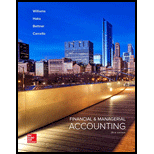
a.
Calculate the target cost for Product B and Product M.
a.

Explanation of Solution
Target costing:
Target costing is a business procedure that targets at the earliest stages of new product and service development, before creating and designing of production techniques.
Calculate the target cost for Product B.
Working note:
(1)
Calculate the target price of the Product M.
Working note:
(2)
Therefore, the target cost of Product B is $105.60 and Product M is $158.40.
b.
Estimate the total
b.

Explanation of Solution
Manufacturing overhead costs:
Manufacturing overhead costs are costs that are not directly related with the manufacturing of the products and it is also known as indirect costs. For example, indirect materials, indirect labour, indirect supplies.
Calculate the total manufacturing cost per unit:
Particulars | Product B | Product M |
Direct materials cost per unit | $25 | $40 |
Direct labor cost per unit | $20 | $50 |
Variable overhead cost | $5 | $12.50 |
Fixed overhead cost (3) | $62.50 | $62.50 |
Total manufacturing cost per unit | $112.50 | $165 |
Table (1)
- The cost per unit of Product B is above its target cost of $105.60 thus, it is not earnings the desired 12% return.
- The cost per unit of Product M is below its target cost of $158.40 thus, it is not earning a greater return than the desired rate.
Working note:
Calculate the fixed overhead cost per unit:
(3)
- The manufacturing cost per unit of Product B is $112.50 and for Product M is $165.
- Both of the products are not earning a return greater than the desired rate since the cost per unit is above the target cost.
c.
Recalculate the total manufacturing cost per unit if fixed overhead costs are assigned to products on the basis of direct labor hours and state the product that is earning the desired income.
c.

Explanation of Solution
Manufacturing overhead costs:
Manufacturing overhead costs are costs that are not directly related with the manufacturing of the products and it is also known as indirect costs. For example, indirect materials, indirect labour, indirect supplies.
Recalculate the total manufacturing cost per unit of the products:
Particulars | Product B | Product M |
Direct materials cost per unit | $25 | $40 |
Direct labor cost per unit | $20 | $50 |
Variable overhead cost | $5 | $12.50 |
Fixed overhead cost | $45.46 | $113.65 |
Total manufacturing cost per unit | $95.46 | $216.15 |
Table (2)
- The cost per unit of Product B is below its target cost of $105.60 thus, it is earning a greater return than the desired rate.
- The cost per unit of Product M is above its target cost of $158.40 thus, it is not earnings the desired return.
Working notes:
Calculate the time taken to produce each unit of Product B:
(4)
Calculate the time taken to produce each unit of Product M:
(5)
Calculate the total time taken to produce the estimated production of Product B:
(6)
Calculate the total time taken to produce the estimated production of Product M:
(7)
Calculate the allocation rate per hour:
Note:
(8)
Calculate the fixed overhead cost of Product B:
(9)
Calculate the fixed overhead cost of Product M:
(10)
d.
Estimate the total manufacturing cost per unit of each product if activity-based costing is used for assigning fixed overhead costs and state the product that is earning the desired income under this method.
d.

Explanation of Solution
Manufacturing overhead costs:
Manufacturing overhead costs are costs that are not directly related with the manufacturing of the products and it is also known as indirect costs. For example, indirect materials, indirect labour, indirect supplies.
Calculate the total manufacturing cost per unit of the products:
Particulars | Product B | Product M |
Direct materials cost per unit | $25 | $40 |
Direct labor cost per unit | $20 | $50 |
Variable overhead cost | $5 | $12.50 |
Fixed overhead cost (11) | $38.31 | $85.07 |
Total manufacturing cost per unit | $88.31 | $187.57 |
Table (3)
Therefore, the total manufacturing cost per unit of Product B and Product M is $88.31 and $187.57.
Working note:
Calculate the fixed overhead allocation per unit:
Particulars | Product B | Product M |
Allocation rate per unit | Total fixed overhead cost | |
Activity cost pools | (a) | (b) | (c) | Product B (d) = (a) × (c) | Product M (d) = (b) × (c) |
Setup costs | 100 | $00 | $875 | $87,500 | $262,500 |
Purchase orders | 300 | 100 | $1,625 | $487,500 | $162,500 |
Machining | 3,000 | 4,000 | $71.43 | $214,290 | $285,70 |
Inspection | 40 | 20 | $5,000 | $200,000 | $100,000 |
Shipping | 400 | 100 | $400 | $160,000 | $40,000 |
Total fixed overhead allocated units produced | $1,149,290 | $850,720 | |||
÷Units produced | ÷30,000 | ÷10,000 | |||
Fixed overhead cost per unit | $38.31 | $85.07 |
Table (4)
Note: For the calculation of allocation rate per unit refer Table (5)
(11)
Calculate the allocation rate of each overhead:
Overhead costs (a) |
Rate per set up ( Product B) (b) |
Rate per set up ( Product M) (c) |
Total rate per set up (d)=(b)+(c) |
Allocation rate per unit activity (e) = (a) ÷ (d) |
Machine setups $350,000 | 100 | 300 | $400 | $ 875 |
Purchase orders $650,000 | 300 | 100 | $400 | $1,625 |
Machining rate $500,000 | 3,000 | 4,000 | $7,000 | $71.43 |
Inspection $200,000 | 40 | 20 | $60 | $5,000 |
Shipping $300,000 | 400 | 100 | $500 | $400 |
Table (5)
(12)
- The cost per unit of Product B is below the target cost of 105.60 thus, it is earning a return greater than the desired rate.
- The cost per unit of Product M is above the target cost of $180 thus, it is not earnings the desired return.
e.
State the proportion of fixed overhead that is value added and mention the activity which can be improved first.
e.

Explanation of Solution
- Machining and shipping are the two fixed overhead activities that are value added and the proportion of these costs to total fixed overhead is calculated below:
- Therefore, the proportion of machining and shipping overheads to total fixed costs is 35 %.
- The number of steps taken to produce Product M can be reduced and it appears to be a logical activity.
f.
Ascertain the impact of the design changes on the manufacturing costs of both products and mention the products that will earn the desired return.
f.

Explanation of Solution
Manufacturing overhead costs:
Manufacturing overhead costs are costs that are not directly related with the manufacturing of the products and it is also known as indirect costs. For example, indirect materials, indirect labour, indirect supplies.
Calculate the manufacturing costs of Product B and Product M:
Particulars | Product B | Product M |
Direct materials cost per unit | $25 | $40 |
Direct labor cost per unit | $20 | $50 |
Variable overhead cost | $5 | $12.50 |
Fixed overhead cost (13) | $42.06 | $73.82 |
Total manufacturing cost per unit | $92.06 | $176.32 |
Table (6)
Working note:
Calculate the fixed overhead cost of Product B and Product M:
Particulars | Product B | Product M |
Allocation rate per unit | Total fixed overhead cost | |
Activity cost pools | (a) | (b) | (c) | Product B (d) = (a) × (c) | Product M (d) = (b) × (c) |
Setup costs | 100 | 75 | $2,000 | $200,000 | $200,000 |
Purchase orders | 300 | 100 | $1,625 | $487,500 | $162,500 |
Machining | 3,000 | 4,000 | $71.43 | $214,290 | $285,70 |
Inspection | 40 | 20 | $5,000 | $200,000 | $100,000 |
Shipping | 400 | 100 | $400 | $160,000 | $40,000 |
Total fixed overhead allocated units produced | $1,261,790 | $738,220 | |||
÷Units produced | ÷30,000 | ÷10,000 | |||
Fixed overhead cost per unit | $42.06 | $73.82 |
Table (7)
Note: For the calculation of allocation rate per unit except for setup costs refer Table (5)
(13)
Calculate the new allocation rate per machine setup:
(14)
Note: Units of production for Product M is reduced to 75 units.
- The cost per unit of Product B is below the target cost of $105.60 thus, it will earn more than the desired return.
- The cost per unit of Product M is above the target cost of $158.40 thus, it is earning lower than the desired rate.
g.
Calculate the manufacturing costs for each product if the machine is purchased and find out whether the Product M should be redesigned or should the machine be purchased.
g.

Explanation of Solution
Manufacturing overhead costs:
Manufacturing overhead costs are costs that are not directly related with the manufacturing of the products and it is also known as indirect costs. For example, indirect materials, indirect labour, indirect supplies.
Calculate the manufacturing costs for each product if a new machine is purchased:
Particulars | Product B | Product M |
Direct materials cost per unit | $25 | $40 |
Direct labor cost per unit | $20 | $50 |
Variable overhead cost | $5 | $12.50 |
Fixed overhead cost (15) | $37.81 | $79.12 |
Total manufacturing cost per unit | $87.81 | $181.62 |
Table (8)
Working note:
Calculate the total fixed overhead allocated per unit:
Particulars | Product B | Product M |
Allocation rate per unit | Total fixed overhead cost | |
Activity cost pools | (a) | (b) | (c) | Product B (d) = (a) × (c) | Product M (d) = (b) × (c) |
Setup costs | 50 | 140 | $1,450 | $72,500 | $203,000 |
Purchase orders | 300 | 100 | $1,625 | $487,500 | $162,500 |
Machining | 3,000 | 4,000 | $71.43 | $214,290 | $285,70 |
Inspection | 40 | 20 | $5,000 | $200,000 | $100,000 |
Shipping | 400 | 100 | $400 | $160,000 | $40,000 |
Total fixed overhead allocated units produced | $1,134,290 | $791,220 | |||
÷Units produced | ÷30,000 | ÷10,000 | |||
Fixed overhead cost per unit | $37.81 | $79.12 |
Table (9)
Note: For the calculation of allocation rate per unit except for setup costs refer Table (5)
(15)
Calculate the new allocation rate per machine setup:
(16)
Note: Units of production for Product B is reduced to 50 units and for Product M it is reduced to 140 units.
- The cost per unit of product B is below the target cost of $105.6 thus, it is earning a return greater than the desired 12% rate.
- The cost per unit of Product M is above the target cost of $158.60 thus, it will not earn the desired return.
- Purchasing new machine or redesigning of product M makes the cost of both the products below the target cost since, the new machine reduces the fixed set-up costs it might be a cots reducing decision.
- Information relating to purchase of new equipment and purchase price are missing for making decision related to the purchase of new equipment.
Want to see more full solutions like this?
Chapter 19 Solutions
Financial & Managerial Accounting
- Please provide answer the general accounting questionarrow_forwardWhat is the asset turnover ratio on these general accounting question?arrow_forwardHow can the accounting concept of materiality be applied to the recognition and disclosure of contingent liabilities? Explore the factors that accountants should consider when determining the appropriate level of detail to include in financial statements regarding potential future obligations.arrow_forward
- 5.5 PTS Accounting Problem: Red Farms produces three crop grades: Premium sells at twice standard grade Value grade at half standard grade If standard is $8/kg and daily harvest was: Premium: 120kg Standard: 250kg Value: 180kg Calculate daily revenue.arrow_forwardThe manana corporation had sales solve this accounting questionsarrow_forwardFinancial Accountingarrow_forward
- AccountingAccountingISBN:9781337272094Author:WARREN, Carl S., Reeve, James M., Duchac, Jonathan E.Publisher:Cengage Learning,Accounting Information SystemsAccountingISBN:9781337619202Author:Hall, James A.Publisher:Cengage Learning,
- Horngren's Cost Accounting: A Managerial Emphasis...AccountingISBN:9780134475585Author:Srikant M. Datar, Madhav V. RajanPublisher:PEARSONIntermediate AccountingAccountingISBN:9781259722660Author:J. David Spiceland, Mark W. Nelson, Wayne M ThomasPublisher:McGraw-Hill EducationFinancial and Managerial AccountingAccountingISBN:9781259726705Author:John J Wild, Ken W. Shaw, Barbara Chiappetta Fundamental Accounting PrinciplesPublisher:McGraw-Hill Education
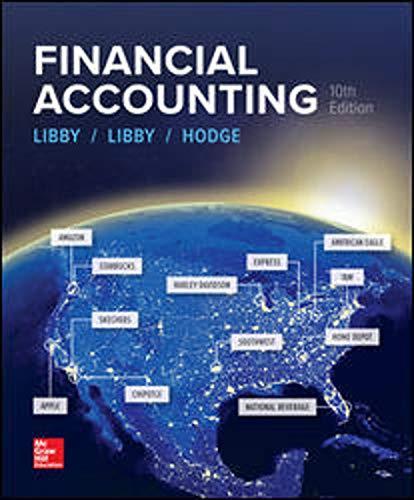
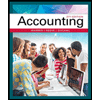
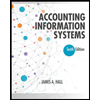
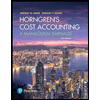
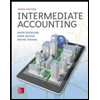
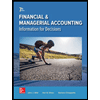