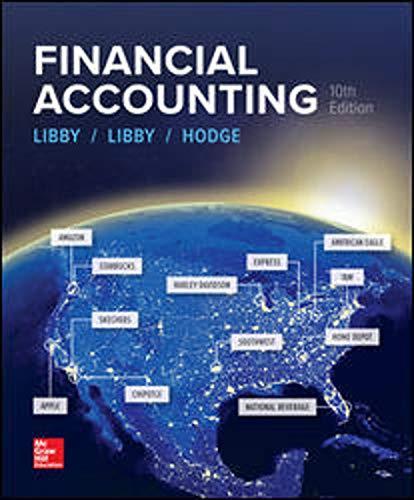
FINANCIAL ACCOUNTING
10th Edition
ISBN: 9781259964947
Author: Libby
Publisher: MCG
expand_more
expand_more
format_list_bulleted
Question
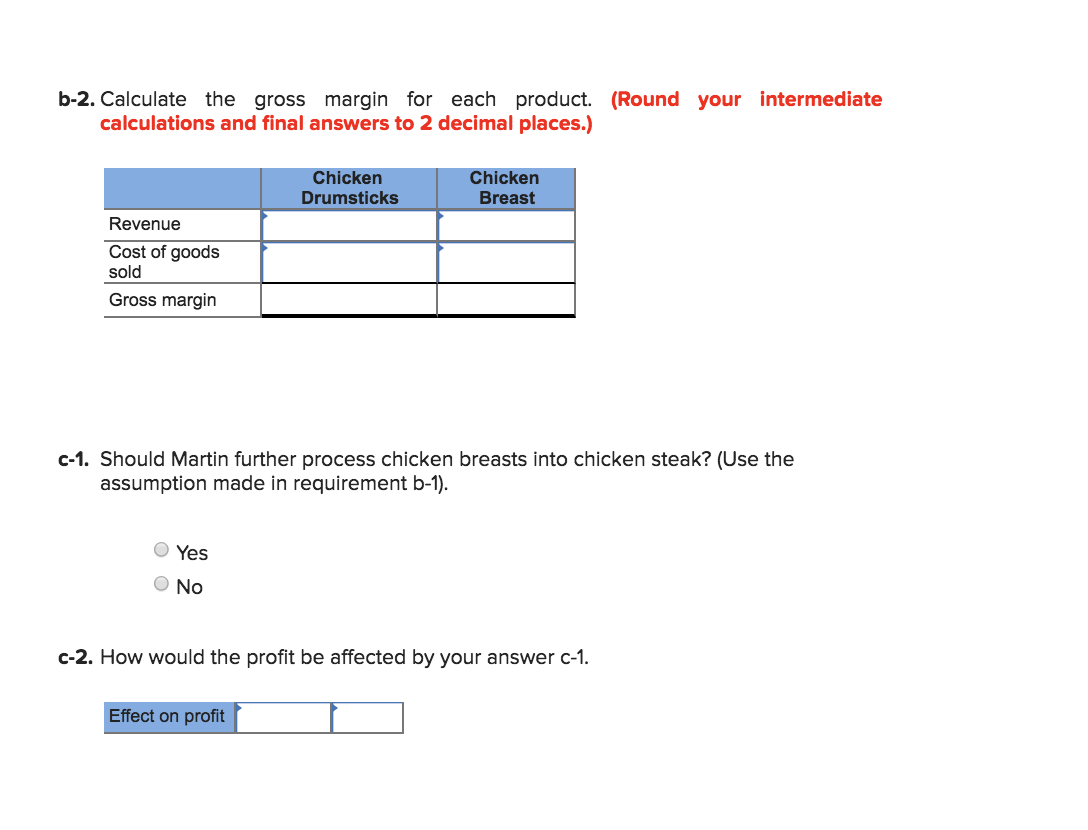
Transcribed Image Text:b-2. Calculate the gross margin for each product. (Round your intermediate
calculations and final answers to 2 decimal places.)
Chicken
Chicken
Drumsticks
Breast
Revenue
Cost of goods
sold
Gross margin
c-1. Should Martin further process chicken breasts into chicken steak? (Use the
assumption made in requirement b-1)
Yes
ONo
c-2. How would the profit be affected by your answer c-1
Effect on profit
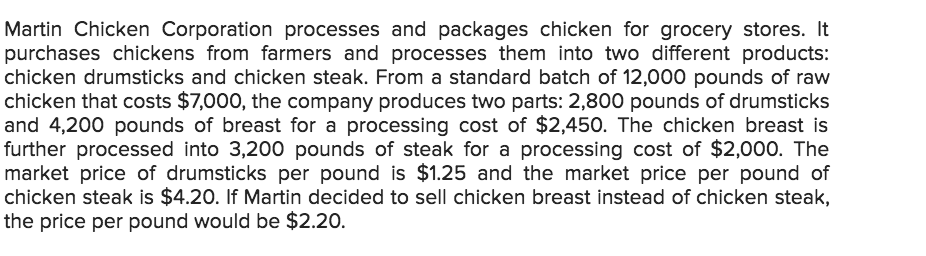
Transcribed Image Text:Martin Chicken Corporation processes and packages chicken for grocery stores. It
purchases chickens from farmers and processes them into two different products:
chicken drumsticks and chicken steak. From a standard batch of 12,000 pounds of raw
chicken that costs $7,000, the company produces two parts: 2,800 pounds of drumsticks
and 4,200 pounds of breast for a processing cost of $2,450. The chicken breast is
further processed into 3,200 pounds of steak for a processing cost of $2,00o. The
market price of drumsticks per pound is $1.25 and the market price per pound of
chicken steak is $4.20. If Martin decided to sell chicken breast instead of chicken steak,
the price per pound would be $2.20.
Expert Solution

This question has been solved!
Explore an expertly crafted, step-by-step solution for a thorough understanding of key concepts.
This is a popular solution
Trending nowThis is a popular solution!
Step by stepSolved in 3 steps with 3 images

Knowledge Booster
Similar questions
- Atlas Foods produces three supplemental food products simultaneously through a refining process costing $85,000. The joint products, Alfa and Betters, have a final selling price of $8 per pound and $5 per pound, respectively, after additional processing costs of $3 per pound of each product are incurred after the split-off point. Morefeed, a by-product, is sold at the split- off point for $2.50 per pound. Additional information are as follows: Alfa - 15,000 pounds of Alfa, a popular but relatively rare grain supplement of having a caloric value of 8,800 calories/pound. Betters - 5,000 pounds of Betters, a flavouring material high in carbohydrates with a caloric value of 12,000 calories/pound. Morefeed - 2,000 pounds of Morefeed, used as a cattle feed supplement with a caloric value of 1,000 calories/pound. Questions: 1. Assuming Atlas Foods does not inventory Morefeed, the by-product, the joint cost to be allocated to Betters using the net realizable method is?arrow_forwardIllion Soy Products (ASP) buys soybeans and processes them into other soy products. Each ton of soybeans that ASP purchases for $250 can be converted for an additional $180 into 700 lbs of soy meal and 80 gallons of soy oil. A pound of soy meal can be sold at splitoff for $1.08 and soy oil can be sold in bulk for $4 per gallon. ASP can process the 700 pounds of soy meal into 800 pounds of soy cookies at an additional cost of $370. Each pound of soy cookies can be sold for $2.08 per pound. The 80 gallons of soy oil can be packaged at a cost of $200 and made into 320 quarts of Soyola. Each quart of Soyola can be sold for $1.45. Read the requirements. Requirement 1. Allocate the joint cost to the cookies and the Soyola using the (a) Sales value at splitoff method and (b) NRV method. a. First, allocate the joint cost using the Sales value at splitoff method. (Round the weights to three decimal places and joint costs to the nearest dollar.) Sales value of total production at splitoff…arrow_forwardCarleigh, Inc., is a pork processor. Its plants, located in the Midwest, produce several products from a common process: sirloin roasts, chops, spare ribs, and the residual. The roasts, chops, and spare ribs are packaged, branded, and sold to supermarkets. The residual consists of organ meats and leftover pieces that are sold to sausage and hot dog processors. The joint costs for a typical week are as follows: Direct materials $87,000 Direct labor 36,600 Overhead 19,500 The revenues from each product are as follows: sirloin roasts, $72,000; chops, $67,000; spare ribs, $37,500; and residual, $8,200. Carleigh’s management has learned that certain organ meats are a prized delicacy in Asia. They are considering separating those from the residual and selling them abroad for $53,000. This would bring the value of the residual down to $3,350. In addition, the organ meats would need to be packaged and then air freighted to Asia. Further processing cost per week is estimated to be…arrow_forward
- 34) Boney Corporation processes sugar beets that it purchases from farmers. Sugar beets are processed in batches. A batch of sugar beets costs $60 to buy from farmers and $19 to crush in the company's plant. Two intermediate products, beet fiber and beet juice, emerge from the crushing process. The beet fiber can be sold as is for $30 or processed further for $29 to make the end product industrial fiber that is sold for $77. The beet juice can be sold as is for $51 or processed further for $33 to make the end product refined sugar that is sold for $77. What is the financial advantage (disadvantage) for the company from processing one batch of sugar beets into the end products industrial fiber and refined sugar rather than not processing that batch at all?arrow_forwardGibson Chicken Corporation processes and packages chicken for grocery stores. It purchases chickens from farmers and processes them into two different products: chicken drumsticks and chicken steak. From a standard batch of 15,000 pounds of raw chicken that costs $8,200, the company produces two parts: 2,000 pounds of drumsticks and 5,000 pounds of breast for a processing cost of $3,887. The chicken breast is further processed into 4,200 pounds of steak for a processing cost of $2,200. The market price of drumsticks per pound is $1.65 and the market price per pound of chicken steak is $4.20. If Gibson decided to sell chicken breast instead of chicken steak, the price per pound would be $2.40. Required a-1. Allocate the joint cost to the joint products, drumsticks and breasts, using weight as the allocation base. a-2. Calculate the gross profit for each product. a-3. If the drumsticks are producing a loss, should that product line be eliminated? b-1. Reallocate the joint cost to the…arrow_forwardYour Corporation processes sugar beets in batches. A batch of sugar beets costs $625 to buy from farmers and $275 to crush in the company's plant. Two intermediate products, beet fiber (750 units) and beet juice (250 units), emerge from the crushing process. The beet fiber can be sold as is for $20 or processed further for $18 to make the end product industrial fiber that is sold for $45. The beet juice can be sold as is for $42 or processed further for $24 to make the end product refined sugar that is sold for $62. How much more profit (loss) does the company make by processing one batch of sugar beets into the end products industrial fiber and refined sugar? Group of answer choices $3,975 $6,000 $4,250 ($4,250) $5,250arrow_forward
- Rundle Chicken Corporation processes and packages chicken for grocery stores. It purchases chickens from farmers and processes them into two different products: chicken drumsticks and chicken steak. From a standard batch of 16,000 pounds of raw chicken that costs $8,800, the company produces two parts: 4,000 pounds of drumsticks and 5,400 pounds of breast for a processing cost of $7,805. The chicken breast is further processed into 4,600 pounds of steak for a processing cost of $2,600. The market price of drumsticks per pound is $1.75 and the market price per pound of chicken steak is $4.60. If Rundle decided to sell chicken breast instead of chicken steak, the price per pound would be $2.50.arrow_forwardCowboy Ice Cream Company (CIC) produces ice cream bars that it markets through a variety of grocery stores. It makes the ice cream bars in batches of 2,000 units. CIC produced 36,000 ice cream bars during the prior accounting period. The cost of producing the ice cream bars is shown below. Materials cost ($29 per unit x 36,000) Labor cost ($26 per unit x 36,000) Manufacturing supplies ($9 x 36,000) Batch-level costs (18 batches at $6,000 per batch) Product-level costs $1,044,000 936,000 324,000 108,000 300,000 370,000 Facility-level costs Total costs $3,082,000 Cost per unit = $3,082,000 + 36, 000 = $85.61 Required a. OnCue has offered to buy a batch of 500 ice cream bars for $68 each. CIC's normal selling price is $93 per unit. Calculate the relevant cost per unit for the special order. Based on the preceding quantitative data, should CIC accept the special order? b. OnCue offered to buy a batch of 2,000 ice cream bars for $68 per unit, calculate the relevant cost per unit for the…arrow_forwardBenson Chicken Corporation processes and packages chicken for grocery stores. It purchases chickens from farmers and processes them into two different products: chicken drumsticks and chicken steak. From a standard batch of 14,000 pounds of raw chicken that costs $7,450, the company produces two parts: 2,500 pounds of drumsticks and 4,500 pounds of breast for a processing cost of $2,466. The chicken breast is further processed into 3,700 pounds of steak for a processing cost of $1,700. The market price of drumsticks per pound is $1.40 and the market price per pound of chicken steak is $3.70. If Benson decided to sell chicken breast instead of chicken steak, the price per pound would be $2.20. Required a-1. Allocate the joint cost to the joint products, drumsticks and breasts, using weight as the allocation base. a-2. Calculate the gross profit for each product. a-3. If the drumsticks are producing a loss, should that product line be eliminated? b-1. Reallocate the joint cost to the…arrow_forward
arrow_back_ios
arrow_forward_ios
Recommended textbooks for you
- AccountingAccountingISBN:9781337272094Author:WARREN, Carl S., Reeve, James M., Duchac, Jonathan E.Publisher:Cengage Learning,Accounting Information SystemsAccountingISBN:9781337619202Author:Hall, James A.Publisher:Cengage Learning,
- Horngren's Cost Accounting: A Managerial Emphasis...AccountingISBN:9780134475585Author:Srikant M. Datar, Madhav V. RajanPublisher:PEARSONIntermediate AccountingAccountingISBN:9781259722660Author:J. David Spiceland, Mark W. Nelson, Wayne M ThomasPublisher:McGraw-Hill EducationFinancial and Managerial AccountingAccountingISBN:9781259726705Author:John J Wild, Ken W. Shaw, Barbara Chiappetta Fundamental Accounting PrinciplesPublisher:McGraw-Hill Education
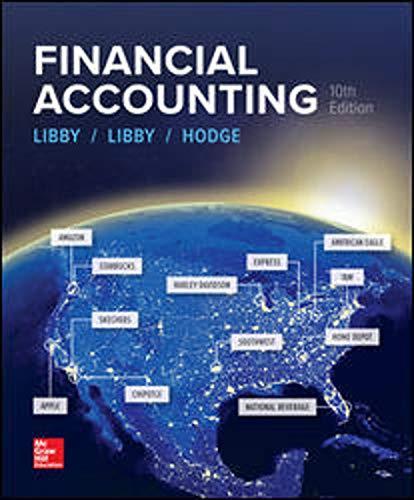
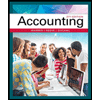
Accounting
Accounting
ISBN:9781337272094
Author:WARREN, Carl S., Reeve, James M., Duchac, Jonathan E.
Publisher:Cengage Learning,
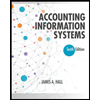
Accounting Information Systems
Accounting
ISBN:9781337619202
Author:Hall, James A.
Publisher:Cengage Learning,
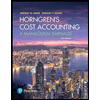
Horngren's Cost Accounting: A Managerial Emphasis...
Accounting
ISBN:9780134475585
Author:Srikant M. Datar, Madhav V. Rajan
Publisher:PEARSON
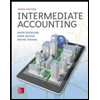
Intermediate Accounting
Accounting
ISBN:9781259722660
Author:J. David Spiceland, Mark W. Nelson, Wayne M Thomas
Publisher:McGraw-Hill Education
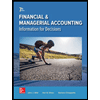
Financial and Managerial Accounting
Accounting
ISBN:9781259726705
Author:John J Wild, Ken W. Shaw, Barbara Chiappetta Fundamental Accounting Principles
Publisher:McGraw-Hill Education