BSBWHS518_AG_SW_1of1
pdf
School
TAFE NSW - Sydney Institute *
*We aren’t endorsed by this school
Course
518
Subject
Mechanical Engineering
Date
Apr 3, 2024
Type
Pages
25
Uploaded by ChefDanger980
Student Workbook Answer Guide Topics 1-5 BSBWHS518 Manage WHS hazards associated with maintenance and use of plant
Document title: BSBWHS518_AG_SW_1of1 Page 2 of 25 Resource ID: TBS_20_003_BSBWHS518_AG_SW_1of1 © TAFE NSW 2020 TAFE NSW would like to pay our respect and acknowledge Aboriginal and Torres Strait Islander Peoples as the Traditional Custodians of the Land, Rivers and Sea. We acknowledge and pay our respect to the Elders, both past and present of all Nations. Version: 20201130
Date created: 30 November 2020 Date modified: Region to insert date if modified For queries contact: Technology and Business Services SkillsPoint © TAFE NSW 2020 RTO Provider Number 90003 | CRICOS Provider Code: 00591E This resource is based on information from the BSBWHS518 Learner Resources, © RTO Materials Ltd. Contact to the user licence agreement at the relevant SkillsPoint
This resource can be found in the TAFE NSW Learning Bank. The content in this document is copyright © TAFE NSW 2020 and should not be reproduced without the permission of TAFE NSW. Information contained in this document is correct at time of printing: 15 February 2021. For current information please refer to our website or your teacher as appropriate.
Document title: BSBWHS518_AG_SW_1of1 Page 3 of 25 Resource ID: TBS_20_003_BSBWHS518_AG_SW_1of1 © TAFE NSW 2020 Contents Feedback: Topic 1 .......................................................................................................................
4
Activity 1.1: Identify how to access sources of WHS information ........................................
4
Activity 1.2: identify how to inspect items of plant and identify how they are to be used . 5
Activity 1.3: Determine WHS hazards ...................................................................................
7
Activity 1.4: Forum: Consult with others to confirm hazard identification ..........................
8
Activity 1.5: Identify how to record and report identified hazards ......................................
9
Feedback: Topic 2 .....................................................................................................................
11
Activity 2.1: Identify how to access sources of information, data and advice ...................
11
Activity 2.2: Identify how to consult with others to inform WHS risk assessment ............
11
Activity 2.3: Identify how to record and report on WHS risk assessment ..........................
13
Feedback: Topic 3 .....................................................................................................................
14
Activity 3.1: Identify how to access sources of information, data ......................................
14
Activity 3.2: Identify how to develop risk controls .............................................................
14
Activity 3.3: Forum: Identify how to consult with internal and specialist personnel .........
15
Activity 3.4: Identify how to communicate rights, obligations and duties of workplace personnel
.............................................................................................................................
16
Activity 3.5: Identify how to monitor the effectiveness of implemented risk controls .....
18
Activity 3.6: Identify how to record and report on implemented risk controls .................
19
Feedback: Topic 4 .....................................................................................................................
20
Activity 4.1: Identify types of plant requiring registration and tasks requiring operator licensing ...............................................................................................................................
20
Activity 4.2: Identify how to document registration, licensing and certification requirements .......................................................................................................................
21
Activity 4.3: Identify how to monitor and report compliance with WHS regulatory requirements .......................................................................................................................
21
Feedback: Topic 5 .....................................................................................................................
23
Activity 5.1: Identify WHS-related training needs and identify skill gaps ...........................
23
Activity 5.2: Identify how to ensure training is undertaken and completed ......................
24
Image attributions ....................................................................................................................
25
Your preview ends here
Eager to read complete document? Join bartleby learn and gain access to the full version
- Access to all documents
- Unlimited textbook solutions
- 24/7 expert homework help
Document title: BSBWHS518_AG_SW_1of1 Page 4 of 25 Resource ID: TBS_20_003_BSBWHS518_AG_SW_1of1 © TAFE NSW 2020 Feedback: Topic 1 Activity 1.1: Identify how to access sources of WHS information For two different items of plant used at your organisation, or in your business industry, access WHS information and research how you can work safely with these items. Document your findings using MS Word or similar and provide a one A4 page summary of your findings; as a minimum, you must include: •
three WHS requirements or recommendations for each item of plant and •
provide a reference of your information sources (stating the name of the source and where you obtained this from). Note: Information must be sourced from trusted/authoritative sources; this may include WHS legislation, codes of practice, manufacturer information and WHS legal advice sources. You will need to attach your document to this workbook, labelled with your name and activity reference number. Feedback
You must access WHS information and research on how to work safely with two different items of plant that are used at your organisation or in your business industry. You must provide a reference for your information sources with your written summary. Items of plant may vary, depending on your business industry; plant may include: •
pressure equipment •
cranes •
hoists •
lifts, escalators and moving walkways •
manufacturing machines •
printing machines •
scaffolding •
amusement devices. Working safely may relate to: •
using machine guards •
using PPE •
setting-up plant •
working in isolation from others •
working with a colleague
Document title: BSBWHS518_AG_SW_1of1 Page 5 of 25 Resource ID: TBS_20_003_BSBWHS518_AG_SW_1of1 © TAFE NSW 2020 •
performing maintenance and machine care •
checking plant readings or machine parts •
having isolation controls to turn off energy sources •
having emergency stops to shut-down machinery •
having alarms and lights to warn of plant use. Activity 1.2: identify how to inspect items of plant and identify how they are to be used Resources and equipment required to complete this activity: •
A real or simulated work environment such as Plan2go (visit Plan2go by logging in with your TAFE NSW credentials). (Long URL: https://plan2go.nctafe.edu.au/) •
Policy and procedures for inspecting plant (from your workplace or you may use Appendix A at the end of this workbook).
•
Two items of workplace plant (as relevant to your business industry). You are required to inspect two items of workplace plant and record what they are and how they are to be used. You should include any relevant notes relating to health and safety, such as wear and tear of plant, emergency stop functions or machine guards. You may include photographs to support your findings. Attach to this workbook with a reference to the activity number in the file name. Feedback
Plant How is it used WHS considerations Existing controls The saw is operated by a person who stands in front and pulls the handle down to apply pressure from the blade onto the metal to be cut. Steel is loaded onto the roller bed prior to cutting. PPS requirements, glasses and or face shield, gloves. Rotating machinery poses a risk of entanglement, particularly loose clothing and long hair. Manual handling of heavy lengths of steel. Guard is in place over the blade. Existing controls include the safe operating procedure and PPE provided for the operator. Forklift for heavy lifting, or use of other people to carry out a team lift as specified in the safe operating procedure.
Document title: BSBWHS518_AG_SW_1of1 Page 6 of 25 Resource ID: TBS_20_003_BSBWHS518_AG_SW_1of1 © TAFE NSW 2020 Plant How is it used WHS considerations Existing controls No existing emergency stop is installed. Hydraulic Press is operated by an individual using control levers. Work item to be pressed is loaded onto the bed of the press in the desired position. Press is operated until the work item is in the desired. state Work item is removed from the press bed. Crush injury of the operator is holding the work item. Flying objects if the work item is not positioned safely and securely. Hydraulic injection injury if the hoses or fittings fail. No guarding is in place. No emergency stop is installed. A competent person regularly services the press. Safe Operating Procedure in place and personnel trained before use.
Your preview ends here
Eager to read complete document? Join bartleby learn and gain access to the full version
- Access to all documents
- Unlimited textbook solutions
- 24/7 expert homework help
Document title: BSBWHS518_AG_SW_1of1 Page 7 of 25 Resource ID: TBS_20_003_BSBWHS518_AG_SW_1of1 © TAFE NSW 2020 Activity 1.3: Determine WHS hazards Following on from Activity 1.2: identify how to inspect items of plant and identify how they are to be used
, as relevant to your work environment, document the hazards that are associated with using the two items of plant, their condition, their suitability for the workplace, their potential location in the workplace and any potential abnormal situations that may exist. Feedback
You must refer to Activity 1.2, and the inspections carried out. You must document your conclusions found from the assessment of your inspections. You must identify any hazards with: Plant 1 – Cut-off saw Plant 2 – Hydraulic press Using the plant Plant operation requires the operator to place and clamp the steel to be cut in position, turn on the saw and use the handle to pull the saw down and cut through the steel. When the steel has been cut, the handle is raised, and the plant turned off. Plant operation requires the operator to place the item to be "pressed" onto the bed of the press in a suitable position. The operator will need to select a suitable "dolly" for the pressing application and hold or secure it in place while operating a lever to extend the ram until it contacts the dolly. At this point, the operator can let go of the dolly and operate the levers to finish the process. The condition of the plant The saw is old, though well maintained and serviceable. The table it operates on is well made and fitted with rollers to make the operation easier. The press is old, functional and in good order, though lacks the relevant engineering approval. If anything it is over-engineered for its "pressing capacity", though this has not been formally assessed. Their suitability for the workplace Both items of plant are suitable for use in this workplace. They are well constructed, robust and well serviced/maintained. The lack of engineering certification on the press is a concern which needs to be addressed. This is something that can be corrected. Both items of plant are suitable for use in this workplace. They are well constructed, robust and well serviced/maintained. The lack of engineering certification on the press is a concern which needs to be addressed. This is something that can be corrected.
Document title: BSBWHS518_AG_SW_1of1 Page 8 of 25 Resource ID: TBS_20_003_BSBWHS518_AG_SW_1of1 © TAFE NSW 2020 Plant 1 – Cut-off saw Plant 2 – Hydraulic press Their potential location in the workplace Both items of plant are in a suitable location for their intended use. The saw has been placed so that lengths of steel can be fed into it without pre-cutting, and the wall modified so that long pieces can be cut off and removed without obstruction. The press is located outside, under a skillion roof which provides a level of separation from other staff at the worksite should something o wrong during the process. Both items of plant are in a suitable location for their intended use. The saw has been placed so that lengths of steel can be fed into it without pre-cutting, and the wall modified so that long pieces can be cut off and removed without obstruction. The press is located outside, under a skillion roof which provides a level of separation from other staff at the worksite should something o wrong during the process. Any abnormal situations that may exist with the plant. The normal operation of the saw requires a pre-start checklist to be completed which will highlight any issues with the operation of the saw. The main area of concern is damage to the saw blade. There are no abnormal situations that may exist with the plant. It is particularly hazardous if used incorrectly. Activity 1.4: Forum: Consult with others to confirm hazard identification Go to the Forum and post the hazards that you found in Activity 1.3: Determine WHS hazards. Then
comment on the potential harm that may be caused by their occurrence. Post your response in the 'Consult with others to confirm hazard identification' forum. After you have posted your answers, review the replies of other students and, where appropriate, provide feedback on others' responses. Feedback
You must post your answers in the forum, review the replies of other students and, where appropriate, provide feedback on others' responses. You must comment on what you confirm and identify the potential harm that may be caused by each one. For example, hazards and their harm may include: •
Exposed moving parts – operators may become caught in machinery. •
Hot temperature of plant – operators and passers-by may suffer burns if touching hot parts. •
Noisy machinery – operators may not hear other people or noises around them, making them unaware of what is happening around them.
Document title: BSBWHS518_AG_SW_1of1 Page 9 of 25 Resource ID: TBS_20_003_BSBWHS518_AG_SW_1of1 © TAFE NSW 2020 Activity 1.5: Identify how to record and report identified hazards Refer to Case study: Policies and procedures for recording and reporting hazards. 1.
Record your confirmed hazards from Activity 1.4: Consult with others to confirm hazard identification
, following the policy and procedures provided. Feedback
You must follow the guidance provided in the case study to record your confirmed hazards from Activity 1.4. This must be written clearly and permanently, state the hazards and where they are found, state the individuals or parties who are at risk and include their name and the date the report was made. Case study: Policies and procedures for recording and reporting hazards Recording and reporting hazards policy WHS hazards that are identified must be documented and communicated to all relevant personnel; they must be acted upon to prevent risks from occurring or for risks to be controlled to a safe level. Records of hazards must identify the hazard, where this is found, and the persons who are affected by the hazard. Reports should be made to the officer (as soon as it is possible to do so), so hazard/risk management can take place. Recording and reporting hazards procedures Records of hazards must be completed in the following way: • be written clearly and in a permanent form (that is, permanent ink on paper or saved in organisational electronic records) • state the hazard and where this is found • state the individuals and/or parties who are at risk from the hazard • include the name of the person making the record and the date this was made. Reporting hazards must be completed in the following way: • reports must be made to the officer (in person or writing) • report must be made as soon after identification of the hazard, as is possible • reports must be an accurate account of the hazard record that is made and be addressed to 'The Officer'.
Your preview ends here
Eager to read complete document? Join bartleby learn and gain access to the full version
- Access to all documents
- Unlimited textbook solutions
- 24/7 expert homework help
Document title: BSBWHS518_AG_SW_1of1 Page 10 of 25 Resource ID: TBS_20_003_BSBWHS518_AG_SW_1of1 © TAFE NSW 2020 2.
Using the record, you have made, create a short report to inform the officer of the hazards that have been found. For this activity, you may use a suitable report template, create your own using MS Word or similar. Your report should be at least 1 x A4 page. Please ensure you attach a copy to this workbook referencing the activity number. Feedback
You must follow the guidance provided in Case study A to report the hazards to the officer in writing. This must be an accurate account of the hazard record that has been made in activity question one. This report will be similar to the record but must be addressed to 'The Officer'. For example: Dear John, During our recent Plant Inspection at the workshop, a number of items of plant were targeted as part of our in-depth study process. This included a metal cut-off saw and a hydraulic press. The Saw was a fairly normal example of this type of plant. It was not in new condition, though it has clearly been well maintained and serviced. The blade was in good order with no signs of premature failure. The area where the saw was set up is serviceable and functional. The Hydraulic Press is in good operational condition and has been well maintained. It is quite old, though it has had a number of components replaced. While there are no major concerns with this piece of plant from an operational perspective, it does lack the required engineering certification or load rating. This needs to be rectified ASAP. Corrective actions from this process include: •
Review the Safe Operating procedures for both items of plant •
Engage a suitably qualified engineer to calculate the safe working load of the press and install a placard. Your assistance with any financial approval is appreciated. Regards, Worker Bill.
Document title: BSBWHS518_AG_SW_1of1 Page 11 of 25 Resource ID: TBS_20_003_BSBWHS518_AG_SW_1of1 © TAFE NSW 2020 Feedback: Topic 2 Activity 2.1: Identify how to access sources of information, data and advice Following on from Activity 1.4: Consult with others to confirm hazard identification;
for three of the plant hazards that you identified, access reputable sources of information, data and/or advice to help you assess the risks to health and safety. List your three hazards, your information sources, and what you have found. Feedback
You must access sources of information, data or advice to help them assess the risks to three hazards found with the plant from Activity 1.4. The information, data or advice must come from recognised and authoritative sources. You must write down three hazards and associated risks; must identify what you have found through the information, data or advice that has been received. For example, risks may relate to: •
injury or fatality •
damage to the workplace •
loss of work production. Sources of information may include: •
WHS personnel •
WHS regulator •
WHS/OHS codes of practice •
WHS authorities, agencies and consultants. Activity 2.2: Identify how to consult with others to inform WHS risk assessment Following on from Activity 2.1: Identify how to access sources of information, data and advice,
you will now prepare an email to your manager informing them about the three hazard and associated risks with the plant. Your email communication must include relevant details and their impact on others and the environment. In closing, you will need to seek feedback from your manager that they agree on their level of impact and severity of the risk.
Document title: BSBWHS518_AG_SW_1of1 Page 12 of 25 Resource ID: TBS_20_003_BSBWHS518_AG_SW_1of1 © TAFE NSW 2020 You may research a suitable template that can be modified or create your own using MS Word/Outlook or similar program and attach to this workbook referencing the activity number in the file name. Feedback
Student responses must cover the key points above. For example: To: Management Subject: Plant associated Risks Body: Dear Manager, The WHS Department has recently carried out a workplace inspection and uncovered several issues associated with some plant in the workshop. There are two key items of plant which were the focus of risk management activities following the inspection. These are a metal cut-off saw and a hydraulic press. A number of risks are evident: •
Cut-off Saw o
Flying objects – from the cutting process. o
Cuts/lacerations – from sharp edges on the cut metal. o
Entanglement – hair or clothing caught in rotating parts. •
Hydraulic Press o
Flying objects – from misaligned "jobs" on the press bed. o
Hydraulic injection injury – from poorly maintained hydraulic hoses and fittings. o
Structural failure – no Safe Working Load has been established for the press. The potentially serious nature of injuries, which may occur as a result of these risks requires immediate attention. I would appreciate your support and agreement that we can take required action as detailed in the recommendations from the WHS department. Regards, WHS Advisor
Your preview ends here
Eager to read complete document? Join bartleby learn and gain access to the full version
- Access to all documents
- Unlimited textbook solutions
- 24/7 expert homework help
Document title: BSBWHS518_AG_SW_1of1 Page 13 of 25 Resource ID: TBS_20_003_BSBWHS518_AG_SW_1of1 © TAFE NSW 2020 Activity 2.3: Identify how to record and report on WHS risk assessment Referring back to Activity 2.1: Identify how to access sources of information, data and advice and Activity 2.2: Identify how to consult with others to inform WHS risk assessment
, create a brief report that identifies the following: •
your three hazards and the information you found out •
the outcomes of your consultation on the hazards, risks and impacts. •
This should be no more than one A4 page in length. You may research a suitable template that can be modified or create your own using MS Word or similar program and attach to this workbook referencing the activity number in the file name. Feedback
Plant – Risk and control A recent workplace inspection uncovered a number of concerns associated with items of plant in the workshop. While there is a lot that is being done well, there is a real risk of serious injury associated with the use of the cut-off saw and the hydraulic press. It is considered that the following three risks are more serious and require more urgent attention: •
flying objects from the press •
flying objects from the saw •
entanglement in the saw's rotating components. A series of toolbox talks and safe behaviour observations were undertaken to ensure sufficient consultation took place with workers who have experience using the equipment. This consultation uncovered a number of near-miss incidents and minor injuries went unreported over the past 12 months. This new information highlights the seriousness of the risk and uncovered a culture of non-
reporting. More information is available from the following sources: •
Code of Practice – Managing the risks of plant in the workplace •
NOHSC – National Standard for Plant (1994) •
Australian Standard 4024 – Safety of Machinery •
SafeWork NSW – Hazard Library Further work is required to ensure the safety of workers who are using this plant. Following consultation with workers, there are now other issues which need to be added to the scope of this project.
Document title: BSBWHS518_AG_SW_1of1 Page 14 of 25 Resource ID: TBS_20_003_BSBWHS518_AG_SW_1of1 © TAFE NSW 2020 Feedback: Topic 3 Activity 3.1: Identify how to access sources of information, data Following on from Activity 2.3: Identify how to record and report on WHS risk assessment;
concerning the three plant hazards, access health and safety information, data and/or advice from reputable sources for preliminary research on the development of risk controls. Prepare notes or collect the information you find, as preparation for Activity 3.2: Identify how to develop risk controls.
Feedback
You must access information data or advice in relation to health and safety for developing risk controls for your three identified hazards. You should note down or attach what they find, and this should be from authoritative sources, such as WHS/OHS regulators, local government and WHS experts. Information may relate to WHS management of hazards, risk controls or plant-specific information.
Activity 3.2: Identify how to develop risk controls Following on from Activity 3.1: Identify how to access sources of information, data;
for your three hazards, use the hierarchy of risk control measures (identified in section Develop risk controls
of the unit) to develop risk controls that eliminate or manage the risks. Record what these are and how you would implement them in the workplace. Feedback
You must refer to the hierarchy of risk controls found in section 3.2 of the learning unit; you may also refer to Safe Work Australia or your own WHS/OHS regulator for this information. The hierarchy of risk control measures from Safe Work Australia: •
Level one – eliminate the hazard. •
Level two – substitute the hazard for something safer, isolate the hazard or reduce risks through engineering controls. •
Level three – reduce exposure to the hazard using administrative actions, or use personal protective equipment (PPE). Risk controls for the plant include: •
machine guards
Document title: BSBWHS518_AG_SW_1of1 Page 15 of 25 Resource ID: TBS_20_003_BSBWHS518_AG_SW_1of1 © TAFE NSW 2020 •
access and egress •
barriers and signs •
emergency stops and warning devices •
supervision and training •
improved work procedures for plant. Implementation may refer to producing schedules, prioritising risk controls, and how to carry out activities. A systematic approach should be used to ensure consistent and safe standards of risk control management. Activity 3.3: Forum: Identify how to consult with internal and specialist personnel 1.
Go to the Forum page and post the risk controls you have identified together with details on how you plan to implement them. •
Post your response in the 'Identify how to consult with internal and specialist personnel' forum. •
After you have posted your response, review the replies of other students and comment where applicable. Feedback
You must post your answers in the forum, review the replies of other students and, where appropriate, provide feedback on others' responses. Posts will include details of controls devised in Activity 3.2. 2.
Following your consultation with other forum members in question one, prepare a brief report (1 x A4 page) to report the outcomes of the consultation. For this activity, you may use a suitable template, create your own using MS Word or similar and attach a copy to this workbook activity number. Feedback
Student feedback will vary based on previous activities. The following controls have been proposed following consultation with workers on the three more serious risks associated with the operation of the cut-off saw and the hydraulic press. Flying objects from the cut-off saw •
Proposed controls – cut-off saw:
Your preview ends here
Eager to read complete document? Join bartleby learn and gain access to the full version
- Access to all documents
- Unlimited textbook solutions
- 24/7 expert homework help
Document title: BSBWHS518_AG_SW_1of1 Page 16 of 25 Resource ID: TBS_20_003_BSBWHS518_AG_SW_1of1 © TAFE NSW 2020 o
Installation of additional guarding between the saw table and the operator's position o
Requirement for operators to wear safety glasses and a face shield o
Requirement for operators to have long hair tied back o
Installation of footswitch to keep operators a safe distance from the saw while operating o
Requirement for operators to wear a leather apron while operating the saw o
Review of SOP and additional training for all operators. Flying objects from the hydraulic press •
Proposed controls – hydraulic press o
Install mesh guarding around the press o
Purchase and installation of additional equipment to enable the job to be set-up in the press and the operator to stand outside the cage. •
The controls will be scheduled for review at every operation in the first week, followed by monthly review thereafter. It is anticipated that modification or adjustment to the location of the footswitch will be required. It is also anticipated that a level of objection will be seen regarding the use of the cage around the press. Activity 3.4: Identify how to communicate rights, obligations and duties of workplace personnel Your manager has requested that you address with your team the rights, obligations and duties of workplace personnel for the identified hazards and risk controls from Activity 3.2: Identify how to develop risk controls.
You have decided to address this in the next toolbox talk meeting. In preparation, you will prepare a handout that will be provided to each member. The staff handout needs to conform to the organisation's style guidelines as this will also be filed with the toolbox talk briefing notes for company records. As a minimum your supporting staff handout must include: •
date of discussion •
key points to be covered o
stakeholders o
the rights, obligations and duties of workplace personnel for the identified hazards and risk controls •
how you will accommodate any feedback
Document title: BSBWHS518_AG_SW_1of1 Page 17 of 25 Resource ID: TBS_20_003_BSBWHS518_AG_SW_1of1 © TAFE NSW 2020 •
reminder to staff to acknowledge receipt of the handout in the toolbox talk briefing document. For this activity, you may use a suitable template, create your own using MS Word or similar and attach a copy to this workbook referencing the activity number. Feedback
Your responses will vary depending on the template used. Content of the prepared document must include the points above. For example: Toolbox Talk 27/11/2020 Topic The main topic for today's toolbox talk is risk associated with plant Background Workplace inspection carried out, identified risk associated with the use of a number of items of plant. Risks included flying objects from the saw, flying objects from the press and risk of entanglement in the rotating saw blade Stakeholders Any person who uses these items of plant is at risk of injury. This includes regular workers in the workshop and contractors who may use it from time to time. Obligations of workers As everyone already knows, you have the right to work in a safe workplace. This right comes with an obligation to work within the direction given by the PCBU, including policy and procedure and verbal instruction. The existing policies and procedures in place for the operation of plant in the workshop will be reviewed and refresher training provided. Additional PPE will be available. Additional guarding will be installed over the coming week. Feedback Ongoing monitoring of the identified risks will be carried out by the WHS team, though your ongoing feedback and support is appreciated. If you have concerns, they can be passed on through your supervisor, or the WHS team. Reminder Don't forget to sign the attendance sheet for this Toolbox Talk.
Document title: BSBWHS518_AG_SW_1of1 Page 18 of 25 Resource ID: TBS_20_003_BSBWHS518_AG_SW_1of1 © TAFE NSW 2020 Activity 3.5: Identify how to monitor the effectiveness of implemented risk controls 1.
What activities can you do to monitor risk controls? Feedback
•
Monitoring risk controls can take many forms. It can include inspection of a work area, an audit of compliance with procedures, review of incident data over a period following control, consultation with workers. •
Monitoring must consider whether the control has achieved the intended result. In some cases, the desired outcome, or what we want to achieve, does not actually occur. In some cases, we actually even create additional issues. This is particularly relevant where engineering controls are put in place, and other impacts occur. 2.
How should you review and evaluate the effectiveness of risk controls? (Answers to be no more than 100 words). Feedback
Monitoring activities will depend on the nature of the risk. It may include observation, review of procedures and risk assessments, discussion with operators or even a combination of those. Examples might include: •
Control – Install guarding around plant o
Review – observe the operation of the plant to see if the guard allows the worker to operate the plant safely if the guard is being used as intended if the guard creates additional problems or risk for the operator. •
Control – updated safe work procedure o
Review – observe a worker doing the job covered by the procedure and compare the steps int eh procedure compared to actual steps. Uncover differences and discuss them with the operator to uncover issues.
Your preview ends here
Eager to read complete document? Join bartleby learn and gain access to the full version
- Access to all documents
- Unlimited textbook solutions
- 24/7 expert homework help
Document title: BSBWHS518_AG_SW_1of1 Page 19 of 25 Resource ID: TBS_20_003_BSBWHS518_AG_SW_1of1 © TAFE NSW 2020 Activity 3.6: Identify how to record and report on implemented risk controls Refer to Case study: Implemented risk controls
. Create a short report (1 x A4 page) that identifies the progress of the implemented risk controls for Organisation ABC. For this activity, you may use a suitable template, create your own using MS Word or similar and attach a copy to this workbook referencing the activity number. Feedback
Answers may vary in wording, but must identify the following information: •
Plant training has been given to all workers; however, maintenance training has only been provided to three workers, and this can hold up work production when their assistance is required. •
Sound-proof guarding is removed when maintenance and cleaning occur; this is not always put back in place, causing noise hazards. Reports must be written objectively (without bias or personal opinion). Case study: Implemented risk controls Organisation ABC has been working with a new manufacturing plant for three months; an initial hazard and risk assessment was carried out when the plant was installed and made ready for workers to use. The manager must now check on the implemented risk controls to see how these are working. The following information has been gained: • Plant training:
Workers have been trained to operate the plant according to their job roles and to use personal protective equipment; three appointed workers have been trained to perform maintenance duties. • Maintenance and cleaning of plant:
All workers have been given instructions for regular cleaning of plant that they use; when maintenance is required, they must seek one of the workers trained to carry out maintenance tasks. This can sometimes hold-up work production if any of the workers are absent or unable to attend immediately. • Specific control measures:
The plant requires guards to minimise the noise that is emitted from certain functions; these are removable barriers which allow access into a plant for maintenance and cleaning. It has been noted that on several occasions, the guarding has not been put back in place, and the plant has been operated in this condition for one or more days.
Document title: BSBWHS518_AG_SW_1of1 Page 20 of 25 Resource ID: TBS_20_003_BSBWHS518_AG_SW_1of1 © TAFE NSW 2020 Feedback: Topic 4 Activity 4.1: Identify types of plant requiring registration and tasks requiring operator licensing 1.
Provide three examples of plant requiring registration. Feedback
Answers may vary but must identify three examples of plant requiring registration; this may include: •
pressure equipment •
gas cylinders •
tower cranes •
mobile cranes with a rated capacity greater than 10 tonnes •
lifts, escalators and moving walkways •
prefabricated scaffolding •
vehicle hoists •
some amusement devices •
building maintenance units •
concrete placing booms. 2.
According to work health and safety, list three tasks that require operator licensing and/or certification in relation to one or two pieces of plant. You may need to perform research to answer this question. Feedback
Answers will vary depending on your choice of plant. For example, tasks relating to a tower crane may include: •
dismantling and assembling the crane •
climbing to a significant height for operating the crane •
lifting and controlling loads at height •
lifting and controlling moving loads •
operating the crane remotely.
Document title: BSBWHS518_AG_SW_1of1 Page 21 of 25 Resource ID: TBS_20_003_BSBWHS518_AG_SW_1of1 © TAFE NSW 2020 Activity 4.2: Identify how to document registration, licensing and certification requirements Choose an item of plant and, record the registration, licensing and certification requirements for the item of plant chosen. Feedback
You must identify the relevant details as provided in the information given to them. This will include the: •
item of plant •
registration requirements •
licence required for worker operation •
certification/training requirements. Activity 4.3: Identify how to monitor and report compliance with WHS regulatory requirements 1.
Explain how you will need to monitor compliance with WHS regulatory requirements for registration, licensing and certification. Feedback
Answers to include the following points: •
You will need to check on organisational plant registration and records, and employee licensing and certification records to ensure these are current to organisational operations. •
You will need to monitor employee or plant changes to ensure records are kept up-to-date, and registration, licensing or certification requirements are maintained. 2.
To report and communicate the plant registration, licensing and certification requirements from Activity 4.2: Identify how to document registration, licensing and certification requirements,
create a simple one page (one side of A4) fact sheet. For this activity, you may use a suitable template, create your own using MS Word or similar and attach a copy to this workbook referencing the activity number.
Your preview ends here
Eager to read complete document? Join bartleby learn and gain access to the full version
- Access to all documents
- Unlimited textbook solutions
- 24/7 expert homework help
Document title: BSBWHS518_AG_SW_1of1 Page 22 of 25 Resource ID: TBS_20_003_BSBWHS518_AG_SW_1of1 © TAFE NSW 2020 Feedback
You must create and attach a fact sheet that explains the registration, licensing and certification requirements of the item of plant from Activity 4.2. This must be clear and logical in format and content, and be legible to read. The fact sheet must provide accurate details, as sourced from your original information. For example: Vehicle Hoist Registration Design The initial design of the vehicle hoist must be registered with the relevant State/Territory regulator. The owner of a vehicle hoist must ensure that its design has been registered – usually indicated by the installation of a placard on the hoist. Item Not required in NSW Licencing Not applicable Certification Regular inspection by a competent person is required to ensure the vehicle hoist remains fit for purpose (as per AS2550)
Your preview ends here
Eager to read complete document? Join bartleby learn and gain access to the full version
- Access to all documents
- Unlimited textbook solutions
- 24/7 expert homework help
Document title: BSBWHS518_AG_SW_1of1 Page 23 of 25 Resource ID: TBS_20_003_BSBWHS518_AG_SW_1of1 © TAFE NSW 2020 Feedback: Topic 5 Activity 5.1: Identify WHS-related training needs and identify skill gaps 1.
For one item of plant that is used in your business industry, research and identify the WHS training requirements for using this and the applicable registration, licensing and certification requirements. Feedback
Answers will vary; however, you must identify the training requirements for your item of plant along with the registration, licensing and certification needs. For example: Forklift: •
Forklifts are used in a wide variety of workplaces and remain one of the major sources of workplace injury. WHS Legislation requires that any person who is required to drive a forklift must hold a High-Risk Licence of the appropriate class (LF or LO). •
Forklift licences are nationally recognised and last for 5 years. •
Forklift licence training is carried out by a registered training organisation. 2.
With reference to question one, identify a comparable item of plant, for example, a higher-grade model or a different manufacturer's model, and determine any skills gaps and training needs that may apply. Provide a short summary report to record these needs. Feedback
Answers will vary; you must identify any skills gaps or training requirements from comparing the second item of plant against that detailed in your answer to question one. Responses will typically include a reference to improvements in technology or the incorporation of computerisation in some plant. For example: At my workplace, the forklift in operation was very old. It had a gas-powered engine with the heavy cylinder on the back above the counterweight. The seat was torn and loos in its mounts, and there was no seatbelt. The forks lifted up and down, and the mast had some capacity to tile back and forward.
Your preview ends here
Eager to read complete document? Join bartleby learn and gain access to the full version
- Access to all documents
- Unlimited textbook solutions
- 24/7 expert homework help
Document title: BSBWHS518_AG_SW_1of1 Page 24 of 25 Resource ID: TBS_20_003_BSBWHS518_AG_SW_1of1 © TAFE NSW 2020 The replacement forklift is diesel-powered which meant different refuelling procedures. It is fitted with a seatbelt which locks out the ignition, preventing it from starting unless the operator has the seatbelt connected. The forks go up and down, and the mast tilts back and forward, though both movements are considerably faster than on the old forklift. The forks also move sideways on the headboard to allow easier and more accurate placement of pallets. The new features of the forklift presented as gaps in existing worker knowledge and required retraining. Licences were still valid, though the specific operational aspects of the new forklift needed to be highlighted and workers trained. Activity 5.2: Identify how to ensure training is undertaken and completed 1.
How can you make sure that training related to plant is carried out? Feedback
Your responses could include: •
You should plan training, making sure you prioritise needs (training should support workers' needs and work production). •
You should request and obtain a training budget (training must be affordable and agreed with management). •
Organise and agree on training schedules (this must be communicated to all parties). •
Prepare for training (such as providing training details and arrangements, producing itineraries and training materials, and liaising with trainers). 2.
From your own thinking, suggest three ways you can maintain training records to meet WHS and organisational requirements. Feedback
Answers may vary but must suggest three suitable ways to maintain training records; this may include: •
applying data protection and security to protect workers' personal details •
using a logical storing/filing system, so records are easily identifiable •
using a consistent format to record information in training records •
retaining records for the required period of time (for example, five or seven years).
Your preview ends here
Eager to read complete document? Join bartleby learn and gain access to the full version
- Access to all documents
- Unlimited textbook solutions
- 24/7 expert homework help
Document title: BSBWHS518_AG_SW_1of1 Page 25 of 25 Resource ID: TBS_20_003_BSBWHS518_AG_SW_1of1 © TAFE NSW 2020 Image attributions Image
Page # Attribution
Cover 1 © Getty Images copied under licence Credit: WhataWin Creative #: 1185282377
Your preview ends here
Eager to read complete document? Join bartleby learn and gain access to the full version
- Access to all documents
- Unlimited textbook solutions
- 24/7 expert homework help
Related Documents
Related Questions
est 2 (copy) (page 4 of 9)
A wiseup.wsu.acza/mod/quiz/attempt.php7attempt=610918cmid 148960&page=3
ops
O YouTube
M Gmail
Maps
O GENERAL MATHEM.
O New Tab
:WSU WiSeUp
1 MONLO GOA
ashboard / My courses / FLM15B2_KF_WS6222 2021 / Tests / Test 2 (copy)
uestion 4
Quz navigation
Gate AB in Figure below is 1.0 m long and 0.9 wide. Calculate force F on the gate and position X of its centre of
Not yet
answered
pressure.
Marked out of
Finish attempt
10,000
Rag question
3m
Oil,
s.g.=Q81
7m
1.0m
B
50
Answer
arrow_forward
O Tran
Futu
Welc E UGA
М Аpl
Appl
G best
W Acac G most
G elec
t D (3) E
ge.com/course.html?courseld=16544025&OpenVellumHMAC=a6eb58a3f1225d08c58c45ba8177b613#10001
Maps D Web design tutori. A MATH180: HW08-.
Course Home
What is the angle of rope 3?
Express your answer to two significant figures and include the appropriate units.
HA
?
2
O = 38
Submit
Previous Answers Request Answer
2.0 kg
4.0 kg
MacBook Pro
F4
%23
&
3
4
5
7.
8.
%3D
{
E
R
T
Y
U
F
J
K
C
V
M
mand
option
command
arrow_forward
University Of Babylon
College of Mussayb
Automobile Production
Quiz(2) 2024-205
Question one: List and defining the parameters of a robot
Question Two List the functionalities of Robot
Question Three:
1. What is the key factor that determines the
feasibility of a robot's movements?
oa) Speed
ob) Stability
c) Both speed and stability
od) The type of control system used
2. What is the relationship between speed and
stability in robot movements?
oa) They are directly proportional
b) They are inversely proportional
c) They are independent of each other
od) There is no relationship between them
3. Which two disciplines are closely related to
robot movements?
oa) Robotics and Mechanical Engineering
o b) Robotics and Control
c) Control and Computer Science
od) Mechanical Engineering and Computer
Science
4. Why is a powerful control system crucial for
robots?
0 a) To increase the robot's speed
ob) To improve the robot's stability
o c) To maintain a balance between speed
and stability
od) To…
arrow_forward
00
T
R
%24
Bb R
V qa
du/webapps/assessment/take/launch.jsp?course_assessment_id%=_254968_1&course_id%3D 3565256_1&content id= 52826
* Question Completion Status:
Attach File
Browse Local Files
Browse Content Collection
QUESTION 2
A company needs to choose one supplier for a particular type of silicon wafer used'in the production of
semiconductors. The company has three options. Supplier A sells the silicon wafers for $2.50 per wafer,
independently of the number of wafers ordered. Supplier B sells the wafers for $2.40 each but does not
consider an order for less than 2,000 wafers. Supplier C sells the wafers for $2.30 each but does not accept
an order for less than 3,000 wafers. Assume an order setup cost of $100 and an annual requirement of 20,000
wafers. Assume a 20% annual interest rate for holding cost calculations.
a. Which supplier should be chosen to minimize the total annual cost for the wafers, and what is the
optimal order quantity?
b. If the replenishment lead time for wafers…
arrow_forward
Q1 please
arrow_forward
Needs Complete typed solution with complete explanation and 100 % accuracy. Don't use chat gpt or any ai
arrow_forward
Can anyone help me with these questions please
arrow_forward
Task 1
You are employed as a mechanical engineer within an unnamed research center, specializing in the
development of innovative air conditioning systems. Your division is tasked with providing computer-based
modeling and design solutions using computational fluid dynamics through ANSYS software. Your primary
responsibilities involve the analysis of horizontal channel dynamics to meet specific criteria. Under the
guidance of your immediate supervisor, you have been assigned unique responsibilities within an ongoing
project. As a member of the research team, your role includes constructing an appropriate model and
executing a sequence of simulation iterations to explore and enhance channel performance. Figure 1
provides a visualization of the horizontal channel under consideration. Consider 2D, incompressible, steady
flow in a horizontal channel at a Reynolds number of 150. The schematic below illustrates the channel flow,
not drawn to scale. For simplicity, neglect gravity. The…
arrow_forward
Subject: Air Pollution Formation and Control
Do not just copy and paster other online answers
arrow_forward
A Team of Engineers asked for an internal combustion engine to use it in a designed car. Your role is to describe the operation sequence of different types of available engines, explain their mechanical efficiency, and deliver a detailed technical report to show your approach in solving and discussing the following tasks and issues.
You must follow the following steps to help the team:
STEP 1
Describe the operational sequence of four-stroke spark ignition and four-stroke compression ignition engines with the aid of sketches by constructing simple sketch representing the operation and plotting the P-V diagrams for each process during the cycle to show the following:
The input and output heat and net output work
The expansion and compression strokes
The air-fuel mixture intake and exhaust gasses
The spark plug when it is in the active mode
The complete cycle of ideal Otto and Diesel cycles that shows the input and output heat and net output work.
STEP 2
Explain the mechanical…
arrow_forward
this is a practice problem, not a graded assignment
arrow_forward
You are assigned as the head of the engineering team to work on selecting the right-sized blower that will go on your new line of hybrid vehicles.The fan circulates the warm air on the inside of the windshield to stop condensation of water vapor and allow for maximum visibility during wintertime (see images). You have been provided with some info. and are asked to pick from the bottom table, the right model number(s) that will satisfy the requirement. Your car is equipped with a fan blower setting that allow you to choose between speeds 0, 1,2 and 3. Variation of the convection heat transfer coefficient is dependent upon multiple factors, including the size and the blower configuration.You can only use the following parameters:
arrow_forward
SEE MORE QUESTIONS
Recommended textbooks for you
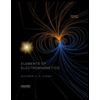
Elements Of Electromagnetics
Mechanical Engineering
ISBN:9780190698614
Author:Sadiku, Matthew N. O.
Publisher:Oxford University Press
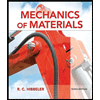
Mechanics of Materials (10th Edition)
Mechanical Engineering
ISBN:9780134319650
Author:Russell C. Hibbeler
Publisher:PEARSON
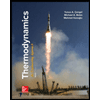
Thermodynamics: An Engineering Approach
Mechanical Engineering
ISBN:9781259822674
Author:Yunus A. Cengel Dr., Michael A. Boles
Publisher:McGraw-Hill Education
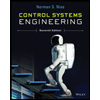
Control Systems Engineering
Mechanical Engineering
ISBN:9781118170519
Author:Norman S. Nise
Publisher:WILEY
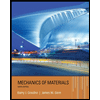
Mechanics of Materials (MindTap Course List)
Mechanical Engineering
ISBN:9781337093347
Author:Barry J. Goodno, James M. Gere
Publisher:Cengage Learning
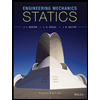
Engineering Mechanics: Statics
Mechanical Engineering
ISBN:9781118807330
Author:James L. Meriam, L. G. Kraige, J. N. Bolton
Publisher:WILEY
Related Questions
- est 2 (copy) (page 4 of 9) A wiseup.wsu.acza/mod/quiz/attempt.php7attempt=610918cmid 148960&page=3 ops O YouTube M Gmail Maps O GENERAL MATHEM. O New Tab :WSU WiSeUp 1 MONLO GOA ashboard / My courses / FLM15B2_KF_WS6222 2021 / Tests / Test 2 (copy) uestion 4 Quz navigation Gate AB in Figure below is 1.0 m long and 0.9 wide. Calculate force F on the gate and position X of its centre of Not yet answered pressure. Marked out of Finish attempt 10,000 Rag question 3m Oil, s.g.=Q81 7m 1.0m B 50 Answerarrow_forwardO Tran Futu Welc E UGA М Аpl Appl G best W Acac G most G elec t D (3) E ge.com/course.html?courseld=16544025&OpenVellumHMAC=a6eb58a3f1225d08c58c45ba8177b613#10001 Maps D Web design tutori. A MATH180: HW08-. Course Home What is the angle of rope 3? Express your answer to two significant figures and include the appropriate units. HA ? 2 O = 38 Submit Previous Answers Request Answer 2.0 kg 4.0 kg MacBook Pro F4 %23 & 3 4 5 7. 8. %3D { E R T Y U F J K C V M mand option commandarrow_forwardUniversity Of Babylon College of Mussayb Automobile Production Quiz(2) 2024-205 Question one: List and defining the parameters of a robot Question Two List the functionalities of Robot Question Three: 1. What is the key factor that determines the feasibility of a robot's movements? oa) Speed ob) Stability c) Both speed and stability od) The type of control system used 2. What is the relationship between speed and stability in robot movements? oa) They are directly proportional b) They are inversely proportional c) They are independent of each other od) There is no relationship between them 3. Which two disciplines are closely related to robot movements? oa) Robotics and Mechanical Engineering o b) Robotics and Control c) Control and Computer Science od) Mechanical Engineering and Computer Science 4. Why is a powerful control system crucial for robots? 0 a) To increase the robot's speed ob) To improve the robot's stability o c) To maintain a balance between speed and stability od) To…arrow_forward
- 00 T R %24 Bb R V qa du/webapps/assessment/take/launch.jsp?course_assessment_id%=_254968_1&course_id%3D 3565256_1&content id= 52826 * Question Completion Status: Attach File Browse Local Files Browse Content Collection QUESTION 2 A company needs to choose one supplier for a particular type of silicon wafer used'in the production of semiconductors. The company has three options. Supplier A sells the silicon wafers for $2.50 per wafer, independently of the number of wafers ordered. Supplier B sells the wafers for $2.40 each but does not consider an order for less than 2,000 wafers. Supplier C sells the wafers for $2.30 each but does not accept an order for less than 3,000 wafers. Assume an order setup cost of $100 and an annual requirement of 20,000 wafers. Assume a 20% annual interest rate for holding cost calculations. a. Which supplier should be chosen to minimize the total annual cost for the wafers, and what is the optimal order quantity? b. If the replenishment lead time for wafers…arrow_forwardQ1 pleasearrow_forwardNeeds Complete typed solution with complete explanation and 100 % accuracy. Don't use chat gpt or any aiarrow_forward
- Can anyone help me with these questions pleasearrow_forwardTask 1 You are employed as a mechanical engineer within an unnamed research center, specializing in the development of innovative air conditioning systems. Your division is tasked with providing computer-based modeling and design solutions using computational fluid dynamics through ANSYS software. Your primary responsibilities involve the analysis of horizontal channel dynamics to meet specific criteria. Under the guidance of your immediate supervisor, you have been assigned unique responsibilities within an ongoing project. As a member of the research team, your role includes constructing an appropriate model and executing a sequence of simulation iterations to explore and enhance channel performance. Figure 1 provides a visualization of the horizontal channel under consideration. Consider 2D, incompressible, steady flow in a horizontal channel at a Reynolds number of 150. The schematic below illustrates the channel flow, not drawn to scale. For simplicity, neglect gravity. The…arrow_forwardSubject: Air Pollution Formation and Control Do not just copy and paster other online answersarrow_forward
- A Team of Engineers asked for an internal combustion engine to use it in a designed car. Your role is to describe the operation sequence of different types of available engines, explain their mechanical efficiency, and deliver a detailed technical report to show your approach in solving and discussing the following tasks and issues. You must follow the following steps to help the team: STEP 1 Describe the operational sequence of four-stroke spark ignition and four-stroke compression ignition engines with the aid of sketches by constructing simple sketch representing the operation and plotting the P-V diagrams for each process during the cycle to show the following: The input and output heat and net output work The expansion and compression strokes The air-fuel mixture intake and exhaust gasses The spark plug when it is in the active mode The complete cycle of ideal Otto and Diesel cycles that shows the input and output heat and net output work. STEP 2 Explain the mechanical…arrow_forwardthis is a practice problem, not a graded assignmentarrow_forwardYou are assigned as the head of the engineering team to work on selecting the right-sized blower that will go on your new line of hybrid vehicles.The fan circulates the warm air on the inside of the windshield to stop condensation of water vapor and allow for maximum visibility during wintertime (see images). You have been provided with some info. and are asked to pick from the bottom table, the right model number(s) that will satisfy the requirement. Your car is equipped with a fan blower setting that allow you to choose between speeds 0, 1,2 and 3. Variation of the convection heat transfer coefficient is dependent upon multiple factors, including the size and the blower configuration.You can only use the following parameters:arrow_forward
arrow_back_ios
arrow_forward_ios
Recommended textbooks for you
- Elements Of ElectromagneticsMechanical EngineeringISBN:9780190698614Author:Sadiku, Matthew N. O.Publisher:Oxford University PressMechanics of Materials (10th Edition)Mechanical EngineeringISBN:9780134319650Author:Russell C. HibbelerPublisher:PEARSONThermodynamics: An Engineering ApproachMechanical EngineeringISBN:9781259822674Author:Yunus A. Cengel Dr., Michael A. BolesPublisher:McGraw-Hill Education
- Control Systems EngineeringMechanical EngineeringISBN:9781118170519Author:Norman S. NisePublisher:WILEYMechanics of Materials (MindTap Course List)Mechanical EngineeringISBN:9781337093347Author:Barry J. Goodno, James M. GerePublisher:Cengage LearningEngineering Mechanics: StaticsMechanical EngineeringISBN:9781118807330Author:James L. Meriam, L. G. Kraige, J. N. BoltonPublisher:WILEY
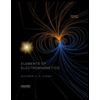
Elements Of Electromagnetics
Mechanical Engineering
ISBN:9780190698614
Author:Sadiku, Matthew N. O.
Publisher:Oxford University Press
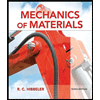
Mechanics of Materials (10th Edition)
Mechanical Engineering
ISBN:9780134319650
Author:Russell C. Hibbeler
Publisher:PEARSON
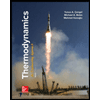
Thermodynamics: An Engineering Approach
Mechanical Engineering
ISBN:9781259822674
Author:Yunus A. Cengel Dr., Michael A. Boles
Publisher:McGraw-Hill Education
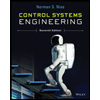
Control Systems Engineering
Mechanical Engineering
ISBN:9781118170519
Author:Norman S. Nise
Publisher:WILEY
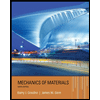
Mechanics of Materials (MindTap Course List)
Mechanical Engineering
ISBN:9781337093347
Author:Barry J. Goodno, James M. Gere
Publisher:Cengage Learning
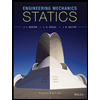
Engineering Mechanics: Statics
Mechanical Engineering
ISBN:9781118807330
Author:James L. Meriam, L. G. Kraige, J. N. Bolton
Publisher:WILEY