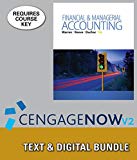
(A)
It is a method of cost accounting, which is used where the production is continuous, and the product needs various processes to complete. This method is used to ascertain the cost of the product at each process or stage of production.
Equivalents units for production
The activity of a processing department in terms of fully completed units is known as equivalent units. It includes the completed units of direct materials and conversion cost of beginning work in process, units completed and transferred out, and ending work in process.
To Prepare: The table showing the paper cost per output pound coating cost per pound, conversion cost per output pound, and yield (pounds transferred out / pounds input) for each month.
(b)
To Interpret: The table results of Incorporation PP.

Want to see the full answer?
Check out a sample textbook solution
Chapter 18 Solutions
Bundle: Financial & Managerial Accounting, 13th + Working Papers, Volume 1, Chapters 1-15 For Warren/reeve/duchac’s Corporate Financial Accounting, ... 13th + Cengagenow™v2, 2 Terms Access Code
- Managerial AccountingAccountingISBN:9781337912020Author:Carl Warren, Ph.d. Cma William B. TaylerPublisher:South-Western College PubEssentials of Business Analytics (MindTap Course ...StatisticsISBN:9781305627734Author:Jeffrey D. Camm, James J. Cochran, Michael J. Fry, Jeffrey W. Ohlmann, David R. AndersonPublisher:Cengage LearningCornerstones of Cost Management (Cornerstones Ser...AccountingISBN:9781305970663Author:Don R. Hansen, Maryanne M. MowenPublisher:Cengage Learning
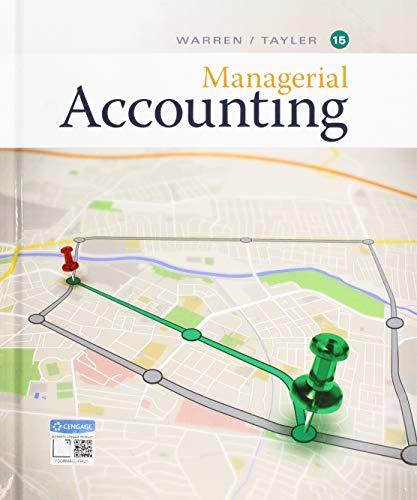
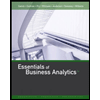
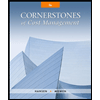