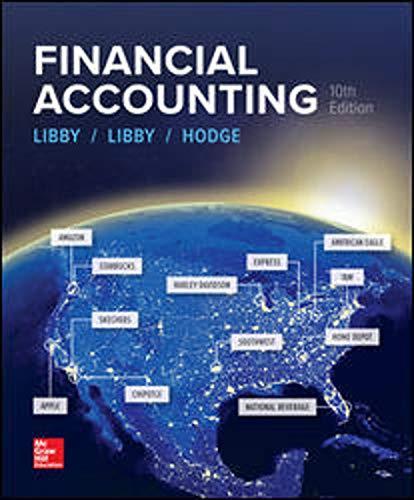
Concept explainers
Bender Automotive Works Inc. manufactures a variety of front-end assemblies for automobiles. A front-end assembly is the unified front of an automobile that includes the headlamps, fender, and surrounding metal/plastic. Bender has two producing departments: Drilling and Assembly. Usually, the front-end assemblies are ordered in batches of 100.
Two support departments provide support for Bender’s producing departments: Maintenance and Power. Budgeted data for the coming quarter follow. The company does not separate fixed and variable costs.
|
Support Departments |
|
Producing Departments |
||
|
Maintenance |
Power |
|
Drilling |
Assembly |
|
$320,000 |
$400,000 |
|
$163,000 |
$90,000 |
Machine hours |
- |
22,500 |
|
30,000 |
7,500 |
Kilowatt-hours |
40,000 |
- |
|
36,000 |
324,000 |
Direct labor hours |
- |
- |
|
5,000 |
40,000 |
The predetermined overhead rate for Drilling is computed on the basis of machine hours. Direct labor hours are used for Assembly.
Recently, a truck manufacturer requested a bid on a 3-year contract that would supply front-end assemblies to a nearby factory. The prime costs for a batch of 100 front-end assemblies are $1,817. It takes two machine hours to produce a batch in the drilling department and 50 direct labor hours to assemble the 100 front-end assemblies in the assembly department.
Bender’s policy is to bid full
REQUIRED:
- Prepare bids for Bender by using each of the following allocation methods: (a) direct method and (b) sequential method, allocating power costs first. (Note: Round allocation ratios to four decimal places, allocated support department cost to the nearest dollar, and the job cost components to the nearest cent.)
- Which method most accurately reflects the cost of producing the front-end assemblies? Why?

Trending nowThis is a popular solution!
Step by stepSolved in 7 steps with 6 images

- Juda Recliners manufactures leather recliners and uses flexible budgeting and a standard cost system. Juda allocates overhead based on yards of direct materials. The company's performance report includes the following selected data: Data table Sales Static Budget (1,025 recliners) Actual Results (1,005 recliners) (1,025 recliners x $515 each) (1,005 recliners x $480 each) S 527,875 S 482,400 Variable Manufacturing Costs Direct Materials (6.150 yds @ $8.90/yd.) (6,300 yds @ $8.70/yd.) 54,735 54 810 Direct Labor (10,250 DLHr @ $11.30/DLHr) (9,850 DLHr @ $11.40/DLHr) 115,825 112,290 Variable Overhead (6,150 yds @ $5.10/yd.) 31,365 (6,300 yds. @ $6.50/yd) 40,950 Fixed Manufacturing Costs: Fixed Overhead Total Cost of Goods Sold Gross Profit 62,730 64,730 264,655 272,780 $ 263,220 $ 209,620 - Xarrow_forwardCarlton, Inc. manufactures model airplane kits and projects production at 550, 420, 150, and 800 kits for the next four quarters. (Click the icon to view the manufacturing information.) Prepare Carlton's direct materials budget, direct labor budget, and manufacturing overhead budget for the year. Round the direct labor hours needed for production, budgeted overhead costs, and predetermined overhead allocation rate to two decimal places. Round other amounts to the nearest whole number. Begin by preparing Carlton's direct materials budget. Direct materials (ounces) per kit Direct materials needed for production. Plus: Total direct materials needed Less: Budgeted purchases of direct materials Direct materials cost per ounce Budgeted cost direct materials purchases Carlton, Inc. Direct Materials Budget For the Year Ended December 31 First Second Quarter Quarter Third Quarter Fourth Quarter Total More info Direct materials are five ounces of plastic per kit and the plastic costs $3 per…arrow_forwardFlounder Possible Inc. (FP) is a manufacturer of toaster ovens. To improve control over operations, the president of FP wants to begin using a flexible budgeting system, rather than using only the current master budget. The following data are available for FP's expected costs at production levels of 81,000, 90,000, and 99,000 units. Variable costs Manufacturing $5 per unit Administrative $3 per unit Selling $3 per unit Fixed costs Manufacturing $144,000 Administrative $72,000arrow_forward
- Dashboard Inc. manufactures and assembles automobile instrument panels for both eCar Motors and Greenville Motors. The process consists of a lean product cell for each customer’s instrument assembly. The data that follow concern only the eCar lean cell. For the year, Dashboard Inc. budgeted the following costs for the eCar production cell: Conversion Cost Categories Budget Labor $800,000 Supplies 275,000 Utilities 325,000 Total 1,400,000 Dashboard Inc. plans 2,000 hours of production for the eCar cell for the year. The materials cost is $240 per instrument assembly. Each assembly requires 24 minutes of cell assembly time. There was no April 1 inventory for either Raw and In Process Inventory or Finished Goods Inventory. The following summary events took place in the eCar cell during April: Electronic parts and wiring were purchased to produce 450 instrument assemblies in April. Conversion costs were applied for the production of 400 units in…arrow_forwardAlyeski Tours operates day tours of coastal glaciers in Alaska on its tour boat the Blue Glacier. Management has identified two cost drivers—the number of cruises and the number of passengers—that it uses in its budgeting and performance reports. The company publishes a schedule of day cruises that it may supplement with special sailings if there is sufficient demand. Up to 88 passengers can be accommodated on the tour boat. Data concerning the company’s cost formulas appear below: Fixed Cost per Month Cost per Cruise Cost per Passenger Vessel operating costs $ 6,400 $ 478.00 $ 3.20 Advertising $ 2,600 Administrative costs $ 5,000 $ 32.00 $ 1.50 Insurance $ 3,300 For example, vessel operating costs should be $6,400 per month plus $478.00 per cruise plus $3.20 per passenger. The company’s sales should average $35.00 per passenger. In July, the company provided 51 cruises for a total of 3,000 passengers. Required: Prepare the company’s flexible budget for…arrow_forwardUse the image below to answer the following question. The blue box represents the VAnswer the following question The Lebanese Bakery Inc. also allocates FMOH to products on the basis of standard direct manufacturing labor - hours. For the year, FMOH was budgeted at $4.00 per DMLH. Actual FMOH incurred during the year was $272,000. Baguettes are baked in batches of 100 loaves. Following are some pertinent data for Lebanese Bakery Inc: Direct manufacturing labor use: 2.00 DMLH per batch Fixed manufacturing overhead: $4.00 per DMLH Lebanese Bakery Inc. recorded the following additional data for the year ended December 31: Planned (budgeted) output 3, 840,000 baguettes Actual production 3, 360, 000 baguettes Direct manufacturing labor 50, 400 DMLH Actual fixed MOH $272,000 Question: 1) Why do we use these headings in specific? Explain each heading. 2) How do you know whether the rate variance ($35200 F) and production volume - variance ($38400 U) are favourable or unfavourable? Is there a…arrow_forward
- The Gourmand Cooking School runs short cooking courses at its small campus. Management has Identified two cost drivers it uses in Its budgeting and performance reports-the number of courses and the total number of students. For example, the school might run two courses in a month and have a total of 50 students enrolled in those two courses. Data concerning the company's cost formulas appear below: Instructor wages Classroom supplies Utilities Campus rent Insurance Administrative expenses Revenue Instructor wages Classroom supplies Utilities Campus rent Insurance Administrative expenses Courses Students Revenue For example, administrative expenses should be $3,270 per month plus $15 per course plus $4 per student. The company's sales should average $800 per student. Expenses: The company planned to run three courses with a total of 45 students; however, it actually ran three courses with a total of only 42 students. The actual operating results for September were as follows: Instructor…arrow_forwardOriole Stairs Co. designs and builds factory-made premium wooden stairways for homes. The manufactured stairway components (spindles, risers, hangers, hand rails) permit installation of stairways of varying lengths and widths. All are of white oak wood. Budgeted manufacturing overhead costs for the year 2025 are as follows. Purchasing Handling materials Production (cutting, milling, finishing) Setting up machines Overhead Cost Pools Inspecting Inventory control (raw materials and finished goods) Utilities Total budgeted overhead costs Purchasing Handling materials Production (cutting, milling, finishing) Setting up machines Inspecting Inventory control (raw materials and finished goods) Utilities Activity Cost Pools Direct labor For the last 4 years, Oriole Stairs Co. has been charging overhead to products on the basis of machine hours. For the year 2025, 100,000 machine hours are budgeted. Jeremy Nolan, owner-manager of Oriole Stairs Co., recently directed his accountant, Bill…arrow_forwardPerfect Parties, Inc. has several divisions, one of which provides birthday parties at their facility, and has provided the actual and planning budget results for the month of June. The Controller has asked you prepare the Birthday Party Division Budget Performance Report. Please provide me with the answers for the cells in yellow. greatly appreciate your help!arrow_forward
- The Gourmand Cooking School runs short cooking courses at its small campus. Management has identified two cost drivers it uses in its budgeting and performance reports-the number of courses and the total number of students. For example, the school might run two courses in a month and have a total of 61 students enrolled in those two courses. Data concerning the company's cost formulas appear below. Instructor wages Classroom supplies Utilities Campus rent Insurance Administrative expenses Cost per Fixed Cost per Month Cost per Course Student 2,940 $ 290 1,210 $ 50 4,700 2,200 3,700 $ 46 $ For example, administrative expenses should be $3,700 per month plus 546 per course plus $4 per student. The company's sales should average $880 per student. The company planned to run four courses with a total of 61 students; however, it actually ran four courses with a total of only 55 students. The actual operating results for September appear below. Revenue Actual 50,780 Instructor wages $ 11,040…arrow_forwardPerez Publications established the following standard price and costs for a hardcover picture book that the company produces. Standard price and variable costs Sales price Materials cost Labor cost Overhead cost Selling, general, and administrative costs Planned fixed costs Manufacturing overhead Selling, general, and administrative Perez planned to make and sell 25,000 copies of the book. Number of units Variable manufacturing costs Required: a.-d. Prepare the pro forma income statement that would appear in the master budget and also flexible budget income statements, assuming production volumes of 24,000 and 26,000 units. Determine the sales and variable cost volume variances, assuming volume is actually 26,000 units. Indicate whether the variances are favorable (F) or unfavorable (U). Note: Select "None" if there is no effect (i.e., zero variance). Fixed costs $36.50 8.60 4.40 Master Budget 25,000 7.10 $ 131,000 50,000 Flexible Budgets 24,000 < Prev 4 of 4 26,000 Volume Variances…arrow_forwardAAA Manufacturing Firm has provided the following sales, cost and expense figures in relation to expected operations for the coming year. You are tasked to prepare forecast Statements of Financial Performance using flexible budget techniques and incorporating the following information.All units are sold when manufactured due to the highly perishable nature of the company’s product. As such there are no inventories of raw materials, work in process or finished goods on hand.The selling price of the company’s single product is $50.00 and the expected sales quantity for the coming year is in the vicinity of 20,000 and 25,000 units.Required: Prepare an Income Statement budget using flexible budgeting techniques at production and sales levels of:(Scenario a) 20,000 units(Scenario b) 25,000 units Question: 1. Total fixed factory overhead under Scenario A (No dollar sign and comma) 2. Gross profit under Scenario B? (No dollar sign and comma) 3. Total non-manufacturing expenses under…arrow_forward
- AccountingAccountingISBN:9781337272094Author:WARREN, Carl S., Reeve, James M., Duchac, Jonathan E.Publisher:Cengage Learning,Accounting Information SystemsAccountingISBN:9781337619202Author:Hall, James A.Publisher:Cengage Learning,
- Horngren's Cost Accounting: A Managerial Emphasis...AccountingISBN:9780134475585Author:Srikant M. Datar, Madhav V. RajanPublisher:PEARSONIntermediate AccountingAccountingISBN:9781259722660Author:J. David Spiceland, Mark W. Nelson, Wayne M ThomasPublisher:McGraw-Hill EducationFinancial and Managerial AccountingAccountingISBN:9781259726705Author:John J Wild, Ken W. Shaw, Barbara Chiappetta Fundamental Accounting PrinciplesPublisher:McGraw-Hill Education
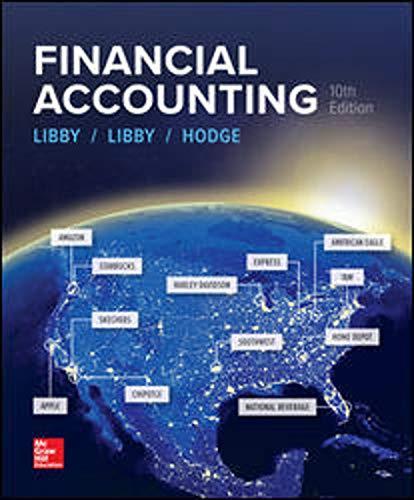
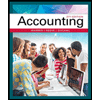
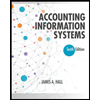
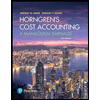
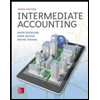
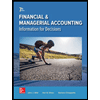