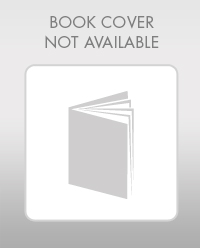
Concept explainers
A compound shaft drives three gears, as shown. Segments (1) and (2) of the compound shaft are hollow bronze [G = 6,500 ksi] tubes, which have an outside diameter of 1.55 in. and a wall thickness of 0.1975 in. Segments (3) and (4) are solid 1.10-in.-diameter steel [G = 11,500 ksi] shafts. The shaft lengths are L1 = 78 in., L2 = 8 in., L3 = 25 in., and L4 = 25 in. The torques applied to the shafts have magnitudes of TB = 940 lb·ft, TD = 500 lb·ft, and TE = 100 lb·ft, acting in the directions shown. The bearings shown allow the shaft to turn freely. Using the sign convention presented in Section 6.6., calculate:
(a) the magnitude of the maximum shear stress in the compound shaft.
(b) the rotation angle of flange C with respect to flange A.
(c) the rotation angle of gear E with respect to flange A.
![A compound shaft drives three gears, as shown. Segments (1) and (2) of the compound shaft are hollow bronze
[G = 6,500 ksi] tubes, which have an outside diameter of 1.55 in. and a wall thickness of 0.1975 in. Segments (3)
and (4) are solid 1.10-in-diameter steel [G= 11,500 ksi] shafts. The shaft lengths are L₁ = 78 in., L₂ = 8 in., L3=
25 in., and L4 = 25 in. The torques applied to the shafts have magnitudes of TB = 940 lb·ft, Tp = 500 lb-ft, and TE
= 100 lb-ft, acting in the directions shown. The bearings shown allow the shaft to turn freely. Using the sign
convention presented in Section 6.6., calculate:
(a) the magnitude of the maximum shear stress in the compound shaft.
(b) the rotation angle of flange C with respect to flange A.
(c) the rotation angle of gear E with respect to flange A.
TB
TD
(1)
TE
(3)
Answer:
(a) Tmax=
(b) OC/A=
(c) ΦΕΙΑ =
A
L₁
(2)
B
L2₂
psi
rad
rad
C
L3
D
(4)
L4
E
-X](https://content.bartleby.com/qna-images/question/749be18b-22f2-4fe5-9f05-6fa35acbb4d0/11237695-558b-4f3c-b062-6c5323336f77/qeee1zll_thumbnail.png)

Trending nowThis is a popular solution!
Step by stepSolved in 3 steps with 2 images

- .arrow_forwardProblem 4.81 The 60-mm-diameter cylinder is made from Am 1004- T61 magnesium and is placed in the clamp when the temperature is T₁ = 20° C. (Figure 1) Figure 1 of 1 -11 100 mm 150 mm Part A If the 304-stainless-steel carriage bolts of the clamp each have a diameter of 9 mm, and they hold the cylinder snug with negligible force against the rigid jaws, determine the force in the cylinder when the temperature rises to T2 = 130°C. Express your answer to three significant figures and include the appropriate units. F= Submit HA Value Units My Answers Give Up ? Provide Feedback Continuearrow_forward4 - Two circular shafts are connected via a gear assembly as shown in the figure. Shaft 1 is fixed to a wall at point A. Torque T is applied to shaft 2 at point D. Shaft 1 is made of steel with a shear modulus of 85 GPa; shaft 2 is made of aluminum with a shear modulus of 28 GPa. The other relevant paramters are indicated alongside the figure. The shafts are restrained by bearings such that they do not undergo bending (i.e., it is a case of pure torsion). Determine the angular rotation at point D relative to that at point A. Shafts L₁=1.5m; L₂=1m r=50mm; ₂= 25 mm gear radii R₁-200mm; R₂=40mm Torque T=4KN-m Li C L2 * assume the gears to be rigid Tarrow_forward
- Please read instructions carefully.arrow_forwardSolve all the parts ( Hand written please )arrow_forwardFor the assembly shown, as the screw is tightened down, the strain in the horizontal direction at B is 900×106 m/m. What is the load P on the screw. E= 200 Gla.= of le 20 60 20mm hans s 201 Bo 40 Section a-a 104mm a← 120mm IT. at 300 mm →arrow_forward
- Be quick pleasearrow_forwardThe following tubular A36 steel shaft has an inner diameter of 25mm and an outer diameter of 35mm under the following loading condition. Determine the angle of twist of the end V. Consider: GA-36 = 75 GPa 1) What would happen if a solid shaft was used? 2) As a designer, do you recommend a solid or tubular shaft for the loading above? Why?arrow_forwardThe gas storage tank is fabricated in the following manner: a 10-mm thick plate is rolled to form a cylindrical shell which is bolted on one side, then its ends are sealed by bolting two hemispherical shells. The resulting inner diameter of the tank is 4 m. All bolts have a diameter of 15 mm. If the internal pressure in the tank is 1 MPa, determine the following:a. the number of bolts needed in each hemispherical shell if the normal stress in the bolts should not exceed 250 MPab. the minimum required thickness of the hemispherical shells if the normal stress in the shell should not exceed 125 MPac. the hoop stress in the cylinderd. the minimum require spacing of the bolts in the cylindrical shell if the normal stress in the bolts should not exceed 250 MPa.arrow_forward
- A compound shaft drives three gears, as shown. Segments (1) and (2) of the compound shaft are hollow bronze [G = 6,500 ksi] tubes, which have an outside diameter of 2.15 in. and a wall thickness of 0.1375 in. Segments (3) and (4) are solid 1.15-in.-diameter steel [G = 11,500 ksi] shafts. The shaft lengths are L1 = 62 in., L2 = 8 in., L3 = 25 in., and L4 = 33 in. The torques applied to the shafts have magnitudes of TB = 980 lb·ft, TD = 420 lb·ft, and TE = 170 lb·ft, acting in the directions shown. The bearings shown allow the shaft to turn freely. Using the sign convention presented in Section 6.6., calculate: (a) the magnitude of the maximum shear stress in the compound shaft. (b) the rotation angle of flange C with respect to flange A. (c) the rotation angle of gear E with respect to flange A.arrow_forwardA bolted connection shown is bolted with a A-325 bolts with an allowable shearing stress of 207 MPa. A-36 steel is used. The applied force "T" is equally divided among the bolts. Assume bolt hole diameter to be 3 mm bigger than bolt diameter. Diameter of bolt is 20 mm. T/2 Lamamatax 300 mm A Determine the efficiency in percentage. с 90.15 10 mm 94.58 DOOG OOO OO T/2 10 mm T/2 B D 93.19 90.61arrow_forwardPart A If the required clamping force at the board A is to be 85 N, determine the torque M that must be applied to the handle of the "C" clamp to tighten it down. The single square-threaded screw has a mean radius of 10 mm, a lead of 3 mm, and the coefficient of static friction is u, = 0.35. Express your answer to three significant figures and include the appropriate units. M = 1.1142 Nm O The unit you entered is not recognized. Review a list of acceptable units. No credit lost. Try again. Submit Previous Answers Request Answer Figure 1 of 1 Provide Feedback Next > M O Pearsonarrow_forward
- Structural Analysis (10th Edition)Civil EngineeringISBN:9780134610672Author:Russell C. HibbelerPublisher:PEARSONPrinciples of Foundation Engineering (MindTap Cou...Civil EngineeringISBN:9781337705028Author:Braja M. Das, Nagaratnam SivakuganPublisher:Cengage Learning
- Fundamentals of Structural AnalysisCivil EngineeringISBN:9780073398006Author:Kenneth M. Leet Emeritus, Chia-Ming Uang, Joel LanningPublisher:McGraw-Hill EducationTraffic and Highway EngineeringCivil EngineeringISBN:9781305156241Author:Garber, Nicholas J.Publisher:Cengage Learning
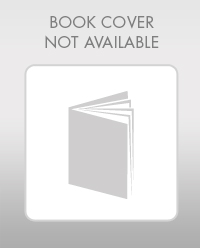
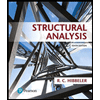
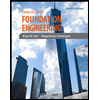
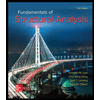
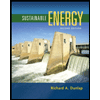
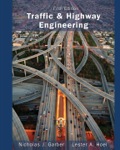