Concept explainers
A retailer has two merchandizers, Sue and Bob, who are responsible for setting order quantities for the
- a. Sue because she doesn’t incur the cost of salvaging inventory.
- b. Sue because she must have sold more units than Bob.
- c. Bob because even leftover inventory generates some additional revenue.
- d. Bob because he is probably ordering more than the mean of the demand forecast.

Want to see the full answer?
Check out a sample textbook solution
Chapter 13 Solutions
OPERATIONS MANAGEMENT
Additional Business Textbook Solutions
Horngren's Cost Accounting: A Managerial Emphasis (16th Edition)
Marketing: An Introduction (13th Edition)
Principles of Operations Management: Sustainability and Supply Chain Management (10th Edition)
Corporate Finance (4th Edition) (Pearson Series in Finance) - Standalone book
Gitman: Principl Manageri Finance_15 (15th Edition) (What's New in Finance)
Fundamentals of Management (10th Edition)
- Jill's Job Shop buys two parts (Tegdiws and Widgets) for use in its production system from two different suppliers. The parts are needed throughout the entire 52-week year. Tegdiws are used at a relatively constant rate and are ordered whenever the remaining quantity drops to the reorder level. Widgets are ordered from a supplier who stops by every three weeks. Data for both products are as follows: A. Find the total inventory costs if using inventory policy. This is a case considering safety stock (make sure to use the right formula)arrow_forwardA retailer uses a periodic review order-up-to model to control the inventory of one of its high volume products. Average demand is 2580 units per week with a standard deviation of 1270. The review period is 5 weeks, the lead time is 11 weeks, and the safety factor used is 0.61. How many stockouts should the retailer expect for this product next year?arrow_forwardSuppose the weekly demand at each regional distribution center (RDC) is normally distributed with a mean =117 and standard deviation =23. The company is considering to replace the RDCs with one central distribution center (CDC). The CDC would continue to have a continuous review policy, and the delivery lead time from Asia will remain 8 weeks. What is the average weekly demand at CDC?arrow_forward
- Solve this question:arrow_forwardA company incurs an ordering cost of $232 each time it places an order, regardless of the order size. The item's cost is $5, and the annual carrying charge for the item is 30%. If the annual demand for this item is 2,880 and the company's order quantity (Q) is 944, calculate its total annualized cost of inventory. The total annualized inventory costs are $.arrow_forwardCheryl Druehl has asked you to help her determinethe best ordering policy for a new product. The demand for thenew product has been forecasted to be about I ,000 units annually.To help you get a handle on the carrying and ordering costs,Cheryl has given you the list of last year's costs. She thought thatthese costs might be appropriate for the new product. She also told you that these data were compiled for 10,000 inventoryitems that were carried or held during the year. You havealso determined that 200 orders were placed last year. Your job as a new opera tions management graduate is to help Cheryl determinethe economic order quantity for the new product.arrow_forward
- Bakery A sells bread for $2 per loaf that costs $0.50 per loaf to make. Bakery A gives an 80% discount for its bread at the end of the day. Demand for the bread is normally distributed with a mean of 300 and a standard deviation of 30. What order quantity maximizes expected profit for Bakery A? (use the normal distribution table posted on Canvas and round up to the nearest integer)arrow_forwardA golf specialty wholesaler operates 50 weeks per year. Management is trying to determine an inventory policy for its 1-irons, which have the following characteristics: > Demand (D) = 2,000 units/year > Demand is normally distributed > Standard deviation of weekly demand = 2 units > Ordering cost = $30/order > Annual holding cost (H) = $5.00/unit > Desired cycle-service level = 85% > Lead time (L) = 4 weeks Refer to the standard normal table for z-values. a. If the company uses a periodic review system, P should be 3.87 weeks. (Enter your response rounded to the nearest whole number.) T should be units. (Enter your response rounded to the nearest whole number.)arrow_forwardplease answer within 30 minutes.arrow_forward
- Andy's Job Shop buys two parts (Tegdiws and Widgets) for use in its production system from two different suppliers. The parts are needed throughout the entire 52-week year to assemble Uediracs for sale. Tegdiws are used at a relatively constant rate but the use of Widgets vary with demand. Andy wants to improve his inventory management system and use either a "P" system or a "Q" system. What are the advantages and disadvantages of each system in this application and what information is needed to choose between them?arrow_forwardThe annual demand for a product is 16,800 units. The weekly demand is 323 units, with a standard deviation of 95 units. The cost to place an order is $31.50, and the time from ordering to receipt is two weeks. The annual inventory carrying cost is $0.20 per unit. Find the optimal order quantity.arrow_forwardHow do you do this? Please list step by step instructions.arrow_forward
- Purchasing and Supply Chain ManagementOperations ManagementISBN:9781285869681Author:Robert M. Monczka, Robert B. Handfield, Larry C. Giunipero, James L. PattersonPublisher:Cengage Learning
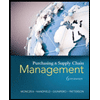