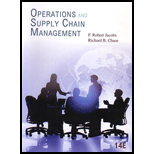
a)
To determine: The time and parts costs for the dozen units.
Introduction: It is the rate to measure the performance of the person in the new skills and in gaining experiences.
a)

Explanation of Solution
Given information:
The first unit produced by Company L took 5,000 hours for production and required $250,000 worth of material. The second unit took 3,500 hours and $200,000. It is given that labor is $30 per hour.
Estimate the learning rate for labor:
Estimate the learning rate for Unit 1 to Unit 2:
It is calculated by dividing the time taken to complete the second unit and first unit.
Hence, the learning percentage is 70%.
Estimate the learning rate for material:
Estimate the learning rate for Unit 1 to Unit 2:
It is calculated by dividing the time taken to complete the second unit and first unit.
Hence, the learning percentage is 80%.
Determine the labor cost for 10 more units:
It is computed by subtracting the cumulative value for 2 units from cumulative value for 12 units and multiplying it with the time to produce first unit and labor cost per hour.
The cumulative values can be determined using the table of cumulative values. For example, 5.501 is the cumulative value for 12 units and 70% learning rate.
Hence, the labor cost for 10 more units is $570,150.
Determine the material cost for 10 more units:
It is computed by subtracting the cumulative value for 2 units from cumulative value for 12 units and multiplying it with the time to produce first unit and labor cost per hour.
The cumulative values can be determined using the table of cumulative values. For example, 5.427 is the cumulative value for 12 units and 80% learning rate.
Hence, the material cost for 10 more units is $1,356,750.
Compute the total cost:
It is computed by adding labor cost and material cost.
Hence, the total cost is $1,926,900.
b)
To determine: The way the reassignment of personnel and equipment to another project would affect the subsequent bid.
Introduction: It is the rate to measure the performance of the person in the new skills and in gaining experiences.
b)

Explanation of Solution
Given information:
The first unit produced by Company L took 5,000 hours for production and required $250,000 worth of material. The second unit took 3,500 hours and $200,000. It is given that labor is $30 per hour.
Determine the labor cost for 10 more units:
The cumulative values can be determined using the table of cumulative values. For example, 4.931 is the cumulative value for 10 units and 70% learning rate.
Hence, the labor cost for 10 more units is $739,650.
Determine the material cost for 10 more units:
The cumulative values can be determined using the table of cumulative values. For example, 6.315 is the cumulative value for 10 units and 80% learning rate.
Hence, the material cost for 10 more units is $1,578,750.
Compute the total cost:
It is computed by adding labor cost and material cost.
Hence, the total cost is $2,318,400.
Want to see more full solutions like this?
Chapter 6 Solutions
Operations and Supply Chain Management
- Practical Management ScienceOperations ManagementISBN:9781337406659Author:WINSTON, Wayne L.Publisher:Cengage,Operations ManagementOperations ManagementISBN:9781259667473Author:William J StevensonPublisher:McGraw-Hill EducationOperations and Supply Chain Management (Mcgraw-hi...Operations ManagementISBN:9781259666100Author:F. Robert Jacobs, Richard B ChasePublisher:McGraw-Hill Education
- Purchasing and Supply Chain ManagementOperations ManagementISBN:9781285869681Author:Robert M. Monczka, Robert B. Handfield, Larry C. Giunipero, James L. PattersonPublisher:Cengage LearningProduction and Operations Analysis, Seventh Editi...Operations ManagementISBN:9781478623069Author:Steven Nahmias, Tava Lennon OlsenPublisher:Waveland Press, Inc.
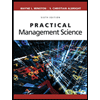
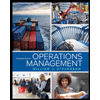
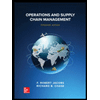
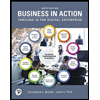
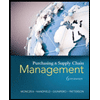
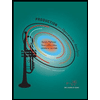