine hours needed inDepartment 102 for each period of the MPS developed inProblem 4.arrow_forwardKrafts, Inc. uses the decentralized form of organization and considers each of its divisions as an investment center. Division A is currently selling 30,000 units of Part X annually, although it has sufficient production capacity to produce 42,000 parts per year. Variable manufacturing costs amount to P36 per part, while the total fixed costs amount to P180,000. These 30,000 parts are sold to outside market at P76 per part. Division S, also a part of the Krafts, Inc. has indicated that they would like to get from Division A 3,000 parts at a price of P74. Per part because they presently buying the parts from the outside supplier at that price. Assume that Division A could sell the entire 42,000 parts to outside market. What is the effect on the overall operating income of Krafts, Inc. if Division A will be required by the top management to sell 3,000 parts to Division S at a price of: a.) P36 b.)P74arrow_forwardThe production manager asked the foreman to achieve a target production of 200 units per day, but he doesn't give him the authority to requisition tools and materials from the stores department. Can the production manager blame the foreman if he is not able to achieve the desired target? Give reasons.arrow_forward
- Why is there a need to understand the manual computation of restaurant operations if there are point of sales already?arrow_forwardNonearrow_forwardA 25,000-seat college football stadium is used 20 times for games. Each event averages four hours and assumes the stadium is at 80% capacity for each event. The stadium is available 365 days a year from 8 a.m. to midnight. Use Equation 11.1: Utilization (U) = Resources Used/Resources Available Perform calculations. Provide calculations used and numerical response to #1. Provide detailed response for #2 (min one good paragraph.) What is the seat utilization? (Be careful here, this is total seat utilization. Be cautious when determining availability. Be specific.) As an operations manager, what could you do to improve seat utilization?arrow_forward
- Hi, I need help determining the correct answer to this Operations Management problem. Thank you!arrow_forwardNumber of Pickers (per Hour) 0 1 2 3 4 5 6 7 8 9 Total Strawberry Output (Boxes per Hour) 0 5 10 14 17 19 20 20 18 15 Price of Total Strawberries Revenue (per Box) (per Hour) $2 2 2 2 2 2 2 2 2 2 $0 10 20 28 34 38 40 40 36 30 Marginal Revenue New Price of Product Strawberries $10 10 8 6 + NO + -4 -6 $4 4 4 4 4 4 4 4 4 4 New Total Revenue (per Hour) How many pickers would be hired at $12 an hour after the price change? picker(s) New Marginal Revenue Productarrow_forwardThere are two competing alternatives in your textile business. A-type Tufting Machine costs $10,000 and B-Type Tufting Machine costs $10,000. A-type Tufting Machine can result in $7.000 labour savings in the first two years and $10.000 in year three. B-type Tufting Machine can result in $11.000 labour savings in the first two years. Assume MARR=20%. and find the difference between the net present worth of these two alternatives using infinite planning horizon with project repeatability. a) Between $6.480 and $6,700 O b) Between $5.480 and $5,700 O c) Between $2.480 and $2,700 d) None of the answers are correct O e) Between $4.480 and $4,700 f) Between $3,480 and $3.700arrow_forward
- Unilever Manufacturing operates year-round. The following data are pulled from thecompany’s most recent semi-annual report.Assets• Raw material inventory $120,000• Work-in-process inventory $50,000• Finished goods inventory $300,000• Property, plant, and equipment $500,000• Other assets $200,000• Total assets $1,150,000Condensed Income Statement• Revenue $2,000,000• Cost of goods sold $600,000• Other expenses $1,000,000• Net income $400,000Calculate the following based on a year duration:(a) Percentage invested in inventory (PIII);(b) Inventory turnover (TURNS); and(c) Weeks of supply (WOS)arrow_forwardTwo trouble-shooters handle service calls for 10 machines. The average time between service requirements is 18 days, and service time averages 2 days. Assume exponential distributions. While running, each machine can produce 1,500 pieces per day. Hint: Finite Source Determine: (i) the percentage of time trouble-shooters are idle (ii) each machine's net productivity (iii) If trouble-shooters represent a cost of $150 per day, and machine downtime cost is $600 per day, would another trouble-shooter be justified? Explain.arrow_forward63- The biggest difference among football teams in terms of revenue-generating capacity is A- luxury box revenue B- local television in the city C- the cost of living in the city D- memorabilia salesarrow_forward
arrow_back_ios
SEE MORE QUESTIONS
arrow_forward_ios
Recommended textbooks for you
- Practical Management ScienceOperations ManagementISBN:9781337406659Author:WINSTON, Wayne L.Publisher:Cengage,Operations ManagementOperations ManagementISBN:9781259667473Author:William J StevensonPublisher:McGraw-Hill EducationOperations and Supply Chain Management (Mcgraw-hi...Operations ManagementISBN:9781259666100Author:F. Robert Jacobs, Richard B ChasePublisher:McGraw-Hill Education
- Purchasing and Supply Chain ManagementOperations ManagementISBN:9781285869681Author:Robert M. Monczka, Robert B. Handfield, Larry C. Giunipero, James L. PattersonPublisher:Cengage LearningProduction and Operations Analysis, Seventh Editi...Operations ManagementISBN:9781478623069Author:Steven Nahmias, Tava Lennon OlsenPublisher:Waveland Press, Inc.
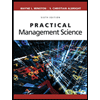
Practical Management Science
Operations Management
ISBN:9781337406659
Author:WINSTON, Wayne L.
Publisher:Cengage,
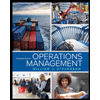
Operations Management
Operations Management
ISBN:9781259667473
Author:William J Stevenson
Publisher:McGraw-Hill Education
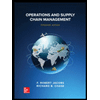
Operations and Supply Chain Management (Mcgraw-hi...
Operations Management
ISBN:9781259666100
Author:F. Robert Jacobs, Richard B Chase
Publisher:McGraw-Hill Education
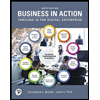
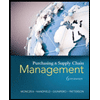
Purchasing and Supply Chain Management
Operations Management
ISBN:9781285869681
Author:Robert M. Monczka, Robert B. Handfield, Larry C. Giunipero, James L. Patterson
Publisher:Cengage Learning
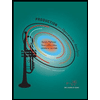
Production and Operations Analysis, Seventh Editi...
Operations Management
ISBN:9781478623069
Author:Steven Nahmias, Tava Lennon Olsen
Publisher:Waveland Press, Inc.