What is Process Costing?
Process costing is a sort of operation costing which is employed to determine the value of a product at each process or stage of producing process, applicable where goods produced from a series of continuous operations or procedure.
The prices are averaged over the units produced during the amount. Process costing is completely for companies manufacturing-related goods and where production is in repetitive inflow.
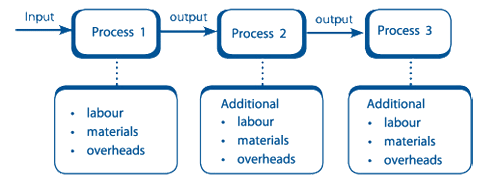
The method is used by taking the full expense of the process and averages it over the amount units in the production process.
Cost per unit = Cost of inputs / Expected output in units
Features of a Process Costing System
- Manufacturing costs such as materials, labor, and overheads are accumulated for an accounting period by the process.
- At the end of an accounting period, each process account is adjusted for normal losses and abnormal losses and gains.
- The unit expense is evaluated for every process by allocating the entire expenses allocated to the process for the time by the amounts of units made.
- When one production process is done the units and expenses relating to them are transferred to the next process account.
- After the end process is done, units are allocated to the completed goods inventory account.
Characteristics of Process Costing
- Production is continuous and separated into several processes.
- Costs are allocated to processes, e.g., the manufacture of a chemical might involve processes such as purification, cooling, etc.
- The finished product units are identical.
- The manufacturing procedure results in joint goods (numerous products) or byproducts.
Importance of Process Costing
Following is the importance of process costing-:
- The information about the costs is the first step in being able to control expenditure. A company needs to choose an appropriate type of costing system for its product type and industry.
- Any unit passes with several processes and the processes are simply distinguishable then the expense of the unit will be the expense of the process.
- Costing is commonly utilized in enterprises for example petroleum, chemicals, textiles, paper, food, banks, and soap.
Four basic steps in Accounting for Process Cost
- Summarize the process of physical units produced of product.
- Compute output in terms of equivalent units.
- Summarize total costs to account for and Compute equivalent unit costs.
- Allocate full expense/cost to units produced and to units in ending work in process inventory.
Types of Process Costing
- Weighted average cost—This process estimates that all expenses, whether from a preceding beginning of the recent one, are lumped jointly and allocated to units completed. It is the easiest process to calculate.
- Standard cost—The evaluation is identical to weighted average costing, but standard costs are allocated to production units, rather than real expenses; after full costs are accumulated depending on standard expenses, these totals are correlated to real accumulated costs, and the difference is taken to a variance.
- First-in first-out costing(FIFO)— First-in first-out costing is a complex evaluation that produces layers of expenses, one for any units of production that were begun in the before production period but not produced, and another coating for any production that is beginning in the recent time.
A Real-life Example of Process Costing
A paper manufacturing unit has the following processes
- Making pulp
- Beating
- Pulp to paper
- Finishing
Let us assume the costs incurred for producing 1000 units as shown in the table below:
Item | Amount in $ |
Making pulp | 100 |
Beating | 200 |
Pulp to paper | 150 |
Finishing | 300 |
Total Costs | 750 |
Total units | 1000 |
Cost per unit | 0.75 |
The above tabular data is an example presentation of process costing. However, in an actual unit, there will be Work in Progress (WIP) at any given period end. So, the steps for process costing will be
The total production is calculated as below:
Total production = Opening stock at beginning of period + Production during the period - Rejections if any + Equivalent units of Work in process
(To convert the number of WIP units to finished product equivalent lets understand this example: Say 500 units are in WIP and they are 50% complete then the finished product equivalent will be 500*50% =250)
To determine the total costs, direct and indirect expenses included for the beginning stock and current production are to be considered.
Allocation of the costs incurred for the full inventory is done by allocating the entire costs by equivalent units of goods.
To compute costs under process costing we, can use either the FIFO or weighted average cost flow assumption.
In FIFO, it is estimated that the material that comes in first is allocated out first, and therefore the two processes (FIFO and weighted average) vary while evaluating opening inventory.
The evaluation of work in progress in both the procedure is as below:
Steps | Weighted Average | First in first out |
Total production | Units transferred out + Ending inventory WIP | Beginning WIP + Units transferred out + Ending WIP |
Total Costs | Beginning WIP costs + Costs incurred during the period | Total costs incurred during the period |
Cost allocation | Total costs / Total units | Total costs / Total units |
In the case of WIP, there will be a percentage of completion that will have to be looked into and equivalent units will have to be computed. For instance, the notion is that the percentage of finishing is similar for both material and labor.
Item | Percentage |
Opening inventory | 5000, 40% complete |
Units started during the period | 12000 |
Closing inventory | 4000, 60% complete |
In the FIFO process, the evaluation of total production will be as below:
Opening inventory - 5000*60% (since 40% has been completed) = 3000
Completed units (Units started - closing inventory) – 12000 - 4000 = 8000
Closing inventory - 4000*60% = 2400
Therefore, total production is 3000+8000+2400 = 13400
Now, let us evaluate total production under the WAA method:
Completed units 12000-4000 = 8000
Closing WIP (4000*60%) = 2400
Total production = 10400
Similarly, the expenses will have to be calculated and allocated to the Equivalent units of manufacture.
Common Mistakes and Pitfalls
- Not starting with a pre-cost.
- Each style, product, or item, will need its separate costing, e.g., the same fabric for multiple styles, the amount of fabric may vary, which will affect the overall cost for each item.
- It is essential to include every feature component into your costing because when you are multiplying things by a factor to get your retail price, it all adds up.
- Not considering shipping.
- Not updating the numbers in your spreadsheet according to practical costs.
Related Concepts
- Operation costing
- Accounting Methodology
- Cost accounting
Context and Applications
This topic is significant in the professional exams for both undergraduate and graduate courses
- Bachelor programs in accounting
- B. Com
- M.Com
- Intermediate Cost Accountancy
- CPA
Want more help with your accounting homework?
*Response times may vary by subject and question complexity. Median response time is 34 minutes for paid subscribers and may be longer for promotional offers.
Search. Solve. Succeed!
Study smarter access to millions of step-by step textbook solutions, our Q&A library, and AI powered Math Solver. Plus, you get 30 questions to ask an expert each month.
Process Costing Homework Questions from Fellow Students
Browse our recently answered Process Costing homework questions.
Search. Solve. Succeed!
Study smarter access to millions of step-by step textbook solutions, our Q&A library, and AI powered Math Solver. Plus, you get 30 questions to ask an expert each month.