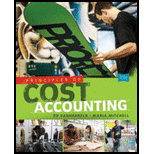
Concept explainers
A company manufactures a liquid product called Crystal. The basic ingredients are put into process in Department 1. In Department 2, other materials are added that increase the number of units being processed by 50%. The factory has only two departments.
Calculate the following for each department: (a) unit cost for the month for materials, labor, and factory
1.

Compute unit cost for materials, labor and factory overhead, cost of the units transferred and cost of the ending work in process-department 1.
Explanation of Solution
Compute equivalent unit of production.
Particulars | Units |
Units finished and transferred out | 14,000 |
Ending work in process | 1,000 |
Total | 15,000 |
Table (1)
a. Compute unit cost.
Particulars | Amount ($) |
Materials | 6 |
Labor | 2 |
Factory overhead | 1 |
Total | 9 |
Table (2)
Working Notes:
Calculate the cost of work in process, end of month-material.
Calculate the cost of work in process, end of month-labor.
Calculate the cost of work in process, end of month-factory overhead.
b. Compute cost of units finished and transferred.
c. Compute total work in process, end of month.
Particulars | Amount ($) |
Materials | 6,000 |
Labor | 2,000 |
Factory overhead | 1,000 |
Total | 9,000 |
Table (3)
Working Notes:
Calculate the cost of work in process-material.
Calculate the cost of work in process-labor.
Calculate the cost of work in process-factory overhead.
2.

Compute unit cost for materials, labor and factory overhead, cost of the units transferred and cost of the ending work in process-department 2.
Explanation of Solution
Compute equivalent unit of production- department 2.
Particulars | Units |
Units finished and transferred out | 15,000 |
Ending work in process | 3,000 |
Total | 18,000 |
Table (4)
a. Compute unit cost-department 2.
Particulars | Amount ($) |
Materials | 2 |
Labor | 0.75 |
Factory overhead | 0.25 |
Total | 3 |
Table (5)
Working Notes:
Calculate the cost of work in process, end of month-material.
Calculate the cost of work in process, end of month-labor.
Calculate the cost of work in process, end of month-factory overhead.
b. Compute cost of units finished and transferred- department 2.
Particulars | Amount ($) |
Cost in department 1 | 90,000 |
Cost in department 2 | 45,000 |
Total | 135,000 |
Table (6)
Working Notes:
Calculate the cost in department 1.
(1) Calculate the adjusted unit cost.
(2) Calculate the new quantity.
Particulars | Amount ($) |
Units from department | 14,000 |
Units added | 7,000 |
New quantity | 21,000 |
Table (7)
Calculate the cost in department 2.
c. Compute work in process, end of month- department 2.
Particulars | Amount ($) | Amount ($) |
Cost in department 1 | 36,000 | |
Cost in department 2 | ||
Materials | 6,000 | |
Labor | 2,000 | |
Factory overhead | 1,000 | 9,000 |
Total | 45,000 |
Table (8)
Working Notes:
Calculate the cost of work in process-material.
Calculate the cost of work in process-labor.
Calculate the cost of work in process-factory overhead.
Want to see more full solutions like this?
Chapter 6 Solutions
Principles of Cost Accounting
Additional Business Textbook Solutions
Managerial Accounting
Horngren's Accounting (12th Edition)
Horngren's Accounting (11th Edition)
Cost Accounting (15th Edition)
- A manufacturing company has two service and two production departments. Building Maintenance and Factory Office are the service departments. The production departments are Assembly and Machining. The following data have been estimated for next years operations: The direct charges identified with each of the departments are as follows: The building maintenance department services all departments of the company, and its costs are allocated using floor space occupied, while factory office costs are allocable to Assembly and Machining on the basis of direct labor hours. 1. Distribute the service department costs, using the direct method. 2. Distribute the service department costs, using the sequential distribution method, with the department servicing the greatest number of other departments distributed first.arrow_forwardLansing. Inc., provided the following data for its two producing departments: Machine hours are used to assign the overhead of the Molding Department, and direct labor hours are used to assign the overhead of the Polishing Department. There are 30,000 units of Form A produced and sold and 50,000 of Form B. Required: 1. Calculate the overhead rates for each department. 2. Using departmental rates, assign overhead to live two products and calculate the overhead cost per unit. How does this compare with the plantwide rate unit cost, using direct labor hours? 3. What if the machine hours in Molding were 1,200 for Form A and 3,800 for Form B and the direct labor hours used in Polishing were 5,000 and 15,000, respectively? Calculate the overhead cost per unit for each product using departmental rates, and compare with the plantwide rate unit costs calculated in Requirement 2. What can you conclude from this outcome?arrow_forwardK-Briggs Company uses the FIFO method to account for the costs of production. For Crushing, the first processing department, the following equivalent units schedule has been prepared: The cost per equivalent unit for the period was as follows: The cost of beginning work in process was direct materials, 40,000; conversion costs, 30,000. Required: 1. Determine the cost of ending work in process and the cost of goods transferred out. 2. Prepare a physical flow schedule.arrow_forward
- The standard cost summary for the most popular product of Phenom Products Co. is shown as follows, together with production and cost data for the period. One gallon each of liquid lead and varnish are added at the start of processing. The balance of the materials is added when the process is two-thirds complete. Labor and overhead are added evenly throughout the process. There were no units in process at the beginning of the month. Required: Calculate equivalent production for materials, labor, and overhead. (Be sure to refer to the standard cost summary to help determine the percentage of materials in ending work in process.) Calculate materials and labor variances and indicate whether they are favorable or unfavorable, using the diagram format shown in Figure 8-4. Determine the cost of materials and labor in the work in process account at the end of the month.arrow_forwardThe following data appeared in the accounting records of Craig Manufacturing Inc., which uses the weighted average cost method: Case 1All materials are added at the beginning of the process, and labor and factory overhead are added evenly throughout the process. Case 2One-half of the materials are added at the start of the manufacturing process, and the balance of the materials is added when the units are one-half completed. Labor and factory overhead are applied evenly during the process. Make the following computations for each case: a. Unit cost of materials, labor, and factory overhead for the month b. Cost of the units finished and transferred during the month c. Cost of the units in process at the end of the montharrow_forwardSonoma Products Inc. manufactures a liquid product in one department. Due to the nature of the product and the process, units are regularly lost during production. Materials and conversion costs are added evenly throughout the process. The following summaries were prepared for March: Calculate the unit cost for materials, labor, and factory overhead for March and show the costs of units transferred to finished goods and to ending work in process inventory.arrow_forward
- A manufacturing company has two service and two production departments. Human Resources and Machine Repair are the service departments. The production departments are Grinding and Polishing. The following data have been estimated for next years operations: The direct charges identified with each of the departments are as follows: The human resources department services all departments of the company, and its costs are allocated using the numbers of employees within each department, while machine repair costs are allocable to Grinding and Polishing on the basis of machine hours. 1. Distribute the service department costs, using the direct method. 2. Distribute the service department costs, using the sequential distribution method, with the department servicing the greatest number of other departments distributed first.arrow_forwardUsing the same data found in Exercise 6.22, assume the company uses the FIFO method. Required: Prepare a schedule of equivalent units, and compute the unit cost for the month of December. Fordman Company has a product that passes through two processes: Grinding and Polishing. During December, the Grinding Department transferred 20,000 units to the Polishing Department. The cost of the units transferred into the second department was 40,000. Direct materials are added uniformly in the second process. Units are measured the same way in both departments. The second department (Polishing) had the following physical flow schedule for December: Costs in beginning work in process for the Polishing Department were direct materials, 5,000; conversion costs, 6,000; and transferred in, 8,000. Costs added during the month: direct materials, 32,000; conversion costs, 50,000; and transferred in, 40,000.arrow_forwardThe Converting Department of Worley Company had 2,400 units in work in process at the beginning of the period, which were 35% complete. During the period, 10,800 units were completed and transferred to the Packing Department. There were 1,900 units in process at the end of the period, which were 60% complete. Direct materials are placed into the process at the beginning of production. Determine the number of equivalent units of production with respect to direct materials and conversion costs.arrow_forward
- Holmes Products, Inc., produces plastic cases used for video cameras. The product passes through three departments. For April, the following equivalent units schedule was prepared for the first department: Costs assigned to beginning work in process: direct materials, 90,000; conversion costs, 33,750. Manufacturing costs incurred during April: direct materials, 75,000; conversion costs, 220,000. Holmes uses the weighted average method. Required: 1. Compute the unit cost for April. 2. Determine the cost of ending work in process and the cost of goods transferred out.arrow_forwardHealthway uses a process-costing system to compute the unit costs of the minerals that it produces. It has three departments: Mixing, Tableting, and Bottling. In Mixing, at the beginning of the process all materials are added and the ingredients for the minerals are measured, sifted, and blended together. The mix is transferred out in gallon containers. The Tableting Department takes the powdered mix and places it in capsules. One gallon of powdered mix converts to 1,600 capsules. After the capsules are filled and polished, they are transferred to Bottling where they are placed in bottles, which are then affixed with a safety seal and a lid and labeled. Each bottle receives 50 capsules. During July, the following results are available for the first two departments (direct materials are added at the beginning in both departments): Overhead in both departments is applied as a percentage of direct labor costs. In the Mixing Department, overhead is 200 percent of direct labor. In the Tableting Department, the overhead rate is 150 percent of direct labor. Required: 1. Prepare a production report for the Mixing Department using the weighted average method. Follow the five steps outlined in the chapter. Round unit cost to three decimal places. 2. Prepare a production report for the Tableting Department. Materials are added at the beginning of the process. Follow the five steps outlined in the chapter. Round unit cost to four decimal places.arrow_forwardBox Springs. Inc., makes two sizes of box springs: queen and king. The direct material for the queen is $35 per unit and $55 is used in direct labor, while the direct material for the king is $55 per unit, and the labor cost is $70 per unit. Box Springs estimates it will make 4,300 queens and 3,000 kings in the next year. It estimates the overhead for each cost pool and cost driver activities as follows: How much does each unit cost to manufacture?arrow_forward
- Principles of Cost AccountingAccountingISBN:9781305087408Author:Edward J. Vanderbeck, Maria R. MitchellPublisher:Cengage LearningCornerstones of Cost Management (Cornerstones Ser...AccountingISBN:9781305970663Author:Don R. Hansen, Maryanne M. MowenPublisher:Cengage LearningManagerial AccountingAccountingISBN:9781337912020Author:Carl Warren, Ph.d. Cma William B. TaylerPublisher:South-Western College Pub
- Financial And Managerial AccountingAccountingISBN:9781337902663Author:WARREN, Carl S.Publisher:Cengage Learning,Principles of Accounting Volume 2AccountingISBN:9781947172609Author:OpenStaxPublisher:OpenStax CollegeManagerial Accounting: The Cornerstone of Busines...AccountingISBN:9781337115773Author:Maryanne M. Mowen, Don R. Hansen, Dan L. HeitgerPublisher:Cengage Learning
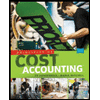
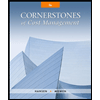
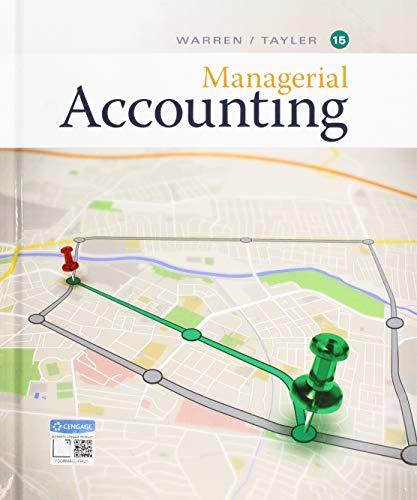
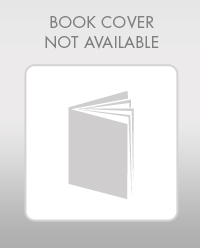
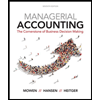