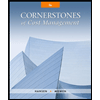
Cornerstones of Cost Management (Cornerstones Series)
4th Edition
ISBN: 9781305970663
Author: Don R. Hansen, Maryanne M. Mowen
Publisher: Cengage Learning
expand_more
expand_more
format_list_bulleted
Question
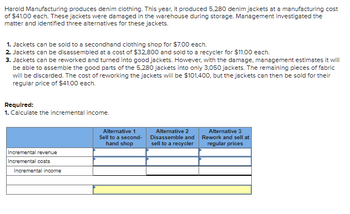
Transcribed Image Text:Harold Manufacturing produces denim clothing. This year, it produced 5,280 denim jackets at a manufacturing cost
of $41.00 each. These jackets were damaged in the warehouse during storage. Management investigated the
matter and identified three alternatives for these jackets.
1. Jackets can be sold to a secondhand clothing shop for $7.00 each.
2. Jackets can be disassembled at a cost of $32,800 and sold to a recycler for $11.00 each.
3. Jackets can be reworked and turned into good jackets. However, with the damage, management estimates it will
be able to assemble the good parts of the 5,280 jackets into only 3,050 jackets. The remaining pieces of fabric
will be discarded. The cost of reworking the jackets will be $101,400, but the jackets can then be sold for their
regular price of $41.00 each.
Required:
1. Calculate the incremental income.
Incremental revenue
Incremental costs
Incremental income
Alternative 1
Sell to a second-
hand shop
Alternative 2
Disassemble and
sell to a recycler
Alternative 3
Rework and sell at
regular prices
Expert Solution

This question has been solved!
Explore an expertly crafted, step-by-step solution for a thorough understanding of key concepts.
Step by stepSolved in 3 steps

Knowledge Booster
Learn more about
Need a deep-dive on the concept behind this application? Look no further. Learn more about this topic, accounting and related others by exploring similar questions and additional content below.Similar questions
- Hip Manufacturing produces denim clothing. This year it produced 3,140 denim jackets at a cost of $94,200. These jackets were damaged in the warehouse during storage. Management identified three alternatives for these jackets. 1. Jackets can be sold as scrap to a secondhand clothing shop for $18,840. 2. Jackets can be disassembled at a cost of $6,280 and sold to a recycler for $37,680. 3. Jackets can be reworked and turned into good jackets. The cost of reworking the jackets will be $106,760, and the jackets can then be sold for $141,300. Required: (1) Compute the income for each alternative. (2) Which alternative should be chosen? Scrap, Recycle or Rework Analysis Revenue from scrap/recycle/rework Cost of recycled/reworked units Income Scrap Recycle Reworkarrow_forwardHarold Manufacturing produces denim clothing. This year, it produced 5,000 denim jackets at a manufacturing cost of $45 each. These jackets were damaged in the warehouse during storage. Management investigated the matter and identified three alternatives for these jackets. 1. Jackets can be sold as is to a secondhand clothing shop for $6 each. 2. Jackets can be disassembled at a cost of $32,000 and sold to a recycler for $12 each. 3. Jackets can be reworked and turned into good jackets. However, with the damage, management estimates it will be able to assemble the good parts of the 5,000 jackets into only 3,000 jackets. The remaining pieces of fabric will be discarded. The cost of reworking the jackets will be $102,000, but the jackets can then be sold for their regular price of $45 each. Required: 1. Calculate the incremental income. Alternative 1 Sell to a secondhand shop Alternative 2 Disassemble and sell to a recycler Alternative 3 Rework and sell at regular prices Incremental…arrow_forwardEarrow_forward
- Ampro-Mag is a small company that makes materials for safely controlling hazardous spills of all kinds. It sells these items as a neutralizing kit priced at $120. The costs of the materials that go into each kit are $45. It costs $5 in labor to assemble a kit. The company has monthly expenses of $1,000 for rent and insurance, $200 for 3 heat and electricity, $500 for advertising in trade journals, and $3,500 for the monthly salary of its owner. What is Ampro-Mag's monthly break-even point in terms of number of neutralizing kits sold? Ace Shoe Company sells heel replacement kits for men's shoes. It has fixed costs of $6 million and unit variable costs of $5 per pair. Ace is considering a switch from manual labour to an automated process. New equipment would cost an additional $4 million per year while lowering variable costs by $3 per shoe repair kit. How many kits would Ace have to sell at $15 per pair to make $2 million in profits in the next year with the automated process? Swiss…arrow_forwardHeyer Appliances assembles dishwashers at its plant in Tuscaloosa, Alabama. In February 2017, 60 circulation motors that cost $110 each (from a new supplier who subsequently went bankrupt) were defective and had to be disposed of at zero net disposal value. Heyer Appliances was able to rework all 60 dishwashers by substituting new circulation motors purchased from one of its existing suppliers. Each replacement motor cost $125. Q. Should Heyer Appliances use the $110 circulation motor or the $125 motor to calculate the cost of materials reworked? Explain.arrow_forwardEdmund Supplies Company sold 3,170 metal connectors on account to Door Incorporated for $200 each on September 15. Each metal connector costs Edmund $150 to make. Door has 60 days to return the unused goods. Edmund believes that Door will ultimately return 75 of the connectors. On September 29, Door returns 50 connectors. Edmund has a September 30 fiscal year end. At year end, Edmund believes 75 connectors is a good estimate of the total that will be returned. The cost of recovering these products is immaterial. Edmund expects to be able to resell these goods for a profit. Instructions Prepare the following journal entries on the books of Edmund Company: Entries to record the initial sales on September 15. Entries to record the return of goods September 29. Entries to record the year-end adjustment based on estimated returns on September 30.arrow_forward
- Teal Mountain Company has been a retailer of audio systems for the past 3 years. However, after a thorough survey of audio system markets, Teal Mountain decided to turn its retail store into an audio equipment factory. Production began October 1, 2022. Direct materials costs for an audio system total $77 per unit. Workers on the production lines are paid $13 per hour. An audio system takes 6 labor hours to complete. In addition, the rent on the equipment used to assemble audio systems amounts to $5,070 per month. Indirect materials cost $5 per system. A supervisor was hired to oversee production; her monthly salary is $3,700. Factory janitorial costs are $2,030 monthly. Advertising costs for the audio system will be $9,030 per month. The factory building depreciation is $6,360 per year. Property taxes on the factory building will be $8,520 per year. Assuming that Teal Mountain manufactures, on average, 1,400 audio systems per month, enter each cost item on your answer sheet, placing…arrow_forwardABC Company manufactures boats. During September, 2020, the company purchased 100 cellular phones at a cost of P100 each. Isaac withdrew 70 phones from the warehouse during the month. Twenty of these phones were installed in salespersons’ cars and the remaining 50 phones were put in boats manufactured during the month. Of the boats put into production during September, 2020, 80% were completed and transferred to the company's storage lot. Fifty percent of the boats completed during the month were sold by September 30. COMPUTE FOR THE: 1. cost of goods sold 2.COMPUTE THE SELLING EXPENSES 3. COMPUTE HOW MUCH IS THE FINISHED GOODS INVENTORY OF CELLULAR PHONES 4. COMPUTE HOW MUCH IS THE WORK IN PROCESS INVENTORY OF CELLULAR PHONES 5. COMPUTE HOW MUCH IS THE RAW MATERIALS INVENTORY OF CELLULAR PHONESarrow_forwardKinnear Plastics manufactures various components for the aircraft and marine industry. Kinnear buys plastic from two vendors: Tappan Corporation and Hill Enterprises. Kinnear chooses the vendor based on price. Once the plastic is received, it is inspected to ensure that it is suitable for production. Plastic that is deemed unsuitable is disposed of. The controller at Kinnear collected the following information on purchases for the past year: Tappan Hill Total purchases (tons) 6,000 10,000 Plastic discarded 120 600 The purchasing manager has just received bids on an order for 290 tons of plastic from both Tappan and Hill. Tappan bid $1,813 and Hill bid $1,786 per ton. Required: Assume that the average quality, measured by the amounts discarded…arrow_forward
- Splish Brothers Company has been a retailer of audio systems for the past 3 years. However, after a thorough survey of audio system markets Spish Brothers decided to turn its retail store into an audio equipment factory Production began October 1.2025. Direct materials costs for an audio system total $75 per unit Workers on the production lines are paid $15 per hour An audio system takes 7 labor hours to complets. In addition, the rent on the equipment used to assemble audio systems amounts to $5,960 per month Indirect materials cost $7 per system. A supervisor was hired to oversee production her monthly salary is $2.060 Factory janitorial costs are $2.310 monthly Advertising costs for the audio system will be $9.330 per month. The factory building depreciation is $7,080 per year. Property taxes on the factory building will be $8.400 per year (a) Assuming that Splish Brothers manufactures, on average 1.500 audio systems per month enter each cost item on your answer sheet placing the…arrow_forwardHarmon Household Products, Inc., manufactures a number of consumer items for general household use. One of these products, a chopping board, requires an expensive hardwood. During a recent month, the company manufactured 4,000 chopping boards using 11,000 board feet of hardwood. The hardwood cost the company $18,700. The company’s standards for one chopping board are 2.5 board feet of hardwood, at a cost of $1.80 per board foot. Required: 1. What cost for wood should have been incurred to make 4,000 chopping blocks? How much greater or less is this than the cost that was incurred? 2. Break down the difference computed in (1) above into a materials price variance and a materials quantity variance.arrow_forwardElijah Electronics makes wireless headphone sets. The firm produced 58,500 wireless headphone sets during its first year of operation. At year-end, it had no inventory of finished goods. Elijah sold 54,990 units through regular market channels, but 585 of the units produced were so defective that they had to be sold as scrap. The remaining units were reworked and sold as seconds. For the year, the firm spent $312,000 on prevention costs and $156,000 on quality appraisal. There were no customer returns. An income statement for the year follows. (See attached) a. Compute the total pre-tax profit lost by the company in its first year of operations by selling defective units as seconds or as scrap rather than selling the units through regular channels. $______ b. Compute the total failure cost for the company in its first year. $______ c. Compute total quality cost incurred by the company in its first year. $______arrow_forward
arrow_back_ios
SEE MORE QUESTIONS
arrow_forward_ios
Recommended textbooks for you
- Cornerstones of Cost Management (Cornerstones Ser...AccountingISBN:9781305970663Author:Don R. Hansen, Maryanne M. MowenPublisher:Cengage LearningPrinciples of Accounting Volume 2AccountingISBN:9781947172609Author:OpenStaxPublisher:OpenStax College
- Managerial Accounting: The Cornerstone of Busines...AccountingISBN:9781337115773Author:Maryanne M. Mowen, Don R. Hansen, Dan L. HeitgerPublisher:Cengage LearningEssentials Of Business AnalyticsStatisticsISBN:9781285187273Author:Camm, Jeff.Publisher:Cengage Learning,
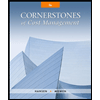
Cornerstones of Cost Management (Cornerstones Ser...
Accounting
ISBN:9781305970663
Author:Don R. Hansen, Maryanne M. Mowen
Publisher:Cengage Learning
Principles of Accounting Volume 2
Accounting
ISBN:9781947172609
Author:OpenStax
Publisher:OpenStax College
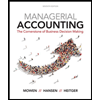
Managerial Accounting: The Cornerstone of Busines...
Accounting
ISBN:9781337115773
Author:Maryanne M. Mowen, Don R. Hansen, Dan L. Heitger
Publisher:Cengage Learning
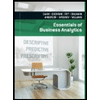
Essentials Of Business Analytics
Statistics
ISBN:9781285187273
Author:Camm, Jeff.
Publisher:Cengage Learning,