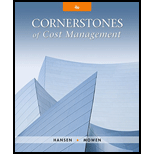
Cornerstones of Cost Management (Cornerstones Series)
4th Edition
ISBN: 9781305970663
Author: Don R. Hansen, Maryanne M. Mowen
Publisher: Cengage Learning
expand_more
expand_more
format_list_bulleted
Concept explainers
Textbook Question
Chapter 20, Problem 5CE
See Cornerstone Exercise 20.4. Fisher Company has three sequential processes: cutting, welding, and assembly. Assume that the optimal mix is Component A = 0 units per week; and Component B = 30 units per week. Demand is uniformly spread out over the five-day work week. Fisher requires a 2.5-day buffer.
Required:
- 1. Identify the drummer, the rate of production, the time buffer, and the rope.
- 2. Illustrate the DBR structure of Fisher Company.
- 3. What if the Welding Department was allowed or encouraged to produce at capacity? What effect will this have on work-in-process inventories?
Expert Solution & Answer

Want to see the full answer?
Check out a sample textbook solution
Students have asked these similar questions
Accounting: The warehouse supervisor at Emerald Bay Trading must reconcile damaged goods claims. Their policy allows claims within 48 hours of delivery, requires photographic evidence, and management approval for values over $500. Last week, from 45 deliveries worth $28,000, customers reported 8 damages, submitted 6 photos, and 5 claims met the time limit. What is the value of valid claims if each averages $180?
Can you please give correct solution for this general accounting question?
Please tutor help me to get answer of this below general accounting question
Chapter 20 Solutions
Cornerstones of Cost Management (Cornerstones Series)
Ch. 20 - What are ordering costs? What are setup costs?...Ch. 20 - Explain why, in the traditional view of inventory,...Ch. 20 - Discuss the traditional reasons for carrying...Ch. 20 - Prob. 4DQCh. 20 - Explain how safety stock is used to deal with...Ch. 20 - Prob. 6DQCh. 20 - What approach does JIT take to minimize total...Ch. 20 - One reason for inventory is to prevent shutdowns....Ch. 20 - Prob. 9DQCh. 20 - Explain how long-term contractual relationships...
Ch. 20 - What is a constraint? An internal constraint? An...Ch. 20 - Prob. 12DQCh. 20 - Prob. 13DQCh. 20 - Explain how lowering inventory produces better...Ch. 20 - Prob. 15DQCh. 20 - Thomas Corporation produces heating units. The...Ch. 20 - Sterling Corporation has an EOQ of 5,000 units....Ch. 20 - Patz Company produces two types of machine parts:...Ch. 20 - Prob. 4CECh. 20 - See Cornerstone Exercise 20.4. Fisher Company has...Ch. 20 - Ottis, Inc., uses 640,000 plastic housing units...Ch. 20 - Ottis, Inc., uses 640,000 plastic housing units...Ch. 20 - Melchar Company uses 78,125 pounds of oats each...Ch. 20 - Prob. 9ECh. 20 - Morrison Manufacturing produces casings for sewing...Ch. 20 - Morrison Manufacturing produces casings for sewing...Ch. 20 - Refer to Exercise 20.10. Assume the economic lot...Ch. 20 - Eyring Manufacturing produces a component used in...Ch. 20 - Hales Company produces a product that requires two...Ch. 20 - Many companies have viewed JIT as a panaceaa...Ch. 20 - Prob. 16ECh. 20 - Prob. 17ECh. 20 - Which of the following describes the economic...Ch. 20 - The economic order quantity (EOQ) for Part X15 is...Ch. 20 - A JIT inventory management system maintains which...Ch. 20 - For the theory of constraints, which of the...Ch. 20 - A dedicated pharmaceutical plant uses the theory...Ch. 20 - Prob. 23PCh. 20 - Burnett Company produces two types of gears: Model...Ch. 20 - Taylor Company produces two industrial cleansers...Ch. 20 - Prob. 26PCh. 20 - Calen Company manufactures and sells three...Ch. 20 - Confer Company produces two different metal...Ch. 20 - Pratt Company produces two replacement parts for a...Ch. 20 - Bountiful Manufacturing produces two types of bike...
Knowledge Booster
Learn more about
Need a deep-dive on the concept behind this application? Look no further. Learn more about this topic, accounting and related others by exploring similar questions and additional content below.Similar questions
arrow_back_ios
SEE MORE QUESTIONS
arrow_forward_ios
Recommended textbooks for you
- Managerial Accounting: The Cornerstone of Busines...AccountingISBN:9781337115773Author:Maryanne M. Mowen, Don R. Hansen, Dan L. HeitgerPublisher:Cengage LearningCornerstones of Cost Management (Cornerstones Ser...AccountingISBN:9781305970663Author:Don R. Hansen, Maryanne M. MowenPublisher:Cengage LearningManagerial AccountingAccountingISBN:9781337912020Author:Carl Warren, Ph.d. Cma William B. TaylerPublisher:South-Western College Pub
- Financial And Managerial AccountingAccountingISBN:9781337902663Author:WARREN, Carl S.Publisher:Cengage Learning,Essentials of Business Analytics (MindTap Course ...StatisticsISBN:9781305627734Author:Jeffrey D. Camm, James J. Cochran, Michael J. Fry, Jeffrey W. Ohlmann, David R. AndersonPublisher:Cengage Learning
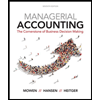
Managerial Accounting: The Cornerstone of Busines...
Accounting
ISBN:9781337115773
Author:Maryanne M. Mowen, Don R. Hansen, Dan L. Heitger
Publisher:Cengage Learning
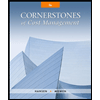
Cornerstones of Cost Management (Cornerstones Ser...
Accounting
ISBN:9781305970663
Author:Don R. Hansen, Maryanne M. Mowen
Publisher:Cengage Learning
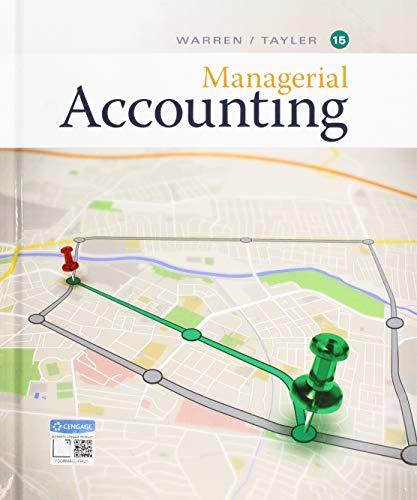
Managerial Accounting
Accounting
ISBN:9781337912020
Author:Carl Warren, Ph.d. Cma William B. Tayler
Publisher:South-Western College Pub
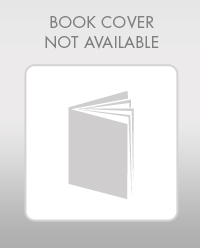
Financial And Managerial Accounting
Accounting
ISBN:9781337902663
Author:WARREN, Carl S.
Publisher:Cengage Learning,
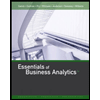
Essentials of Business Analytics (MindTap Course ...
Statistics
ISBN:9781305627734
Author:Jeffrey D. Camm, James J. Cochran, Michael J. Fry, Jeffrey W. Ohlmann, David R. Anderson
Publisher:Cengage Learning
Cost Accounting - Definition, Purpose, Types, How it Works?; Author: WallStreetMojo;https://www.youtube.com/watch?v=AwrwUf8vYEY;License: Standard YouTube License, CC-BY