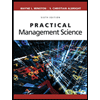
Carlos Cavalas, the manager of Echo Products’ Brazilian Division, is trying to set the production
Units | |
---|---|
Inventory, January 1 | 0 |
Production | 71,100 |
Sales | 63,700 |
Inventory, September 30 | 7,400 |
The division can rent warehouse space to store up to 30,500 units. The minimum inventory level that the division should carry is 2,800 units. Mr. Cavalas is aware that production must be at least 4,440 units per quarter in order to retain a nucleus of key employees. Maximum production capacity is 44,200 units per quarter.
Demand has been soft, and the sales
Required:
1a. Assume that the division is using variable costing. How many units should be scheduled for production during the last quarter of the year?
1b. Assume that the division is using variable costing. Will the number of units scheduled for production affect the division’s reported income or loss for the year?
2. Assume that the division is using absorption costing and that the divisional manager is given an annual bonus based on divisional operating income. If Mr. Cavalas wants to maximize his division’s operating income for the year, how many units should be scheduled for production during the last quarter?

Trending nowThis is a popular solution!
Step by stepSolved in 2 steps with 2 images

- Need answer ASAP. Please include the solution for the problem. Thank you.arrow_forwardWhat role does demand variability play in the Wilson Approach, and how can it be managed effectively?arrow_forwardGiven the following information: 2022 2021 Ending inventory $52,650 $20,490 Cost of goods sold. $306,300 $213,600 What is average days in inventory for 2022? 24 days 35 days 44 days 90 daysarrow_forward
- 2. Complete the following grid using the weeks-of-supply method: Plan Sales for a Week $5,000 $8,000 $9,100 $500 $21,000 Annual Turnover 2.0 4.0 8.0 10.0 16.0 Weeks of Supply Inventoryarrow_forward7. Inventory at Sports Haven was $326,790 on September 1 and $166,388 on September 30. What was the average inventory for September?arrow_forwardForecast Data is given within problem. Cost Data is attached Southeast Soda Pop, Inc., has a new fruit drink for which it has high hopes. John Mittenthal, the production planner, has assembled the following cost data and demand forecast: LOADING... Click the icon to view the demand forecast. LOADING... Click the icon to view the cost data. John's job is to develop an aggregate plan. The three initial options he wants to evaluate are: • Plan A: a strategy that hires and fires personnel as necessary to meet the forecast. • Plan B: a level strategy. • Plan C: a level strategy that produces 1,000 cases per quarter and meets the forecast demand with inventory and subcontracting. Part 2 a) Which strategy is the lowest-cost plan? Try hiring and layoffs (to meet the forecast) as necessary (enter your responses as whole numbers). Hiring and Layoff Plan Quarter Forecast Production Hire (Units) Layoff (Units)…arrow_forward
- When calculating the cycle time, 8*60*60/520, where did the 60 came from?arrow_forwardTable 5.1: The demand forecast developed for the year ended 31 December 2022. Month Production days Demand forecast Jan 16 150 Feb 16 150 Mar 23 250 Apr 21 250 May 22 400 Jun 22 500 Jul 21 600 Aug 20 750 Sep 20 450 Oct 20 250 Nov 16 150 Dec 16 150 1. Compute and tabulate the daily demand for each month in the table below (round off to the nearest whole number). 2. Assuming that MPQ Limited had adopted a level strategy for the year ended 31 December 2022, compute the average daily demand for the year (round off to the nearest whole number).arrow_forwardGregory has started a small agricultural business that specialises in maize and sunflower seeds inGrey Town, KZN. His produce is AgriSA approved, and his organisation is looking to hire a supply chain management consultant given their impact and contribution to the local economy. You have been recruited by Gregory, assist him with the following questions: Gregory is uncertain as to which replenishment system he should use. Differentiate between the continuous review and periodic review models and suggest the most suited for him with the aid of at least two practical examples.Note: you are required to provide a paraphrased overview of the models before at least two practical examples are provided to support the choice.arrow_forward
- Crystal Clear Health Drinks: A health drink production company, Crystal Clear Health Drinks, decides to introduce a new line of health drink that will include several flavours. The marketing team forecasts an increase in demand for the new line of product; this is due to the growing popularity of the idea of living healthier lifestyles. They prepare the following aggregate forecasts (tank loads of several flavours) for the next six-month planning horizon: May: 50 June: 60 July: 70 August: 90 September: 80 October: 70 The operations team prepared the following information: 1. The production line has the capacity to produce 60 tank loads per month in regular time at the cost of R10,000 per tank load. 2. Overtime production and subcontracting to the available suppliers cost R16,000 and R18,000 per tank load, respectively. 3. The cost to hold one tank load for one month is R2,000. 4. Demand can also be back-ordered at the cost of R5,000 per month. 5. The company has no starting inventory…arrow_forwardMonth Item 1 Item 2 Item 3 Item 4 1 751 250 666 287 2 741 268 618 352 3 728 289 483 416 4 773 314 375 313 5 718 337 303 359 6 752 367 242 440 7 736 391 210 520 8 768 409 239 391 9 729 433 342 449 10 777 459 396 550 11 748 481 457 650 12 756 500 587 489 Make a demand forecast for the next six periods for each item using any method you wish. What are the differences between qualitative and quantitative types of forecasting methods?arrow_forward11 Olympic Enterprises plans to assemble a new breed of mountain bikes as per the bill of materials (BOM) in Figure 11.33. a. Which component has more than one parent? b. How many unique components does product A have at all levels? c. How many intermediate items does product A have at all levels? d. Given the lead times (LT) in weeks noted on Figure 11.33, how far can the business delay the purchase of component C if the outcome is beneficial for the business? B (1) LT=1 A LT=2 C (2) LT = 4 D (1) LT=2 E (1) F (2) E (1) G (3) 1 (1) J (3) LT = 2 LT=3 LT = 3 LT = 2 LT=1 LT = 1 H (2) LT = 3 ▲ FIGURE 11.33 BOM for Product Aarrow_forward
- Practical Management ScienceOperations ManagementISBN:9781337406659Author:WINSTON, Wayne L.Publisher:Cengage,Operations ManagementOperations ManagementISBN:9781259667473Author:William J StevensonPublisher:McGraw-Hill EducationOperations and Supply Chain Management (Mcgraw-hi...Operations ManagementISBN:9781259666100Author:F. Robert Jacobs, Richard B ChasePublisher:McGraw-Hill Education
- Purchasing and Supply Chain ManagementOperations ManagementISBN:9781285869681Author:Robert M. Monczka, Robert B. Handfield, Larry C. Giunipero, James L. PattersonPublisher:Cengage LearningProduction and Operations Analysis, Seventh Editi...Operations ManagementISBN:9781478623069Author:Steven Nahmias, Tava Lennon OlsenPublisher:Waveland Press, Inc.
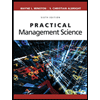
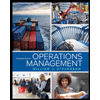
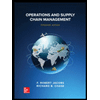
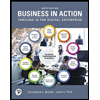
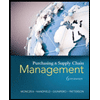
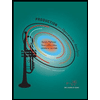