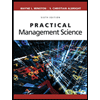
Practical Management Science
6th Edition
ISBN: 9781337406659
Author: WINSTON, Wayne L.
Publisher: Cengage,
expand_more
expand_more
format_list_bulleted
Question
thumb_up100%
A tire store orders its stock for a popular winter tire once every year. The cost of a tire for the store is $120. The store sells a tire for $140 at the regular price. The regular demand per year is 1,000 tires, which is
How many tires the store should order each year?
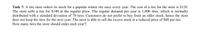
Transcribed Image Text:Task 7: A tire store orders its stock for a popular winter tire once every year. The cost of a tire for the store is $120.
The store sells a tire for $140 at the regular price. The regular demand per year is 1,000 tires, which is normally
distributed with a standard deviation of 70 tires. Customers do not prefer to buy from an older stock; hence the store
does not keep the tires for the next year. The store is able to sell the excess stock at a reduced price of $80 per tire.
How many tires the store should order each year?
Expert Solution

This question has been solved!
Explore an expertly crafted, step-by-step solution for a thorough understanding of key concepts.
This is a popular solution
Trending nowThis is a popular solution!
Step by stepSolved in 2 steps with 2 images

Knowledge Booster
Similar questions
- AAA auto supply store sells snow tires which are ordered every Friday to meet next week's demand. The sales price for the most popular size is $50 per tire and its cost for AAA is $35. If too many tires are ordered AAA incurs an inventory carrying cost of $2 per tire. If AAA is out of stock, it forgoes the profits from missed sales. AAA has the option to order 100, 150, or 200 tires to meet next week's demand which can be either 100, 150, or 200 tires.Based on its historical demand distribution, assume that AAA Inc. has determined the followingprobability information: P(100) = 0.4, P(150) = 0.3, and P(200) = 0.3 e. Which alternative should be chosen based on the minimax regret criterion? f. Which alternative should be chosen using the expected monetary value (EMV) criterion? g. What is the expected value under perfect information (EVPI)? Show Workarrow_forwardA food processor purchases corn for use in its products. The firm uses 700 pounds of corn per week and purchases corn for $0.45 per pound from a supplier. The cost to hold one pound of corn in inventory for one year is $0.09. Each time the firm orders corn from the supplier, the firm must pay a $48 order processing charge. Assume there are 52 weeks in a year and round your answer to the nearest integer value. What is the optimal order quantity (in pounds)? poundsarrow_forwardCurrently, a company places orders for diaries to give away as tokens for its customers. Each diary costs the company $137.50. It costs the company $0.65 to place an order for the diaries and $0.87 to carry each diary annually in its inventory. The suppliers wish to offer the company a deal on the cups, by having it pay $85 for each diary, but ONLY if the company orders in sizes of 500 instead of the usual amount. Annual demand for the cups is 8000. Should the company accept the deal?arrow_forward
- Algro Inc. keeps a wide range of parts and materials on hand for use in its production processes. Management has recently had difficulty managing parts inventory as demand for its finished goods has increased; they frequently run out of some critical parts while having an endless supply of others. They would like to classify their parts inventory according to the ABC approach to better control inventory. The following is a list of parts, along with their annual usage and unit value: Item Annual Unit Item Annual Unit Number Usage Cost Number Usage Cost 1 36 $350 2 510 30 3 50 23 4 300 45 5 18 1900 6 500 8 7 710 4 8 80 26 9 344 28 10 67 440 11 510 2 12 682 35 13 1216 95 50 14 10 3 15 820 1 KARAN2222222222 16 60 $610 17 120 20 18 270 15 19 45 50 20 19 3200 21 910 3 12 4750 23 30 2710 24 24 1800 25 870 105 26 244 30 27 750 15 28 45 110 29 46 160 30 165 25 a. Classify the inventory items according to the ABC approach using the dollar value of annual demand. b. Clearly explain why you…arrow_forwardAndy's Auto Dealership (AAD) is a family-run auto dealership selling both new and used vehicles. In an average month, AAD sells a total of 160 vehicles. New vehicles represent 60 percent of sales, and used vehicles represent 40 percent of sales. Max has recently taken over the business from his father. His father always emphasized the importance of carefully managing the dealership's inventory. Inventory financing was a significant expense for AAD. Max's father consequently taught him to keep inventory turns as high as possible. Examining the dealership's performance over recent years, Max discovered that AAD had been turning its inventory (including both new and used vehicles) at a rate of 8 times per year. What is AAD's average inventory (including both new and used vehicles)? Drilling down into the numbers, Max has determined that the dealerships new and used businesses appear to behave differently. He has determined that turns of new vehicles are 7.2 per year, while turns of used…arrow_forwardA Mercedes dealer purchases vehicles for $20,000. The annual holding cost is estimated to be 25% of the dollar value of inventory. The dealer sells an average of 500 cars per year. He believes that demand is backlogged, but estimates that if he is short one car for one year, he will lose $20,000 in future profits. Each time the dealer places an order for cars, the ordering cost amounts to $10,000. Determine the Mercedes dealer's optimal (?,?) ordering policy.arrow_forward
- True or False: Single-Period inventory model makes the assumption that the demand follows a standard normal distribution.arrow_forwardA manufacturing plant procures 100,000 filters per year. Each unit has a fixed order cost is $50. To maintain the inventory in optimal conditions, there is a carrying cost rate of 10% per year. The vendor of filters has offered the following price breaks: for orders of more than 5,000 filters, cost is $4.50/unit; for orders between 1,000 and 5,000 filters, cost is $4.75/unit; orders less than 1,000 filters have a cost of $5.00/unit. Find the economic order quantity. Calculate the average annual cost for the optimal solution.arrow_forwardMilk is stocked at the grocery store each week. At the end of the week unsold milk is reduced in price by 50% of its selling price, and always sells for this lower price instantly. Weekly demand for milk is normally distributed with a mean of 200 gallons and standard deviation of 25 gallons. Each gallon of milk costs $1.75. Assuming a service level of 90% and that the store sells the milk for $3 per gallon, how many gallons should the store order this week?arrow_forward
- Cynthia Knott's oyster bar buys fresh Louisiana oysters for $5 per pound and sells them for $9 per pound. Any oysters not sold that day are sold to her cousin, who has a nearby grocery store, for $3 per pound. Cynthia believes that demand follows the normal distribution, with a mean of 100 pounds and a standard deviation of 14 pounds. How many pounds should she order each day? Refer to the standard normal table LOADING... for z-values. Part 2 Cynthia should order enter your response here pounds of oysters each day (round your response to one decimal place).arrow_forwardA firm experiences demand with a mean of 100 units per day. Lead time demand is normally distributed with mean 1000 units and standard deviation 200 units. It costs $6 to hold one unit for one year. If the firm wants to meet 90% of all demand on time, what is the expected annual cost of holding safety stock? Assume that each order costs $50.arrow_forward
arrow_back_ios
arrow_forward_ios
Recommended textbooks for you
- Practical Management ScienceOperations ManagementISBN:9781337406659Author:WINSTON, Wayne L.Publisher:Cengage,Operations ManagementOperations ManagementISBN:9781259667473Author:William J StevensonPublisher:McGraw-Hill EducationOperations and Supply Chain Management (Mcgraw-hi...Operations ManagementISBN:9781259666100Author:F. Robert Jacobs, Richard B ChasePublisher:McGraw-Hill Education
- Purchasing and Supply Chain ManagementOperations ManagementISBN:9781285869681Author:Robert M. Monczka, Robert B. Handfield, Larry C. Giunipero, James L. PattersonPublisher:Cengage LearningProduction and Operations Analysis, Seventh Editi...Operations ManagementISBN:9781478623069Author:Steven Nahmias, Tava Lennon OlsenPublisher:Waveland Press, Inc.
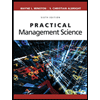
Practical Management Science
Operations Management
ISBN:9781337406659
Author:WINSTON, Wayne L.
Publisher:Cengage,
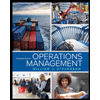
Operations Management
Operations Management
ISBN:9781259667473
Author:William J Stevenson
Publisher:McGraw-Hill Education
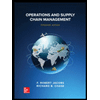
Operations and Supply Chain Management (Mcgraw-hi...
Operations Management
ISBN:9781259666100
Author:F. Robert Jacobs, Richard B Chase
Publisher:McGraw-Hill Education
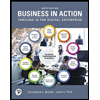
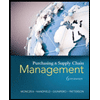
Purchasing and Supply Chain Management
Operations Management
ISBN:9781285869681
Author:Robert M. Monczka, Robert B. Handfield, Larry C. Giunipero, James L. Patterson
Publisher:Cengage Learning
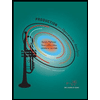
Production and Operations Analysis, Seventh Editi...
Operations Management
ISBN:9781478623069
Author:Steven Nahmias, Tava Lennon Olsen
Publisher:Waveland Press, Inc.