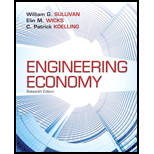
Engineering Economy (16th Edition) - Standalone book
16th Edition
ISBN: 9780133439274
Author: William G. Sullivan, Elin M. Wicks, C. Patrick Koelling
Publisher: PEARSON
expand_more
expand_more
format_list_bulleted
Concept explainers
Question
Chapter 3, Problem 14P
To determine
Calculate the estimated capital investment.
Expert Solution & Answer

Want to see the full answer?
Check out a sample textbook solution
Students have asked these similar questions
The capital investment cost for a switchgrass-fueled ethanol plant with a capacity of 250.000 gallons per year is $6.6 million. The costcapacity factor for this particular plant
technology is 0.62 for capacities ranging from 200.000 gallons per year to 600.000 gallons per year. What is the estimated capital investment for a similar ethanol plant with a capac
of 550.000 gallons per year?
The estimated capital investment for a similar ethanol plant with a capacity of 550,000 gallons per year is $ (Round to the nearest ten thousands)
An Engineering consultant firm measures its output in a standard hour unit, which is a function of the personnel grade levels in the professional stuff. The variable cost is $62 per standard service hour. The charge-out rate (i.e., selling price) is $85.56 per hour. The maximum output of the firm is 160,000 hours per year, and its fixed cost is $2,024,000 per year. For this firm:
(a) What is the breakeven point in standard service hours and in percentage of total capacity?
(b) What is the percentage reduction in breakeven (sensitivity) if fixed costs are reduced 10%; if variable cost per hour is reduced 10%; and if the selling price per unit is increased by 10%.
Note:-
Do not provide handwritten solution. Maintain accuracy and quality in your answer. Take care of plagiarism.
Answer completely.
You will get up vote for sure.
A company is analyzing a make-versus-purchase situation for a component used in several products, and the engineering department has developed these data: Option A: Purchase 10,000 items per year at a fixed price of $8.50 per item. The cost of placing the order is negligible according to the present cost accounting procedure. Option B: Manufacture 10,000 items per year, using available capacity in the factory. Cost estimates are direct materials = $5.00 per item and direct labor = $1.50 per item. Manufacturing overhead is allocated at 200% of direct labor (= $3.00 per item). Based on these data, should the item be purchased or manufactured?
Chapter 3 Solutions
Engineering Economy (16th Edition) - Standalone book
Ch. 3 - Prob. 1PCh. 3 - Prob. 2PCh. 3 - Prob. 3PCh. 3 - Prob. 4PCh. 3 - Prob. 5PCh. 3 - Prob. 6PCh. 3 - Prob. 7PCh. 3 - Prepare a composite (weighted) index for housing...Ch. 3 - Prepare a composite (weighted) index for housing...Ch. 3 - Prob. 10P
Ch. 3 - Prob. 11PCh. 3 - Prob. 12PCh. 3 - Prob. 13PCh. 3 - Prob. 14PCh. 3 - Prob. 15PCh. 3 - A biotech firm is considering abandoning its old...Ch. 3 - Prob. 17PCh. 3 - Prob. 18PCh. 3 - Prob. 19PCh. 3 - Prob. 20PCh. 3 - Prob. 21PCh. 3 - Prob. 22PCh. 3 - Prob. 23PCh. 3 - Prob. 24PCh. 3 - Prob. 25PCh. 3 - Prob. 26PCh. 3 - Prob. 28SECh. 3 - Prob. 31CSCh. 3 - Prob. 32CSCh. 3 - Prob. 36FECh. 3 - Prob. 37FECh. 3 - Prob. 38FECh. 3 - Prob. 39FECh. 3 - Prob. 40FECh. 3 - Prob. 41FE
Knowledge Booster
Learn more about
Need a deep-dive on the concept behind this application? Look no further. Learn more about this topic, economics and related others by exploring similar questions and additional content below.Similar questions
- A company is analyzing a make-versus-purchase situation for a component used in several products, and the engineering department has developed these data: Option A: Purchase 10,000 items per year at a fixed price of $8.46 per item. The cost of placing the order is negligible according to the present cost accounting procedure. Option B: Manufacture 10,000 items per year, using available capacity in the factory. Cost estimates are direct materials = $5.11 per item and direct labor = $1.32 per item. Manufacturing overhead is allocated at 200% of direct labor (= $2.64 per item). Based on these data, should the item be purchased or manufactured? The total cost of Option A is $ (Round to the nearest dollar.)arrow_forwardA company is analyzing a make-versus-purchase situation for a component used in several products, and the engineering department has developed these data: Option A: Purchase 10,000 items per year at a fixed price of $9.31 per item. The cost of placing the order is negligible according to the present cost accounting procedure. Option B: Manufacture 10,000 items per year, using available capacity in the factory. Cost estimates are direct materials=$5.16 per item and direct labor=$1.57 per item. Manufacturing overhead is allocated at 200% of direct labor (-$3.14 per item). Based on these data, should the item be purchased or manufactured? The total cost of Option A is $. (Round to the nearest dollar) The total cost of Option B is $ (Round to the nearest dollar.) Should the item be purchased or manufactured? Choose the correct answer below. The item should be manufactured. The item should be purchased. 00arrow_forwardEstimate the cost of expanding a planned new clinic by 50,000 ft2. The appropriate capacity exponent is 0.66, and the budget estimate for 200,000 ft2 is $15M.arrow_forward
- An engineering consulting firm measures its output in a standard service hour unit, which is a function of the personnel grade levels in the professional staff. The variable cost (cv) is $62 per standard service hour. The charge-out rate [i.e., selling price (p)] is $85.56 per hour. The maximum output of the firm is 160,000 hours per year, and its fixed cost (CF ) is $2,024,000 per year. For this firm, (a) what is the breakeven point in standard service hours and in percentage of total capacity? (b) what is the percentage reduction in the breakeven point (sensitivity) if fixed costs are reduced 10%; if variable cost per hour is reduced 10%; and if the selling price per unit is increased by 10%?arrow_forwardThe capital investment cost for a switchgrass-fueled ethanol plant with a capacity of 250,000 gallons per year is $6 million. The cost-capacity factor for this particular plant technology is 0.59 for capacities ranging from 200,000 gallons per year to 500,000 gallons per year. What is the estimated capitalinvestment for a similar ethanol plant with a capacity of 450,000 gallons per year?arrow_forwardA manufacturing company needs to know whether to produce components for a Bird Feeder in-house or buy the components from a fabricator. To make the components in-house, the company needs to buy an injection molding machine, which costs $9,000. The company expects to produce 10,000 units per year. The following estimates have been made: Fixed cost per year Variable cost per part Make $9,000 $6.45 Buy. $0 $7.20 a. What is the break-even point? b. If the number of units produced is 10,000, which option is cheaper: Make or Buy? Explain why. b. If the number of units produced is increased to 12,500, which option is cheaper: Make or Buy? Explain why.arrow_forward
- Company A has fixed expenses of $15,000 per year and each unit of product has a $0.20 variable cost. Company B has fixed expenses of $6,000 per year and can produce the same product at a $0.60 variable cost per unit. At what number of units of annual production will Company A have the same overall cost as Company B? (i.e., find the breakeven point)arrow_forwardA company planning to manufacture Webcams has to decide on the location of the production facility. Three location are being considered A, B and C. the fixed costs at the three locations are estimated to be $40000, $65000, and $32000 per year respectively. The variable costs are $4, $2.5 and $4.5 per unit, selling price in three location is $110, $180 and $90 respectively. Maximum capacity is 12000 unit/year in A, 19500 unit/year in B and 9600 unit/year in C. Find the following below: 1- Break- Even quantity in three location2- Profit or loss in location A when quantity is 400 and 300 3- Profit or loss in location B when quantity is 350 and 450 4- Profit or loss in location C when quantity is 425 and 325 5- Maximum revenues in A, B and C6- Range of profit at Demand in A, B and C Sketch the Break – Even chart each three locationarrow_forwardM. Cotteleer Electronics supplies microcomputer circuitry to a company that incorporates microprocessors into refrigerators and other home appliances. One of the components has an annual demand of 250 units, and this is constant throughout the year. Carrying cost is estimated to be $1 per unit per year, and the ordering (setup) cost is $20 per order. a) To minimize cost, how many units should be ordered each time an order is placed? b) How many orders per year are needed with the optimal policy? c) What is the average inventory if costs are minimized? d) Suppose that the ordering (setup) cost is not $20, and Cotteleer has been ordering 150 units each time an order is placed. For this order policy (of Q 5 150) to be optimal, determine what the ordering (setup) cost would have to be.arrow_forward
- Pure gasoline has an energy density of 115,600 BTU per gallon while ethanol has an energy density of 75,670 BTU per gallon. If gasoline costs $3.50 per gallon, (a) what would the cost of pure ethanol have to be in order for the energy costs of the two fuels to break even? (b) What would the price of E85 (85% ethanol, 15% gasoline) have to be for its energy cost to be the same as that of pure gasoline?arrow_forwardCompany “A” has fixed expenses of P10000 per month and each unit of product has a variable cost of P0.02, while company “B” has fixed expenses of P2200 per month and can produce the same unit of product at 0.05 variable cost. At what number of units of annual production will company “A” have the same overall cost as company “B”?arrow_forwardThe landfill for Wellsburg has an area of 30 acres available for receiving waste from the city of 40,000 people who generate 36,000 tons of municipal solid waste (MSW) per year. If the fixed cost of the landfill is $425,000 per year and the operating cost is $14 per ton, how much must the landfill charge per ton of MSW to break even? The landfill charge per ton of MSW to break even is determined to be $arrow_forward
arrow_back_ios
SEE MORE QUESTIONS
arrow_forward_ios
Recommended textbooks for you
- Principles of Economics (12th Edition)EconomicsISBN:9780134078779Author:Karl E. Case, Ray C. Fair, Sharon E. OsterPublisher:PEARSONEngineering Economy (17th Edition)EconomicsISBN:9780134870069Author:William G. Sullivan, Elin M. Wicks, C. Patrick KoellingPublisher:PEARSON
- Principles of Economics (MindTap Course List)EconomicsISBN:9781305585126Author:N. Gregory MankiwPublisher:Cengage LearningManagerial Economics: A Problem Solving ApproachEconomicsISBN:9781337106665Author:Luke M. Froeb, Brian T. McCann, Michael R. Ward, Mike ShorPublisher:Cengage LearningManagerial Economics & Business Strategy (Mcgraw-...EconomicsISBN:9781259290619Author:Michael Baye, Jeff PrincePublisher:McGraw-Hill Education
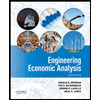
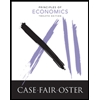
Principles of Economics (12th Edition)
Economics
ISBN:9780134078779
Author:Karl E. Case, Ray C. Fair, Sharon E. Oster
Publisher:PEARSON
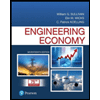
Engineering Economy (17th Edition)
Economics
ISBN:9780134870069
Author:William G. Sullivan, Elin M. Wicks, C. Patrick Koelling
Publisher:PEARSON
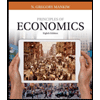
Principles of Economics (MindTap Course List)
Economics
ISBN:9781305585126
Author:N. Gregory Mankiw
Publisher:Cengage Learning
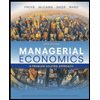
Managerial Economics: A Problem Solving Approach
Economics
ISBN:9781337106665
Author:Luke M. Froeb, Brian T. McCann, Michael R. Ward, Mike Shor
Publisher:Cengage Learning
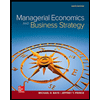
Managerial Economics & Business Strategy (Mcgraw-...
Economics
ISBN:9781259290619
Author:Michael Baye, Jeff Prince
Publisher:McGraw-Hill Education