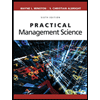
Concept explainers
A company manufactures clay bricks in batches. A batch consists of 200 bricks. The manager reports that his weekly production target is 1500 bricks. Each brick has to be processed through 5 machines on average. It takes on average 30 minutes to set up the machines and the average operation time is 6 minutes. There are 10 machines in the plant.
Calculate the manufacturing lead time if the average non-operation time is 2 hrs.
Calculate the production rate and If the plant operates 70 hours per week, calculate the production capacity Calculate the Production Capacity if the machines are only available for 85% of the time.
Will the manager be able to meet his production target? Justify your answer.

Trending nowThis is a popular solution!
Step by stepSolved in 3 steps

- Clients are served in a process with two resources. The processing time of the first resource is 6 minutes. The processing time of the second resource is 6 minutes. The first resource has 9 worker and the second resource has 5 workers. The cycle time of the process is 11.8 minutes. Instruction: Round your answer to one decimal place. What is the average labor utilization (%)? percent ation CRook Airarrow_forwardCustomers are served in a process with two resources. The first resource has a capacity of 45 customers per hour. The capacity of the second resource is 32 customers per hour. The first resource has 9 workers and the second resource has 3 workers. Demand for this process is 29 customers per hour. What is the average labor utilization? ______percentarrow_forwardRandy, James, Michael, Sophie, and Emily are employees of an organization. Their boss has requested them to gift-wrap toys for some children in their local community. Calculate Emily's efficiency, if an average employee takes an average of 10 minutes to complete a gift-wrap. The average production by each employee in an 8-hour workday is as follows Randy- 66 packages James- 48 packages Michael- 59 packages Sophie- 52 packages Emily- 48 packages A. 0.90 (90%). B. 1.50 (150%). C. 9.0 packages per hour. D. 1.50 packages per hour. E. 9.0 minutes per package. F. 1.00 (100%)arrow_forward
- A bicycle component manufacturer produces hubs for bike wheels. Two processes are possible for manufacturing, and the parameters of each process are as follows: Process 1 Production rate Daily production time Process 2 35 parts/hour 4 hours/day 20% 15 parts/hour 7 hours/day 9% Percent parts rejected Assume that the daily demand for hubs allows all defect-free hubs to be sold. Select the process that maximizes profit per day if each part is made from $4 worth of material and can be sold for $30. Both processes are fully automated, and variable overhead cost is charged at the rate of $40 per hour.arrow_forwardA startup company is considering making a part by injection molding. The part is moderately complex and the volume of the part is about 10 cubic centimeters. Assume that the part is designed for injection molding and can be made with a two part mold. The company needs to make 250,000 parts made from ABS plastic. Once the mold is made it will take a worker 1 minute to make one part using the injection molding machine. The company will use contract manufacturing to produce the parts. Estimate the cost per part and explain how you came up with the number. (If you are stuck look at the Contract Manufacturing Cost per Unit section. Also keep in mind that there is no exact right answer, the goal is to come up with a reasonable estimate.) Contract Manufacturing Cost per Unit: It’s not uncommon to hire another company to perform some or all the manufacturing for a product. To estimate the cost use ((Cost of Parts and Materials) + (man hours) × $40)/.75arrow_forwardFor the production of part R-193, two operations are being considered. The capital investment associated with each operation is identical. Operation 1 produces 2,100 parts per hour. After each hour, the tooling must be adjusted by the machine operator. This adjustment takes 15 minutes. The machine operator for Operation 1 is paid $24 per hour (this includes fringe benefits). Operation 2 produces 2,350 parts per hour, but the tooling needs to be adjusted by the operator only once every two hours. This adjustment takes 45 minutes. The machine operator for Operation 2 is paid $13 per hour (this includes fringe benefits). Assume an 8-hour workday. Further assume that all parts produced can be sold for $0.35 each. a. Should Operation 1 or Operation 2 be recommended? b. What is the basic tradeoff in this problem?arrow_forward
- Hammond Inc. has analyzed the setup time on its computer-controlled lathe. The setup requires changing the type of fixture that holds a part. The average setup time has been 135 minutes, consisting of the following steps: Step Time (in minutes) Turn off machine and remove fixture from lathe 13 Go to tool room with fixture 15 Record replacement of fixture to tool room 18 Return to lathe 20 Clean lathe 17 Return to tool room 20 Record withdrawal of new fixture from tool room 12 Return to lathe 15 Install new fixture and turn on machine 8 Total setup time 138 Why should management be concerned about improving setup time? What do you recommend to Hammond Inc. for improving setup time? How much time would be required for a setup, using your suggestion in (b)?arrow_forwardAn average of 1200 parts arrive to the EP chamber during an 8-hour workday. Each part goes through two stages of processing. At each stage, a single product is processed at a time, and processing takes an average of 15 seconds at the first station and 12 seconds at the second station. Inter-arrival times and service times are exponentially distributed. At the end of the second step, the product goes through a quality check. 5% of the parts fail the quality check and are sent back to the second stage of service. Parts exit the system only after they pass the quality check. Ignoring the time required to perform the quality check or in moving the part through the facility, what is the average cycle time for parts?arrow_forwardA cell-phone repair shop consists of three processes. Step 1 requires 4 minutes per unit, step 2 requires 6 minutes per unit and step 3 requires 2 minutes per unit. 40% of units that complete the third step require rework, which means those units must start the process over at step 2 (processing times are the same for units being reworked) and rework is always successful. Demand at the shop is 0.8 units per minute. Instruction: Round your answer to three decimal places. What is the capacity of the shop (in units per units per minute)? units per minutearrow_forward
- Processes A, B, C, and D are all used to produce seafood gumbo with seemingly infinite demand. The steps feed directly into one another, so A’s output goes to B, and B’s output goes to C, and finally, C’s output goes to D. Process A can produce 400 units per minute, Process B can produce 300 units per minute, Process C can produce 300 units per minute, and Process D can produce 400 units per minute. Which process step(s) can experience idle time while the overall process still maximizes output? a. Processes B and C b. Processes A and D c. Process A d. Process Darrow_forwardA process of making chair is described as follows: Stage 1 Seat and back attached Stage 2 Legs attached The production speeds are 15 chairs per hour for Stage 1 and 30 chairs per hour for stage 2. The cycle time of the process is ______minutes. The flow time of the process is ______ minutes.arrow_forwardA machine makes two components; call them types A and B. It takes 630 seconds to switch production between the component types. During that time, no production occurs. When in production, each unit of A or B requires 0.5 second to be completed. The two components, A and B, are combined in an assembly process to make a final product; call it C. The assembly step can combine the two components into 1 unit every 4 seconds, or 15 units per minute. Suppose the machine rotates between one batch of 2,520 units of A and 2,520 units of B. In that case, what is the capacity of the machine in component pairs per minute, where a component pair is one unit of A and one unit of B? Suppose the machine rotates between one batch of 2,520 units of A and 2,520 units of B. What is the utilization of the machine? Suppose the machine rotates between one batch of 2,520 units of A and 2,520 units of B. What is the average inventory of B components? If the production schedule could be adjusted with…arrow_forward
- Practical Management ScienceOperations ManagementISBN:9781337406659Author:WINSTON, Wayne L.Publisher:Cengage,Operations ManagementOperations ManagementISBN:9781259667473Author:William J StevensonPublisher:McGraw-Hill EducationOperations and Supply Chain Management (Mcgraw-hi...Operations ManagementISBN:9781259666100Author:F. Robert Jacobs, Richard B ChasePublisher:McGraw-Hill Education
- Purchasing and Supply Chain ManagementOperations ManagementISBN:9781285869681Author:Robert M. Monczka, Robert B. Handfield, Larry C. Giunipero, James L. PattersonPublisher:Cengage LearningProduction and Operations Analysis, Seventh Editi...Operations ManagementISBN:9781478623069Author:Steven Nahmias, Tava Lennon OlsenPublisher:Waveland Press, Inc.
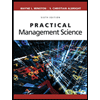
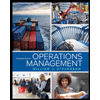
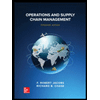
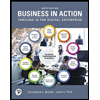
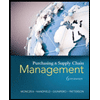
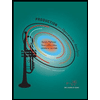