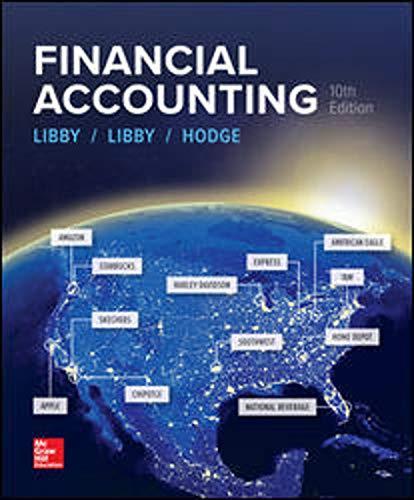
FINANCIAL ACCOUNTING
10th Edition
ISBN: 9781259964947
Author: Libby
Publisher: MCG
expand_more
expand_more
format_list_bulleted
Question
A company bought 45,025 pounds of plastic pellets to make DVDs at a cost of $9,990. The
Expert Solution

This question has been solved!
Explore an expertly crafted, step-by-step solution for a thorough understanding of key concepts.
This is a popular solution
Trending nowThis is a popular solution!
Step by stepSolved in 2 steps

Knowledge Booster
Learn more about
Need a deep-dive on the concept behind this application? Look no further. Learn more about this topic, accounting and related others by exploring similar questions and additional content below.Similar questions
- Bandar Industries manufactures sporting equipment. One of the company's products is a football helmet that requires special plastic. During the quarter ending June 30, the company manufactured 3,800 helmets, using 2,812 kilograms of plastic. The plastic cost the company $21,371. According to the standard cost card, each helmet should require 0.66 kilogram of plastic, at a cost of $8.00 per kilogram. Required: 1. What is the standard quantity of kilograms of plastic (SQ) that is allowed to make 3,800 helmets? 2. What is the standard materials cost allowed (SQ x SP) to make 3,800 helmets? 3. What is the materials spending variance? 4. What are the materials price variance and the materials quantity variance? Note: For requirements 3 and 4, indicate the effect of each variance by selecting "F" for favorable, "U" for unfavorable, and "None" for no effect (i.e., zero variance). Input all amounts as positive values. Do not round intermediate calculations. 1. Standard quantity of kilograms…arrow_forwardPan Demic, Inc. (PDI) manufactures and sells cast iron skillets. A finished skillet sells for $40 and costs $15 to manufacture. PDI uses one raw material, iron ore, which is buys for $8/pound. Skillet Forgers heat the iron ore and form it into skillets. Forgers are paid $55/hour. Period 1: During the period, PDI purchased $4,000 of Iron Ore. At the end of the period, they had $2,400 of ore left in Raw Materials They used 120 hours of direct labor and incurred $12,000 of Factory Overhead. At the beginning of the period, PDI had $3,000 of costs in WIP and $2,400 of costs in Finished Goods. Prepare the Schedule of Cost of Goods Sold for PDI. Do not use dollar signs. Use whole numbers only (no decimal places) PDI Schedule of Cost of Goods Sold Finished Goods Beginning Inventory Cost of Goods Manufactured Account Cost of Goods Available for Sale Finished Goods Ending Inventory Cost of Goods Sold WIP Inventory Based on your work above, compete the Inventory section of the Balance Sheet as of…arrow_forwardHarold Manufacturing produces denim clothing. This year, it produced 5,280 denim jackets at a manufacturing cost of $41.00 each. These jackets were damaged in the warehouse during storage. Management investigated the matter and identified three alternatives for these jackets. 1. Jackets can be sold to a secondhand clothing shop for $7.00 each. 2. Jackets can be disassembled at a cost of $32,800 and sold to a recycler for $11.00 each. 3. Jackets can be reworked and turned into good jackets. However, with the damage, management estimates it will be able to assemble the good parts of the 5,280 jackets into only 3,050 jackets. The remaining pieces of fabric will be discarded. The cost of reworking the jackets will be $101,400, but the jackets can then be sold for their regular price of $41.00 each. Required: 1. Calculate the incremental income. Incremental revenue Incremental costs Incremental income Alternative 1 Sell to a second- hand shop Alternative 2 Disassemble and sell to a recycler…arrow_forward
- Bandar Industries manufactures sporting equipment. One of the company's products is a football helmet that requires special plastic. During the quarter ending June 30, the company manufactured 4,000 helmets, using 2,200 kilograms of plastic. The plastic cost the company $14,520. According to the standard cost card, each helmet should require 0.50 kilograms of plastic, at a cost of $7.00 per kilogram. Required: 1. What is the standard quantity of kilograms of plastic (SQ) that is allowed to make 4,000 helmets? 2. What is the standard materials cost allowed (SQ × SP) to make 4,000 helmets? 3. What is the material's spending variance?arrow_forwardRough Stuff makes 2 products: khaki shorts and khaki pants for men. Each product passes through the cutting machine area, which is the chief constraint during production. Khaki shorts take 15 minutes on the cutting machine and have a contribution margin per pair of shorts of $17. Khaki pants take 24 minutes on the cutting machine and have a contribution margin per pair of pants of $34. If it is assumed that Rough Stuff has 4,800 hours available on the cutting machine to service a minimum demand for each product of 3,000 units, how much will profits increase if 88 more hours of machine time can be obtained? $????arrow_forwardCowboy Ice Cream Company (CIC) produces ice cream bars that it markets through a variety of grocery stores. It makes the ice cream bars in batches of 2,000 units. CIC produced 36,000 ice cream bars during the prior accounting period. The cost of producing the ice cream bars is shown below. Materials cost ($29 per unit x 36,000) Labor cost ($26 per unit x 36,000) Manufacturing supplies ($9 x 36,000) Batch-level costs (18 batches at $6,000 per batch) Product-level costs $1,044,000 936,000 324,000 108,000 300,000 370,000 Facility-level costs Total costs $3,082,000 Cost per unit = $3,082,000 + 36, 000 = $85.61 Required a. OnCue has offered to buy a batch of 500 ice cream bars for $68 each. CIC's normal selling price is $93 per unit. Calculate the relevant cost per unit for the special order. Based on the preceding quantitative data, should CIC accept the special order? b. OnCue offered to buy a batch of 2,000 ice cream bars for $68 per unit, calculate the relevant cost per unit for the…arrow_forward
- Rough Stuff makes 2 products: khaki shorts and khaki pants for men. Each product passes through the cutting machine area, which is the chief constraint during production. Khaki shorts take 15 minutes on the cutting machine and have a contribution margin per pair of shorts of $15. Khaki pants take 24 minutes on the cutting machine and have a contribution margin per pair of pants of $30. If it is assumed that Rough Stuff has 4,800 hours available on the cutting machine to service a minimum demand for each product of 3,000 units, how much will profits increase if 82 more hours of machine time can be obtained?arrow_forwardBandar Industries manufactures sporting equipment. One of the company's products is a football helmet that requires special plastic. During the quarter ending June 30, the company manufactured 3,400 helmets, using 2,584 kilograms of plastic. The plastic cost the company $17,054. According to the standard cost card, each helmet should require 0.69 kilogram of plastic, at a cost of $7.00 per kilogram. Required: 1. What is the standard quantity of kilograms of plastic (SQ) that is allowed to make 3,400 helmets? 2. What is the standard materials cost allowed (SQx SP) to make 3,400 helmets? 3. What is the materials spending variance? 4. What are the materials price variance and the materials quantity variance? Note: For requirements 3 and 4, indicate the effect of each variance by selecting "F" for favorable, "U" for unfavorable, and "None" for no effect (i.e., zero variance). Input all amounts as positive values. Do not round intermediate calculations. 1. Standard quantity of kilograms…arrow_forwardTerminator, Inc., manufactures a motorcycle part in lots of 350 units. The raw materials cost for the part is $170, and the value added in manufacturing 1 unit from its components is $320, for a total cost per completed unit of $490. The lead time to make the part is 2 weeks, and the annual demand is 3,800 units. Assume 50 working weeks per year. a. How many units of the part are held, on average, as cycle inventory? nothing units. (Enter your response as an integer.) What is its value? $nothing. (Enter your response as an integer.) b. How many units of the part are held, on average, as pipeline inventory? nothing units. (Enter your response as an integer.) What is its value? $nothing. (Enter your response as an integer.)arrow_forward
arrow_back_ios
arrow_forward_ios
Recommended textbooks for you
- AccountingAccountingISBN:9781337272094Author:WARREN, Carl S., Reeve, James M., Duchac, Jonathan E.Publisher:Cengage Learning,Accounting Information SystemsAccountingISBN:9781337619202Author:Hall, James A.Publisher:Cengage Learning,
- Horngren's Cost Accounting: A Managerial Emphasis...AccountingISBN:9780134475585Author:Srikant M. Datar, Madhav V. RajanPublisher:PEARSONIntermediate AccountingAccountingISBN:9781259722660Author:J. David Spiceland, Mark W. Nelson, Wayne M ThomasPublisher:McGraw-Hill EducationFinancial and Managerial AccountingAccountingISBN:9781259726705Author:John J Wild, Ken W. Shaw, Barbara Chiappetta Fundamental Accounting PrinciplesPublisher:McGraw-Hill Education
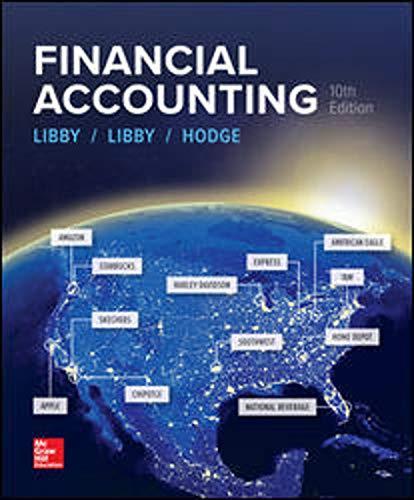
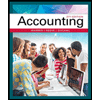
Accounting
Accounting
ISBN:9781337272094
Author:WARREN, Carl S., Reeve, James M., Duchac, Jonathan E.
Publisher:Cengage Learning,
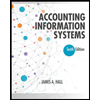
Accounting Information Systems
Accounting
ISBN:9781337619202
Author:Hall, James A.
Publisher:Cengage Learning,
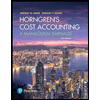
Horngren's Cost Accounting: A Managerial Emphasis...
Accounting
ISBN:9780134475585
Author:Srikant M. Datar, Madhav V. Rajan
Publisher:PEARSON
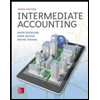
Intermediate Accounting
Accounting
ISBN:9781259722660
Author:J. David Spiceland, Mark W. Nelson, Wayne M Thomas
Publisher:McGraw-Hill Education
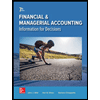
Financial and Managerial Accounting
Accounting
ISBN:9781259726705
Author:John J Wild, Ken W. Shaw, Barbara Chiappetta Fundamental Accounting Principles
Publisher:McGraw-Hill Education