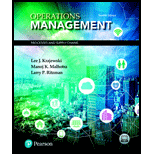
Concept explainers
Bold Vision, Inc., makes laser printer and photocopier toner cartridges. The demand rate is 625 EP cartridges per week. The production rate is 1,736 EP cartridges per week, and the setup cost is $100. The value of inventory is $130 per unit, arid the holding cost is 20 percent of the inventory value. Bold Vision operates 52 weeks a year. What is the economic production lot size?

Interpretation: The Economic production of the lot of printer and cartridges made by the company are to be calculated.
Concept Introduction: Economic production of a lot is the quantity produced at lowest stock value. It is the minimum of total cost that requires for output.
Answer to Problem 1P
Economic production of the lot is 625.
Explanation of Solution
Given information:
Demand rate per week = 625 units, Production Rate per week = 1,736 Units and Holding cost = 20% of Stock value
Economic Order Quantity is the ideal quantity of stock to order for a given product.
The demand rate per week = 625 units
This means
Production Rate per week = 1,736 Units
Holding cost = 20% of Stock value
The Economic Production of Lot size,
So, 625 units are required for the economic production lot size.
Want to see more full solutions like this?
Chapter C Solutions
Operations Management: Processes and Supply Chains (12th Edition) (What's New in Operations Management)
- The chapter presented various approaches for the control of inventory investment. Discuss three additional approaches not included that might involve supply chain managers.arrow_forwardplease answer both parts of the question within 30 minutes.arrow_forwardFresh Market opens 300 days a year. The usage of cash register tape is on average about 262 rolls daily (daily demand). Fresh Market pays a flat fee $21 to place an order of cash register tape. Fresh Market pays a unit price of $2 to the register tape supplier. The holding cost per unit per year is 5% of the unit price. Calculate the annual holding cost for Fresh Market? keep two decimals if not exact. either round up or down is ok For example. for 0.1346, (0.13 or .13) and (0.14 or.14) are correct.arrow_forward
- My Kitchen Delights (MKD), a regional producer ofgourmet jams and jellies, uses approximately 24,000 glass jarseach month during its production. Because of space limitations,MKD orders 5000 jars at a time. Monthly holding cost is $0.08 perjar, and the ordering cost is $60 per order. Th e company operates20 days per month.(a) What penalty cost is the company incurring by its presentreplenishment policy?(b) MKD would prefer to order eight times each month butneeds to justify any change in order size. How muchwould ordering cost need to be reduced to justify a lot sizeof 3000 jars?(c) If MKD can reduce its ordering cost to $30, what is theoptimal replenishment order quantity?arrow_forwardJust need help with the underlinedarrow_forwardControlling inventory is one of Wheeled Coach’s toughest problems.Operating according to a strategy of mass customizationand responsiveness, management knows that success is dependenton tight inventory control. Anything else results in an inabilityto deliver promptly, chaos on the assembly line, and a hugeinventory investment. Wheeled Coach finds that almost 50% ofthe cost of every ambulance it manufactures is purchased materials.A large proportion of that 50% is in chassis (purchased fromFord), aluminum (from Reynolds Metal), and plywood usedfor flooring and cabinetry construction (from local suppliers).Wheeled Coach tracks these A inventory items quite carefully,maintaining tight security/control and ordering carefully so as tomaximize quantity discounts while minimizing on-hand stock.Because of long lead times and scheduling needs at Reynolds,aluminum must actually be ordered as much as 8 months inadvance. In a crowded ambulance industry in which it is the only giant, its45…arrow_forward
- Joe Henry's machine shop uses 2,520 brackets during the course of a year. These brackets are purchased from a supplier 90 miles away. The following information is known about the brackets: Annual demand 2,520 Holding cost per bracket per year Order cost per order $1.55 $19.00 Lead time 2 days Working days per year 250 a) What is the EOQ? units (round your response to two decimal places). b)What is the average inventory if the EOQ is used? What would be the annual inventory holding cost? $ units (round your response to two decimal places). (round your response to two decimal places). c)Given the EOQ, how many orders will be made annually? orders (round your response to two decimal places). What would be the annual order cost? $ (round your response to two decimal places). d)Given the EOQ, what is the total annual cost of managing (ordering and holding) the inventory? $ (round your response to two decimal places). e)What is the time between orders? days (round your response to two…arrow_forwardJoe Henry's machine shop uses 2,500 brackets during the course of a year. These brackets are purchased from a supplier 90 miles away. The following information is known about the brackets: Annual demand 2,500 Holding cost per bracket per year $1.50 Order cost per order $18.75 Lead time 2 days Working days per year 250 a) What is the EOQ?units (round your response to two decimal places).arrow_forwardYellow Press, Inc., buys paper in 1,500-pound rolls for print-ing. Annual demand is 2,500 rolls. The cost per roll is $800,and the annual holding cost is 15 percent of the cost. Eachorder costs $50 to process.a. How many rolls should Yellow Press, Inc., order at a time?b. What is the time between orders?arrow_forward
- Pet Empire operates 52 weeks per year, 6 days per week, and uses a continuous review inventory system. It purchases kitty litter for $11.70 per bag. The following information is available about these bags. Demand is 90 bags per week, order cost is $54 per order, annual holding cost is 27% of the cost, service level is 80%, lead time is 3 weeks (18 working days), and standard deviation of weekly demand is 15 bags. Current on hand inventory is 320 bags with no open orders or back orders. Require to calculate Economic Order Quantity (EOQ). What would be the average time between orders (in weeks)? Calculate reorder point (R). The store currently uses a lot size of 500 bags (i.e., Q = 500). Calculate the annual holding cost of this policy and also annual ordering cost. Without calculating the EOQ, how can you conclude from these two calculation that the current lot size is too large? What would be the annual cost saved by shifting from the 500-bag lot size to the EOQ? Consider again the…arrow_forwardSam's Pet Hotel operates 52 weeks per year, 6 days per week, and uses a continuous review inventory system. It purchases kitty litter for $13.00 per bag. The following information is available about these bags: ≻Demand=75 bags/week ≻Order cost=$55.00/order ≻Annual holding cost=25 percent of cost ≻Desired cycle-service level=80 percent ≻Lead time=4 weeks (24 working days) ≻Standard deviation of weekly demand=15 bags ≻Current on-hand inventory is 320 bags, with no open orders or backorders. Part 2 a. Suppose that the weekly demand forecast of 75 bags is incorrect and actual demand averages only 50 bags per week. How much higher will total costs be, owing to the distorted EOQ caused by this forecast error? The costs will be $enter your response here higher owing to the error in EOQ. (Enter your response rounded to two decimal places.) a. What is the EOQ? What would the average time between orders (in weeks)? b. What should R be? c. An inventory withdraw…arrow_forwardRace One Motors is an Indonesian car manufacturer. Atits largest manufacturing facility, in Jakarta, the company producessubcomponents at a rate of 300 per day, and it uses these subcomponentsat a rate of 12,500 per year (of250 working days). Holding costsare $2 per item per year, and orde1ing (setup) costs are $30 per order.a) What is the economic production quantity?b) How many production runs per year will be made?c) What will be the maximum inventory level?d) What percentage of time will the facility be producing components?e) What is the annual cost of ordering and holding inventory?arrow_forward
- Purchasing and Supply Chain ManagementOperations ManagementISBN:9781285869681Author:Robert M. Monczka, Robert B. Handfield, Larry C. Giunipero, James L. PattersonPublisher:Cengage Learning
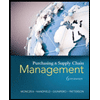