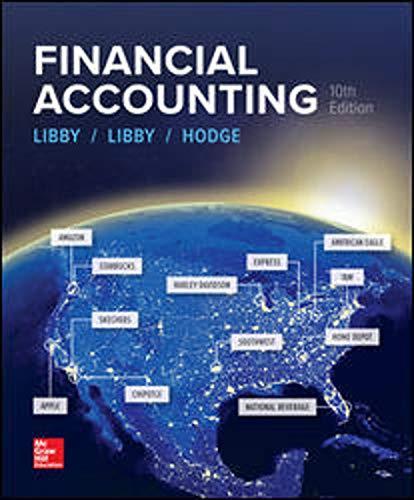
Concept explainers
Product Decisions Under Bottlenecked Operations
Youngstown Glass Company manufactures three types of safety plate glass: large, medium, and small. All three products have high demand. Thus, Youngstown Glass is able to sell all the safety glass that it can make. The production process includes an autoclave operation, which is a pressurized heat treatment. The autoclave is a production bottleneck. Total fixed costs are $234,000 for the company as a whole. In addition, the following information is available about the three products:
Large | Medium | Small | ||||
Unit selling price | $122 | $446 | $382 | |||
Unit variable cost | 96 | 365 | 336 | |||
Unit contribution margin | $ 26 | $ 81 | $ 46 | |||
Autoclave hours per unit | 2 | 6 | 4 | |||
Total process hours per unit | 4 | 12 | 12 | |||
Budgeted units of production | 3,400 | 3,400 | 3,400 |
a. Determine the contribution margin by glass type and the total company income from operations for the budgeted units of production.
Large | Medium | Small | Total | |
Units produced | fill in the blank 1 | fill in the blank 2 | fill in the blank 3 | |
Revenues | $fill in the blank 4 | $fill in the blank 5 | $fill in the blank 6 | $fill in the blank 7 |
Variable costs | fill in the blank 8 | fill in the blank 9 | fill in the blank 10 | fill in the blank 11 |
Contribution margin | $fill in the blank 12 | $fill in the blank 13 | $fill in the blank 14 | $fill in the blank 15 |
Fixed costs | fill in the blank 16 | |||
Income from operations | $fill in the blank 17 |
b. Prepare an analysis showing which product is the most profitable per bottleneck hour. Round the "Unit contribution margin per production bottleneck hour" amounts to the nearest cent.
Large | Medium | Small | |
Contribution margin | $fill in the blank 18 | $fill in the blank 19 | $fill in the blank 20 |
Autoclave hours per unit | fill in the blank 21 | fill in the blank 22 | fill in the blank 23 |
Unit contribution margin per production bottleneck hour | $fill in the blank 24 | $fill in the blank 25 | $fill in the blank 26 |

Trending nowThis is a popular solution!
Step by stepSolved in 2 steps with 2 images

- Jordan Bicycle Manufacturing Company currently produces the handlebars used in manufacturing its bicycles, which are high- quality racing bikes with limited sales. Jordan produces and sells only 7,400 bikes each year. Due to the low volume of activity, Jordan is unable to obtain the economies of scale that larger producers achieve. For example, Jordan could buy the handlebars for $33 each; they cost $36 each to make. The following is a detailed breakdown of current production costs. Item Unit-level costs Materials Labor Overhead Allocated facility-level costs Total Unit Cost $17 8 2 9 $36 Per Unit Total relevant cost Do you agree with the president's conclusion? After seeing these figures, Jordan's president remarked that it would be foolish for the company to continue to produce the handlebars at $36 each when it can buy them for $33 each. Total $125,800 59,200 14,800 66,600 $266,400 Required Calculate the total relevant cost. Do you agree with the president's conclusion? Totalarrow_forwardThe Heating Division of Oriole International produces a heating element that it sells to its customers for $47 per unit. Its variable cost per unit is $23, and its fixed cost per unit is $8. Top management of Oriole International would like the Heating Division to transfer 15.000 heating units to another division within the company at a price of $35. Assume that the Heating Division has sufficient excess capacity to provide the 15,000 heating units to the other division. What is the minimum transfer price that the Heating Division should accept? Minimum transfer price $arrow_forwardPeppertree Company has two divisions, East and West. Division East manufactures a component that Division West uses. The variable cost to produce this component is $1.56 per unit; full cost is $1.98. The component sells on the open market for $4.96. Assuming Division East has excess capacity, what is the lowest price Division East will accept for the component? What is the highest price that Division West will pay for it? (Enter your answers in 2 decimal places.)arrow_forward
- Hercules Steel Company produces three grades of steel: high, good, and regular grade. Each of these products (grades) has high demand in the market, and Hercules is able to sell as much as it can produce of all three. The furnace operation is a bottleneck in the process and is running at 100% of capacity. Hercules wants to improve steel operation profitability. The variable conversion cost is $15 per process hour. The fixed cost is $200,000. In addition, the cost analyst was able to determine the following information about the three products: Category High Grade Good Grade Regular Grade Budgeted units produced 4,900 4,900 4,900 Total process hours per unit 11 10 9 Furnace hours per unit 4 3 2.5 Unit selling price $270 $260 $240 Direct materials cost per unit $85 $81 $75 The furnace operation is part of the total process for each of these three products. Thus, for example, 4.0 of the 12.0 hours required to process…arrow_forwardThe Compressor Division and the Fabrication Division of Plash Company, which exclusively produces one type of washing machine, respectively, are its two divisions. For the Fabrication Division, which completes the washing machine and sells it to retailers, the Compressor Division makes compressors. The Fabrication Division buys compressors from the Compressor Division. The Fabrication Division will spend $40.00 on a compressor, which is the market price. (Skip updates to the inventory.) It is expected that the fixed costs for the Compressor Division remain constant for orders between 5,000 and 10,000 units. The Fabrication Division's fixed expenses are estimated to be $7.50 per unit at 10,000 units. Compressor's costs per compressor are: Direct materials $15.00 Direct labor $7.25 Variable overhead $3.00 Division fixed costs $7.50 Fabrication's costs per completed air conditioner are: Direct materials $150.00 Direct labor $62.50 Variable overhead $20.00 Division fixed costs $7.50 Assume…arrow_forwardHaving trouble with some questions from the last chapter.arrow_forward
- Piedmont Fasteners Corporation makes three different clothing fasteners in its manufacturing facility in North Carolina. All three products are sold in highly competitive markets, so the company is unable to raise prices without losing an unacceptable number of customers. Data from the most recent period concerning these products appear below: Annual sales volume Velcro 101,800 Metal 203,600 Nylon 407,200 Unit selling price $ 1.65 $ 1.50 $ 0.85 Variable expense per unit $ 1.25 $ 0.70 Contribution margin per unit $ 0.40 $ 0.80 $ 0.25 $ 0.60 Total fixed expenses are $407,200 per period. Of the total fixed expenses, $20,000 could be avoided if the Velcro product is dropped, $80,000 if the Metal product is dropped, and $60,000 if the Nylon product is dropped. The remaining fixed expenses of $247,200 consist of common fixed expenses such as administrative salaries and rent on the factory building that could be avoided only by going out of business entirely. The company's managers would like…arrow_forwardArtisan Metalworks has a bottleneck in their production that occurs within the engraving department. Jamal Moore, the COO, is considering hiring an extra worker, whose salary will be $54,000 per year, to solve the problem. With this extra worker, the company could produce and sell 3,000 more units per year. Currently, the selling price per unit is $25.00 and the cost per unit is $7.80. Direct materials $3.50 Direct labor 1.10 Variable overhead 0.40 Fixed overhead (primarily depreciation of equipment) 2.80 Total $7.80 Using the information provided, calculate the annual financial impact of hiring the extra worker. Profit $_____ ______arrow_forwardAdams Bicycle Manufacturing Company currently produces the handlebars used in manufacturing its bicycles, which are high-quality racing bikes with limited sales. Adams produces and sells only 6,200 bikes each year. Due to the low volume of activity, Adams is unable to obtain the economies of scale that larger producers achieve. For example, Adams could buy the handlebars for $30 each; they cost $33 each to make. The following is a detailed breakdown of current production costs. Item Unit-level costs Materials Labor Overhead Allocated facility-level costs Total Unit Cost $15 9 2 7 $33 Total $ 93,000 55,800 12,400 43,400 $204,600 After seeing these figures, Adams's president remarked that it would be foolish for the company to continue to produce the handlebars at $33 each when it can buy them for $30 each. Required Calculate the total relevant cost. Do you agree with the president's conclusion? Answer is complete but not entirely correct. Per Unit Totalarrow_forward
- Memanarrow_forwardAnswerarrow_forwardYoungstown Glass Company manufactures three types of safety plate glass: large, medium, and small. All three products have high demand. Thus, Youngstown Glass is able to sell all the safety glass that it can make. The production process includes an autoclave operation, which is a pressurized heat treatment. The autoclave is a production bottleneck. Total fixed costs are $160,000 for the company as a whole. In addition, the following information is available about the three products: Large Medium Small Unit selling price $353 $253 $133 Unit variable cost (278) (207) (117) Unit contribution margin $ 75 $ 46 $ 16 Autoclave hours per unit 6 4 2 Total process hours per unit 12 8 6 Budgeted units of production 2,600 2,600 2,600 a. Determine the contribution margin by glass type and the total company operating income for the budgeted units of production. Large Medium Small Total Units…arrow_forward
- AccountingAccountingISBN:9781337272094Author:WARREN, Carl S., Reeve, James M., Duchac, Jonathan E.Publisher:Cengage Learning,Accounting Information SystemsAccountingISBN:9781337619202Author:Hall, James A.Publisher:Cengage Learning,
- Horngren's Cost Accounting: A Managerial Emphasis...AccountingISBN:9780134475585Author:Srikant M. Datar, Madhav V. RajanPublisher:PEARSONIntermediate AccountingAccountingISBN:9781259722660Author:J. David Spiceland, Mark W. Nelson, Wayne M ThomasPublisher:McGraw-Hill EducationFinancial and Managerial AccountingAccountingISBN:9781259726705Author:John J Wild, Ken W. Shaw, Barbara Chiappetta Fundamental Accounting PrinciplesPublisher:McGraw-Hill Education
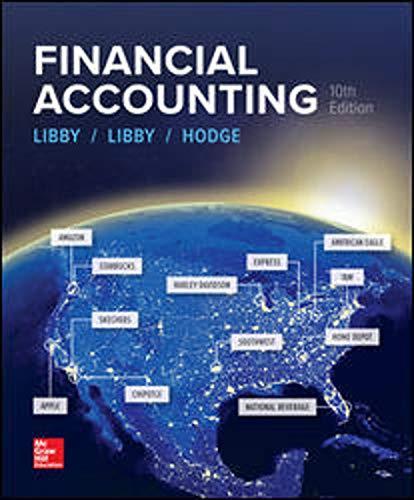
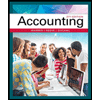
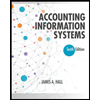
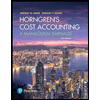
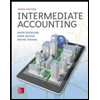
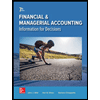