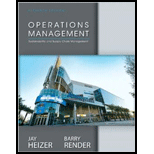
Operations Management
11th Edition
ISBN: 9780132921145
Author: Jay Heizer
Publisher: PEARSON
expand_more
expand_more
format_list_bulleted
Concept explainers
Textbook Question
Chapter 16, Problem 3P
Question
•• 16.3 Pauline Found Manufacturing, Inc., is moving to kanbans to support its telephone switching-board assembly lines. Determine the size of the kanban for subassemblies and the number of kanbans needed.
Setup cost = $30
Annual holding cost = $120 per subassembly
Daily production = 20 subassemblies
Annual usage = 2,500 (50 weeks × 5 days each × daily usage of 10 subassemblies)
Lead time = 16 days
Safety stock = 4 days’ production of subassemblies.
Expert Solution & Answer

Want to see the full answer?
Check out a sample textbook solution
Students have asked these similar questions
Question NO. 4
Convinced by the efficiency of hybrid model, Sony, started to produce LED filaments of its Soy TV's
itself while outsourcing all its other components. Initially, Sony can only produce these LED filaments at a
very steady rate of eight hundred per day. Three hundred TVs are assembled daily in eight hours shift, 250
days a year. Due to difference in TVs demands and its production, LED filaments are only produced in
batches of 2,000 units. Your are required to estimate;
Annual production of LED filament batches in numbers
b. Starting with zero inventory, if usage and production remains the same what would be the inventory
levels after 76 hrs.
Calculate average inventory levels when each production cycle starts with zero inventory.
d. The same equipment that is used to make the LED filaments could also be used to make another
filament used in the firm's other products. That job would require four days, including setup time.
Setup time for making a batch of the LED filament…
Question 19
4 pts
Based on available information, lead time demand for PC jump drives averages 53 units (normally distributed), with a standard
deviation of 4 drives. Management wants a 93.7% service level. Refer to the standard normal table for z-values.
What is the appropriate safety stock? (round your response to the nearest whole number).
6 units
3 units
53 units
56 units
59 units
Question 23
A truck maintenance facility has annual demand of 25000 gallons of motor oil and
operates 360 days per year. The lead time from placement of an order for motor oil
until delivery is 5 days and the standard deviation of daily usage is 12.5 gallons. Use
z=1.28 for a 90% service level and determine the appropriate re-order point.
O 347.22 gallons
35.77 gallons
383 gallons
370 gallons
Chapter 16 Solutions
Operations Management
Ch. 16 - Question 1. What is JIT?Ch. 16 - Prob. 2DQCh. 16 - Question 3. What is TPS?Ch. 16 - Question 4. What is level scheduling?Ch. 16 - Question 5. JIT attempts to remove delays, which...Ch. 16 - Prob. 6DQCh. 16 - Question 7. How does TPS contribute to competitive...Ch. 16 - Prob. 8DQCh. 16 - Question 9. Discuss how the Japanese word for card...Ch. 16 - Question 10. Standardized, reusable containers...
Ch. 16 - Prob. 11DQCh. 16 - Prob. 12DQCh. 16 - Question 16.1 Leblanc Electronics, Inc., in...Ch. 16 - Question 16.2 Tej Dhakars company wants to...Ch. 16 - Question 16.3 Pauline Found Manufacturing, Inc.,...Ch. 16 - Prob. 4PCh. 16 - Question 16.5 Discount-Mart, a major East Coast...Ch. 16 - Question 16.6 Discount-Mart (see Problem 16.5),...Ch. 16 - Prob. 7PCh. 16 - Question 16.8 Carol Cagle has a repetitive...Ch. 16 - Question 16.9 Given the following information...Ch. 16 - Question 16.10 Rick Wing has a repetitive...Ch. 16 - Mutual Insurance Company of Iowa Mutual Insurance...Ch. 16 - Prob. 2CSCh. 16 - Prob. 3CSCh. 16 - Prob. 4CSCh. 16 - Question JIT at Arnold Palmer Hospital Video Case...Ch. 16 - Question JIT at Arnold Palmer Hospital Video Case...Ch. 16 - Question JIT at Arnold Palmer Hospital Video Case...Ch. 16 - Question JIT at Arnold Palmer Hospital Video Case...
Knowledge Booster
Learn more about
Need a deep-dive on the concept behind this application? Look no further. Learn more about this topic, operations-management and related others by exploring similar questions and additional content below.Similar questions
- Question 3 Which of the following Inventory Holding Costs refers to the cost associated with return on the investment in inventory? Service Capital Cost Space Riskarrow_forwardQUESTION 28 Since information systems keep track of inventory levels, there is little need to perform periodic inventory counts.TrueFalsearrow_forwardQuestion 29 Kona's Manufacturing purchases 7000 boxes of organic dog treats per year. Boxes of the treats are priced as follows: 1 to 999 $1.30 dollars each, 1,000-1,499: $0.80 cents each, and 1,500 or more: $0.65 cents each. It costs $25 to prepare an order and receive it and carrying costs are 25 percent of unit cost per unit on an annual basis. Determine the feasible order quantity (you do not need to determine the total cost for this problem). O 1038 O 1686 O1323 O 1075 1468arrow_forward
- Question 3 Yellow Press, Inc., buys paper in 1,500-pound rolls for printing. Annual demand is 2,750 rolls. The cost per roll is $875, and the annual holding cost is 28 percent of the cost. Each order costs $75. How many rolls should Yellow Press order at a time? _______________rolls at a time. (Enter your response rounded to the nearest whole number.) What is the time between orders? (Assume 200 workdays per year.) __________________days. (Enter your response rounded to one decimal place.)arrow_forwardQUESTION 5 Peet's Coffees in Menlo Park, California, sells Melitta Number 101 coffee filters at a fairly steady rate of about 70 boxes of filters monthly. The filters are ordered from a supplier in Trenton, New Jersey. Peet's manager is interested in applying some inventory theory to determine the best replenishment strategy for the filters. Peet's pays $2.80 per box of filters and estimates that fixed costs of employee time for placing and receiving orders amount to about $20. Peet's uses a 22 percent annual interest rate to compute holding costs. How large a standing order should Peet's have with its supplier in Trenton, and how often should these orders be placed? EOQ= 216.22 Cycle=3 in yearsarrow_forwardQUESTION #4 James Marshall, owner and operator of the Hearing Bells Megastore, is reviewing the costs associated with the store's best-selling hearing aid, the HB100. The data available to Mr. Marshall concerning this device follow. 30 units/week Demand Order cost = $5/order Holding cost = $2.50/unit/year %3D The Hearing Bells Megastore operates 52 weeks a year. a. What is the EOQ? b. Given the data from above, and assuming a 300-day work year; how many orders should be processed per year? What is the expected time between orders? c. What is the total cost for the inventory?arrow_forward
- Question 5 Safety Stock Model Consider the following information on an inventory management system (one year is 50 weeks, one year is 365 days and 1 week is 7 days): Item Cost:$10 Order Cost:$250 Annual Holding Cost:33% of item cost Average Demand:515 per week Std. Dev. of Demand:125 per week Lead time:14 days a) Ignoring the uncertainty in the demand (i.e. looking only at average values), find the optimal order quantity and the reorder point. b) Consider now the uncertainty. The order quantity remains the same. If the target is to have a 98% annual service level, what should be the ROP? What is the safety stock? c) If the ROP is 1178 units (note that z value has been changed), what is the corresponding annual service level that the firm can provide?arrow_forwardQuestion 29 Which one of the following methods will be most suitable for managing dependent demand? Q-model ABC Analysis P-model The single-period model Material Requirements Planningarrow_forwardQ7arrow_forward
- Question 23 Company A carries 5,000 items. Customers ordered 1,000 items from inventory last week. Company A was able to fulfill 600 items of the order. What is the stock out probability for last week? Group of answer choices 0.08 0.4 0.6 0.92arrow_forwardQuestion 2. A convenience store, Shop Around the Corner, sells 5000 cans of peas every year. Shop Around the Corner owns his own trucks, each of which has capacity of carrying 100 cans. Utilizing each truck costs $100. There is also $50 fixed replenishment cost and $1 per unit per year inventory holding cost. a) Calculate the optimal order quantity of Shop Around the Corner at each replenishment? b) If Shop Around the Corner has a storage capacity of 680 cans, how would the optimal order quantity change?arrow_forwardQuestion 4 Illustrate Guardian pharmacy’s reorder system to manage their inventory so meet customer expectation. answer guidelines To use order point system and periodic review system. Illustrate its characteristics/advantage in the context of managing inventory in a pharmacy. For example: 1. Order point system - When the quantity of an item on hand in inventory falls to a predetermined level, an order is placed. • The quantity ordered is based on economic order quantity (EOQ). • Order quantity are usually fixed. • The order point is determined by the average demand during the lead time. • If the average demand or the lead time changes, there is no corresponding change in the order point, effectively there is a change in the safety stock. • The interval between replenishment are not constant but vary depending on the actual demand during the order cycle. Usually used for stocks that are longer to sell from the store so to…arrow_forward
arrow_back_ios
SEE MORE QUESTIONS
arrow_forward_ios
Recommended textbooks for you
- Practical Management ScienceOperations ManagementISBN:9781337406659Author:WINSTON, Wayne L.Publisher:Cengage,Operations ManagementOperations ManagementISBN:9781259667473Author:William J StevensonPublisher:McGraw-Hill EducationOperations and Supply Chain Management (Mcgraw-hi...Operations ManagementISBN:9781259666100Author:F. Robert Jacobs, Richard B ChasePublisher:McGraw-Hill Education
- Purchasing and Supply Chain ManagementOperations ManagementISBN:9781285869681Author:Robert M. Monczka, Robert B. Handfield, Larry C. Giunipero, James L. PattersonPublisher:Cengage LearningProduction and Operations Analysis, Seventh Editi...Operations ManagementISBN:9781478623069Author:Steven Nahmias, Tava Lennon OlsenPublisher:Waveland Press, Inc.
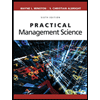
Practical Management Science
Operations Management
ISBN:9781337406659
Author:WINSTON, Wayne L.
Publisher:Cengage,
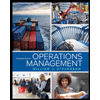
Operations Management
Operations Management
ISBN:9781259667473
Author:William J Stevenson
Publisher:McGraw-Hill Education
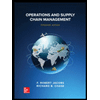
Operations and Supply Chain Management (Mcgraw-hi...
Operations Management
ISBN:9781259666100
Author:F. Robert Jacobs, Richard B Chase
Publisher:McGraw-Hill Education
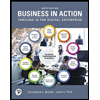
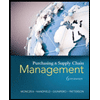
Purchasing and Supply Chain Management
Operations Management
ISBN:9781285869681
Author:Robert M. Monczka, Robert B. Handfield, Larry C. Giunipero, James L. Patterson
Publisher:Cengage Learning
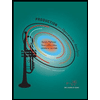
Production and Operations Analysis, Seventh Editi...
Operations Management
ISBN:9781478623069
Author:Steven Nahmias, Tava Lennon Olsen
Publisher:Waveland Press, Inc.
Inventory Management | Concepts, Examples and Solved Problems; Author: Dr. Bharatendra Rai;https://www.youtube.com/watch?v=2n9NLZTIlz8;License: Standard YouTube License, CC-BY