Concept explainers
A.
Compute the single plant-wide
A.

Explanation of Solution
Single plant-wide factory overhead rate: The rate at which the factory or manufacturing overheads are allocated to products is referred to as single plant-wide factory overhead rate.
Formula to compute single plant-wide overhead rate:
Activity-based costing (ABC) method: The costing method which allocates overheads to the products based on factory overhead rate for each activity or cost object, according to the cost pooled for the cost drivers (allocation base).
Formula to compute activity-based overhead rate:
Complete the blanks for Column A, B, and C.
Product Volume Class |
Column A (Single Rate Overhead Allocation Per Unit) (1) | Column B (ABC Overhead Allocation Per Unit) (2) | Column C (Percent Change in Allocation) (3) |
Low | $30.00 | $58.06 | |
Medium | 30.00 | 29.31 | |
High | 30.00 | 25.46 |
Table (1)
Working Note (1):
Compute factory overhead allocated per unit of each product, using single machine rate of $200 per machine hour (MH) (Column A).
Product Volume Class | Single Plant-Wide Overhead Rate | × | Total Number of MH | = | Total Factory Overhead | ÷ | Number of Units | = | Factory Overhead Per Unit |
Low | $200 | × | 24 MH | = | $4,800 | ÷ | 160 | = | $30.00 |
Medium | $200 | × | 225 MH | = | 45,000 | ÷ | 1,500 | = | $30.00 |
High | $200 | × | 900 MH | = | 180,000 | ÷ | 6,000 | = | $30 .00 |
Table (2)
Working Note (2):
Compute ABC factory overhead allocated per unit of each product (Column B).
Step 1: Compute activity cost allocated per unit of low volume refrigerators.
Activity | Activity-Based Overhead Rates | × | Actual Use of Activity-Base | = | Activity Cost |
Machining | $160 per MH | × | 24 MH | = | $3,840 |
Setup | $240 per setup | × | 14 setups | = | 3,360 |
Sales order processing | $55 per sales order | × | 38 orders | = | 2,090 |
Total activity costs allocated to low volume refrigerators | $9,290 | ||||
Number of units of low volume refrigerators | ÷160 units | ||||
Activity-based overhead cost per unit of low volume refrigerator | $58.06 |
Table (3)
Step 2: Compute activity cost allocated per unit of medium volume refrigerators.
Activity | Activity-Based Overhead Rates | × | Actual Use of Activity-Base | = | Activity Cost Allocated |
Machining | $160 per MH | × | 225 MH | = | $36,000 |
Setup | $240 per setup | × | 13 setups | = | 3,120 |
Sales order processing | $55 per sales order | × | 88 orders | = | 4,840 |
Total activity costs allocated to medium volume refrigerators | $43,960 | ||||
Number of units of medium volume refrigerators | ÷1,500 units | ||||
Activity-based overhead cost per unit of refrigerator | $29.31 |
Table (4)
Step 3: Compute activity cost allocated per unit of high volume refrigerators.
Activity | Activity-Based Overhead Rates | × | Actual Use of Activity-Base | = | Activity Cost Allocated |
Machining | $160 per MH | × | 900 MH | = | $144,000 |
Setup | $240 per setup | × | 9 setups | = | 2,160 |
Sales order processing | $55 per sales order | × | 120 orders | = | 6,600 |
Total activity costs allocated to high volume refrigerators | $152,760 | ||||
Number of units of high volume refrigerators | ÷6,000 units | ||||
Activity-based overhead cost per unit of refrigerator | $25.46 |
Table (5)
Working Note (3):
Compute the percent change in the allocation (Column C).
Product Volume Class | Column B (ABC Overhead Allocation Per Unit) | ˗ |
Column A (Single Rate Overhead Allocation Per Unit) | ÷ |
Column A (Single Rate Overhead Allocation Per Unit) | = | Percent Change in Allocation |
Low | $58.06 | ˗ | $30.00 | ÷ | $30.00 | = | 93.53% |
Medium | 29.31 | ˗ | 30.00 | ÷ | 30.00 | = | (2.3)% |
High | 25.46 | ˗ | 30.00 | ÷ | 30.00 | = | (15.1)% |
Table (6)
Note: refer to Tables (2), (3), (4), and (5) for value and computation of Column A and Column B values.
B.
Discuss the reasons for the difference in machine rate under single plant-wide approach and ABC approach.
B.

Explanation of Solution
The machine hour rate under ABC, $160 per machine hour, as computed in Part (1), is different from the $200 single machine rate under single plant-wide approach. This is because the ABC method allocates all the overheads based on the activities under production. So, setup and sales order processing activities are allocated their share in factory overheads.
C.
Discuss the percent change in allocation (Column C).
C.

Explanation of Solution
As per the ABC method, low volume refrigerator has high activity cost per unit comparatively. This is because this product consumes high overheads for the setup activity with highest cost. The company could reduce the cost of setup activity.
Want to see more full solutions like this?
Chapter 4 Solutions
Managerial Accounting
- Patterson Company produces wafers for integrated circuits. Data for the most recent year are provided: aCalculated using number of dies as the single unit-level driver. bCalculated by multiplying the consumption ratio of each product by the cost of each activity. Required: 1. Using the five most expensive activities, calculate the overhead cost assigned to each product. Assume that the costs of the other activities are assigned in proportion to the cost of the five activities. 2. Calculate the error relative to the fully specified ABC product cost and comment on the outcome. 3. What if activities 1, 2, 5, and 8 each had a cost of 650,000 and the remaining activities had a cost of 50,000? Calculate the cost assigned to Wafer A by a fully specified ABC system and then by an approximately relevant ABC approach. Comment on the implications for the approximately relevant approach.arrow_forwardLarsen, Inc., produces two types of electronic parts and has provided the following data: There are four activities: machining, setting up, testing, and purchasing. Required: 1. Calculate the activity consumption ratios for each product. 2. Calculate the consumption ratios for the plantwide rate (direct labor hours). When compared with the activity ratios, what can you say about the relative accuracy of a plantwide rate? Which product is undercosted? 3. What if the machine hours were used for the plantwide rate? Would this remove the cost distortion of a plantwide rate?arrow_forwardSilven Company has identified the following overhead activities, costs, and activity drivers for the coming year: Silven produces two models of cell phones with the following expected activity demands: 1. Determine the total overhead assigned to each product using the four activity drivers. 2. Determine the total overhead assigned to each model using the two most expensive activities. The costs of the two relatively inexpensive activities are allocated to the two expensive activities in proportion to their costs. 3. Using ABC as the benchmark, calculate the percentage error and comment on the accuracy of the reduced system. Explain why this approach may be desirable.arrow_forward
- Evans, Inc., has a unit-based costing system. Evanss Miami plant produces 10 different electronic products. The demand for each product is about the same. Although they differ in complexity, each product uses about the same labor time and materials. The plant has used direct labor hours for years to assign overhead to products. To help design engineers understand the assumed cost relationships, the Cost Accounting Department developed the following cost equation. (The equation describes the relationship between total manufacturing costs and direct labor hours; the equation is supported by a coefficient of determination of 60 percent.) Y=5,000,000+30X,whereX=directlaborhours The variable rate of 30 is broken down as follows: Because of competitive pressures, product engineering was given the charge to redesign products to reduce the total cost of manufacturing. Using the above cost relationships, product engineering adopted the strategy of redesigning to reduce direct labor content. As each design was completed, an engineering change order was cut, triggering a series of events such as design approval, vendor selection, bill of materials update, redrawing of schematic, test runs, changes in setup procedures, development of new inspection procedures, and so on. After one year of design changes, the normal volume of direct labor was reduced from 250,000 hours to 200,000 hours, with the same number of products being produced. Although each product differs in its labor content, the redesign efforts reduced the labor content for all products. On average, the labor content per unit of product dropped from 1.25 hours per unit to one hour per unit. Fixed overhead, however, increased from 5,000,000 to 6,600,000 per year. Suppose that a consultant was hired to explain the increase in fixed overhead costs. The consultants study revealed that the 30 per hour rate captured the unit-level variable costs; however, the cost behavior of other activities was quite different. For example, setting up equipment is a step-fixed cost, where each step is 2,000 setup hours, costing 90,000. The study also revealed that the cost of receiving goods is a function of the number of different components. This activity has a variable cost of 2,000 per component type and a fixed cost that follows a step-cost pattern. The step is defined by 20 components with a cost of 50,000 per step. Assume also that the consultant indicated that the design adopted by the engineers increased the demand for setups from 20,000 setup hours to 40,000 setup hours and the number of different components from 100 to 250. The demand for other non-unit-level activities remained unchanged. The consultant also recommended that management take a look at a rejected design for its products. This rejected design increased direct labor content from 250,000 hours to 260,000 hours, decreased the demand for setups from 20,000 hours to 10,000 hours, and decreased the demand for purchasing from 100 component types to 75 component types, while the demand for all other activities remained unchanged. Required: 1. Using normal volume, compute the manufacturing cost per labor hour before the year of design changes. What is the cost per unit of an average product? 2. Using normal volume after the one year of design changes, compute the manufacturing cost per hour. What is the cost per unit of an average product? 3. Before considering the consultants study, what do you think is the most likely explanation for the failure of the design changes to reduce manufacturing costs? Now use the information from the consultants study to explain the increase in the average cost per unit of product. What changes would you suggest to improve Evanss efforts to reduce costs? 4. Explain why the consultant recommended a second look at a rejected design. Provide computational support. What does this tell you about the strategic importance of cost management?arrow_forwardThe management of Nova Industries Inc. manufactures gasoline and diesel engines through two production departments, Fabrication and Assembly. Management needs accurate product cost information in order to guide product strategy. Presently, the company uses a single plantwide factory overhead rate for allocating factory overhead to the two products. However, management is considering the multiple production department factory overhead rate method. The following factory overhead was budgeted for Nova: Direct labor hours were estimated as follows: In addition, the direct labor hours (dlh) used to produce a unit of each product in each department were determined from engineering records, as follows: a. Determine the per-unit factory overhead allocated to the gasoline and diesel engines under the single plantwide factory overhead rate method, using direct labor hours as the activity base. b. Determine the per-unit factory overhead allocated to the gasoline and diesel engines under the multiple production department factory overhead rate method, using direct labor hours as the activity base for each department. c. Recommend to management a product costing approach, based on your analyses in (a) and (b). Support your recommendation.arrow_forwardGeneva, Inc., makes two products, X and Y, that require allocation of indirect manufacturing costs. The following data were compiled by the accountants before making any allocations: The total cost of purchasing and receiving parts used in manufacturing is 60,000. The company uses a job-costing system with a single indirect cost rate. Under this system, allocated costs were 48,000 and 12,000 for X and Y, respectively. If an activity-based system is used, what would be the allocated costs for each product?arrow_forward
- Whirlpool Corporation (WHR) conducted an activity-based costing study of its Evansville, Indiana, plant in order to identify its most profitable products. Assume that we select three rep- resentative refrigerators (out of 333): one low-, one medium-, and one high-volume refrigerator. Additionally, we assume the following activity-base information for each of the three refrigerators: Number of Three Representative Refrigerators Number of Number of Number of Machine Hours Setups Sales Orders Units Refrigerator-Low Volume Refrigerator-Medium Volume Refrigerator-High Volume 24 14 38 160 225 13 88 1,500 900 9 120 6,000 Prior to conducting the study, the factory overhead allocation was based on a single machine hour rate. The machine hour rate was $200 per hour. After conducting the activity-based costing study, assume that three activities were used to allocate the factory overhead. The new activity rate infor- mation is assumed to be as follows: Sales Order Machining Activity Setup…arrow_forwardSingle plantwide rate and activity-based costing Whirlpool Corporation (WHR) conducted an activity-based costing study of its Evansville, Indiana, plant in order to identify its most profitable products. Assume that we select three representative refrigerators (out of 333): one low-, one medium-, and one high-volume refrigerator. Additionally, we assume the following activity-base information for each of the three refrigerators: Three Representative Refrigerators Refrigerator-Low Volume Refrigerator-Medium Volume Refrigerator-High Volume Activity rate Product Volume Class Low Number of Machine Hours Machining Activity Medium $160 High 24 225 900 Prior to conducting the study, the factory overhead allocation was based on a single machine hour rate. The machine hour rate was $200 per hour. After conducting the activity-based costing study, assume that three activities were used to allocate the factory overhead. The new activity rate information is assumed to be as follows: Setup Activity…arrow_forwardPlease answer asaparrow_forward
- Under an activity based costing system, what is the per-unit overhead cost of Zarrow_forwardUse this information for Miramar Industries to answer the question that follow.Miramar Industries manufactures two products: A and B. The manufacturing operation involves three overhead activities—production setup, materials handling, and general factory activities. Miramar uses activity-based costing to allocate overhead to products. An activity analysis of the overhead revealed the following estimated costs and activity bases for these activities: Activity Cost Activity Base Production setup $250,000 Number of setups Material handling 150,000 Number of parts General overhead 80,000 Number of direct labor hours Each product's total activity in each of the three areas are as follows: Product A Product B Number of setups 100 300 Number of parts 40,000 20,000 Number of direct labor hours 8,000 12,000 What is the overhead allocated to Product B using activity-based costing?arrow_forwardNorth Street Corporation manufactures two models of motorized go - carts, a standard and a deluxe model. The following activity and cost information has been compiled: Number of Number of Number of Product Setups Components Direct Labor Hours Standard 16 7 730 Deluxe 34 19 490 Overhead costs $16,000 $24,960 Number of setups and number of components are identified as activity - cost drivers for overhead. Assuming an activity - based costing system is used, what is the total amount of overhead cost assigned to the standard model? (Do not round interim calculations. Round the final answer to the nearest whole dollar.) O A. $17,600 O B. $11,840 OC. $29,120 O D. $20,480arrow_forward
- Managerial AccountingAccountingISBN:9781337912020Author:Carl Warren, Ph.d. Cma William B. TaylerPublisher:South-Western College PubFinancial And Managerial AccountingAccountingISBN:9781337902663Author:WARREN, Carl S.Publisher:Cengage Learning,Cornerstones of Cost Management (Cornerstones Ser...AccountingISBN:9781305970663Author:Don R. Hansen, Maryanne M. MowenPublisher:Cengage Learning
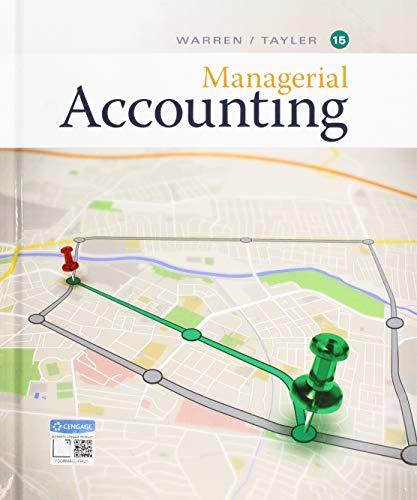
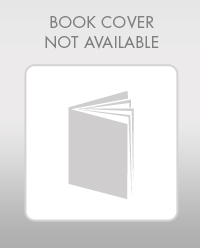
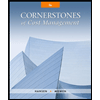