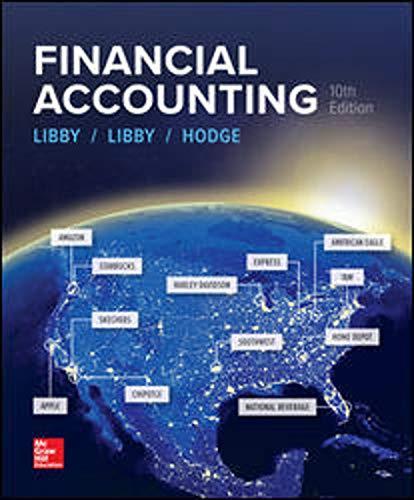
Concept explainers
Structuring the Sell-or-Process-Further Decision
Bart’s Butters receives 1,000,000 containers of raw milk each period that it subsequently processes into consumable milk by adjusting the fat content, adding vitamins, and destroying any potentially harmful bacteria. For Bart’s, one container equals one gallon of consumable milk. Bart’s then must decide whether to sell its consumable milk at split-off or to process it further into butter. Bart’s normally sells consumable milk for a per-gallon price of $3. Alternately, each gallon of milk can be processed further into one-half tub of butter (i.e., one gallon of milk equals 0.5 gallon of butter) at an additional cost of $1.50 per tub of butter. Also, butter can be sold for $6.00 per tub.
Required:
1. What is the contribution to income from selling the consumable milk?
$fill in the blank 1
2. What is the contribution to income from processing the consumable milk into butter?
$fill in the blank 2
3. Should Bart’s continue to sell the consumable milk or process it further into butter?
Sell the consumable milk without processing

Trending nowThis is a popular solution!
Step by stepSolved in 3 steps

- Sell or Process Further Dakota Coffee Company produces Columbian coffee in batches of 7,500 pounds. The standard quantity of materials required in the process is 7,500 pounds, which cost $6.00 per pound. Columbian coffee can be sold without further processing for $9.80 per pound. Columbian coffee can also be processed further to yield Decaf Columbian, which can be sold for $11.60 per pound. The processing into Decaf Columbian requires additional processing costs of $6,300 per batch. The additional processing will also cause a 5% loss of product due to evaporation. Question Content Area a. Prepare a differential analysis dated December 11 on whether to sell regular Columbian (Alternative 1) or process further into Decaf Columbian (Alternative 2). If required, use a minus sign to indicate a loss. Differential AnalysisSell Regular (Alt. 1) or Process Further into Decaf (Alt. 2)December 11 SellRegular(Alternative 1) ProcessFurther intoDecaf(Alternative 2)…arrow_forwardNervana Soy Products (NSP) buys soybeans and processes them into other soy products. Each ton of soybeans that NSP purchases for $350 can be converted for an additional $210 into 650 lbs of soy meal and 100 gallons of soy oil. A pound of soy meal can be sold at splitoff for $1.32 and soy oil can be sold in bulk for $4.5 per gallon. NSP can process the 650 pounds of soy meal into 750 pounds of soy cookies at an additional cost of $300. Each pound of soy cookies can be sold for $2.32 per pound. The 100 gallons of soy oil can be packaged at a cost of $230 and made into 400 quarts of Soyola. Each quart of Soyola can be sold for $1.15. Read the requirements. Requirement 1. Allocate the joint cost to the cookies and the Soyola using the (a) Sales value at splitoff method and (b) NRV method. a. First, allocate the joint cost using the Sales value at splitoff method. (Round the weights to three decimal places and joint costs to the nearest dollar.) Sales value of total production at splitoff…arrow_forwardSell of Process Further Rose Hill, a soybean farm in northern Minnesota, has a herd of 50 dairy cows. The cows produce approximately 2,800 gallons of milk per week. The farm currently sells all its milk to a nearby processor for $1.25 per gallon, a significant drop from the $2.00 per gallon they were able to charge five years ago. It costs $1.60 per gallon to produce the milk. The owners of Rose Hill are deciding whether to sell the dairy cows or expand into the artisan cheese market. Both owners have prior cheese-making experience and they already have all the needed equipment. It takes 0.8 gallons of milk to make a pound of cheese. Costs to produce a pound of cheese are expected to total $7 per pound. Artisan cheeses are currently selling for $10 per pound at farmer's markets and upscale groceries. Required a. How much incremental profit would Rose Hill recognize if half the milk each week was used to make cheese? $ 1,050 X b. How much, in total, would Rose Hill earn each week if…arrow_forward
- Accountarrow_forwardBrevall Industries makes corn oil and corn meal from harvested corn in a joint process. Corn oil can be further processed into margarine, and the corn meal can be further processed into corn muffin mix. The joint cost incurred to process the corn to the split-off point is $140,000. Information on the quantities, value, and further processing costs for the joint product appears below: Sales Value Estimated Further Sales Value Quantity At Split-off Processing Cost After Processing Corn Oil 800,000 lbs. $0.30/lb. $0.35/lb. $0.60/lb. Corn Meal 1,600,000 lbs. 0.10/lb. 0.40/lb. 0.55/lb. Brevall allocates the joint cost to the products based on physical units. Corn oil is assigned $46,667 of joint cost and corn meal is assigned $93,333 of joint cost. Which…arrow_forward9. New Madrid Chocolate Corporation manufactures bulk chocolate that it sells to Venus Candy Company. Currently, New Madrid packages and ships their bulk chocolate in 50-pound bars that are then shipped by truck to Venus. Venus then unpacks the bars, disposes of the packaging, melts the bars, and works the chocolate into smaller retail products. An astute and environmental conscientious employee observes that New Madrid could make the chocolate keep it hot or warm and ship it in heated tankers to Venus. This would save cooling and reheating energy cost, packaging cost and time associated with these activities. Assume the following cost: • Cooling cost and time for New Madrid $10,000 • Packaging cost for New Madrid $20,000 Annual transportation cost by truck $50,000 paid by New Madrid Annual transportation cost by train $40,000 paid by New Madrid Unpackaging and disposal cost of packaging for Venus $10,000 • Reheating cost and time for Venus $30,000 How much will New Madrid gain if they…arrow_forward
- Make or Buy A restaurant bakes its own bread for a cost of $168 per unit (100 loaves), including fixed costs of $36 per unit. A proposal is offered to purchase bread from an outside source for $98 per unit, plus $9 per unit for delivery. Prepare a differential analysis dated July 7 to determine whether the company should make (Alternative 1) or buy (Alternative 2) the bread, assuming that fixed costs are unaffected by the decision. If an amount is zero, enter "0". For those boxes in which you must enter subtracted or negative numbers use a minus sign. Differential Analysis Make Bread (Alt. 1) or Buy Bread (Alt. 2) July 7 Make Bread(Alternative 1) Buy Bread(Alternative 2) Differential Effecton Income(Alternative 2) Sales price $0 $0 $0 Unit Costs: Purchase price $fill in the blank c067b9003ffaff2_1 $fill in the blank c067b9003ffaff2_2 $fill in the blank c067b9003ffaff2_3 Delivery fill in the blank c067b9003ffaff2_4 fill in the blank c067b9003ffaff2_5…arrow_forwardAtlas Foods produces three supplemental food products simultaneously through a refining process costing $85,000. The joint products, Alfa and Betters, have a final selling price of $8 per pound and $5 per pound, respectively, after additional processing costs of $3 per pound of each product are incurred after the split-off point. Morefeed, a by-product, is sold at the split- off point for $2.50 per pound. Additional information are as follows: Alfa - 15,000 pounds of Alfa, a popular but relatively rare grain supplement of having a caloric value of 8,800 calories/pound. Betters - 5,000 pounds of Betters, a flavouring material high in carbohydrates with a caloric value of 12,000 calories/pound. Morefeed - 2,000 pounds of Morefeed, used as a cattle feed supplement with a caloric value of 1,000 calories/pound. Questions: 1. Assuming Atlas Foods does not inventory Morefeed, the by-product, the joint cost to be allocated to Betters using the net realizable method is?arrow_forwardIllion Soy Products (ASP) buys soybeans and processes them into other soy products. Each ton of soybeans that ASP purchases for $250 can be converted for an additional $180 into 700 lbs of soy meal and 80 gallons of soy oil. A pound of soy meal can be sold at splitoff for $1.08 and soy oil can be sold in bulk for $4 per gallon. ASP can process the 700 pounds of soy meal into 800 pounds of soy cookies at an additional cost of $370. Each pound of soy cookies can be sold for $2.08 per pound. The 80 gallons of soy oil can be packaged at a cost of $200 and made into 320 quarts of Soyola. Each quart of Soyola can be sold for $1.45. Read the requirements. Requirement 1. Allocate the joint cost to the cookies and the Soyola using the (a) Sales value at splitoff method and (b) NRV method. a. First, allocate the joint cost using the Sales value at splitoff method. (Round the weights to three decimal places and joint costs to the nearest dollar.) Sales value of total production at splitoff…arrow_forward
- Make or Buy A company manufactures various sized plastic bottles for its medicinal product. The manufacturing cost for small bottles is $56 per unit (100 bottles), including fixed costs of $18 per unit. A proposal is offered to purchase small bottles from an outside source for $29 per unit, plus $4 per unit for freight. Prepare a differential analysis dated March 30 to determine whether the company should Make Bottles (Alternative 1) or Buy Bottles (Alternative 2), assuming that fixed costs are unaffected by the decision. If an amount is zero, enter "0". For those boxes in which you must enter subtracted or negative numbers use a minus sign. Differential Analysis Make Bottles (Alt. 1) or Buy Bottles (Alt. 2) March 30 Make Buy Differential Bottles Bottles Effect (Alternative 1) (Alternative 2) (Alternative 2) Unit Costs: Purchase price Freight Variable costs Fixed factory overhead Total unit costs Determine whether the company should make (Alternative 1) or buy (Alternative 2) the…arrow_forwardSell or Process Further Zing Coffee Company produces Columbian coffee in batches of 5,800 pounds. The standard quantity of materials required in the process is 5,800 pounds, which cost $4.00 per pound. Columbian coffee can be sold without further processing for $8.40 per pound. Columbian coffee can also be processed further to yield Decaf Columbian, which can be sold for $10.00 per pound. The processing into Decaf Columbian requires additional processing costs of $12,050 per batch. The additional processing will also cause a 5% loss of product due to evaporation. a. Prepare a differential analysis report for the decision to sell or process further. Zing Coffee Company Proposal to Process Columbian Coffee Further Differential Analysis Report Differential revenue from further processing per batch: Revenue from sale of Decaf Columbian v Revenue from sale of Columbian coffee v Differential revenue v Differential cost per batch: Additional cost of producing Decaf Columbian v Differential…arrow_forwardHaving trouble with some questions from the last chapter.arrow_forward
- AccountingAccountingISBN:9781337272094Author:WARREN, Carl S., Reeve, James M., Duchac, Jonathan E.Publisher:Cengage Learning,Accounting Information SystemsAccountingISBN:9781337619202Author:Hall, James A.Publisher:Cengage Learning,
- Horngren's Cost Accounting: A Managerial Emphasis...AccountingISBN:9780134475585Author:Srikant M. Datar, Madhav V. RajanPublisher:PEARSONIntermediate AccountingAccountingISBN:9781259722660Author:J. David Spiceland, Mark W. Nelson, Wayne M ThomasPublisher:McGraw-Hill EducationFinancial and Managerial AccountingAccountingISBN:9781259726705Author:John J Wild, Ken W. Shaw, Barbara Chiappetta Fundamental Accounting PrinciplesPublisher:McGraw-Hill Education
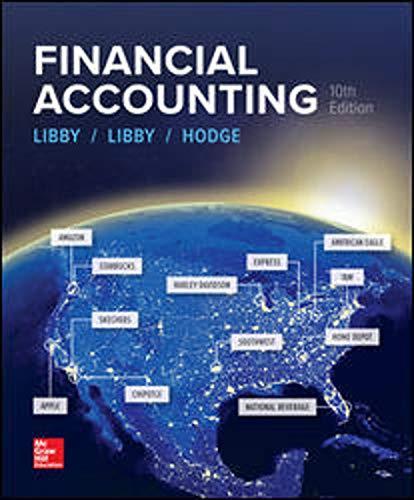
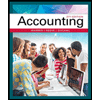
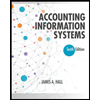
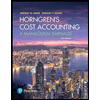
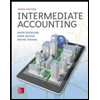
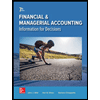