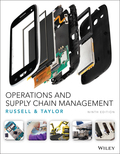
Concept explainers
Case summary:
T, a F500 company in M is one the largest retail chains in U. it has over 900 stores in 49 states, over 365,000 employees and revenue of over $70 billion. Its supply chain includes 37 distribution centres, and 4 warehouses near coastal ports to receive foreign shipments.
For its non-fabric products, such as electronics, furniture, hardware, kitchen goods and sporting goods, T collaborates with over 3000 factories worldwide. To maintain total quality, it must strictly monitor quality standards.
To do so, T ensures quality is maintained even as products move through the supply chain, before arriving on shop shelves. However, with 3000 vendors globally the chance of quality variation is high. When a supplier joins T’s supply chain, it must sign a “standards of supplier engagement” to meet quality requirements. Further the factory is inspected, and a rating assigned to determine if a supplier can use the factory. The factories are also required to sign and conform to T’s global social compliance about worker treatment.
T assists factories to improve performance on these fronts, however repeated failures lead to a termination of the agreement. T employs Six Sigma and various statistical processes in monitoring and quality control.
To determine: How other large companies with a global supply chain might use formal rating systems to evaluate suppliers.

Want to see the full answer?
Check out a sample textbook solution
Chapter 2 Solutions
Operations and Supply Chain Management 9th edition
- When football fans watch a game, they believe the other side commits more infractions on the field than does their own team. This favoritism can best be termed _____. Group of answer choices A. ethnocentrism B. the fundamental attribution error C. the affiliation bias D. marginalizationarrow_forwardWhen football fans watch a game, they believe the other side commits more infractions on the field than does their own team. This favoritism can best be termed _____. Group of answer choices ethnocentrism the fundamental attribution error the affiliation bias marginalizationarrow_forwardWhich of the following best describes the differences between egalitarianism and hierarchy as cultural values in negotiation? Group of answer choices A. Egalitarian cultures communicate directly; hierarchical cultures communicate indirectly. B. Egalitarian cultures treat people equally; hierarchical cultures discriminate among people. C. Egalitarian cultures divide things equally; hierarchical cultures divide things according to merit and status. D. Egalitarian cultures believe that status is permeable through effort and achievement; hierarchical cultures believe that superiors should take care of the needs of subordinates.arrow_forward
- Which of the following best describes the differences between individualism and collectivism as cultural values in negotiation? Group of answer choices A. Individualists see themselves as autonomous entities; collectivists see themselves in relation to others. B. Individualists prefer to work in groups; collectivists prefer to work alone. C. Individualists are cooperative; collectivists are competitive. D. Individualists focus on relationships; collectivists focus on money.arrow_forwardWhen it comes to resolving conflict, managers from hierarchical cultures prefer _____. Group of answer choices A. to attribute a disagreeable person's behavior to an underlying disposition and desire formal dispute resolution procedures B. an interests model that relies on resolving underlying conflicts C. to regulate behavior via public shaming D. to defer to a higher status personarrow_forwardThe tripartite model of culture is based on three cultural prototypes that represent negotiators’ self-views and are highly correlated with particular geographic regions. Give an example of the three. Face Dignity Honorarrow_forward
- The personality and unique character of a social group is best known as its _____ and includes the values and norms shared by its members and encompasses the structure of its social, political, economic, and religious institutions. Group of answer choices group identity group potency group stereotype culturearrow_forwardagree or disagree with this post Face - “Face” or dignity in a negotiation has been called “one of an individual’s most sacred possessions.”102 Face is the value a person places on his or her public image, reputation, and status vis-à-vis other people in the negotiation. Direct threats to face in a negotiation include making ultimatums, criticisms, challenges, and insults (Thompson, 2019). A good example of face is when I go to the negotiation table with a counterpart that is known to be difficult or not as knowledgeable about the category as they should be, my approach wouldn't be to point out their weakness, I will respect their thought process, show consideration for their perspective, all while guiding the conversation in the direction of my intended negotiation strategy in hopes to achieve my desired outcome. Dignity - endorses views such as, “People should stand up for what they believe in, even when others disagree,” and “How much a person respects oneself is far more…arrow_forward16:53 ◄ Mail 5G CSTUDY_Jan25_SCMH_O...Final_20250220143201.pdf CHOOSING FORECASTING MODELS gradienting are more mode. Yet when selecting a forecasting method, the door forecasts in fact, each of the three methods has different strength and can play important ing importance of the factors, such as the index and cast model, or a unified approach, ch del runs individual series separately A galable manufacturer is facing changes with demand fuctuations due to economiyapply make changes. Comment on why this has been the case and propose a forecasting approach that can be utilised t Question 13 ashit from a batch production process to a continuous flows to enhance efficiency. Critically analyse the trade- A public hospital in Free State is experiencing increasing patient wait times due to limited operacity. The hospital management is considering either expanding existing facilities orating more efficient Question 1.5 A farming consponsible for planting grain crops in Free State As expected…arrow_forward
- How can a college basketball coach use lean system strategies to improve the team's performance and win the national championship? What wastes can be eliminated from the team's training and equipment? How can performance data be used to adjust the team's strategy and tactics?arrow_forwardHow much does self-awareness influence the Interpersonal Trust Scale's results?arrow_forwardWhich of the following statements about organization's strategy is FALSE? OA. They are formulated after the organization's mission is determined. OB. They reflect an organization's purpose. OC. An organization's strategy exploits opportunities and threats. OD. They help determine how an organization expects to achieve its miss OE. Each functional area of the organization will have a strategy. The ability of an organization to match changes in a marketplace where design volumes fluctuate substantially is: OA. competing on productivity. OB. mass production. OC. time-based competition. OD. competing on differentiation. O E. competing on response. Porter's Five Forces Model is used to evaluate competition based on which 5 asp A. immediate rivals, potential entrants, customers, suppliers, and substitute B. potential entrants, customers, suppliers, legal regulations, and costarrow_forward
- MarketingMarketingISBN:9780357033791Author:Pride, William MPublisher:South Western Educational PublishingPurchasing and Supply Chain ManagementOperations ManagementISBN:9781285869681Author:Robert M. Monczka, Robert B. Handfield, Larry C. Giunipero, James L. PattersonPublisher:Cengage Learning
- Management, Loose-Leaf VersionManagementISBN:9781305969308Author:Richard L. DaftPublisher:South-Western College Pub
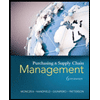
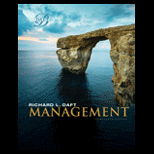