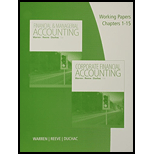
Part–A
Direct material variances:
The difference between the actual material cost per unit and the standard material cost per unit for the direct material purchased is known as direct material cost variance. The direct material variance can be classified as follows:
- Direct materials price variance.
- Direct materials quantity variance.
Direct labor variances:
The difference between the actual labor cost in the production and the standard labor cost for actual production is known as direct labor cost variance. The direct labor variance can be classified as follows:
- Labor rate variance.
- Labor time variance.
Variable factory overhead controllable variances:
The difference between the actual variable overhead costs and the standard overhead for actual production is known as the variable factory overhead controllable variances. The variable factory overhead controllable variance is computed as follows:
Variable factory overheadcontrollable variance}= (Actual variable factory overhead−Standard variable factory overhead )
Fixed factory overhead volume variances:
Factory overhead volume variances refers to the difference between the budgeted fixed
Fixed factory overheadvolume variance}= (Standard hours for 100% ofnormal capacity−Standardhours for actual units produced)×(Fixed factory overhead rate)
To determine: The fixed and variable portion of the utility cost using the high-low method.
Part–A

Explanation of Solution
1.
The fixed, and variable portion of the utility cost using the high-low method is $500,and $240 in the high cost method, and $500,and $100 in the low cost method respectively.
Working Notes:
Calculate the variable cost per unit.
Variable cost per unit = Difference in total costDifference in production=$740 (March)−$600(January) 1,200 cases (March)−500 cases (January)=$140700 cases=$0.20 per case (1)
Calculate the fixed and variable portion of the utility cost using high method:
Total cost=(Variable cost per unit× Units of production)+Fixed cost$740=($0.20 (1) ×1,200 units)+Fixed costVariable cost=$240
$740 =$240+Fixed costFixed cost =$740−$240Fixed cost =$500
Calculate the fixed and variable portion of the utility cost using low method:
Total cost=(Variable cost per unit× Units of production)+Fixed cost$600=($0.20 (1) ×500 units)+Fixed costVariable cost=$100
$600 =$100+Fixed costFixed cost =$600−$100Fixed cost =$500
Hence, using the high method, the fixed and variable portion of the utility cost is $500, and $240. On the other hand, using the low method, the fixed and variable portion of the utility cost is $500, and $100 respectively.
2.
The contribution margin per case.
Selling price | $100.00 | |
Less: Variable costs per case | ||
Direct materials | $ 17.00 | |
Direct labor | 7.20 | |
Utilities (1) | 0.20 | |
Selling expenses | 20.00 | |
Total variable costs per case | 44.40 | |
Contribution margin per case | $ 55.60 |
Table (1)
The contribution margin per case is $55.60.
3.
The fixed costs per month, including the utility fixed cost.
Utilities | $ 500 |
Facility lease | 14,000 |
Equipment |
4,300 |
Supplies | 660 |
Total fixed costs | $19,460 |
Table (2)
(2)
The fixed costs per month are $19,460.
4.
The break-even number of cases per month.
The break-even number of cases per month is 350 cases.
Working Note:
Break-even sales (units)=Fixed costsUnit contribution margin=$19,460$55.60=350 cases
Part–B
The fixed and variable portion of the utility cost using the high-low method.
Part–B

Explanation of Solution
5.
Prepare the production budget for the month of August.
Incorporation GS | |
Production Budget | |
For the month ended August 31 | |
Particulars | Cases |
Expected cases to be sold | 1,500 |
Plus desired ending inventory | 175 |
Total units required | 1,675 |
Less: Estimated beginning inventory | 300 |
Total units to be produced | 1,375 |
Table (3)
6.
Incorporation GS | ||||
Direct Materials Purchases Budget | ||||
For the month ended August 31 | ||||
Particulars | Cream Base (oz.) | Natural oils (oz.) | Bottles | Total |
Units required for production | 137,500 (3) | 41,250 (4) | 16,500 (5) | |
Add: Desired ending inventory | 1,000 | 360 | 240 | |
Total units required | 138,500 | 41,610 | 16,740 | |
Less: Estimated beginning inventory | 250 | 290 | 600 | |
Total materials to be purchased | 138,250 | 41,320 | 16,140 | |
Multiply: Unit price | $ 0.02 | $ 0.30 | $ 0.50 | |
Total direct materials to be purchased | $ 2,765 | $12,396 | $ 8,070 | $23,231 |
Table (4)
Working Notes:
Calculate the units required for producing cream base.
{Units required for producingcream base }={Total cases to be produced×Units per case}=1,375 cases×100 oz.=137,500 oz. (3)
Calculate the units required for producing natural oils.
{Units required for producingnatural oils }={Total cases to be produced×Units per case}=1,375 cases×30 oz.=41,250 oz. (4)
Calculate the units required for producing bottles.
{Units required for producingbottles }={Total cases to be produced×Units per case}=1,375 cases×12 bottles=16,500 bottles (5)
7.
Incorporation GS | |||
Direct Labor Cost Budget | |||
For the month ended August 31 | |||
Particulars | Mixing | Filling | Total |
Hours required for production of: | |||
Hand and body lotion | $458 (6) | $115 (7) | |
Multiply: Hourly rate | 18.00 | 14.40 | |
Total direct labor cost | $ 8,244 | $ 1,656 | $ 9,900 |
Table (5)
Working Notes:
Calculate the hours required for mixing the hand and body lotion.
{Hours required for mixingthe hand and body lotion }={Total cases to be produced×Time per case60 minutes}=1,375 cases×20 minutes60 minutes=458 hours (6)
Calculate the hours required for filling the hand and body lotion.
{Hours required for fillingthe hand and body lotion }={Total cases to be produced×Time per case60 minutes}=1,375 cases×5 minutes60 minutes=115 hours (7)
To prepare the
Incorporation GS | |||
Factory Overhead Cost Budget | |||
For the month ended August 31 | |||
Particulars | Fixed (2) | Variable (8) | Total |
Utilities | $ 500 | $ 275 | $ 775 |
Facility lease | 14,000 | 14,000 | |
Equipment depreciation | 4,300 | 4,300 | |
Supplies | 660 | 660 | |
Total factory overhead cost | $ 19,460 | $ 275 | $19,735 |
Table (6)
Working Note:
Calculate the variable utility cost.
Variable utility cost=Variable cost per unit×Number of cases=$0.20×1,375 cases=$275 (8)
9.
To prepare the
Incorporation GS Budgeted Income Statement For the month ended August 31 |
|||
Sales (9) | $150,000 | ||
Finished goods inventory, August 1 | $12,000 | ||
Direct materials: | |||
Direct materials inventory, August 1 (10) | $ 392 | ||
Direct materials purchases (Table 4) | 23,231 | ||
Cost of direct materials available for use | $ 23,623 | ||
Less: Direct materials inventory, August 31 (11) | 248 | ||
Cost of direct materials used in production | $ 23,375 | ||
Direct labor (Table 5) | 9,900 | ||
Factory overhead (Table 6) | 19,735 | ||
Cost of goods manufactured | 53,010 | ||
Cost of finished goods available for sale | $65,010 | ||
Less: Finished goods inventory, August 31 | 7,000 | ||
Cost of goods sold | 58,010 | ||
Gross profit | $ 91,990 | ||
Less: Selling expenses | 30,000 | ||
Income from operations | $ 61,990 |
Table (7)
Working Notes:
Calculate the sales.
Sales=Number of cases expected×Rate per case=1,500 cases×$100 per case=$150,000 (9)
Calculate the beginning direct materials inventory as on August 1.
[Direct materials inventory,August 1]=[Estimated beginning materials inventoryof cream base, oils, and bottles×Cost perunit of cream base, oils, and bottles]=[(250×$0.02)+(290×$0.30)+(600×$0.50)]=$392 (10)
Calculate the ending direct materials inventory as on August 31.
[Direct materials inventory,August 31]=[Estimated ending materials inventoryof cream base, oils, and bottles×Cost perunit of cream base, oils, and bottles]=[(1,000×$0.02)+(360×$0.30)+(240×$0.50)]=$248 (11)
Calculate the selling expenses.
Selling expenses=(Number of cases expected×Selling commission per case)=1,500 cases×$20 per case=$30,000 (12)
Part–C
The fixed and variable portion of the utility cost using the high-low method.
Part–C

Explanation of Solution
10.
Explanation:
Determine the direct materials price variances for the three materials.
Cream Base | Natural oils | Bottles | |
Actual price | $ 0.016 | $0.32 | $0.42 |
Less: Standard price | 0.020 | 0.30 | 0.50 |
Difference | $(0.004) | 0.02 | $(0.08) |
Multiply: Actual quantity | 153,000 (13) | 46,500 (14) | 18,750 (15) |
Direct materials price variance | $(612) Favorable |
$930 (Unfavorable) | $(1,500) Favorable |
Table (8)
Working Note:
(Actual quantityfor cream base)=(Number of cases expected×Actual directmaterials quantity per case)=1,500 cases×102 oz.=153,000 oz. (13)
(Actual quantityfor natural oils)=(Number of cases expected×Actual directmaterials quantity per case)=1,500 cases×31 oz.=46,500 oz. (14)
(Actual quantityfor bottles)=(Number of cases expected×Actual directmaterials quantity per case)=1,500 cases×12.5 bottles=18,750 bottles (15)
Interpretation:
It can be understood from the above data that there is variances in the direct materials prices due to the fluctuations in the market prices. The actual price for natural oils got increased when compared to its standard price, whereas, the actual prices for the cream base, and bottles got decreased when compared to their respective standard prices.
Determine the direct materials quantity variances for the three materials.
Cream Base | Natural oils | Bottles | |
Actual quantity | 153,000 oz.(13) | 46,500 oz. (14) | 18,750 (15) |
Less: Standard quantity | 150,000 (16) | 45,000 (17) | 18,000 (18) |
Difference | 3,000 oz. | 1,500 | 750 |
Multiply: Standard price | $ 0.02 | $0.30 | $0.50 |
Direct materials quantity variance | $60 Unfavorable |
$450 Unfavorable | $375 Unfavorable |
Table (9)
Working Note:
(Standard quantityfor cream base)=(Number of cases expected×Standard directmaterials quantity per case)=1,500 cases×100 oz.=150,000 oz. (16)
(Standard quantityfor natural oils)=(Number of cases expected×Standard directmaterials quantity per case)=1,500 cases×30 oz.=45,000 oz. (17)
(Standard quantityfor bottles)=(Number of cases expected×Standard directmaterials quantity per case)=1,500 cases×12 bottles=18,000 bottles (18)
Interpretation:
It can be understood from the above data that there are unfavorable direct materials quantity variances for all the three materials because of the fact that the standards were set at ideal quantity amounts for all the three materials.
11.
Determine the direct labor rate variances for the two departments.
Mixing Department | Filling Department | |
Actual rate | $ 18.20 | $14.00 |
Less: Standard rate | 18.00 | 14.40 |
Difference | $0.20 | $(0.40) |
Multiply: Actual time (hours) | 487.5 (19) | 140.00 (20) |
Direct labor rate variance | $97.50 Unfavorable |
$(56.00) Favorable |
Table (10)
Working Note:
(Actual timefor mixing)=(Number of cases expected×Actual time per case)60 minutes=1,500 units×19.50 minutes60 minutes=487.5 hours (19)
(Actual timefor filling)=(Number of cases expected×Actual time per case)60 minutes=1,500 units×5.60 minutes60 minutes=140 hours (20)
Interpretation:
It can be understood from the above finding that the mixing department has the unfavorable direct labor rate variance, and the filling department has favorable direct labor rate variance because of the fact that the former department uses the higher classification of labor, and the latter department uses the lower classification of labor. The higher classification of labor costs an additional cost of $0.20 per hour, whereas, the lower classification of labor saves an amount of $0.40 per hour.
Determine the direct labor time variances for the two departments.
Mixing Department | Filling Department | |
Actual time (hours) | 487.5(19) | 140 (20) |
Less: Standard time (hours) | 500 (21) | 125 (22) |
Difference | (12.5) | 15 |
Multiply: Standard rate | $ 18 | $14.40 |
Direct labor time variance | $(225) Favorable |
$216 Unfavorable |
Table (11)
Working Note:
(Standard timefor mixing)=(Number of cases expected×Standard time per case)60 minutes=1,500 units×20.00 minutes60 minutes=500 hours (21)
(Standard timefor mixing)=(Number of cases expected×Standard time per case)60 minutes=1,500 units×5.00 minutes60 minutes=125 hours (22)
Interpretation:
It can be understood from the above finding that the mixing department has the favorable direct labor time variance, and the filling department has unfavorable direct labor time variance because of the fact that the former department uses the higher classification of labor, and the latter department uses the lower classification of labor.
12.
Determine the variable factory overhead controllable variance.
Factory overheadcontrollable variance}= (Actual variable factory overhead−Standard variable factory overhead (23) )=$305−$300=$5 (24)
Determine the standard variable factory overhead.
Standard variablefactory overhead}=[Variable cost per unit×Units of production]=1,500 cases×$0.20=$300 (23)
Interpretation:
The factory overhead controllable variance is $5 and it is an unfavorable variance.
13.
Determine the factory overhead volume variance.
Factory overheadvolume variance}= (Standard units for 100% ofnormal capacity−Standard units produced (26))×(Fixed factory overhead rate)=(1,600 cases−1,500 cases×$12.1625)=100 cases×$12.1625=$1,216.25 (25)
The factory overhead volume variance is $1,216.25 and it is an unfavorable variance.
14.
To identify: The reason behind the standard direct labor and direct material costs are calculated based on the actual production volume of 1,500 cases rather than the planned production value of 1,375 cases.
Explanation:
The variances are the differences between the actual costs and the
Want to see more full solutions like this?
Chapter 22 Solutions
Working Papers, Volume 1, Chapters 1-15 for Warren/Reeve/Duchac's Corporate Financial Accounting, 13th + Financial & Managerial Accounting, 13th
- Solve this questions accountingarrow_forwardWatson Industries has a predetermined overhead rate of 65% of direct labor cost. During the month, $420,000 of factory labor costs are incurred, of which $120,000 is indirect labor. Actual overhead incurred was $250,000. What would be the amount debited to the Work in Process Inventory? Find outarrow_forwardPlease provide the correct answer to this general accounting problem using valid calculations.arrow_forward
- Determine the inventory turnover for Harbor Supply Co. based on the following information: • Beginning Inventory: $120,000 • Ending Inventory: $135,000 Cost of Goods Sold (COGS): $8,500,000 If the industry average for inventory turnover is 45, compare Harbor Supply Co.'s inventory turnover to the industry standard.arrow_forwardWatson Industries has a predetermined overhead rate of 65% of direct labor cost. During the month, $420,000 of factory labor costs are incurred, of which $120,000 is indirect labor. Actual overhead incurred was $250,000. What would be the amount debited to the Work in Process Inventory?arrow_forwardA company uses a process costing system. Its finishing department's beginning inventory consisted of 48,500 units, 40% complete with respect to direct labor and overhead. The department completed and transferred out 110,000 units during this period. The ending inventory consists of 38,000 units, which are 20% complete with respect to direct labor and overhead. All direct materials are added at the beginning of the process. The department incurred direct labor costs of $29,500 and overhead costs of $35,500 for the period. Assuming the weighted average method, the direct labor cost per equivalent unit (rounded to the nearest cent) is_. Answerarrow_forward
- A company uses a process costing system. Its finishing department's beginning inventory consisted of 48,500 units, 40% complete with respect to direct labor and overhead. The department completed and transferred out 110,000 units during this period. The ending inventory consists of 38,000 units, which are 20% complete with respect to direct labor and overhead. All direct materials are added at the beginning of the process. The department incurred direct labor costs of $29,500 and overhead costs of $35,500 for the period. Assuming the weighted average method, the direct labor cost per equivalent unit (rounded to the nearest cent) is_.arrow_forwardWhat are the incremental free cash flows associated with the new machine in year 3?arrow_forwardPlease provide the correct answer to this financial accounting problem using valid calculations.arrow_forward
- I am looking for help with this general accounting question using proper accounting standards.arrow_forwardPlease provide the accurate answer to this general accounting problem using appropriate methods.arrow_forwardI am searching for the accurate solution to this general accounting problem with the right approach.arrow_forward
- Financial & Managerial AccountingAccountingISBN:9781285866307Author:Carl Warren, James M. Reeve, Jonathan DuchacPublisher:Cengage LearningManagerial AccountingAccountingISBN:9781337912020Author:Carl Warren, Ph.d. Cma William B. TaylerPublisher:South-Western College PubFinancial And Managerial AccountingAccountingISBN:9781337902663Author:WARREN, Carl S.Publisher:Cengage Learning,
- Financial & Managerial AccountingAccountingISBN:9781337119207Author:Carl Warren, James M. Reeve, Jonathan DuchacPublisher:Cengage Learning
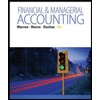
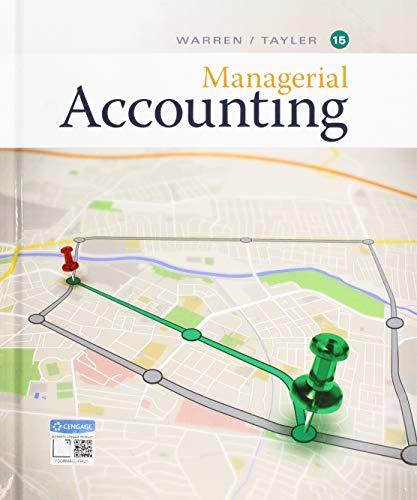
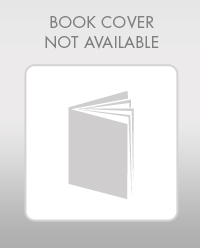
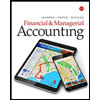