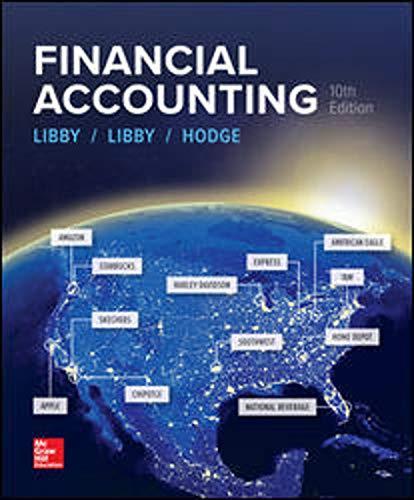
FINANCIAL ACCOUNTING
10th Edition
ISBN: 9781259964947
Author: Libby
Publisher: MCG
expand_more
expand_more
format_list_bulleted
Concept explainers
Topic Video
Question
Kingsport Containers Company makes a single product that is subject to wide seasonal variations in demand. The company uses a job-order costing system and computes plantwide predetermined overhead rates on a quarterly basis using the number of units to be produced as the allocation base. Its estimated costs, by quarter, for the coming year are given below: Quarter First Second Third Fourth Direct materials $ 280,000 $ 140,000 $ 70,000 $ 210,000 Direct labor 80,000 40,000 20,000 60,000 Manufacturing overhead 220,000 196,000 184,000 ? Total manufacturing costs (a) $ 580,000 $ 376,000 $ 274,000 $ ? Number of units to be produced (b) 160,000 80,000 40,000 120,000 Estimated unit product cost (a) ÷ (b) $ 3.63 $ 4.70 $ 6.85 $ ? Management finds the variation in quarterly unit product costs to be confusing. It has been suggested that the problem lies with manufacturing overhead because it is the largest element of total manufacturing cost. Accordingly, you have been asked to find a more appropriate way of assigning manufacturing overhead cost to units of product. Required: 1. Assuming the estimated variable manufacturing overhead cost per unit is $0.30, what must be the estimated total fixed manufacturing overhead cost per quarter? 2. Assuming the assumptions about cost behavior from the first three quarters hold constant, what is the estimated unit product cost for the fourth quarter? 3. What is causing the estimated unit product cost to fluctuate from one quarter to the next? 4. Assuming the company computes one predetermined overhead rate for the year rather than computing quarterly overhead rates, calculate the unit product cost for all units produced during the year.
Expert Solution

This question has been solved!
Explore an expertly crafted, step-by-step solution for a thorough understanding of key concepts.
This is a popular solution
Trending nowThis is a popular solution!
Step by stepSolved in 2 steps with 3 images

Knowledge Booster
Learn more about
Need a deep-dive on the concept behind this application? Look no further. Learn more about this topic, accounting and related others by exploring similar questions and additional content below.Similar questions
- Orange, Inc. has identified the following cost drivers for its expected overhead costs for the year: Overhead Item Expected Cost Cost Driver Expected Quantity Setup costs $ 59,500 Number of setups 250 Ordering costs 49,000 Number of orders 1,500 Maintenance 138,000 Machine hours 2,000 Power 29,500 Kilowatt hours 4,000 Total Overhead $ 276,000 Total direct labor hours budgeted = 2,000 hours. The following actual data applies to one of the products completed during the year: Product X Direct materials $ 6,900 Number of setups 5 Direct labor $ 4,900 Number of orders 50 Units completed 100 Machine hours 50 Direct labor hours 100 Kilowatt hours 500 If Orange, Inc. uses machine hours to allocate overhead cost, the unit product cost of Product X will be: Multiple Choice $117.00. $137.00 $147.00 $167.00. $187.00.arrow_forwardMohammed Company employs a standard cost system. Mohammed has established the following standards for one unit of product: Standard Quantity Standard Price Standard Cost Direct materials 12.0 pounds $ 7.00/pound $ 84.00 Direct labor 2.0 hours $15.00/hour 75.00 During June, Mohammed planned to produce 21,000 units of product. It purchased 330,000 pounds of direct material at a total cost of $2,343,000. The total factory wages for June were $1,440,000. Mohammed manufactured 20,000 units of product during June using 302,000 pounds of direct material and 41,000 direct labor hours. How much is the labor efficiency variance? $15,000 unfavorable $75,000 unfavorable $75,000 favorable $15,000 favorable $35,000 favorablearrow_forwardHuron Company produces a commercial cleaning compound known as Zoom. The direct materials and direct labor standards for one unit of Zoom are given below: Standard Quantity or Standard Price or Standard Hours Rate Cost Direct materials Direct labor 6.90 pounds 0.50 houra $ 2.50 per pound $ 13.50 per hour $ 17.25 $ 6.75 During the most recent month, the following activity was recorded: a. Thirteen thousand four hundred pounds of material were purchased at a cost of $2.40 per pound. b. The company produced only 1,340 units, using 12,060 pounds of material. (The rest of the material purchased remained in raw materials inventory.) c. 770 hours of direct labor time were recorded at a total labor cost of $9,240. Required: Compute the materials price and quantity variances for the month. (Indicate the effect of each variance by selecting "F" for favorable, "U" for unfavorable, and "None" for no effect (i.e., zero variance). Input all amounts as positive values.) Materials price variance…arrow_forward
- Dengerarrow_forwardKingsport Containers Company makes a single product that is subject to wide seasonal variations in demand. The company uses a job-order costing system and computes plantwide predetermined overhead rates on a quarterly basis using the number of units to be produced as the allocation base. Its estimated costs, by quarter, for the coming year are given below:QuarterFirst Second Third FourthDirect materials $ 320,000 $ 160,000 $ 80,000 $ 240,000Direct labor 160,000 80,000 40,000 120,000Manufacturing overhead 230,000 206,000 194,000 ?Total manufacturing costs (a) $ 710,000 $ 446,000 $ 314,000 $ ?Number of units to be produced (b) 160,000 80,000 40,000 120,000Estimated unit product cost (a) ÷ (b) $ 4.44 $ 5.58 $ 7.85 $ ?Management finds the variation in quarterly unit product costs to be confusing and difficult to work with. It has been suggested that the problem lies with manufacturing overhead because it is the largest…arrow_forwardKingsport Containers Company makes a single product that is subject to wide seasonal variations in demand. The company uses a job-order costing system and computes plantwide predetermined overhead rates on a quarterly basis using the number of units to be produced as the allocation base. Its estimated costs, by quarter, for the coming year are given below: Quarter First Second Third Fourth Direct materials $ 320,000 $ 160,000 $ 80,000 $ 240,000 Direct labor 80,000 40,000 20,000 60,000 Manufacturing overhead 230,000 206,000 194,000 ? Total manufacturing costs (a) $ 630,000 $ 406,000 $ 294,000 $ ? Number of units to be produced (b) 80,000 40,000 20,000 60,000 Estimated unit product cost (a) ÷ (b) $ 7.88 $ 10.15 $ 14.70 $ ? Management finds the variation in quarterly unit product costs to be confusing and difficult to work with. It has been suggested that the problem lies with…arrow_forward
- Silven Company has identified the following overhead activities, costs, and activity drivers for the coming year: Activity Expected Cost Activity Driver Activity Capacity $138,000 Number of setups 10,200 Number of orders 92,400 Machine hours 18,480 Receiving hours phones with the following expected activity demands: Setting up equipment Ordering materials Machining Receiving Silven produces two models of cell Model X 5,000 80 200 6,600 385 Units completed Number of setups Number of orders Machine hours Receiving hours Required: Model Y 10,000 40 400 4,950 770 120 600 11,550 1,155arrow_forwardRed Industries produces computers and goes through two operations, Assembling and Packaging before it is ready to be sold to customers. Next year's expected costs and activities are shown below. Data for Dept. Overhead costs Assembling Direct labor 401,000 DLH 99,000 hours Machine hours Packaging $ 586,600 72,000 MH 80,000 MH DLH $ 413,400 1. Compute Red's departmental overhead rate for the Assembling department based on direct labor hours. 2. Compute Red's departmental overhead rate for the Packaging department based on machine hours. 3, Compute a single plantwide rate based on machine hours. Show your work with an Excel spreadsheet or in a Word file.arrow_forwardTrying to find the activity based costing of the following for the allocated overheadarrow_forward
- Obi Wan Pierogi, Inc. has prepared the following estimates for the coming year:Estimated Direct Labor Hours: 80, 000 hoursEstimated Direct Labor Costs: $1,000,000Estimated Machine Hours: 60,000 hoursEstimated Manufacturing Overhead Costs: $600, 000Overhead is applied using machine hours. If Job #123 uses 9, 500 machine hours, how much total overhead will be applied to it ?$60,000 $10.00 $600,000 $95,000arrow_forwardSalisbury Bottle Company manufactures plastic two-liter bottles for the beverage industry. The cost standards per 100 two-liter bottles are as follows: Standard Cost Cost Category per 100 Two-Liter Bottles Direct labor $1.20 Direct materials 6.50 Factory overhead 1.80 Total $9.50 At the beginning of March, Salisbury's management planned to produce 500,000 bottles. The actual number of bottles produced for March was 525,000 bottles. The actual costs for March of the current year were as follows: Actual Cost for the Cost Category Month Ended March 31 Direct labor $6,550 Direct materials 33,800 Factory overhead 9,100 Total $49,450 a. Prepare the March manufacturing standard cost budget (direct labor, direct materials, and factory overhead) for Salisbury, assuming planned production. Salisbury Bottle Company Manufacturing Cost Budget For the Month Ended March 31 Standard Cost at Planned Volume (500,000 Bottles) Check My Work Multiply the standard cost per unit times the units planned…arrow_forwardDeoro Company has identified the following overhead activities, costs, and activity drivers for the coming year: Activity Expected Cost Activity Driver Activity Capacity Setting up equipment Number of setups Ordering costs Number of orders Machine costs Receiving Direct materials Direct labor Deoro produces two models of dishwashers with the following expected prime costs and activity demands: Model A Units completed Direct labor hours Number of setups Number of orders $627,000 481,000 16,200 6,400 370 5,800 24,900 3,700 The company's normal activity is 7,900 direct labor hours. Machine hours Receiving hours Required: Model A Model B $482,510 372,000 864,000 410,000 Receiving hours Model A Machine hours $ del B Model B Unit Cost $836,000 497,000 8,500 1,500 240 1. Determine the unit cost for each model using direct labor hours to apply overhead. Round intermediate calculations and final answers to nearest cent. 12,800 18,300 6,300 610 18,600 43,200 10,000 2. Determine the unit cost for…arrow_forward
arrow_back_ios
SEE MORE QUESTIONS
arrow_forward_ios
Recommended textbooks for you
- AccountingAccountingISBN:9781337272094Author:WARREN, Carl S., Reeve, James M., Duchac, Jonathan E.Publisher:Cengage Learning,Accounting Information SystemsAccountingISBN:9781337619202Author:Hall, James A.Publisher:Cengage Learning,
- Horngren's Cost Accounting: A Managerial Emphasis...AccountingISBN:9780134475585Author:Srikant M. Datar, Madhav V. RajanPublisher:PEARSONIntermediate AccountingAccountingISBN:9781259722660Author:J. David Spiceland, Mark W. Nelson, Wayne M ThomasPublisher:McGraw-Hill EducationFinancial and Managerial AccountingAccountingISBN:9781259726705Author:John J Wild, Ken W. Shaw, Barbara Chiappetta Fundamental Accounting PrinciplesPublisher:McGraw-Hill Education
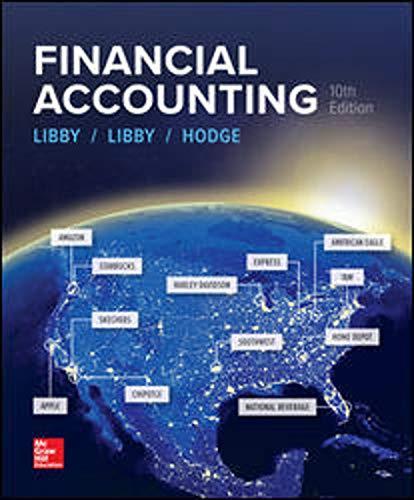
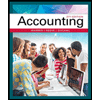
Accounting
Accounting
ISBN:9781337272094
Author:WARREN, Carl S., Reeve, James M., Duchac, Jonathan E.
Publisher:Cengage Learning,
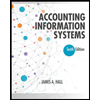
Accounting Information Systems
Accounting
ISBN:9781337619202
Author:Hall, James A.
Publisher:Cengage Learning,
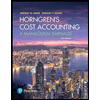
Horngren's Cost Accounting: A Managerial Emphasis...
Accounting
ISBN:9780134475585
Author:Srikant M. Datar, Madhav V. Rajan
Publisher:PEARSON
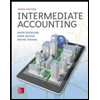
Intermediate Accounting
Accounting
ISBN:9781259722660
Author:J. David Spiceland, Mark W. Nelson, Wayne M Thomas
Publisher:McGraw-Hill Education
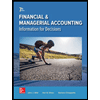
Financial and Managerial Accounting
Accounting
ISBN:9781259726705
Author:John J Wild, Ken W. Shaw, Barbara Chiappetta Fundamental Accounting Principles
Publisher:McGraw-Hill Education